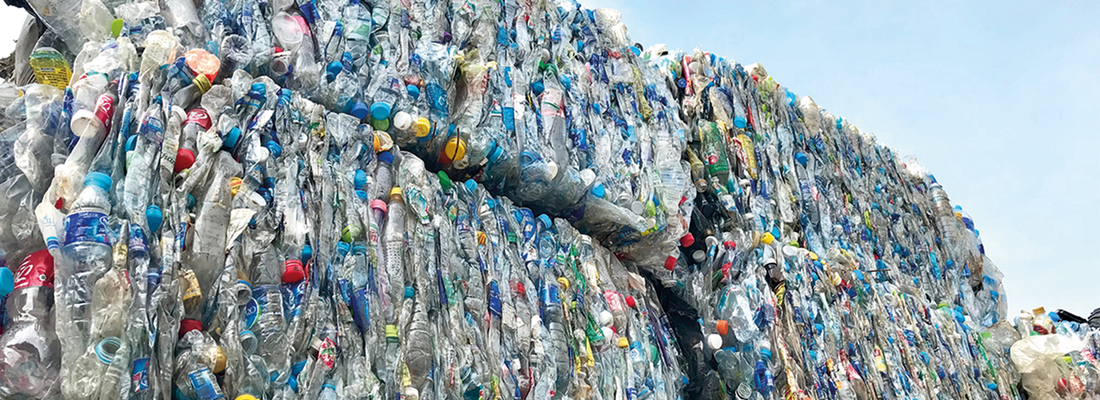
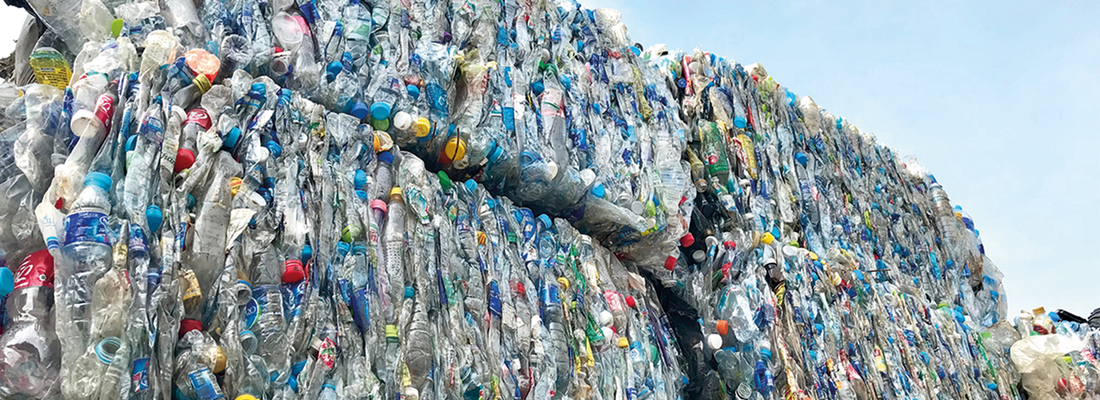
The world around us is filled with activity related to plastics recycling. New alliances, new strategies, and new technologies are aligning with current solutions to greatly increase recycling and perhaps reduce plastics waste and “single use” packaging. Brands, consumers, and governing agencies are implementing changes that will finally capture and return plastics to new usefulness.
SBAcci is a PET packaging consulting group that has closely guided the industry for three decades. We appreciate the broad interest in US PET recycling system and the enormous transformation being seen in addressing the lifecycle of plastics. The strength and reach of this global movement to recycle PET (specifically) and other plastics (in general) is unprecedented. It’s truly an amazing season to be involved with PET. There is always the element of a love/hate relationship with plastics expect we see in the world, but PET plays a valuable role in the creation and delivery of so many important products. Our team closely follows the entire PET value chain, but we will be focusing on what happens to a PET package in the US after its contents have been consumed.
While the SBAcci has international reach, this article will focus on the PET recycling system of the United States and the unique domestic circumstances. The US is blessed with a large landmass for our ~325 million residents. We have abundant natural resources, several geographical regions, and we also have a low recycling rate when compared to many other regions of the world. We can debate the reasons for our deficiency in plastics recycling, but the truth is that PET recycling in the US has been stagnant and not just stable for many years. This is a real problem as we see a concerted push for higher recycle content in plastics. Obviously, you really cannot have higher rPET content in containers unless you are getting the previous bottles recycled and back into the mix.
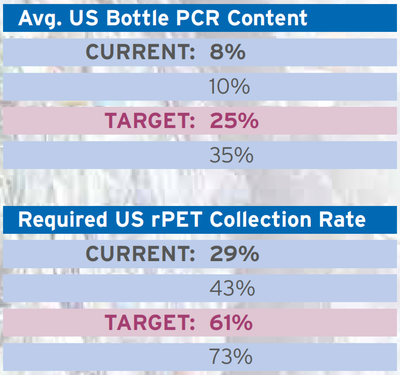
The US has a quantifiable PET recycle rate for rigid packaging of 25% - 30%, mostly for bottles. In 2019, almost 4.5 MMT of virgin PET was consumed in the US for a variety of material including packaging, fiber and textiles. Rigid packaging consumed about 3 MMT of that “vPET”. SBAcci estimates the 2019 PET recycle volume collected to be 900 KMT. 30% is not terrible, but it could and should be much better. Much of the world has much higher PET packaging recycle rates, and the US needs to improve quickly. We can understand that polyester (PET) carpeting has some unique recycling challenges that CSD bottles do not. But there really are not many good reasons why a PET bottle cannot be recovered and then constructively recycled for a new life and usefulness.
