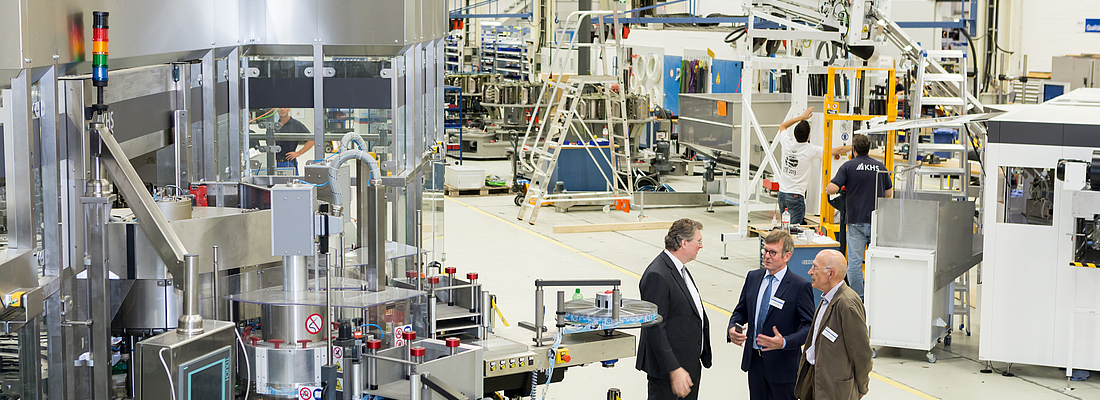
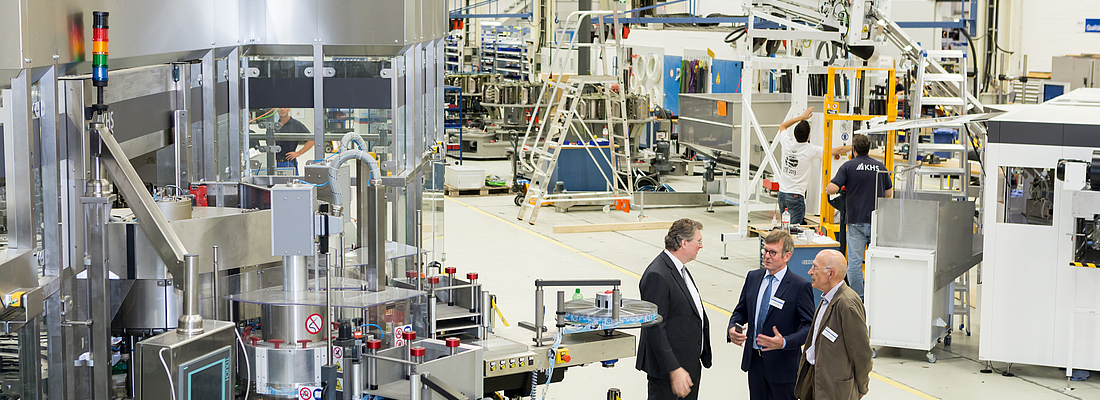
When talking about 40 years of the Hamburg company Corpoplast, the question arises:
What are the roots of this company? How did it all start? What did the competitive environment look like back then? Let us take a look back with an employee who was there at the start and has dedicated his entire professional life to the service of the company. - With this comPETence article, Prof. Dr.-Ing. Otto Appel congratulates Corpoplast on 40 years of excellence.
Corpoplast, Hamburg, 2015
Karl-Heinz Seifert brings the enthusiasm from our tour of the assembly halls into our meeting: the staccato beat of blow molders, the size of the machine, the coating system and the impressive block. We now sit relaxed in the office of Frank Haesendonckx, head of Sales and Technology at KHS Corpoplast.
Seifert is here to tell of the beginning of Corpoplast and its venture “stretch blowing”. The story told by Seifert in the next three hours, tells of the emergence of a successful technology, the story of an lengthy path, not only designing and building the machines, but within the company as well.
We are quickly transported back to the time when the engineering and technological basis for today’s PET stretch blower technology was created. The calm of this retired employee, his penchant for technology and how to deal with disappointment when things do not turn out as planned – all this gives us insight into the uncertainty of that time for this completely new technology and the project environment then. We then dive into the technical, technological adventure.
The story of Corpoplast began exotically and promised to be adventurous from the start. It is a story that wrote the history of technology and thus naturally a path that was not always easy. For this reason, we shall begin like this: Once upon a time, there was a company Heidenreich & Harbeck Werkzeugmaschinenfabrik (H&H) in Hamburg. H&H was looking for new opportunities. The business producing woodworking machines collapsed, and the business producing machine tools and lathes was under increasing pressure from lower priced competition. An idea was needed, a good idea for a business of the future. And so a small team was sent to new areas to look for “the king’s new clothes.”
