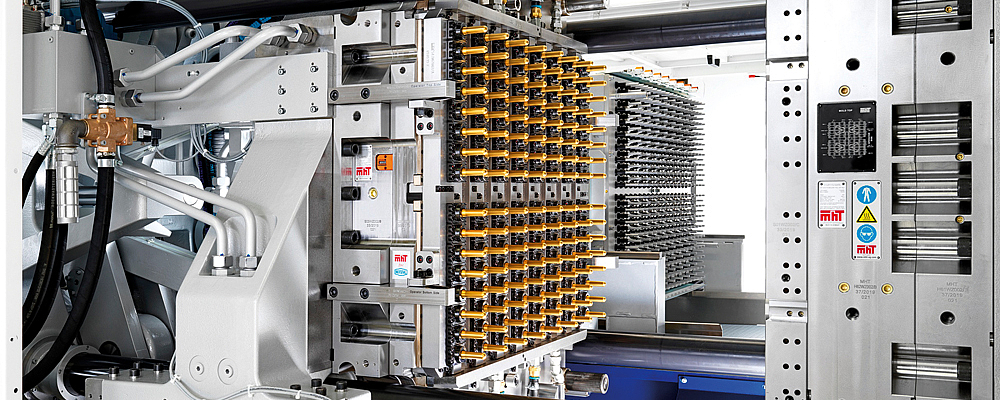
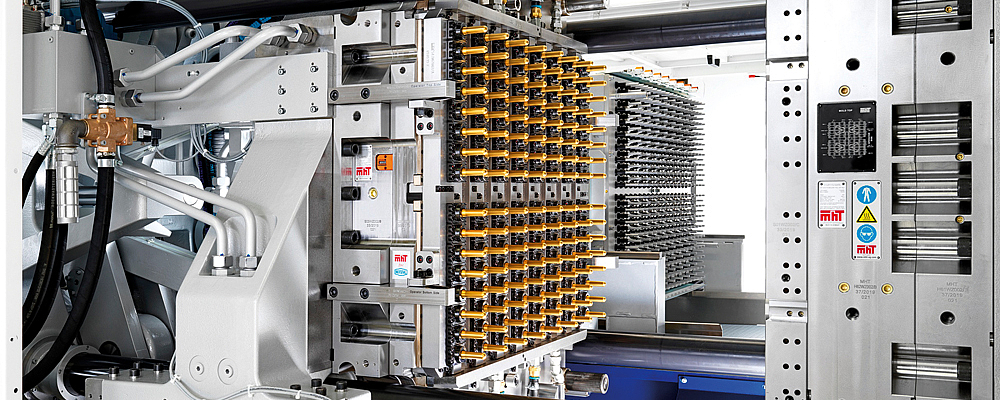
Preform Moulding
MHT AG certifies - The new NETSTAL PET-LINE with side-entry shows comprehensive compatibility
In injection molding systems for PET preforms, the machine and mold components must be optimally matched in order to reliably avoid potential performance gaps.
In the development of the new PET-LINE with side removal, NETSTAL has therefore cooperated closely with mold partner MHT from the very beginning.
Today, users benefit from a particularly powerful system that is characterized by its high speed, outstanding precision and the lowest energy consumption on the market.
In September 2020, NETSTAL presented its game changer to the market: The new PET-LINE now also offers users with sideentry molds a suitable injection molding system. The high output, in combination with the best energy efficiency, does not yet represent all the innovations that the new system offers. It features a modern control system, operated via the central touch display, which can be used to control and optimize all functions of the networked system, and a new screw design that enables recycled PET types to be processed even more efficiently. Right from the start of the brainstorming process for the new NETSTAL PET-LINE with side removal, it was clear that close cooperation would be of great importance. MHT AG from Hochheim am Main, Germany, whose core business has been in the side-entry business since its foundation in 1996, was happy to contribute to the success of the complex project with innovative suggestions and comprehensive know-how.
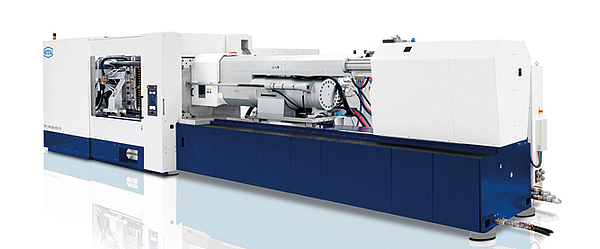
Tool and machine as a symbiosis
“From the very first day, our central development goal was to create a symbiosis between machine and mold.
Our new PET-LINE with side discharge improves the overall energy efficiency by another 7% compared to the previous series”, says Stefan Kleinfeld. The reasons for this are not only to be found in the familiar 5-point double-toggle design of the clamping unit, which is now driven purely electrically, or the recuperation of kinetic energy.
''For many years already, NETSTAL machines have stood for the lowest energy consumption in the market. Our new PET-LINE with side discharge improves the overall energy efficiency by another 7% compared to the previous series.'' - Stefan Kleinfeld
Likewise, a variety of optimizations have a clearly positive effect on the energy efficiency of the MHT mold. For example, there is improved heat dissipation from flow from the sprue to each individual cavity. The result offers users numerous advantages: “We are very pleased that NETSTAL has provided us with the high number of hot runner zones. This means that our optiRUN is now also available for the new PET-LINE. In combination with the PETX screw, it shows excellent performance in the AA-level values”, Christian Tilsner, Technical Director at MHT, is pleased to say. As a result, there are enormous cost advantages for manufacturers. “One customer was able to optimize the process for a sensitive product, which is processed with 50% rPET, to the extent that a reduction of the maximum AA values to a very low 1.69 ppm was possible. The resulting savings of 30% AA blocker pays off significantly over the year with more than €100,000”, adds Stefan Kleinfeld.
