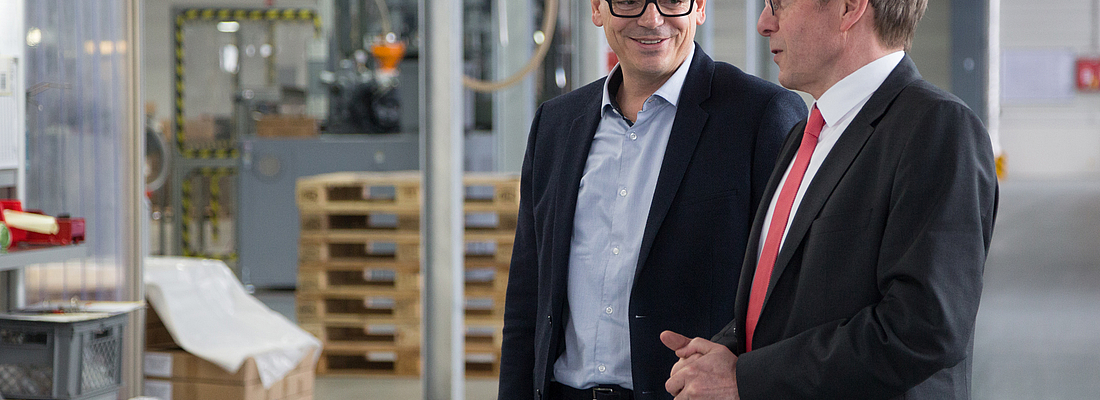
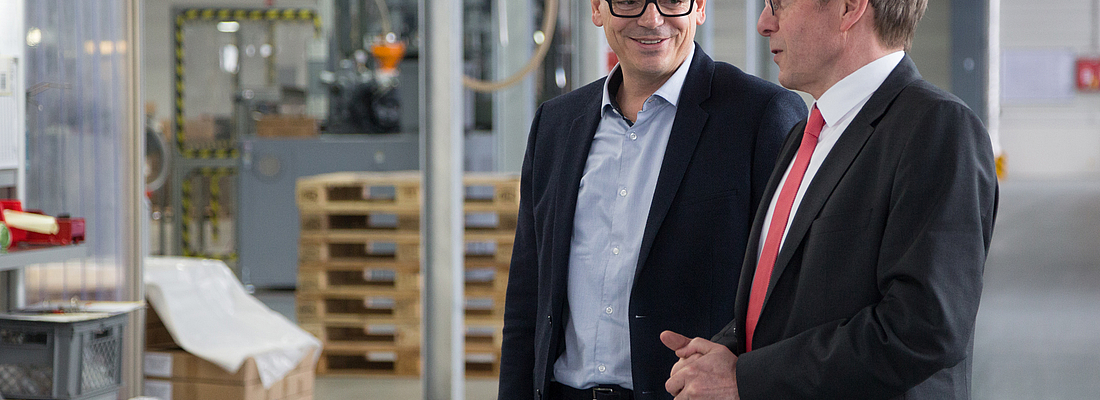
The comPETence interview with Benno Sauer, Alexander Umlauf-Sauer, SAUER
Do you operate solely in the packaging market, or do you also manufacture technical plastic parts?
Umlauf-Sauer: We produce technical plastic parts as well. These are supplied to the furniture (moulded seats), automotive (ventilation ducts), and sports and leisure (ride on baby toys, sledges) industries.
What share of your products are packaging — either in terms of turnover or quantity?
Umlauf-Sauer: Compared to packaging, the technical parts play a very minor role. From a total annual production quantity of 1.3 billion items, they represent a share of approximately 1.5 million pieces.
Which sectors of the packaging market do your products cover?
Sauer: The majority of our products (>50%) are sold to the cosmetics industry. We also supply the chemical/technology industry, the food industry and, to a lesser extent, the pharmaceutical industry.
What technologies or production methods, do you use to supply the packaging market?
Sauer: Our containers are manufactured using extrusion blow moulding (PE, PP, PETG, Coex), IBM (PE, PET) and ISBM (PET, PP) techniques.