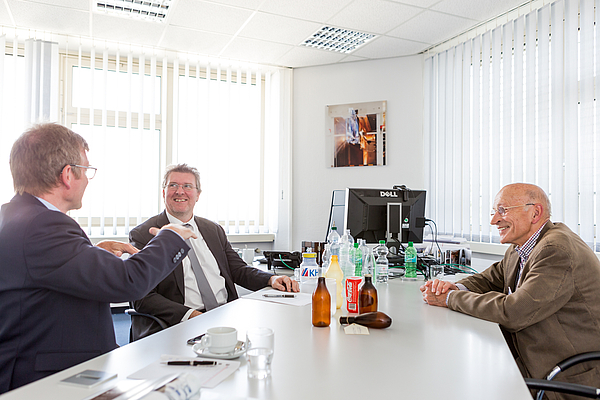
It is hard to believe, but the topics “preform dome” and “beer” in conjunction with plastic bottles heated tempers back in the 1960s as well. The plastic bottle was topic of conversation: For example, in 1967 at Anuga in Cologne and the K-Show in Dusseldorf: “Three balls – one beer”, went the whispers through the exhibition halls (see the bottle in figure 2).
Five times as lightweight, twice as stable and even cheaper – these were the arguments of the makers. But the environmentalists were already on the scene. The same old song? There was talk of them being “unbreakable” and of the “disposable bottle”. After a short message in the Handelsblatt in 1967, the plastic bottle was banned in Denmark.
The birth of a new technology, 1967
The rough outline of the task at hand at H&H was clear: the design and construction of a blow molder for the production of plastic bottles on the order of conventional filling machines. The first focus: beer. The idea was and still is fascinating: a lightweight plastic bottle for drinks.
The small “special machines” design group with Seifert was not universally well regarded. In the view of some other employees, the “playtime group” only generated costs, not revenue. It would be better if they return to the traditional work of optimizing machine tool production: “Earlier, everything was made of wood. Why plastic now? That is crazy, a utopia that will come to nothing in the end.” The “lathe group” was sure they would fail.
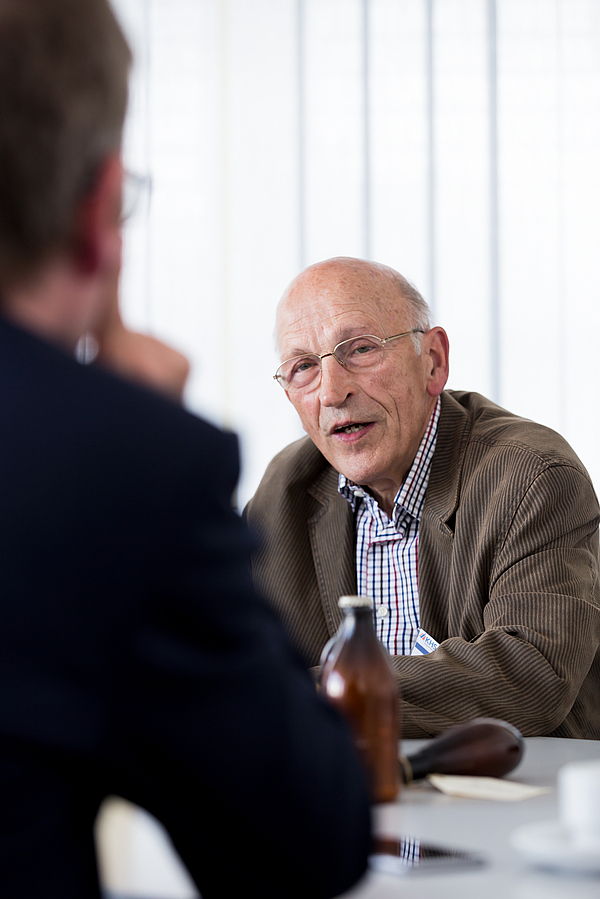
Instead of discouraging them, the doubts awoke the ambition of this “playtime group”. Nonetheless, development was necessary in a wide range of fields for the idea to work. New, complex topics emerged that needed to be addressed: plastic material, manufacturing process, equipment, markets, customers.
The development of knowledge was paramount. “Nosing around”, it was how Seifert called the visits to the process engineering department of the Reifenhäuser company in Troisdorf, Germany. Reifenhäuser was a customer of H&H and used their equipment for deep-hole drilling for extruder cylinders, for example. They were grateful for the help provided and the cooperation. During a visit to the technical center, the head of the testing department took a piece PVC pipe from a pilot extrusion system and using an inserted pneumatic needle, blew it from a molten state directly into an air balloon. He also mentioned in passing that this could also be performed at lower temperatures in the thermoelastic region, improving the strength and toughness of the material. And that was the historic moment for the technology. The term entered into Corpoplast history.
