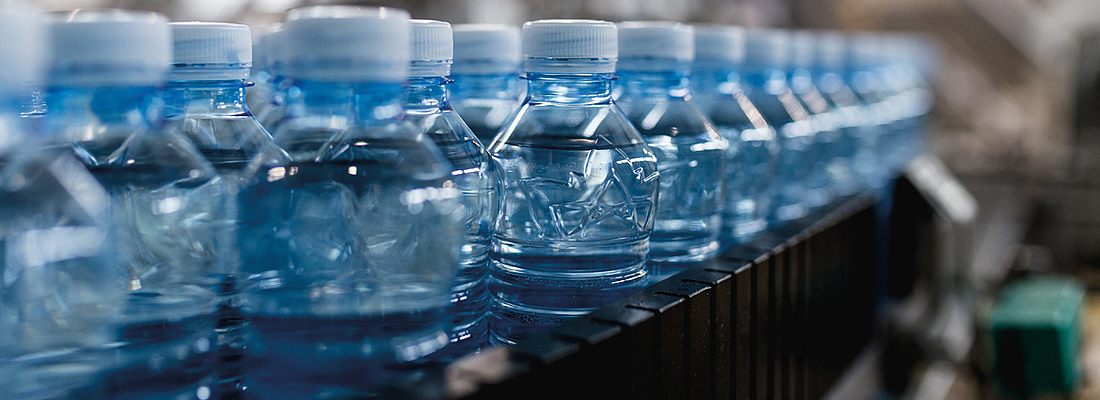
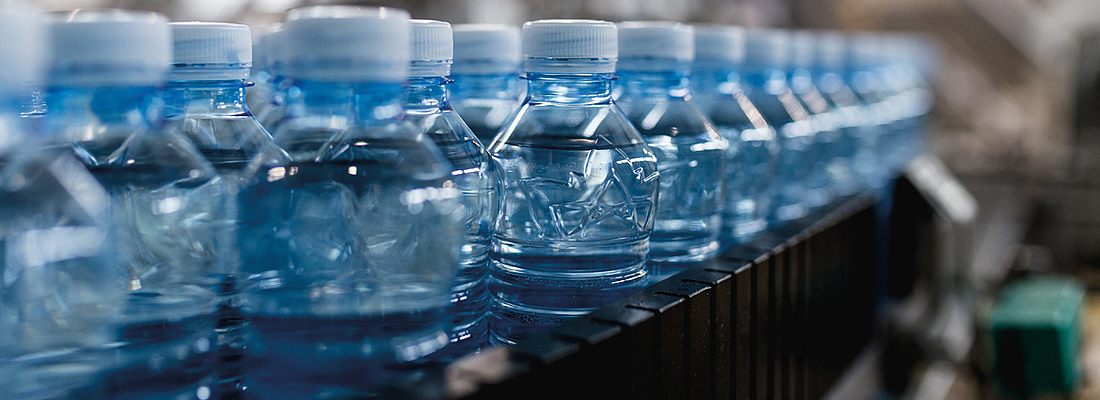
Injection stretch blow moulding
Zero Cooling for Higher Quality& Productivity in PET Containers
Nissei ASB Machine Co., Ltd. recently celebrated its 40th anniversary as the world’s leading supplier of 1-step and 1.5-step injection stretch blow molding machines and molds for PET containers. Drawing on their deep experience, the company recently announced a new twist on the basic molding process that they have termed “Zero Cooling” (patent pending), with the focus on improved product quality at vastly increased production rates.
We have all visited trade shows and seen molding demonstrations with headline grabbing productivity claims, yet on closer inspection, the container molded is often totally unsuitable for real world use or the product quality was at best marginal. This is simply a manifestation of the rule in plastics molding, quality of containers tends to be inversely proportional to cycle times, i.e. productivity increase equals quality decrease.