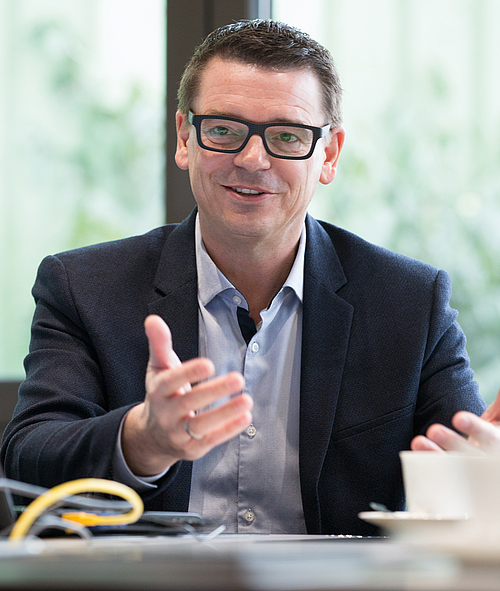
What percentage of your product portfolio for the packaging market is occupied by PET?
Umlauf-Sauer: The share of PET products has steadily grown in recent years. It now accounts for around 15% of our packaging products.
Do you utilise a two-stage process, and if so, for which applications and what are the advantages?
Sauer: Yes, we employ both the single-stage and the two-stage process. In the latter, we manufacture bottles for the cosmetics and food industries. The key factor when deciding whether to use two-stage production is the number of pieces required for the project in question. When large volumes are needed and it would only be possible to complete the job using a large number of machines, two-stage production is the method of choice. Quality factors are also an important decision criterion here. For some products, you can achieve better quality when you employ the two-stage process than with single-stage methods.
Do you manufacture the preforms for these applications?
Sauer: Yes, we produce the preforms ourselves directly on site.
Do you work with biopolymers? What is your opinion of them?
Umlauf-Sauer: We don’t yet work with any PET biopolymers in series production. We have done few R&D projects, but these haven’t yet been translated into a product series. Sugarcane-based PET was tested in this instance. Because this product is “food” based, we, like our customers, view it with a very critical eye. We employ sugarcane-based PE for a single product manufactured with extrusion blow moulding.
Do you conduct your own R&D projects on materials development, recyclate use, container weight reduction or anything else?
Sauer: Material trials always take place in consultation with our clients. We do a great deal of trial testing on materials.It is now standard practice to use recycled materials, and numerous projects have been implemented using both rHDPE and rPET. Since the supply source for rHDPE is very restricted, markedly higher quantities of rPET are employed. The interest in using this material for series production continues to grow. Weight reduction is always high on the agenda. Enormous price pressure means that, from the very beginning of any project, we are automatically committed to identifying and employing the minimum possible base weight. Even when projects are already ongoing, opportunities for reducing weight are always being pursued, trialled and implemented if successful.
Do you manufacture exclusively customer-specific bottles or do you have a range of standard containers?
Umlauf-Sauer: We solely use our customers’ own tools in production. Standard series are only offered on a very, very small scale.
Do you have your own design department to support customers with container and bottle development, and do you make your own moulds?
Sauer: Yes to both. Our company slogan is “We mould your ideas”. Customers receive comprehensive support from us right from the initial product idea through to the finished packaging product. We design packaging in 2D and 3D directly in our CAD system. Creating product presentations, building display models of design drafts, producing pilot and then production moulds are all things we are able to do. Some moulds are made in our own mould making facility, others are procured from external suppliers.
Do you provide a fully complete “bottle”, i.e. a decorated bottle with a cap, and do you also manufacture caps yourself?
Umlauf-Sauer: Sauer has the largest in-house decoration department operated by any packaging manufacturer. 37 screen printing and pad printing units at our premises are used to decorate containers. We can embellish bottles with hot foil stamping, and can also label small batch runs. In addition, we have the facility to sleeve bottles. If a customer requires it, we can also offer fully complete products (bottle-cap). We don’t manufacture caps ourselves, however, so we work with a range of different market partners who supply them.
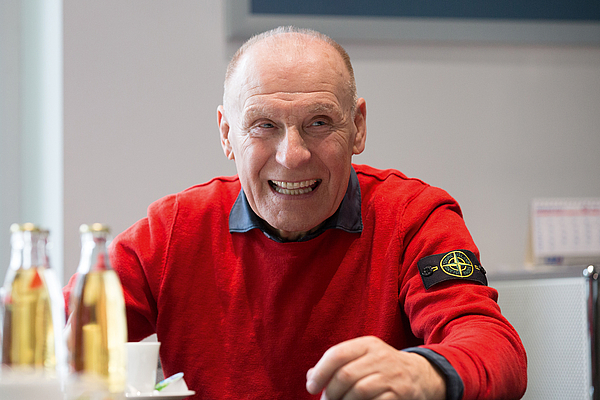
Where are your production facilities?