Seifert: “We attended conferences and trade shows, and I still remember October 1967, I was there with Rosenkranz at Anuga in Cologne and at the K-Show in Düsseldorf. The whole region was completely booked, there were no rooms anywhere. Somewhere in the country we found a room with a double bed in a guest house. We were very tired, but also highly motivated that evening. There was no way we could sleep. And as the night came to an end, the process was done, the Corpoplast process, as it was later named.”
The process steps (Fig. 1):
- Continuous extrusion of pipes made of hard PVC
- Non-cutting dimensioning of pipe sections
- Reheating the pipe ends
- Forming into preforms, by closing one end hemispherically and shaping the other to the later neck
- Reheating the preform body
- Blowing the bottle
The first test and laboratory facility was completed at the end of 1967. A heating jacket was used as a heating station for the first preforms, a very slow process from today’s perspective. The preforms were then blown to bottles on a hydraulic test unit.
Seifert: “This bottle is still around because my wife and I received it from colleagues as a wedding gift, filled with lucky pennies. The luck was meant for us, but the new project was able to use it as well.”
According to Seifert, it was amazing how such a small team with limited resources was able to advance such an important topic for the future. These key experiences, both positive and negative, have been invaluable for further development, which he wants to see for himself as well. And then the technology began to gather pace.
At this point of the conversation, you can practically feel the urgency to continue with the first draft of the production system and the first patent application. The objective for the first high-performance blower was production of 10,000 bottles per hour. And by the end of 1968, the basic designs for the BA2 (blow molder size 2 for bottles up to 0.7 l) were complete.
The project was becoming increasingly complex; the interdependencies needed to be evaluated in detail:
- The material: PVC, PAN, and then there was “this new” that was later recognized as PET
- The design and manufacture of preforms: from one extruded pipe and later by injection molding
- Blowing and filling the bottles
- The bottle properties and specifications
In addition to the technical and technological challenges, according to Seifert it was important to win over a conservative market. “At the same time, we also had to develop the market.” It was only natural, of course, to begin with the bottlers. Interestingly, the first to be approached were the breweries, although the large soft drink producers followed quickly.
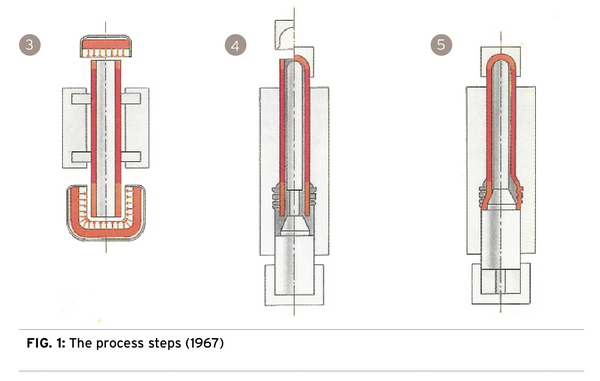
Hannover Messe, 1968
Reifenhäuser offered to introduce the sample bottles at the Hanover trade fair at its stand. The booth was manned with initial color brochures, about 100 sample bottles, pipe sections and preforms. Seifert: “The response was enormous, providing us with better access to material producers, but in particular processors and bottlers.”
1969 was the year of blowing tests, sample filling at practically every well-known brewery – and a year of tastings. Interesting events that the “lathe group” was also happy to take part in. The exotic project of the “playtime group” was looked at in a new light, and the team got the chance to provide arguments against “business as usual” and discuss the vision of the future.
Developing knowhow 1970
On the blowing side:
In the thermoelastic temperature range, PVC was a very sensitive material for blowing
- The accuracy requirements for the wall thickness distribution of the pipe sections had been underestimated
- Heating and energy input brought up many questions
- The blowing procedure had to be performed more slowly (installation of throttles)
On the filling side:
Not all filling systems were designed for a small and lightweight plastic bottle
- Pasteurization was a problem
On the material side:
With antioxidants, it was possible to achieve an improved oxygen barrier
- BASF attempted to improve the barrier with PVDC emulsions
Challenges from the market, Paderborn
At this time the Paderborn brewery brought a very light, somewhat squat glass bottle on the market, the so-called “snobby bottle”. The bottle was more stable than conventional bottles: In the annealed state, it was sent through a tin-vapor atmosphere, thus greatly reducing the surface tension. Of course, the glass industry continued to optimize its beverage bottles, which must be kept in mind. The core team once again sometimes felt like the old “playtime group”, in particular when doubts arose as to whether conservative beer drinkers would accept the plastic bottle. There were misgivings for the whole project.