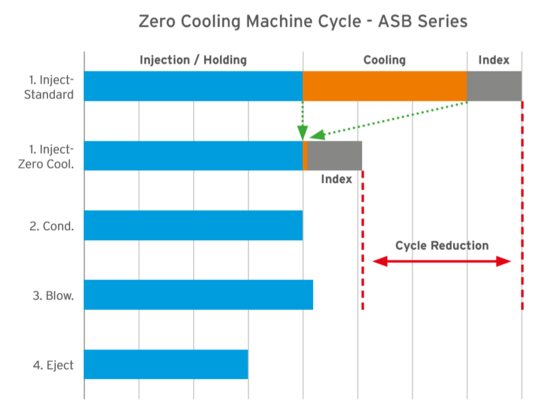
Fig 1: Time chart of standard & reduced cycle time
This is largely due to the classic approach to faster cycles of designing the preform as thin as possible. While improved cycles are achievable by this method, it has the adverse side-effect of creating an unstable process with reduced product quality. So, central to ASB’s challenge developing Zero Cooling was to not only raise the bar on quality, but to do so within significantly shorter cycle times for containers that readily meet or exceed real world specifications.
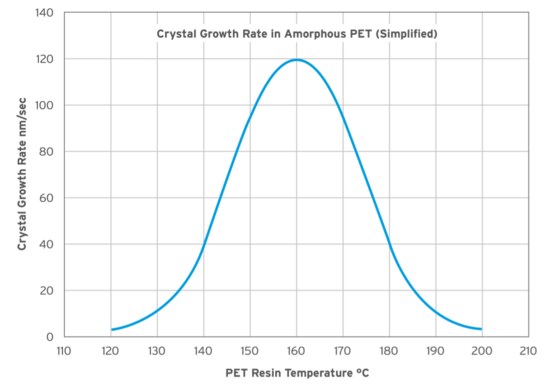
Fig 2: Simplified crystal growth curve
Zero Cooling (patent pending)
Under the Zero Cooling technique, preforms leave the injection mold immediately after completion of filling and packing with no allowance for cooling time, then are transferred to the preform conditioning or cooling station where all necessary cooling is applied together with any temperature optimization allowing the injection mold to be immediately available for the next injection cycle.
In standard 1-step molding, cooling time represents a significant portion of the total machine cycle time (Fig 1), the result with Zero Cooling is an average 35% reduction in overall cycle leading to an average 1.5X increase in output. Despite the faster cycle, due to a revised preform design, container visual quality is actually increased and physical strength is improved by an average of 15% over standard molding.
Many molding machines already use some form of post-molding cooling, but as the name implies, the target with Zero Cooling is to totally eliminate the use of cooling time within the injection mold, to the extent that the preform is at the limits that can be safely de-molded. As the mold opens the preform skin is just stiff enough to resist any deformation.
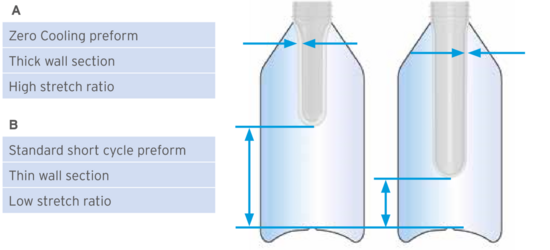
Fig 3: Preform design variations
Crystallization
If molten PET resin is cooled too slowly it will crystallize becoming hazy or white and its physical properties will change making it unsuitable for container molding (Fig 2).
One workaround used by competitors to is to select specially formulated PET resin grades having lower crystallization rates, however these generally carry significant price premiums negating the advantage of a shorter cycle making this route undesirable to converters.
However, with the Zero Cooling technique, multiple tests have proven that standard PET resin grades are perfectly capable of producing stunning results.
