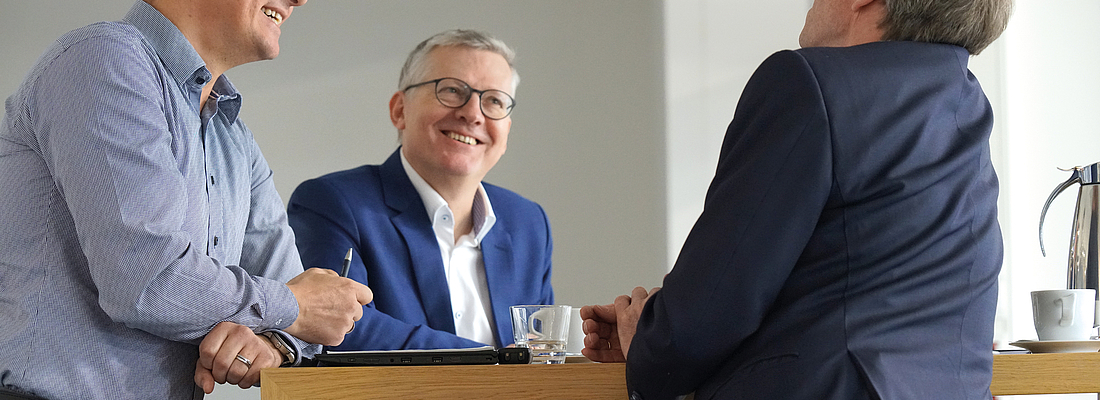
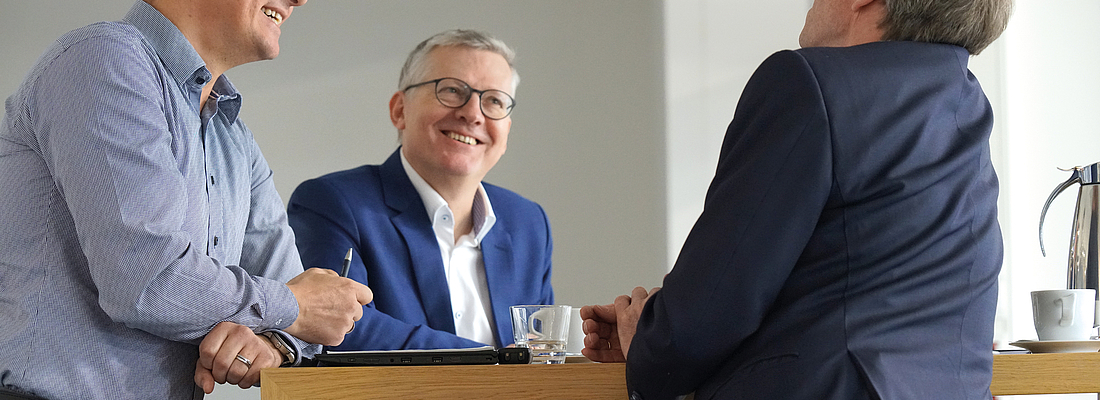
Pellets are the initial ingredients for a new product – or how the circular economy means coming together to achieve our goals. Interview by Barbara and Otto Appel with Manfred Hackl and Christoph Wöss, Erema Group.
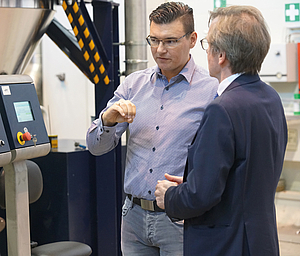
Are recycling technologies the gateway to a better world? The key that opens the complex lock protecting the mountains of waste? During our conversation with Manfred Hackl, CEO and Christoph Wöss, Business Development Manager Application Bottle at EREMA Group GmbH, it becomes clear that the answer to this question is yes. As one piece of the puzzle.
CC: Is there any hope that the plastics industry will solve the world’s recycling problems?
Hackl: Certainly not overnight. The issue is still dominated by emotions. However, I can sense that the tide is turning and discussions are becoming more and more rational. Facts are being listened to and debated. And NGOs are also getting involved. Ultimately, we must ask ourselves what alternatives there are to plastic.