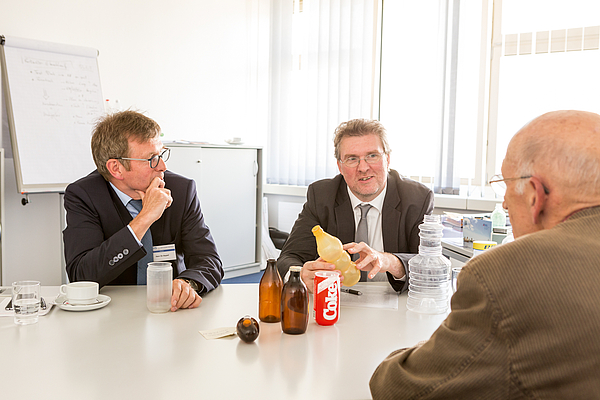
Corpoplast as a process name, Hamburg
At the end of 1969 the name Corpoplast was created as a process name. At the same time, BASF ordered the first test system – the first sales. 1970 the prototype was built, “the king’s new clothes”. It proved to be quite “unruly”. For a completely new machine technology, mechanical and electrical issues were unavoidable: typical “teething troubles”. But it was necessary to admit: Customization of the metaphorical clothes was still far away.
VPM, Düsseldorf
At the same time, it was important not to ignore marketing activities. The distribution company VPM Vertriebsgesellschaft Plastik Maschinenbau mbH (VPM) was founded together with the companies:
- Rheinmetall, Düsseldorf (conventional blow molders)
- Reifenhäuser, Troisdorf (extruders for pipe systems)
- H&H, Hamburg (with the Corpoplast program)
With the VPM headquartered in Düsseldorf, contact was made with competent companies such as Monsanto, Vistron, Owens-Illinois, Pepsico, DuPont, American Can as well as Japanese companies such as Dainippon Ink and Chemicals (DIC) and Nichimen, just to name a few.
PVC and beer, Munich
At this time, PVC as the raw material for beverage packaging began to cause the team increasing troubles. Due to its chlorine chemistry, PVC began to come under fire. In the United States, the PVC bottle was considered unsuitable for food applications. Since the combination of PVC and beer was still fraught with many question marks, bottling and shelf life were analyzed at university TH München Freising-Weihenstephan by Professor Drawert.
A question of survival, Hamburg
At this stage of site selection, a number of new material developments arrived from the United States. “They were practically breaking down the door”, explains Seifert “to use our experimental facility for testing purposes.” An important visit took place at the end of the year from PEPSI Co, Valhalla/USA and Reifenhäuser/USA. PEPSI wanted to go into business with disposable plastic bottles. Experiments were carried out with “Barex” and “Lopac”. In early 1971 a new material was considered. There was a lot of secrecy and many meetings with PEPSI, Reifenhäuser and DuPont. Suddenly there were code words for material types, like in James Bond films: MV11 for DuPont, M1, M2, M3. “There were mysterious clues that increasingly called our 0.3 l PVC beer bottle project into question. If these indications were to become a reality, without better materials and new potent users, we would be confronted with a question of survival for our new development.”
Major contract from Dainippon Ink and Chemicals (DIC), Japan
And then, Dainippon Ink and Chemicals (DIC) from Japan placed a major order for PVC: Laboratory machines and a large-scale plant for BA 2. The thought of delivering the large-scale plant to a distant, foreign land was intimidating. In the end, the order had to be cancelled by the customer: The Japanese legal requirements had not been evaluated in detail. It turned out that bottling mass beverages in plastic bottles was not allowed in Japan. This regulation has only been eased slowly over time. The major order was lost, but the cancellation costs eased the “pain” quite a bit.
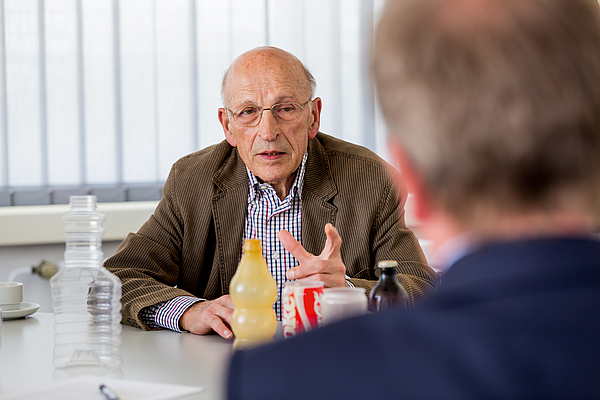
The mysterious material, USA
The DIC project had failed, but the projects for the United States were going well and appeared promising. The process and especially its potential attracted attention – worldwide. As a result Owens-Illinois (O.I.), then the leading manufacturer of glass bottles, was interested in blow molders for production of plastic bottles from PAN. The project with DuPont/Pepsi for 32fl.oz. (about 1.0 l) took shape. DuPont kept everything strictly secret. It was suspected that DuPont wanted to be more than the material supplier in the value chain. Due to the low material consumption and the resulting low margins, it was conceivable that DuPont was interested in selling the finished bottles to Pepsi themselves.