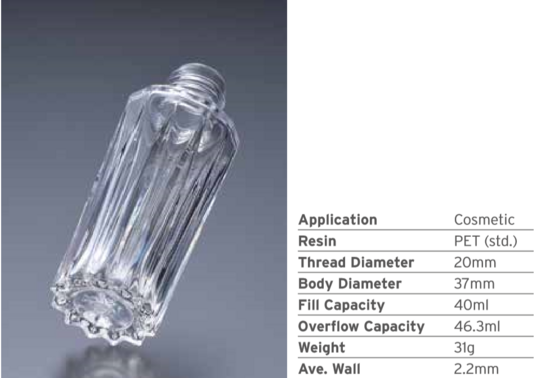
Fig 4: Glass-like PET cosmetic container molded at 13.1 seconds
De-Molding
A very hot preform could stick to the injection core or deform during mold ejection causing a defect or a machine stoppage. So, depending on the requirements of the preform shape, injection cores are specially modified to provide safe and easy mold release and where possible, preform draft angles may be modified as required to avoid any problems.
In all ASB products, preforms are molded in a vertical orientation giving a natural advantage for the Zero Cooling technique – avoiding the possibility of bending that might occur in a horizontal system and enabling the safe transfer of very hot preforms.
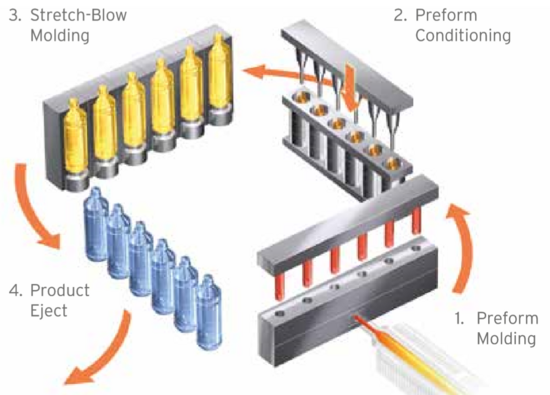
Fig 5: Overview of 4-Station One-Step Molding
Preform Design Perhaps counterintuitively, Zero Cooling takes the approach of designing the preform as small as possible with an increased wall thickness. Past practice for fast cycling has been to design the thinnest possible preform targeting the shortest possible injection / cooling time with the side effect that, for a given weight, the preform necessarily becomes longer. Shifting the preform design priority in this direction nearly always results in lower strength and process instability.
With Zero Cooling, preform thickness no longer dictates cycle time as the preform is cooled outside of the injection mold. This allows shorter, thicker preforms that provide increased stretch ratios (Fig 3) while the additional thickness ensures greater temperature stability throughout the preform as heat transfer occurs more easily in both the vertical and circumferential directions during transfer to the conditioning station.
When PET undergoes biaxial orientation at the correct temperatures and ratios, its yield strength and stiffness increase by around 50-60% axially and by around 160- 250% circumferentially. Gas barrier is also increased by 50% or more. In addition, proper ratios greatly assist to stabilize and control the stretching process resulting in higher quality and stable molding from minimum resin weight.
Since Zero Cooling allows designers to now focus entirely on optimizing the stretch ratios toward container quality, container strength is maximized, and molding stability is enhanced, even where factory infrastructure is not ideal. In addition, since greater strength becomes easier to achieve, there is more scope to reduce the weight of the PET container.
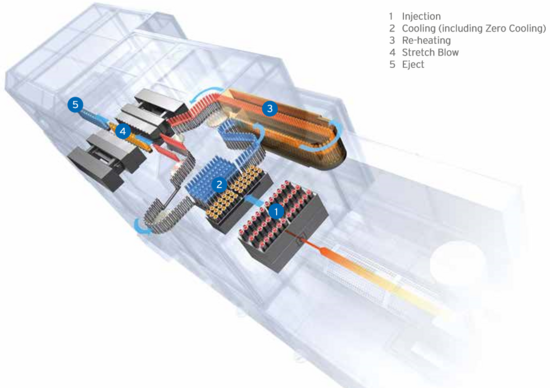
Fig 6: PF36 Process Overview
Zero Cooling Types
Depending on the category and shape of the container, i.e. standard bottle, wide mouth jar, light-weight, heavy cosmetic, etc., the specific method of Zero Cooling will be customized and may include the use of cooling air, pre-blow or compression forming techniques, but all will use a variation of the “pot and core” configuration. The key point is to rapidly remove the heat that would have been normally removed inside the injection mold, and to prepare the preform for optimum blowing within a reduced cycle time.