Wöss: A change in mindset is underway. As an industry, we recognise that we need to tackle this issue together and cooperate to find joint solutions. We need to focus on the various benefits of plastic and on gaining public acceptance. Recycling plastic must become second nature. As has long been the case for metal and paper. It’s all about building trust.
CC: Plastic waste and marine litter are perennial issues. Do you see this as an opportunity or a risk for the industry and your company?
H: Good question! As a manufacturer of plastic recycling machines, we have a business model that is heavily affected by the issues of plastic and packaging waste. At the moment, these terms do not cause any offence. However, if the waste builds up and becomes a problem, people would begin to refer to it as “litter”, which, of course, is a term with clearly negative connotations. Our aim is to deal with the waste cleverly and sensibly so that we can avoid producing “litter” by turning recyclable materials into new, reusable raw materials. This means that we see the current challenges as opportunities with great potential. In fact, finding solutions is our mission. I have every confidence that we in the plastics industry can get a handle on these issues.
CC: Do you see yourself as a lone warrior in your value chain?
W: Far from it. At the start of our conversation, Mr Hackl explained how the situation has changed and the industry is now engaging in rational discussions. Something else has changed as well. A few years ago, each industrial sector focused solely on their own areas of expertise; everyone did their job but kept themselves to themselves. There was little interaction between the various parts of the value chain, even between neighbouring industries. Today, people are more open. They show interest in nearby processes, acquire knowledge for their own sectors, share insights into their work and actively participate in discussions.
CC: What exactly does this mean for plastic recycling?
H: The best way to answer this question is to look at the extrusion process. Effective sorting and washing have a positive impact on extrusion and the quality of the recyclate. Ensuring that quality remains consistent over a long period of time requires ongoing dialogue and coordination between the individual processes.
CC: The PET industry has been cooperating like this for a long time. The sector has been able to optimise its work by considering the effects of upstream and downstream processes. For example, lightweighting has become a reality and the industry has reduced its overall energy consumption and its CO2 emissions. Despite this, there is still work to be done in the PET industry.
H: Yes, PET is an exception. Everywhere you go, there are people working in line with PETnology’s motto of “connecting comPETence”. The PET industry has always been the trailblazer. It all began around 20 years ago when plant manufacturers began working more closely with converters and recyclers. This helped pave the way towards today’s PET bottles being relatively easy to recycle. As a result, closed-loop systems have become a reality. The situation is much more difficult in the area of polyolefin. Significantly more players are involved here, meaning that the challenges as well as the potential are much greater.
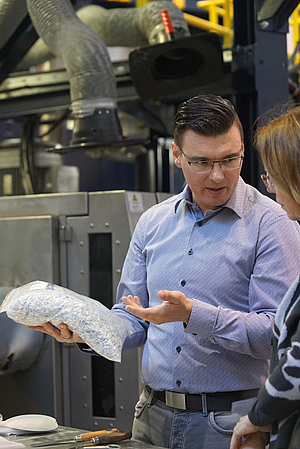
CC: Let’s talk about networking. These days, the technology sector is not the only area interested in this field.
W: This is an unbelievably positive sign and creates hope. As machinery manufacturers, we work closely with used plastic, but have relatively little contact with consumers. Instead, it is brands that shape opinions on the market.
CC: Are brands on the right track with their initiatives against marine litter?
H: Every initiative helps to draw attention to the problem. However, it remains to be seen whether all the initiatives are worthwhile and capable of fighting the root cause of marine litter. What’s important is that there are enough initiatives to bring people together. It is crucial to raise awareness on a community level.
W: Industries from across the supply chain are following in the footsteps of the brands by launching various initiatives around the world to encourage the development of collection systems and to help avoid plastic waste from “littering” our planet. It is crucial that collecting plastic becomes a standard global practice. And, of course, it has to be made clear that collected waste must not be dumped into our oceans and rivers. Whenever waste is collected, it has to be sorted. This needs to be stepped up a gear as well.