Seifert: “There was a confidentiality agreement: Even the smallest scraps of waste material had to be returned. At the time, we did not have the self-confidence and experience to design the confidentiality agreements in our favor.”
But the secretive project also had its advantages: The on-site development work with Jack Nyquist, project manager at DuPont, turned out to be an extremely positive experience. Professionally very technically oriented, privately he enjoyed the finer things in life: a French horn player in a classical orchestra, a pipe smoker and opera fan. “We invited him to “Lucia di Lammermoor” by Gaetano Donizetti, with the famous Australian soprano Joan Sutherland. He was impressed, and we shared an extraordinary experience together.” Despite all efforts and extensive testing, by 1974 we received no recommendations for the optimization of the blowing process. From him all we received was “it’s better” or “it’s worse”.
In December 1974, the first PET machine fulfilled the acceptance test conditions. “We celebrated the business and drank champagne in cut-off PET bottle bases.”
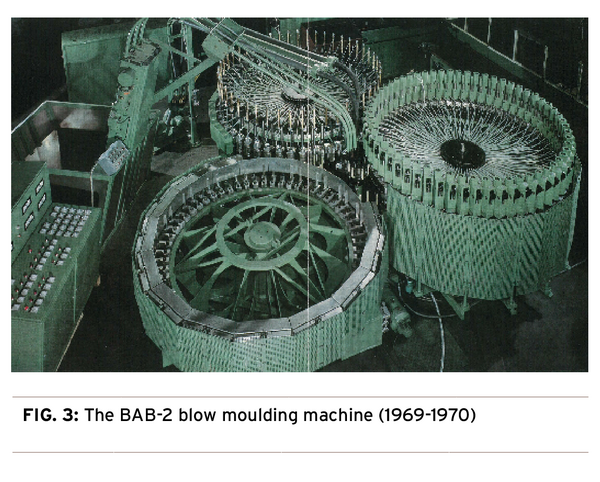
Krupp Maschinentechnik, Essen, 1980
In subsequent years, the plants were further optimized. Significant performance improvements were achieved through intensive mold cooling and improved heating. The performance of BAB-4 increased from 2,500 to 4,000 b/h – it then became the B-40. This performance level was an inspiration to the professional world at K ’79. Seifert: “We celebrated a small victory; it felt like a breakthrough.” At K ’79 rumors also circulated about an imminent corporate takeover by Krupp. Kautex had already been bought. With the successful K-Show in the rear-view mirror and the economic success, Corpoplast could finally enter the next year in a relaxed state of mind – under the Krupp flag.
B80 – the draft horse
The first designs for the B 80 were begun in 1982. The new machine with 10 blowing stations and a production capacity of 8,000 b/h for a 2,000 ml bottle was presented at K ’83 and was an attraction for both customers and competitors.
Seifert: “The B 80 was our best horse in the stable. From 1983-1996 we sold 150 machines. The machine brought confidence and increasing sales.”
B 160-B 200, 1982
In 1982 a blowing machine designed and built for O.I., Brunswick, entirely geared towards small bottles for the US market. The preferred bottle size was 0.5 l. On 18 stations the B160 achieved an output of 15,000 b/h. The larger B200 supplemented the portfolio with a capacity of 20,000 b/h. But according to Seifert they neglected to design and build larger machines with capacities up to 40,000 bo/h. This was partly due to the machine concept with the closed mandrel circulation. They were too concerned with the affects of high performance and the associated centrifugal forces for the mandrel, which is no longer used today.
The standard program was now very good – both technically and economically. They were now open to new challenges. The ambitious goal was to take a new technology from the laboratory scale to the production level: the pressure-resistant PET can.