Cooling air types use low pressure air. Volumetric requirements will depend on the machine, container design and number of cavities, however it is possible for a blow air recovery system to be utilized that will reduce additional air requirements.
Compression types make physical contact with the preform and allow for the possibility of re-shaping of the preform to suit the finished container.
For standard containers the form of the pot may closely follow the preform exterior shape, but thicker preforms for premium cosmetic containers such as in Fig 4 may benefit from a larger pot that allows partial inflation allowing thinning of the preform wall for more efficient cooling. Or, for extreme oval containers, it is possible to design some degree of ovality or eccentricity into the conditioning parts to modify the preform shape in preparation for blowing.
In testing, these cooling methods have reliably reduced the overall preform temperature bringing it below the critical crystal growth region and into the optimum range for stretch blow molding. Since all mold parts are custom designed to the needs of each container specification, almost anything becomes possible. Most importantly, these systems in the machine’s second station are key to enabling this level of quality and performance to be achieved using standard PET grades.
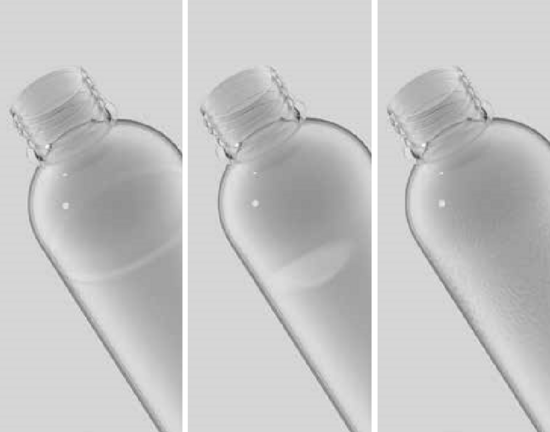
Fig 7: Visual Defects, L to R, “Thick Rings”, “Fisheye” and “Orange Peel”
1-Step Implementation
Standard one-step molding works on the principle that an injection molded preform is removed from its mold while the PET resin is still above its glass transition temperate (Tg) and is still flexible. This residual heat is then used to allow molding of the preform into the finished container shape at the stretch-blow station.
ASB’s signature 4-station, 1-step machines have remained at the forefront of PET molding for 40 years – their success lies in the second of these four stations, known as the “preform conditioning station” (Fig 5) that allows much higher product versatility and process stability over the 3-station alternatives.
Specialized mold components in the second station apply a variety of heating or cooling techniques to optimize the temperature profile of the preforms, or to otherwise modify the preform properties so the preform behaves in a predictable and controllable way according to the design requirements of the finished container.
ASB’s designers reviewed the role of the preform conditioning station and were able to incorporate the Zero Cooling system at this point. By performing increased cooling in tandem with the standard preform preparation, new preform design ideology has resulted in drastic cycle time reductions while achieving improved container performance and quality.
The four stations operate simultaneously within each cycle, but even with Zero Cooling, preform molding still requires the longest time of the four. This means that time reductions achieved by Zero Cooling at the injection station translates directly into reduction of overall cycle time.
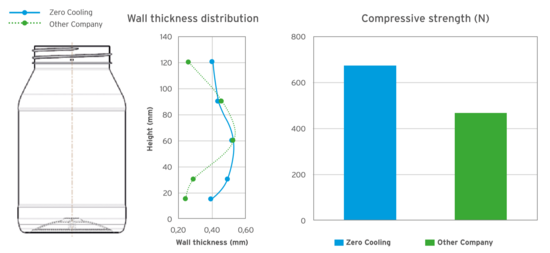
Fig 8: Comparison between competitor company’s short cycle and Zero Cooling
1.5-Step Implementation
In 1996 ASB introduced a radical new approach to 1-step molding with its PF Series. In these machines, the number of injection and blow cavities was changed, typically to a ratio of 3:1 to account for the much longer time required to inject preforms compared to blowing bottles.
