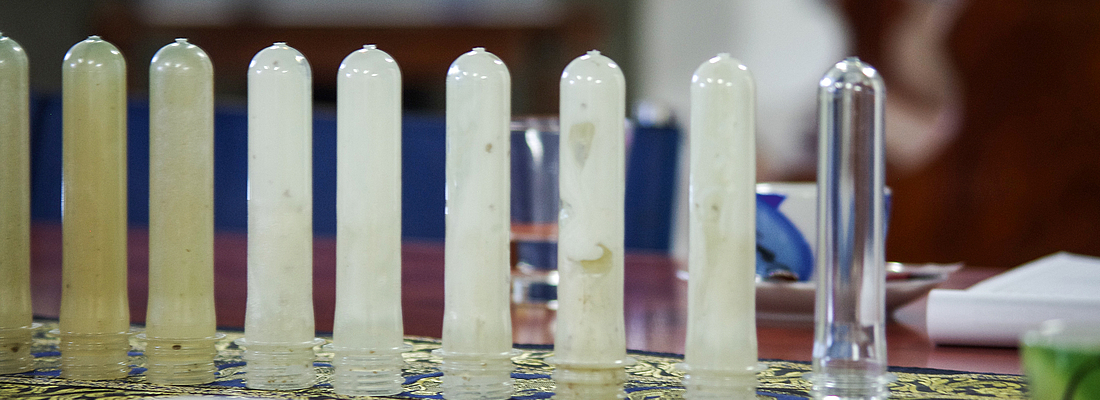
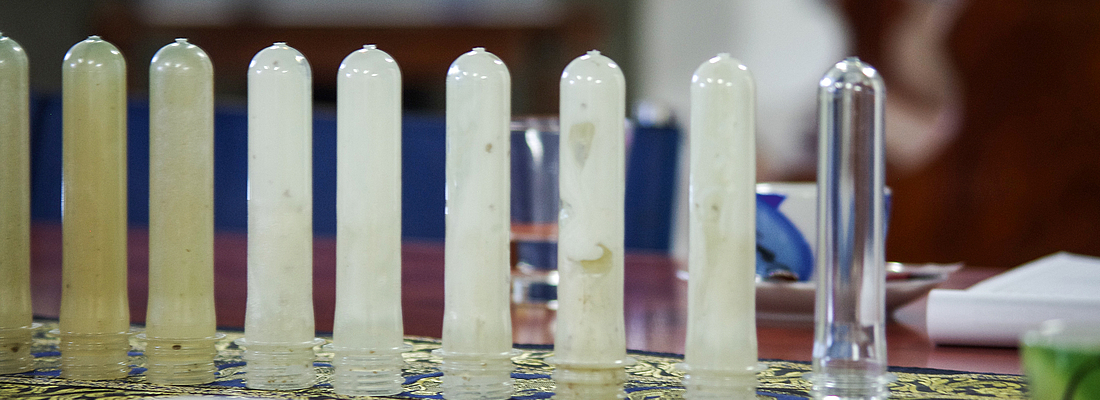
When it comes to packaging for food, pharmaceuticals, and personal and home care products, packaging manufacturers see frequent colour and material changes, especially for small lot sizes, as a necessary evil. Reducing downtime is the top priority. This involves not only optimising the production sequence with respect to colour and material changes, but also minimising machine downtime due to required cleaning.
Shortened cleaning times do not just optimise production, they also reduce waste and lower costs. In order to shorten cleaning times, a purging compound must be used. We wanted to learn more about this material and the markets, so we contacted Ultra System in Martigny, Switzerland, and requested an interview. Shortly before Christmas, Renate Bever and Paolo Balagna warmly welcomed us to the company with a delicious cup of Swiss coffee. Before coming to the real subject of the interview, we spoke a bit about Ultra System itself – which can perhaps be best described as a family-run company in which some things can still be communicated with a glance.
When was Ultra System founded?
Bever: Mr Balagna founded the company in 2003 as Ultra System Italy. At the time, I owned a small injection moulding company that was specialised in preforms. Today I can say that I was my first customer. We tried out Mr Balagna’s material back then and we were impressed. I enjoyed working with the material, joined the company, and in March 2004, we founded ULTRA SYSTEM s.r.l. in Italy, with the goal of carrying out research, continuous development and production of purging compounds for cleaning plastic material processing machines. At that time our production started to be changed from craft to industrial.
What did you find so appealing, Ms Bever? It’s not as if the whole world is talking about purging compounds.