CC: We’ve already spoken about consumer confidence. A lot of plastic is collected, e.g. in Germany. Consumers here should be confident that they have done their duty and that their waste will be recycled effectively. Having said that, people are still unsure as to what actually happens to their waste.
H: When consumers think about recycling, they generally picture the mechanical recycling process. For them, combustion is not a form of recycling. However, before materials are actually reused, the issue of economic efficiency needs to be taken into account. Sorting companies are paid in terms of the weight of the input material and not the quality of the output material. Waste incineration plants do not like accepting mixed waste, i.e. residual and plastic waste, because the plastic has a high heating value and fewer tonnes of residual waste can be processed as a result. In the Netherlands, there is now a large waste management company that operates a sorting and incineration plant in parallel. This is a highly efficient way of processing residual waste. The proportion of waste to be combusted is reduced by sorting for and mechanically recycling materials like plastic and beverage cartons. Here, it all boils down to the quality of the separated waste and not the quantity. I believe that this is the approach we need to pursue.
W: The sorting process holds a lot of potential. The more accurately waste is sorted and the more likely it is to be of one type, the better the quality of the recyclate.
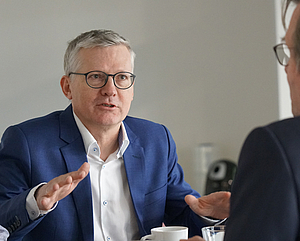
CC: How is digitalisation affecting your industry and is it making recycling more efficient?
H: Digitalisation is helping the various links in the value chain to work together more effectively. This is making systems more stable. It is an essential part of manufacturing recyclate to a reproducible quality. In my opinion, this is an important factor in ensuring that recyclate is recognised and used as a secondary raw material on a wide scale. We need to reach the same level as the raw materials industry by producing materials of identical quality over a long period of time.
W: This is an ongoing challenge, as the input material is becoming increasingly heterogeneous.
CC: From our conversation, I could conclude that the benefits of plastic packaging can be pitted against the issue of waste disposal. It is clear that this problem cannot be solved by the recycling chain alone. The situation is far more complex than that and could be compared to a mosaic in which more and more participants are acting as stones.
H: That’s a good image. Pieces of the mosaic are cropping up around the world and it’s time for us to make it bigger and more capable of bearing the load.
CC: Thank you for sharing your thoughts with us.
The comPETence center provides your organisation with a dynamic, cost effective way to promote your products and services.
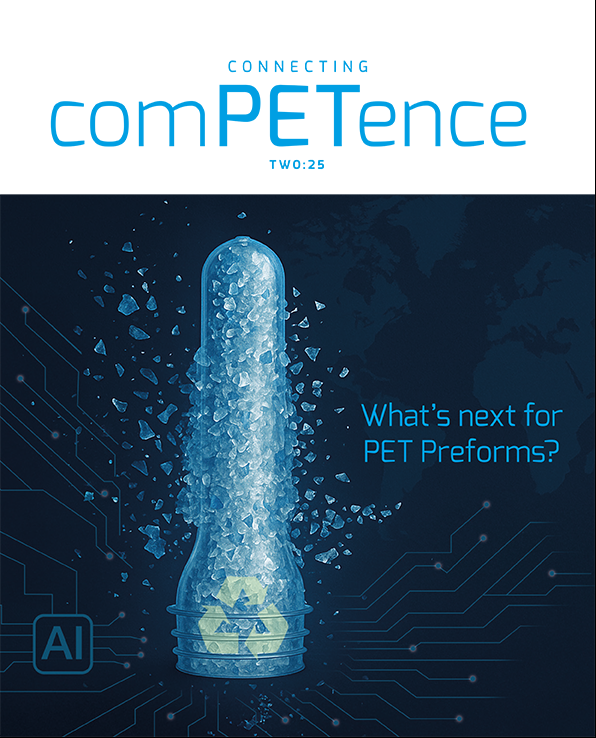
magazine
Find our premium articles, interviews, reports and more
in 3 issues in 2025.