While still a self-contained 1-step process (raw material in, finished product out), the stations are split and optimized more in line with the concept of 2-step molding, hence the 1.5-step title was introduced. In the standard 1.5-step process, injection molded preforms are transferred into a secondary cooling station before going on to partial re-heating. By upgrading the post cooling system to incorporate Zero Cooling capability, a similar effect can be achieved to that described in the 1-step system. That is, preforms can be de-molded at temperatures that are significantly higher than optimum, then all necessary cooling is applied while the injection mold is able to begin the next injection cycle.
Other incremental improvements, including the adoption of ASB’s “Vision1” control system into the PF36 Series, allow analogue machine movements resulting in shorter indexing times further increasing productivity.
With Zero Cooling implemented, the PF36 Series can now produce 500ml water bottles at up to 18,000bph, making these models very competitive in terms of investment cost, energy consumption, footprint and labor cost, and allows them to be matched with filling machines with up to 300bpm throughput.
Quality Improvement
With the ability to better optimize the preform even with fast cycle molding, Zero Cooling leads to container quality improvements in three main areas; ¡ Visual ¡ Physical strength. ¡ Wall thickness control
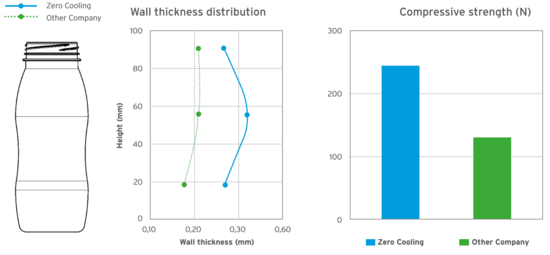
Fig 9: Physical property comparison between standard molding and Zero Cooling
Visual
While chasing short cycle times, preforms tend to be hotter than normal which commonly results in three obvious defects – Thick Rings, Fisheye and Orange Peel (Fig 7). Since Zero Cooling effectively lowers the preform temperature to an equal or greater degree compared to standard molding, all three potential defects are completely eliminated.
Physical Strength
From a combination of better wall thickness control and higher orientation of the PET resin, physical strength of the container is seen to increase by around 15% over standard fast cycle molding. Wall Thickness Control The effectiveness of Zero Cooling is so great that at the time of blowing, the preform temperature is lower than that produced by standard molding, further enhancing the control of wall thickness. In addition, higher stretch ratios also aid control of wall thickness meaning that material usage can be optimized, increasing the scope for light weighting. The results for both characteristics can be seen in Fig 8 & Fig 9.
Productivity Improvement Improvement in productivity brings a wide range of benefits including; ¡ Direct increase of profit ¡ Increased production capacity
- Improved flexibility for maintenance scheduling
- Improved production per square meter of floor space
For typical container designs, this technique produces average reductions in cycle times of around 35% over standard molding, equating to an average 1.5X increase in output using the same machine model. The gains tend to increase with thicker preforms with some heavyweight cosmetic containers achieving reductions as high as 50-60%. (2.0 to 2.5X production rate). Actual results for a range of container types can be seen in the Table 1.