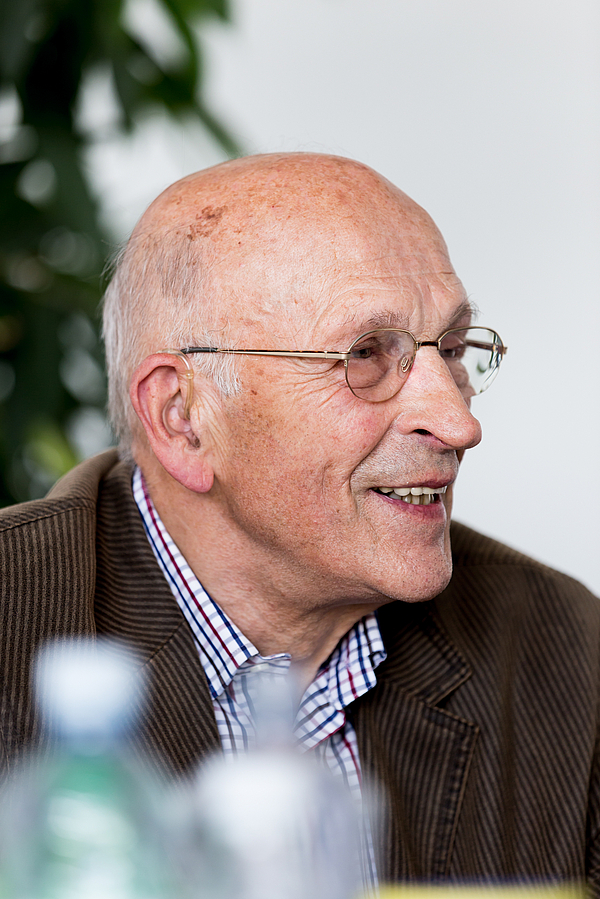
Plastic canmaking, USA
The name said it all – Petainer. A process developed by PLM made it possible to manufacture pressure-resistant PET cans for carbonated beverages. The Petainer company, founded by PLM und Metal-Box delivered the process technology and Corpoplast developed the production machine. Three process steps were necessary to make the pressure-resistant, heat-set PET can without a blowing process. A contract with Corpoplast sealed this exclusive machine development for PET-cans using the so-called PETainer process – a highly demanding engineering and technology task. The goal was to produce 165-200 cans/min. The weight was 21.5 g, just 17% of the aluminum can. The first lightweight optimizations were not long in coming – target: 18.5g. The development phase with PLM ran from 1982 to 1986.
At the end of 1986 the system went to the USA, where Petainer built the pilot production with joint venture partners, mainly to supply Coca-Cola. After considerable initial problems, a first major market test by Coca-Cola was successful.
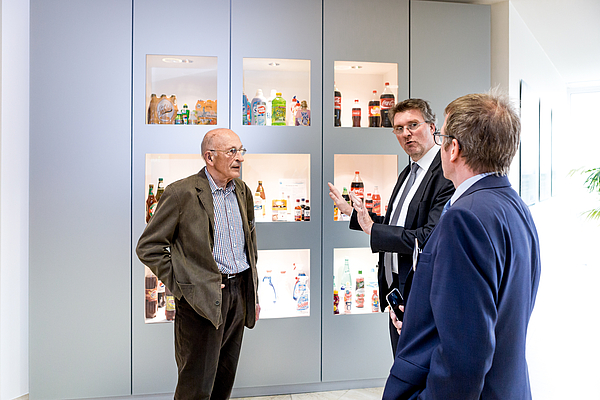
The big BUT
The aluminum industry, led by Alcoa started a massive campaign of resistance, which was not without effect: Coca-Cola got out. Because no other customers could be found, Corpoplast had to write off the high development costs without good prospects for using the expertise gained elsewhere. Seifert did not fail to mention that all Corpoplast technicians regretted this turn of events.
There was some hope for the technology again and the prospects for the PET can were looking better again when Yamamura bought the line in 1989 and installed it in Japan. But regulation prevented production yet again: PET beverage bottles were allowed starting at a volume of 1.0 l. No changes to the regulations were expected in the foreseeable future. That was the end for the PET can, in terms of the hope for large scale production.
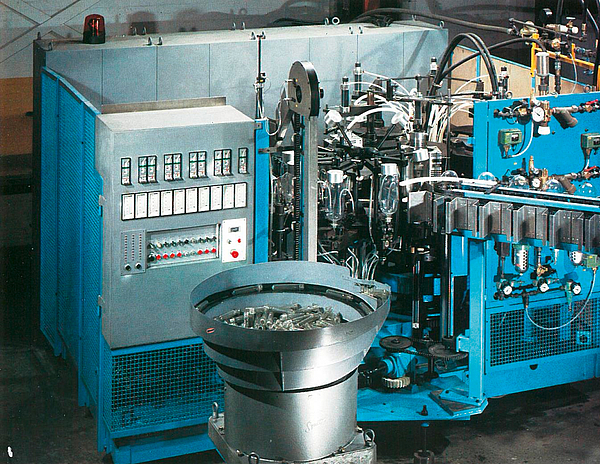
Corpotherm – the thermostable bottle, Japan
A new technological challenge followed the Petainer project – Corpotherm. Seifert becomes animated; he has to provide some background here. The topic was thermostable PET bottles for hot filling and pasteurizing. The market launch was successful in 1989, and it was possible to sell a plant directly to Korea. The entire line consisted of three machines and yielded a production capacity of 6,000 bottles/hour:
MT-60
Crystallization and forming the neck of the extruded preform
B-60
Standard stretch blow molding of a container with slightly smaller dimensions than the subsequent heat-set PET bottle
BT-60
Blowing to the final bottle in a hot blow mold with pronounced stabilizing contours and vacuum resistance
The bottle mouth was heated for precise forming with IR radiators to the crystallization region. Heating was accompanied by a whitening of the material, as large crystalline structures were formed, which lead to a thermally more stable thread. In the B-60 blow molding machine, blowing the pre-bottle form takes place in a cold, water-cooled mold. Thermostabilization occurred in the final process step. Here, the biaxially oriented material of the preformed bottle body was blown into a form heated to about 200 °C. In the thin bottle wall, the material crystallizes into a fine spherulitic structure which transmits the light more or less unhindered – the bottle wall is transparent. Before or during the opening of the blow mold, the bottle was cooled inside with a water spray – an unfortunate solution at the end of the process in terms of machine technology and bottle sterility. A problem lay in the weeds.