Sauer: We have four production sites. The parent company is in Neustadt bei Coburg. A second production site was built and commissioned in 2002 in the neighbouring South Thuringian town of Föritz. 2015 saw the opening of a further factory in Föritz. This site was planned and constructed specifically for manufacturing containers using IBM and ISBM methods. Alongside the three German factories, Sauer also has a fourth production site in France (Sarreguemines, Lorraine). We currently have a total of 211 production machines in operation.
Do you tend to manufacture products to order, or do you maintain stock?
Umlauf-Sauer: Manufacturing to order has now become the market standard. However, in order to meet target times, it is imperative that we have containers in stock. Both concepts are therefore firmly intertwined. Our customers now only have warehouses if absolutely necessary, and responsibility for storage has largely been passed over to suppliers. It is only possible respond quickly and flexibly to sharply fluctuating market demands if you have appropriate warehousing. As far back as 1989, Sauer reacted proactively to this need for flexibility by building a fully automated high-bay warehouse, which at the time had space for some 10,000 pallets. We now operate three of these fully automated warehouses, plus a semi-automatic temporary store, which altogether have room for over 80,000 pallets. This is unique within the industry.
What do you require from today’s blow moulding machines and do the solutions that are available on the market meet your needs?
Sauer: This is another area where Sauer is unique. The extrusion blow moulding machinery available on the market today largely stems from Sauer’s creative powerhouse. Since the 90s, we have been working with suppliers to develop machinery that is specifically tailored to our needs, as the “standard” products available are not sufficiently high quality for us. Additional Sauer expertise is therefore incorporated into all the plants we operate, and we also contribute our “specialist features” to IBM and ISBM facilities. First and foremost, modern plants must be reliable. It must be possible to exploit all available capacities. Where tight project timings and delivery deadlines are concerned, it is imperative to keep downtimes to the absolute minimum. Flexibility is another important factor, so machines need to be all-rounders. Processing widely varying materials in different batch sizes must be a matter of course. The diverse array of colours now available need to be produced with the utmost quality, and it must also be possible to ensure rapid changes of materials, master batches and moulds.
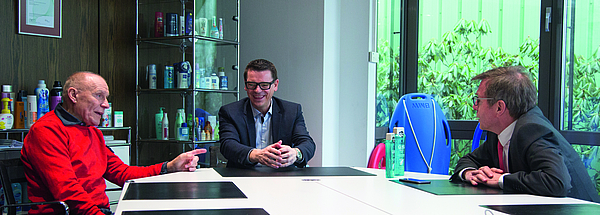
How have the markets changed and what developments do you expect to see in your packaging markets over the next five years?
Sauer: In recent years, markets have become very demanding. Suppliers take high levels of service, flexibility and speed for granted. High quality product standards are a basic prerequisite, and production processes must be fine-tuned to achieve zero defects. Lead times from the receipt of an order to delivery have reduced dramatically. Production quantities and deadlines are constantly being adjusted with the communication of regular forecasts. Pressure on the flexibility already required is set to intensify in coming years.
Umlauf-Sauer: Ever higher demands are being imposed on products whilst the markets exert intense pressure on prices in a bid to bring down item costs. We anticipate that our industry will be subjected to increasing pressures of this nature in future.
What do you see as the biggest technical and technological challenges confronting your company, or will the continued successful development of your company place you before a different set of challenges in the future?
Umlauf-Sauer: From our perspective, the main challenge in coming years will be to retain and increase the availability of skilled workers. In any specialist field, well trained staff are absolutely key to maintaining daily business operations. Clearly, plant technology, automation, logistics and so on always need to be kept up to date, but even the most ultra-modern equipment is useless if you don’t have the right people to operate it.
What is your attitude to the market and customer requirements for greater client focus, more innovation and further automation?
Sauer: Our philosophy is that rather than merely being a supplier, we should be a service provider for our customers. Close communication allows us to get to know the unique characteristics and requirements of each and every client, and enables us to respond to their needs. We maintain high levels of service throughout the entire supply chain.
Umlauf-Sauer: Whenever there is a new project, we get involved right at the very beginning so that we can support and advise customers with our technical expertise and thus guarantee successful implementation. These consulting activities span the entire duration of the project and beyond, right through to the successful launch of the products. We work continuously on product and production optimisation, improvements and new ideas that are discussed with our clients and, if successful, then incorporated into projects and implemented.
Have you explored the topic of digitisation, for example with regard to production?
Umlauf-Sauer: This is something that will take on an important role for all manufacturing businesses in future. Our focus is therefore shifting increasingly towards ‘Industry 4.0’. In the medium term, the world of work will be compelled to change (demography, shortage of skilled workers). As a result, ever more attention must be concentrated on automation, interaction between humans and machines, and on inter-machine communication. We are in the very early stages of this, but have already begun projects headed in this direction. For example, as I already mentioned, we operate fully automated high-bay warehouses, and two years ago also implemented a driverless system for transporting finished goods within our factories.