To investigate the performance of the optiRUN in combination with the new PET-LINE, the developers carried out various short-shot measurements. The results show a stable cavity pressure curve, which ensures precise filling of the molded part (fig. 1).

Convincing energy efficiency combined with optimized cooling
“For many years already, NETSTAL machines have stood for the lowest energy consumption in the market. All contouring components due to the adaptation of serial and parallel cooling, as well as a saving in the amount of cooling water used. This results in a reduction in the required pump capacity in terms of flow rate and pump pressure. A basis for the improved cooling of the preforms results from the use of optimized connection configurations for the cold and hot mold side as well as the post-cooling unit. “The separate cooling circuits now enable us to design the mold ideally. The thinnest possible wall thicknesses in the molded parts, combined with large cooling surfaces, further increase the cooling rate of the preforms. At the same time, we reduce the risk of preform defects, sink marks or hot spots”, explains Christian Tilsner.
On the hot side, improved insulation of the hot runner plates works in several ways: The cooling medium inside the injection mold absorbs less temperature from the hot runner system. On the hot runner side, users can dispense with a constant supply of escaping energy to maintain hot runner temperature control. It turns out that it is possible to increase the cooling water temperature with the result of maintaining the high quality of the preform. The newly designed, integrated hot runner control system of the new PET-LINE - with a significantly increased number of control zones - ensures constant temperatures and further energy savings. The advantages of the optiRUN are thus fully exploited.
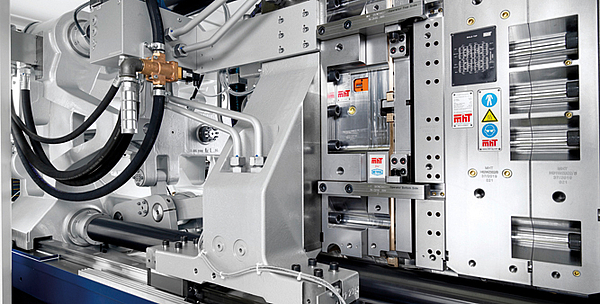
Flexibility of the preform design grows
Even at first glance, the most striking innovation of the machine catches the eye. The addition of a side-entry removal offers users versatile advantages. Not only is the full compatibility with existing side-entry molds and post-cooling stations convincing, but also the reduced installation height of the removal unit.
Tuned for increased output, the molds of MHT AG also benefit from the innovations. Thanks to the laterally retracting removal unit, NETSTAL enables a larger mold cavity distance to be realized in the horizontal direction. Where previously there were limitations with regard to the diameter of a preform, the optimized mold cavity distance now offers an extended travel path for the slides. This offers increased flexibility in the design of large preforms as well as the guaranteed use of the many advantages of a mold cavity with closing cones on both sides, the so-called core or care-lock design.
Removal and cooling - from inside and outside - in multiple stages using a single platen effectively multiplies the production output of the redesigned machine-mold symbiosis. “The independent plenum allows easy coordination between MHT’s patented coolMAX preform internal cooling and removal”, says Christian Tilsner. To further improve cycle times, the cooling air flow in the coolMAX has been split. As a result, the preform body and the thread area are cooled down separately from each other. The additional resulting cycle time reduction of 0.1 to 0.3 seconds proves to be a milestone in energy, cost and time savings.
A versatile benefit for the preform producer
The synthesis of the latest NETSTAL PETLINE and MHT mold technology not only guarantees preform producers high output as well as premium part quality, but users also benefit from maximum reliability, full industry standard compatibility and low energy consumption. This results in lower production costs for each preform. Further machine sizes of the new PETLINE are currently being brought to market maturity in close cooperation between NETSTAL and MHT, which will offer further attractive opportunities to the world of preform production.
The comPETence center provides your organisation with a dynamic, cost effective way to promote your products and services.
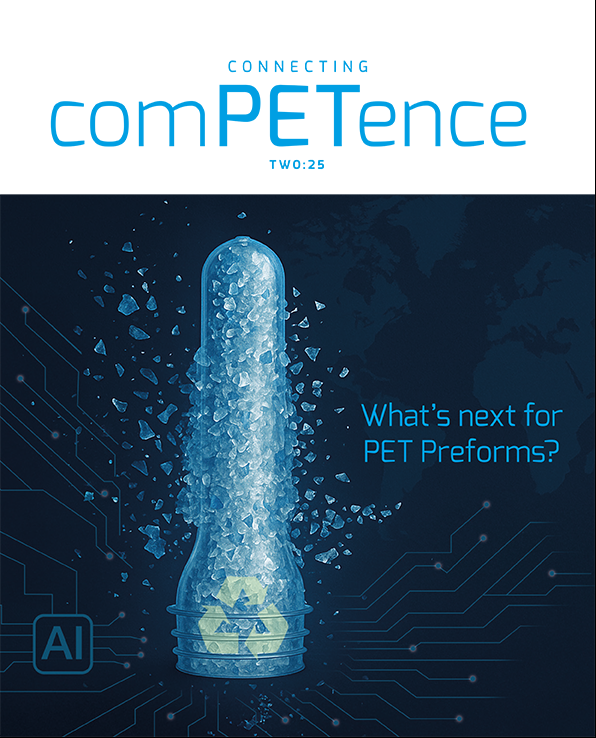
magazine
Find our premium articles, interviews, reports and more
in 3 issues in 2025.