Seifert: “The first line went to Korea. And almost exactly 1 year later, despite the known problems, we sold another line to one of our main customers: Tong Yang Nylon (TNC), Korea. The approval testing was just before Christmas. At 10:00 pm we stopped the testing and went with our customers to the company Christmas party. The rude awakening for both lines: Despite significant improvements, it was not possible to achieve stable and continuous production in compliance with all specifications.“
Today, according to Haesendonckx, – after nearly 50 years of experience – the complexity has not necessary become smaller, rather it is on a different level. This expertise is now more widely available, not least because of “wandering” experts. Looking around, Haesendonxcks includes himself and me in this group.
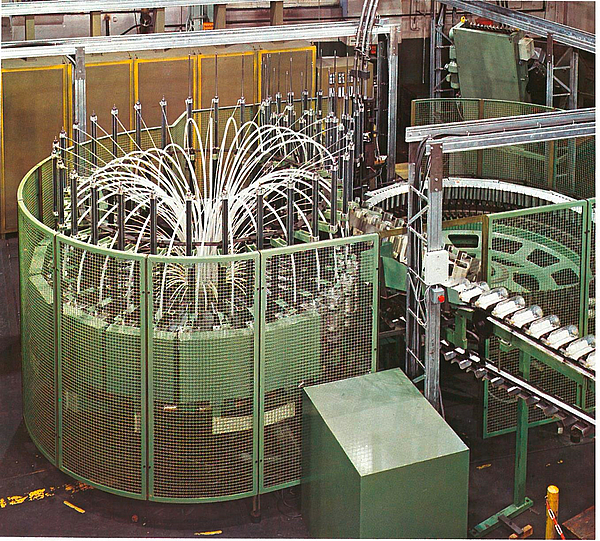
Plasmax-Program, Hamburg
Corpoplast has performed pioneering PET work in many areas. Haesendonckx sees this as part of the corporate culture of Corpoplast. “It is important to take a change sometimes and give things to develop on the market. This requires patience, perseverance and a conviction that the technology will succeed.“ He thinks of Plasmax and first talks about his experiences with multi-layer preforms – the integrated barrier – and that it took over 10 years until the market accepted multilayer preforms. One must always overcome the barrier in front of the barrier. “A great deal of investment was required to develop the Plasmax technology and when users today think ahead a bit, in many areas there is no way around Plasmax technology – the plasma coating is no longer an option in the future, it is a requirement.” The systems are in operation in Europe, USA and Japan with a coating output of 40,000 b/h, and 48,000 b/h are even possible. The significant progress that has been made in the system lie in the area of the vacuum (faster generation and dissipation) and in the process to achieve the elasticity that is required for CSD bottles.
Blomax-Program, Hamburg
For stretch blow molding, explains Haesendonckx, there exist two fundamental topics: sustainable and cost-effective packaging. The two belong together, in his view. The development topics from recent years show this clearly: energy reduction, performance enhancement, lightweighting and recycling. For many years, everyone was satisfied with the performance of blow molders – from an initial 200 bottles per hour and station up to 1,200 bottles per hour and station. From an engineering standpoint, it was an incredible development. About 10-12 years ago, the competition on the market went in a new direction: A race for higher station output began.
With Blomax Series III compact, according to Haesendonckx, Corpoplast set a new benchmark of 1,800 b/h and station. Followed by Series 4 with a capacity of 2,000 b/h and station, today 2,200-2,500 b/h and station can be produced.
