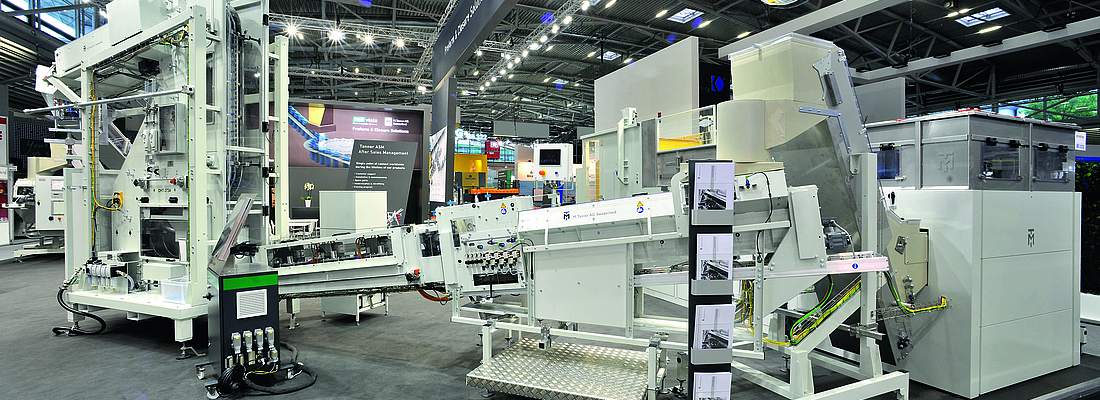
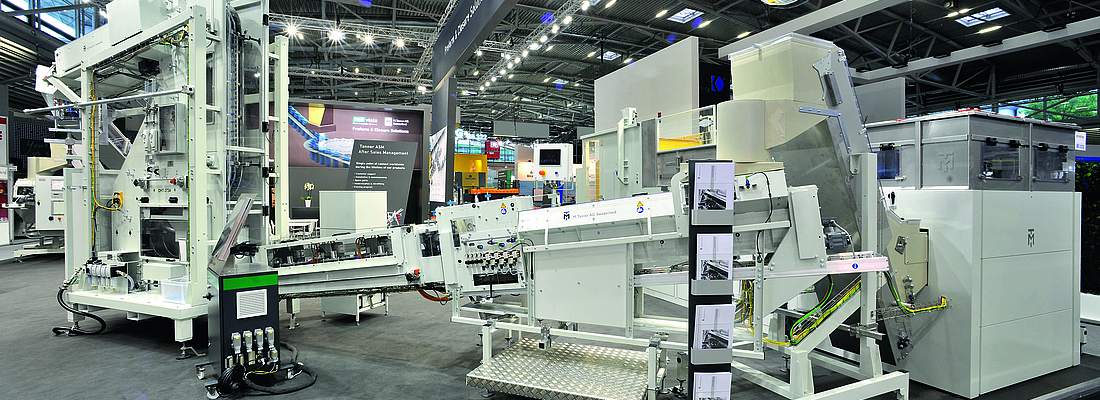
An increase in machine blocking in PET filling lines involving machines such as blow-moulding machines, labellers and fillers has meant that quality and efficiency have taken on much greater significance in the first process step – preform handling.
PREFORM LINE IN THE PET LINE
Interface elimination is crucial for optimising plant efficiency. If interfaces still remain, care must be taken to ensure that they include static (i.e. non-moving) parts. A simple mechanical interface not only removes sources of interference; it is also entirely advantageous for the operator and maintenance staff. Tanner has also taken action regarding this issue. Preform feeding systems are installed worldwide on every blow-moulding machine used for sorting. Upstream of each feeding system is a tipper which transfers the preforms into the silo of the preform feeding system.
Although the function of the tipper is clear, it is an autonomous machine and is equipped with its own control system and its own control cabinet. Moreover, tippers and their preform feeding systems are built by different manufacturers in more than 90% of cases. Additionally equipping the preform silo with a cover (protection against foreign particles) helps to further enhance the signal exchange between the two machines. There is no question that, in addition to technology (the machines have their own software and hardware), each machine also generates additional costs during the administrative process (e.g. purchasing, logistics, operating instructions, electrical planning, certificates). Tanner has now done away with these. Towards the middle of last year, Tanner began to offer our customers different preform lines depending on performance and layout options.
The tipper is no longer a standalone machine, but rather one component in the preform feeding system. In addition to reaping the technical advantages, costs have also been cut. With the preform line, thecustomer receives a complete solution from a single source. Our OEM customers can integrate the preform line plug- and-play into their PET line, offering them a familiar interface to the blow- moulding machine. The added value for customers is particularly apparent in commissioning and the spare parts business. A complete solution in preform handling also means that we are taking on more responsibility, and this helps our customers. There is no reason anymore why the tipper should be an autonomous machine.