Bever: It’s true, purging compound is certainly a niche product and that is precisely what appealed to me. Although the material and its production is certainly challenging. This
is partially due to the constant colour changes and customerspecific requirements, which are taken into account in the development of the carrier resin and the actual purging compound. Different markets such as the automotive market, electronics, pharmaceuticals, and consumer and household goods have additional specifications, although in the context of the packaging sector, it is particularly important to point to the requirements for approval for use
with food (CEE, FDA).
What has changed since the company’s beginnings?
Bever: In 2004, our company produced a total of three tons of material. In 2005, I recall that turnover was seven times compared to 2004, with a total production of 20 tons. In 2009, we produced 60 tons, and today – thanks to careful expansion in the global market and the establishment of new production sites in the USA, Russia, Thailand and Brazil – annual production is around 400 tons. This amount includes both ready-to-use products as well as different types of concentrate which are sent to the USA, Russia, Thailand and South America, where they are mixed with the different carrier resins. So we can estimate our total worldwide sales of ready-to-use products at approximately 1,200 tons. We have continued our development as a “family-run” company and currently send about 50% of what we produce to Europe.
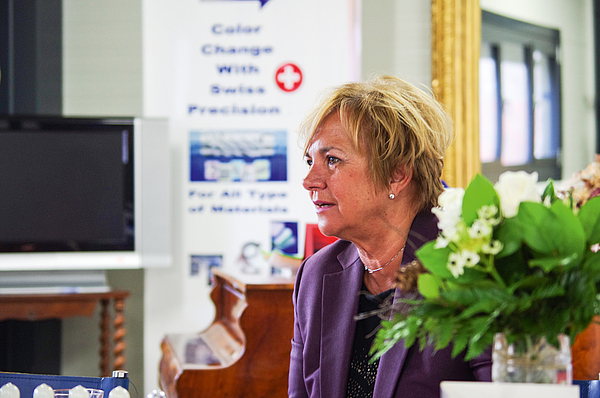
Let’s turn to the use of purging compounds. Where are the problems for users? It is ultimately a question of time, isn’t it?
Balagna: Here we should perhaps distinguish between the products themselves and the lot sizes. It makes a difference whether I manufacture containers in small series, e.g. in a single-stage process, or whether I make millions of one and the same preform. Particularly in the packaging market for the household, cosmetic and health care sectors, products are often becoming smaller, and manufacturing products for the warehouse only makes sense to a limited extent. In other words, the focus is on just-in-time production with minimal warehouse stock. For production, this means frequent changeovers. The main problems associated with this are, for example, black spots which appear when switching from one plastic resin to the other, due to the difference in processing temperatures, black spots and stripes in preforms, caps and films, or gel particles in the product. You could also say that these are the underlying causes of the real problem, namely the long downtime required to safely eliminate these issues.
Let’s talk a bit about the special challenges of the packaging market.
Bever: For us, the packaging market means caps and closures, bottles, containers, canisters, blown film products, cast film products and, of course, preforms. In these segments, colour changes are typically at the root of any problems. And we have the solution. It’s important to take a very close look at the processing equipment. And then, to put it simply: “To purge or not to purge, that is the question.”
In other words, sometimes the melting unit can be cleaned quickly and sometimes the mould causes problems and sometimes there are issues with both?
Bever: Indeed, each case is different and we have to look at the production processes very carefully – especially with more complex applications such as multilayer preforms. For example, when processing PA as a barrier material, one potential problem is that PA can burn in the hot runner. Eliminating deposits inside the hotrunners is not easy and the decomposition products of PA attack tool steel. With regular purging, we can eliminate this 99% of the time.
Balagna: We once had a case where it took 12 hours to clean the machine when switching from black ABS to natural ABS. We managed it in 40 minutes. In another case, we were confronted with a situation in which the injection moulding machine for preforms had been cleaned and after ten shots, stripes were still appearing. Sometimes cleaning the plant without purging compound took 20 hours, with production repeatedly starting and stopping. The problem: some isolators in the hot runner were broken and had not been replaced during maintenance. It costs perhaps 200 euros to
change the isolator. Today, the mould could be cleaned in five shots with our purging compound. Think of the costs that could have been saved! We understand the challenges of the plastic industry and that drives us to further optimise our products.
