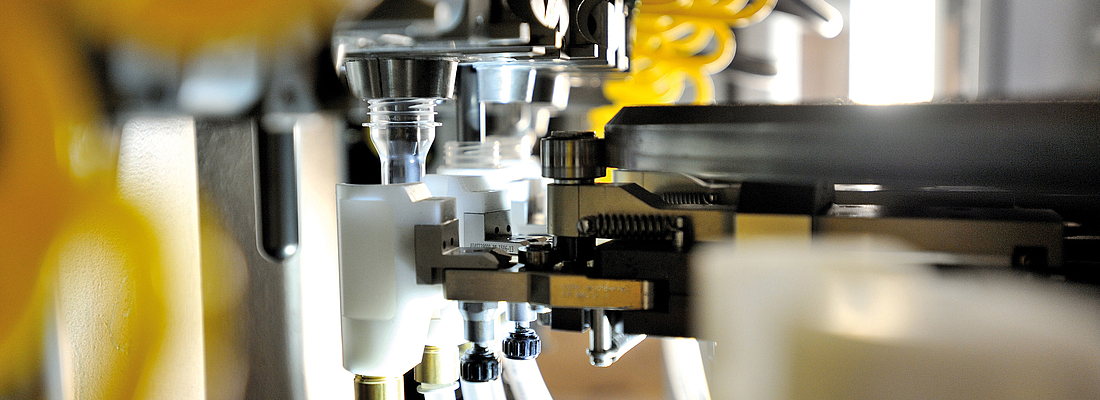
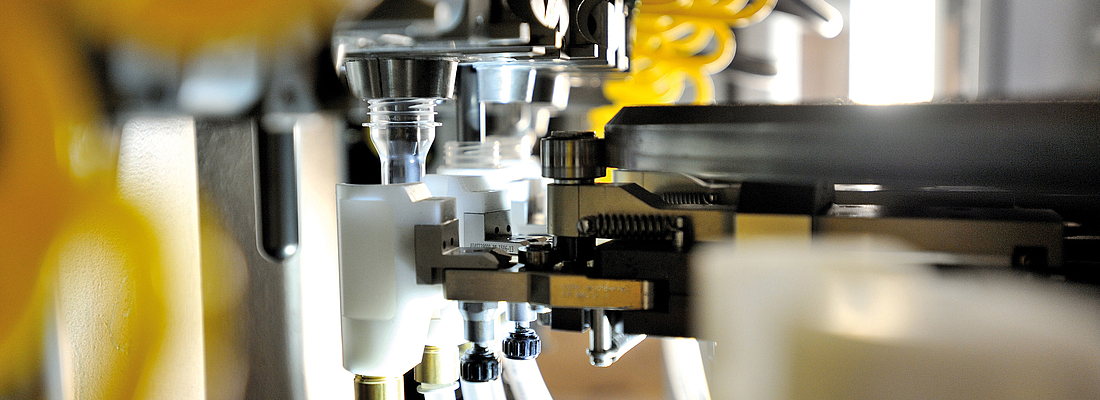
Injection-compression molding technology for prefroms
XTREME, injection-compression moulding technology
XTREME, injection-compression molding technology, can produce preforms that are up to 8% lighter than even the lightest injection molded preform—but without compromising on any key properties. More weight can be shaved off the body and base of the preform than ever before. The technology takes the shackles off developers’ freedom to create new and unique designs, and it is also easy to integrate into other systems, upstream and downstream.
Injection-compression molding overcomes the issue of filling molds with very thin walls, by having the molds slightly open when injection starts, and then closing them as dosing finishes. This means lower injection pressure can be used, lower clamp force is needed (which has the additional benefit of extending mold life), and there is less stress on the melt. All this means that acetaldehyde (AA) levels are reduced by up to 40%, and resin intrinsic viscosity (IV) falls far less: over 70% less in fact.
On top of that, the equipment runs at lower temperatures and consumes 10% less energy than an injection molding system with the same output — and it fits into much less space. A 72-cavity XTREME machine takes up just 34.5 m2, which is over 30 m2 less than SIPA’s own XFORM, one of the most compact preform injection molding machines on the market. XTREME is a clean machine too: it is the first totally oil-free high-output preform production system.
Simple, safe, sure
Operation is foolproof – mechanical cam synchronization of mold movements and preform ejection eliminates operator error for example. Flexible too: the mold carousel can hold molds for two different sizes of preforms at the same time if necessary. Inline total quality control is performed with cameras checking neck finish, body and gate, while an optical pyrometer measures preform temperatures.
The first XTREME system was officially put into operation at the Haruna, Japan plant of Suntory, one of the world’s leading drinks producers, in July 2016. SIPA and Suntory cooperated on the development of XTREME for many months. The start-up of the new plant was the culmination of a project that Suntory says succeeded in meeting all of its specifications and expectations.
XTREME SINCRO: integration with blow molding
The XTREME system can be integrated directly with an SFR EVO3 next-generation rotary stretch-blow bottle molding unit to form XTREME Sincro, the world’s first injection- compression-stretch-blow molding system. Once again, the system is compact, flexible and easy to operate, and has very low materials and energy consumption. XTREME Sincro produces bottles with extraordinary performance, but which are lighter than anything available on the market.