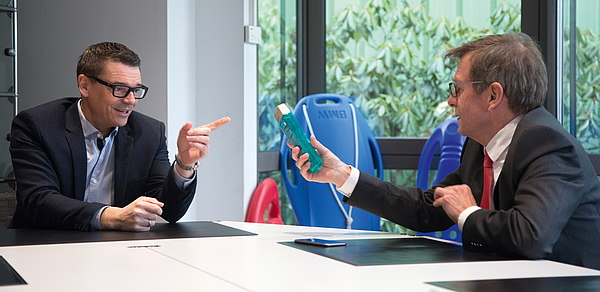
How important is the topic of marine littering for your company? Have you been contacted by customers regarding this issue?
Umlauf-Sauer: Marine littering is something that should be taken extremely seriously. Reports on the pollution of world oceans with plastic waste are becoming ever more present in the media. This gives plastic an extremely negative image, and consequently puts a lot of pressure on our customers as those who bring plastic packaging into circulation.
It is absolutely imperative that we curb this environmental pollution with improved collection and recycling systems worldwide. The advantages of plastic packaging cannot be dismissed. Nevertheless, this issue creates incredibly bad press and encourages plastic’s negative image. Our association, the IK Industrievereinigung Kunststoffverpackungen e.V. (editorial note: Plastics Packaging Industry Association), addresses this in a variety of different publications. As a member of the association, we support this initiative accordingly.
What is your assessment of the competitive situation for converters in the cosmetics/medical, household, food and pharmaceutical packaging markets?
Umlauf-Sauer: Generally speaking, we have recently seen noticeable changes in the supply landscape. In addition to company closures, mergers and takeovers are increasingly being observed. The current markets are very demanding, and some market players no longer have the desire or ability to respond to these challenges. For these reasons, further changes are on the horizon in the medium term. We can say one thing for certain, however: the number of plastic bottle suppliers will not increase in the near future.
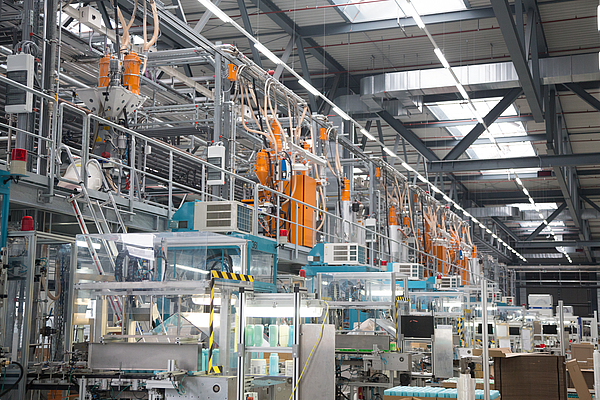
The comPETence center provides your organisation with a dynamic, cost effective way to promote your products and services.
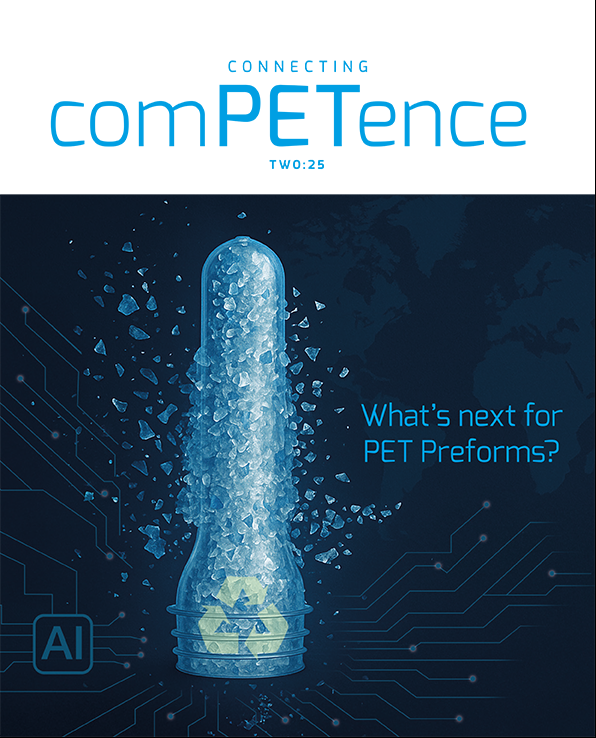
magazine
Find our premium articles, interviews, reports and more
in 3 issues in 2025.