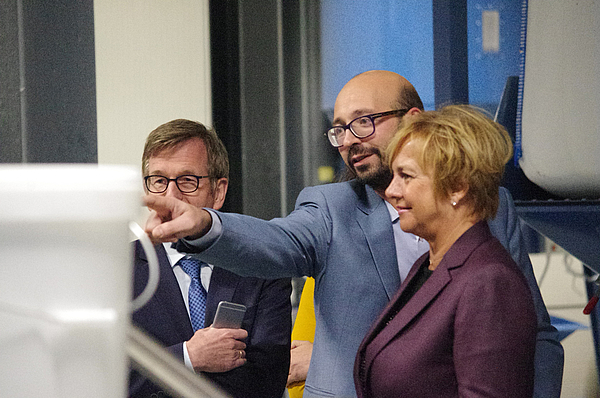
Does adding recycled material lead to more problems?
Balagna: Yes, it does lead to more problems. I make no secret of the fact that, in my opinion, especially with PET, recycled materials should be used for other applications than 100% bottle-to-bottle. Textiles, filaments and strapping applications present excellent opportunities for the use of recycled materials. In the future, PLA contamination will make this even more difficult. Recycling polyethylene again and again is no problem. But how does this work with PET for food and beverage applications? This is a question with no answer in my opinion. For example, when we recycle PP, we don’t know which sector it comes from. Perhaps it was once used in the battery of a car – and then we use it for food applications? It’s impossible to analyse each particle of granulate. You can only analyse a fraction of the whole. If we want to recycle properly, I think we are facing a transition in our markets.
How does your purging material work in the cleaning process?
Bever: The expertise behind our products is not just in the individual components, but naturally also in the manufacturing process, where process control is particularly important for the cleaning power of the end product. You can’t imagine everything that figures into the production of our compound, nor do we want to go into this in detail. Our purging compound is currently in its fifth generation – it is the result of continuous development which draws on a wealth of expertise.
Balagna: One important point is that our material cleans at the processing temperature of the previous production run – there is no need to wait or to allow time for the product to soak. When our Ultra Plast purging compound is melted, the mixture of the various ingredients in combination with the temperature triggers a chemical reaction which causes the material to expand, and this is, in part, what is responsible for the cleaning. Our compound doesn’t contain any solvents, abrasive additives, acids or liquids that could get into seals or affect the inner components of the mould.
Let’s talk about the economic benefits. If we take the examples you’ve provided, it seems like there’s no way around the use of purging compound?
Bever: Yes, that’s right. A customer once told me that buying purging compound is like going to the dentist – you have to do it sooner or later. But the economic benefits are obvious. We have figures from practical experience for all applications – whether canister, film or cap production. Without getting into specific cases, when machine downtime, the materials used for the cleaning procedure and other factors are taken into account, savings are estimated between 60% and 85%, according to the individual cases. It’s worth the effort. We are happy to run a test with the customer so that they can see for themselves.
Mrs Bever, Mr Balagna thank you for talking to us.
The comPETence center provides your organisation with a dynamic, cost effective way to promote your products and services.
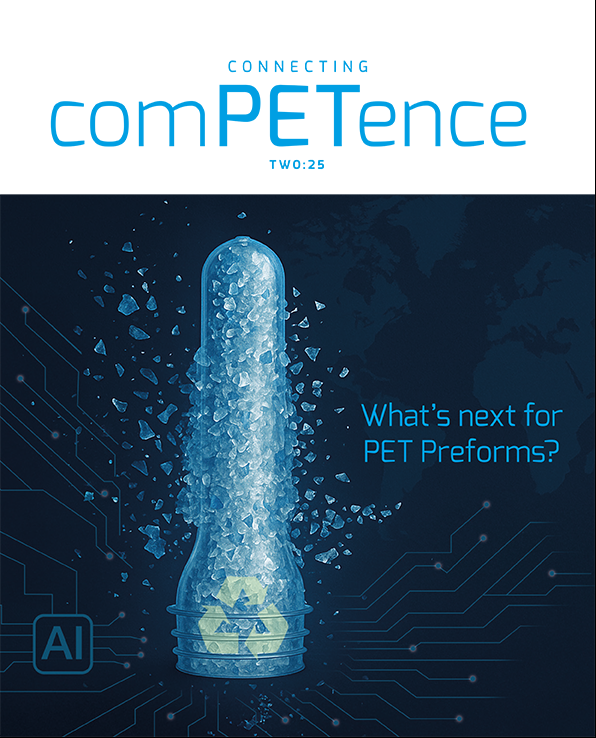
magazine
Find our premium articles, interviews, reports and more
in 3 issues in 2025.