The XTREME Sincro embodies numerous advantages for bottle producers, combining the flexibility of two-stage systems with the convenience of single-stage system. The SFR EVO3 has a maximum output rate of 2250 bottles per hour per cavity, putting it on the front of the grid with the competition.
Minimal energy use
Integration of the preform injection-compression and the bottle blowing operations has a major effect on energy consumption. There is no need on the Sincro XTREME to cool down the preforms immediately after they are molded, and the need to reheat them just before blowing is much reduced. Conventional ovens with infrared heaters are replaced by small ovens that use highly efficient induction heating that is directed only at the areas of the preforms just below the neck.
Just like the XTREME preform molding system, the SFR EVO3 has a new mold changeover system that is quick and easy to use. It is also much easier to convert from production of cold-fill to hot-fill containers, too. This is because, while the heating circuit remains in the shell holder, the cooling circuit is now built into the cavity. Only a simple cavity change is required to switch from production of one type of container to another, while the shell holders remain in place.
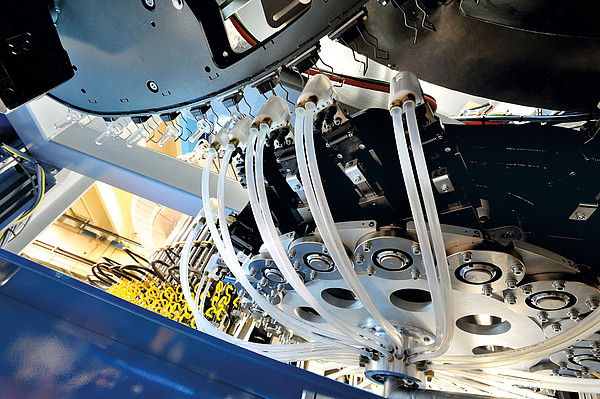
XTREME RENEW: upstream integration for RPET processing
XTREME has also been successfully integrated upstream with another ground-breaking innovation, the VACUREMA process from EREMA for treating recycled PET. XTREME RENEW, unveiled last year, produces injection-compression molded preforms directly from washed PET flakes, signaling the dawn of a new era in PET recycling.
In XTREME RENEW, food-contact-compliant melt produced by EREMA’s VACUREMA process feeds directly into SIPA’s XTREME preform production process, without the need for intermediate cooling and pellet production. The benefit of this direct processing is an enormous boost in energy efficiency, plus considerably lower thermal damage to the PET material. Compared to systems requiring intermediate pelletizing, recrystallization and drying of the RPET, with subsequent re-melting before injection, XTREME RENEW has a Total Cost of Ownership (TCO) up to 15% lower.
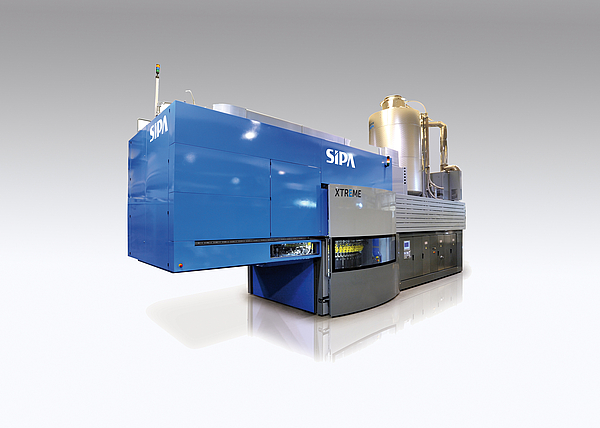
The comPETence center provides your organisation with a dynamic, cost effective way to promote your products and services.
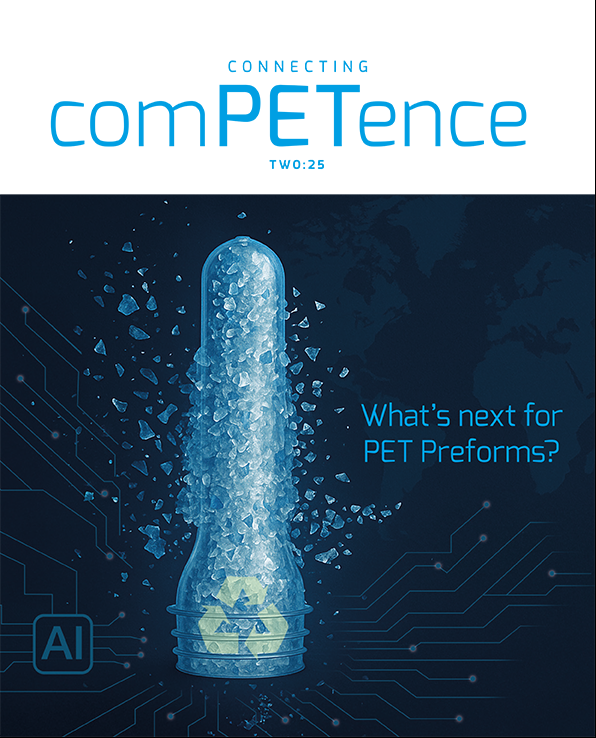
magazine
Find our premium articles, interviews, reports and more
in 3 issues in 2025.