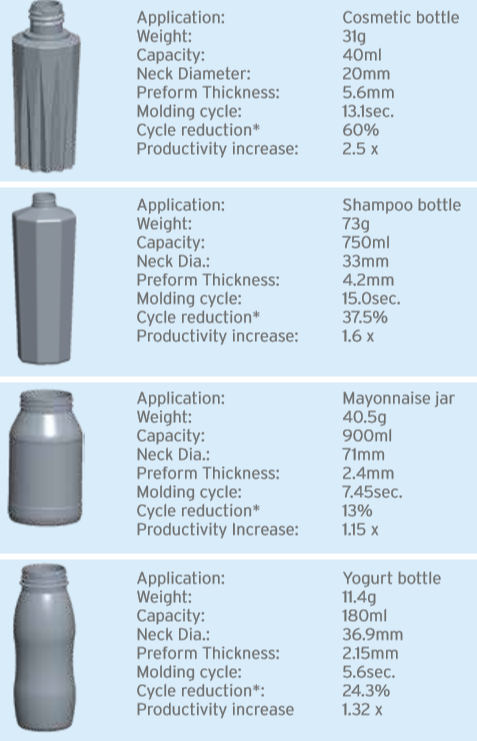
Table 1: Zero Cooling molding cycle examples *ASB comparison
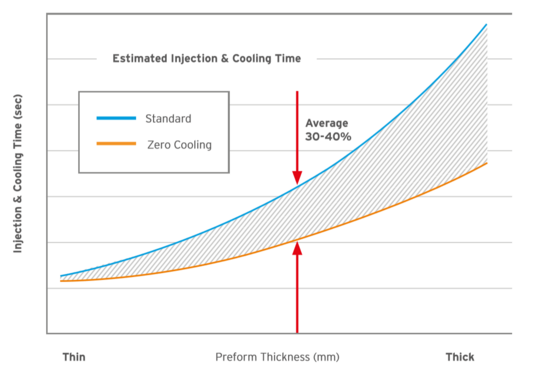
Fig 10: Estimated reduction in molding times
Energy Savings Based on general test data using likefor-like equipment, designers found that energy consumption increases by around 60% of the increase in productivity, or in other words, as output goes up, the cost per bottle tends to come down.
To illustrate this in a specific comparison, a PF36 molding the same bottle at various cycle times exhibited an energy reduction of around 8.5% in terms of watts per bottle for an 11% increase in production (Fig 11).
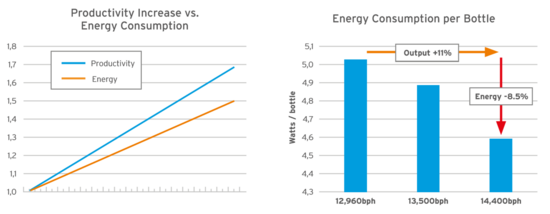
Fig 11: Energy reduction per bottle with increased output
Summary
In the past, the major method to achieve shorter cycle time has been to utilize thin preforms that have the disadvantage of decreasing container quality. Zero Cooling overcomes this limitation and achieves shorter cycle time while maintaining or improving the container quality. The second station in ASB’s four station 1-step models, or the PF Series 1.5-step models continues to give ASB’s customers an advantage over competitor’s equipment.
The additional mold design and components adds minor capital cost to the machine and mold, but the improved productivity has a drastic effect on profitability for converters. Cost studies have shown that the payback period for this additional technology on a mid-sized machine is in the order of weeks.
The comPETence center provides your organisation with a dynamic, cost effective way to promote your products and services.
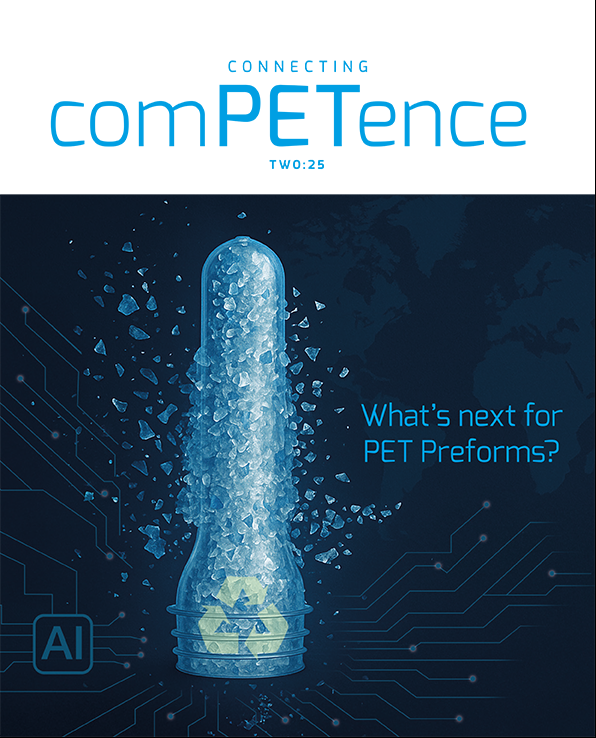
magazine
Find our premium articles, interviews, reports and more
in 3 issues in 2025.