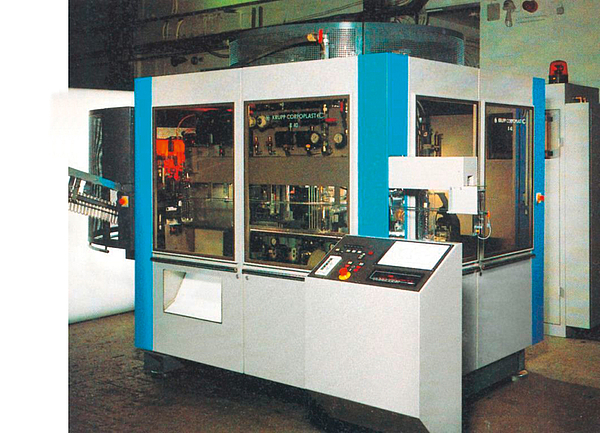
We take a moment to reflect: Is the charm of this technology slowly lost? Are all those involved obsessed? How does our industry define itself today? We talk about complexity, also in comparison to the beginnings. Today, there is an interplay of mechanics, control, preform design, materials, bottle design, base design and other factors, explains Haesendonckx; this makes it difficult to make it clear to a customer why differences exist in the output of the systems. We agree: Earlier, the technology was more “forgiving”, there was more free space and a larger process window. For today’s high-performance systems, everything must fit perfectly in each area to achieve economically efficient production.
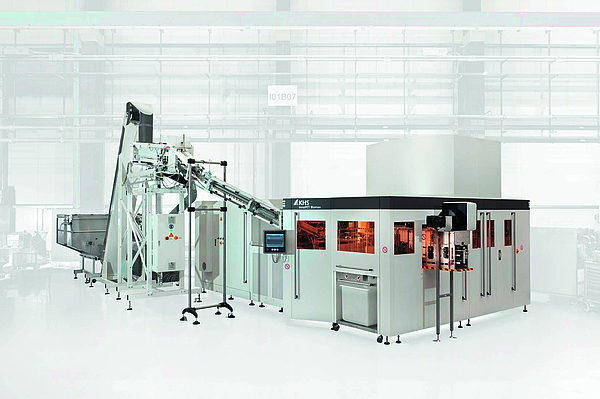
Two examples
- Today preforms are extremely light. The dynamic pressure due to gravity is no longer sufficient to guarantee a secure feed of the preforms into the machine. A new, active transport system is needed at the unscrambler in order to move 80,000 or even 100,000 preforms per hour.
- Today the stretch rod is cooled to have a positive influence on the base stability.
All this, explains Haesendonckx, requires a greater number of monitoring and quality systems on the blow molders along with high preform quality. In his view, this is exactly where the problems lie today. Today as before, mastering complexing means mastering fluctuations in quality.
Block concept - TriBlock, Dortmund
Compared with the early days at H&H, Corpoplast is no longer the “black sheep” but rather the “golden child”. Stretch blow and the coating technology complements the filling and packaging technology segment of the KHS GmbH perfectly. The successful integration of Corpoplast into the KHS Group is documented beautifully through the machines themselves: The first TriBlock - Blomax 18 blow molder, 2 station labelers and KHS filler. Buffers and singling units are thus eliminated, and from a control perspective, everything is driven by servo motors, explains Haesendonckx, and the pre-glued label can handle the expansions of the CSD applications. The labeler before the filler – i.e. no condensate at the labeler. The blower has arrived in the line.
The lightweight bottle, Hamburg
The idea – the lightweight plastic bottle – remains both impressive and demanding. We left many topics unaddressed and a good deal unwritten – it would have been too much. While we focused on the past – we know full well the importance of mastering future challenges and shaping the future. The experience gained, the customer requirements and competition in the market will help.
Article in pdf format
The comPETence center provides your organisation with a dynamic, cost effective way to promote your products and services.
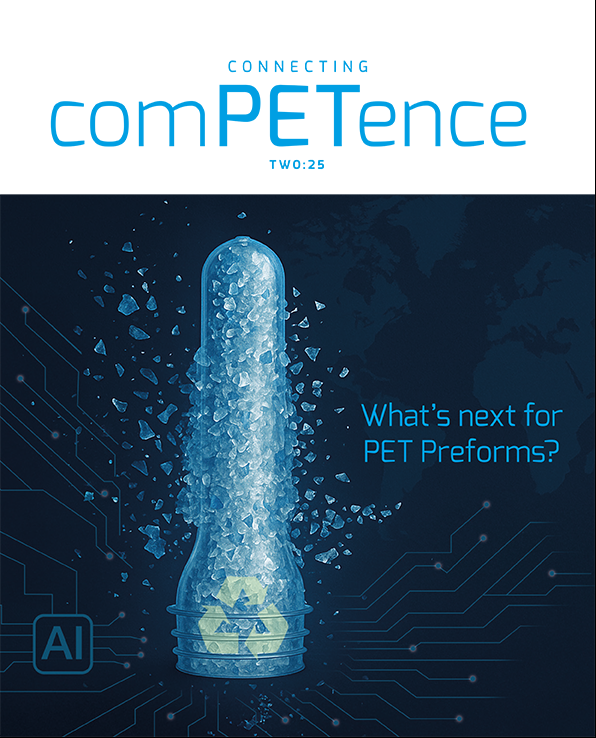
magazine
Find our premium articles, interviews, reports and more
in 3 issues in 2025.