OPTIMUM QUALITY AND EFFICIENCY BEFORE THE BLOCK
In addition to reducing the number of interfaces in recent years, Tanner has also placed increasing emphasis on optimising the efficiency and quality of preforms before the block. The concept of blocking the blow-moulding machine and filler, and in some cases the labeller too, means that machine downtime has an even greater impact on efficiency than before. What does this mean for preform handling? Tanner has divided the preform handling requirements into three categories.
MAXIMUM EFFICIENCY
Irrespective of the preform design (size, weight, shape), layout possibilities, ambient conditions and operator experience, the preform line requires 99.8% efficiency. To date, most line stops are due to inadequate preform feeding systems. Many manufacturers of plants and machinery for the filling industry are focused on other machines. The preforms are becoming lighter, the threads and support rings are smaller – all this makes handling more difficult. In order to achieve optimum efficiency, every detail of the system requires the right technical solution. This is where we as Tanner see our advantages. For over 25 years, we have focused exclusively on handling preforms.
Particularly with the block concept that is conventional today, which offers no possibility for regulation between the individual machines, efficiency in the first process step is of great importance. Every fraction of a percent counts.
THE PERFECT PREFORM FOR THE BLOW-MOULDING MACHINE
The downstream process must not suffer from poor-quality preforms that could have been withdrawn in the first process step. The aim must be to convey the perfect preform into the blow-moulding machine. The camera inspection for ejecting of oval preforms, preforms with damaged mouths or banana-shaped preforms should take place upstream of the block. Once a gap in the block has appeared, it can no longer be corrected. That is why Tanner offers an extensive camera inspection upstream of the blow-moulding machine. The clear objective is to reduce downtime caused by defective preforms. This not only includes gaps caused by missing preforms, but also the effects caused by a gap – in the blow-moulding machine process, for example. For this reason, the camera inspection at the inlet of the blow-moulding machine is only the second best variant.
A CLEAN PREFORM AFTER THE FIRST PROCESS STEP
How important is a clean preform? A guaranteed clean preform is important for many reasons. Before block technology, water rinser was partially used between the blow-moulding machine and the filler. High-quality preform interior cleaning is not just a matter of choice; using ionised air to blow out foreign particles is much more cost- effective. Water is no longer necessary. There are many concepts for preform cleaning. We are convinced that only an overhead solution that does not involve submerged nozzles can bring long-term success. Everything that can find its way into the preform must be able to get out again. Nozzles or lances are effective
for dust removal, but are not suitable for larger particles. This restriction is a „no-go“ for Tanner, therefore we offering an overhead air rinser solution which guarantees efficiency in cleaning out foreign particles as well as dust. Efficient preform cleaning is all the more important when preform/ bottle sterilisation takes place in the downstream process. The majority of germs are found on the particles themselves. Sterilisation without preform cleaning makes little sense. On the contrary, we were able to demonstrably improve the results of sterilisation by efficient preform cleaning upstream of the blow-moulding machine.
INTO THE FUTURE WITH AN OVERALL CONCEPT
Camera inspection and preform interior cleaning can be integrated into the preform line as well as final UVC irradiation. With or without additional components, the interface to the downstream process does not change. As a summary - Tanner is able to offer customers an overall concept with optimum efficiency and support the systems throughout their entire service life with our decades of experience.
The comPETence center provides your organisation with a dynamic, cost effective way to promote your products and services.
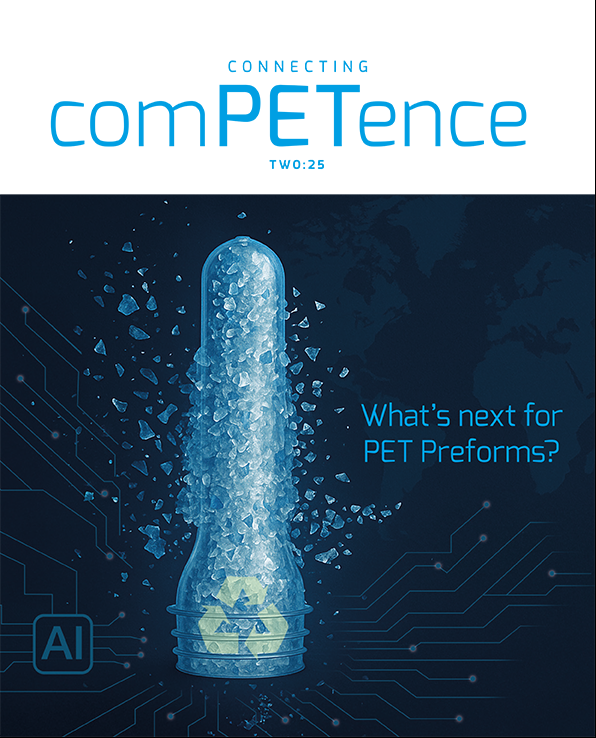
magazine
Find our premium articles, interviews, reports and more
in 3 issues in 2025.