I selected the presentation subject matter based on the unavoidable escalation in competition for the PET feedstocks. There will a “Battle for the rPET Bales” at some level, even with increased recycling rates. Let’s discuss the market forces shaping that rPET competition.
SBAcci places the 2019 PET recycle volume for the 50 US states at ~900 KMT You will discover some variation in that rate number from different sources depending on their market view and sources of the data, but we will work with ~900 KMT. Of that 900 KMT volume, roughly 55% of the rPET comes from US curbside programs while another >40% comes from deposit states and California. Interestingly, California is something of a PET stream in and of itself. There are ten US deposit states, so this tells us that most of the US population’s PET packaging is not being recovered through deposits. Ten US states, led heavily by California delivered over 40% of our 2019 rPET feedstock. Activating new US participants that consistently recycle PET is critical to any improvement in the total rPET value chain.
The US PET reclamation process looks like most other countries, but is spread across a lot of diverse geography. Research suggests that over 90% of the US population has access to “recycling” in some format. There are two distinct feedstock streams for PET, curbside (collecting bottles from residences) and deposit (individuals returning for refunds). The end result of both systems is a bale of rPET ready for processing. There are significant differences in the two systems. Let’s discuss these rPET feedstock streams separately….starting with the curbside collections system for Municipal Recovery Facilities (MRF’s).
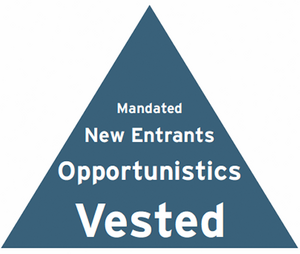
The SBAcci team recently completed a study of the >500 MRF’s in the US. We analyzed site specific details for the individual operations that collect and process ~23 MMT a year of various recyclable materials (including PET). It was a very interesting study that provided us with many useful insights. There were three goals in the project:
To locate geographically where PET is being recycled.
- How much rPET growth could current MRF infrastructure support.
- How would the MRF’s respond to a sudden and significant uptick in curbside PET recycling…if that curbside supply could be activated.
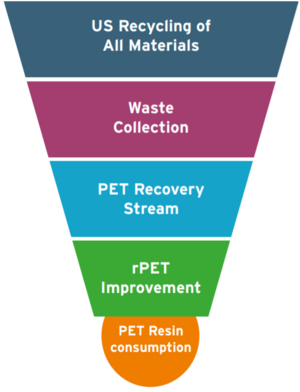
The MRF system in the US is amazing! The plastics industry receives an essential benefit from the recovery of PET and HDPE, but the MRF system is really built for paper, glass, and metals. ALL of the combined PLASTIC volumes processed by the ~500 MRF’s is less than 6% of the total off-take weight. Stated clearly and simply, MRF’s operate to reduce materials going to landfills and to recover paper/ cardboard.
Of the 23 MMT of materials flowing to MRF’s in 2019, between 65% - 70% was paper or cardboard in some form. Glass is heavy and represents ~13% of the total weight processed but does not generate a positive revenue stream. Aluminum is valuable, but it is light weight and there is not much of it going to MRF’s because end users return it for cash. All plastics are roughly 1.4 MMT with PET being the most commonly recovered plastic. PET represents a small portion of the MRF total volume, but surprisingly it represents roughly ~20% of the MRF revenue from off-take sells. So rPET recovery operates in the shadows of a huge network intended to divert landfill deposits and to recover paper. It’s a great place for rPET to be, but also carries the reality that PET recovery is not likely driving current MRF operations or strategy activities. That may change in the future, but today PET is a small portion of a large recovery system focused on recovering paper and cardboard.
The US MRF system is strong and has the ability to process more PET if it is available through the increased and consistent participation of the US population. There are a couple of large companies that hold significant market share of MRF operations, but there is also an eclectic mix of regional MRF’s that are embedded into the infrastructure of their communities. MRF’s receive over 60% of their supply comes from residential sources. There is an upper limit to how much PET a MRF can effectively process. They are not currently running at that rate. Getting to that maximized throughput volume is heavily dependent on end user recycling behaviors.
''The US MRF system is strong and has the ability to process more PET if it is available through the increased and consistent participation of the US population.'' - Steve Lyons
Deposit states typically offer better rPET “bales” by the simple nature of their recovery process where individuals must bring back bottles with some degree of visibility to the return agent. Deposit states provide a monetary incentive that get results:
- Higher participation
- Higher overall rPET bale volumes
- Better bales with higher yield rates
Thus far, we have established that in 2019 the US had ~900K MT of rPET with ~55% being recovered through MRF’s and a recycle rate for rigid packaging of ~29%. My colleague Dave Cornell has done extensive research into the collective goals of some 60+ brands and organizations that want to increase the rPET content in their packaging. Today’s AVERAGE rPET content per package is ~8%. The typical stated goal is to increase average package content of 25% by year 2025. Year end 2025 is 66 months (less than many new car payment schedules). To express that differently, the US has 66 months to effectively triple our average rPET content per package. If we lay aside the current barriers of rPET pricing premium vs. vPET, yield fluctuations, scaleup, then we are still left with the question of how do we double the US recycle rate in that period of time? Dave’s calculations show a need to jump from ~30% to 60%, in a country that has hovered at ~30% for a long time. Therefore, a primary challenge to meet these rPET content targets requires activating more individual participants in PET recycling.
SBAcci recognizes that when two individuals recycle PET bottles that they may do it differently. If both are participants in a curbside recycling program, one may be more efficient in putting all possible bottles while the other may have less discipline and recycles fewer bottles. We need not only for this second person to be more efficient in putting more bottles into the recycle bin, but also to increase the number of people participating in order to get needed quantities of used PET packaging.
Next, let’s examine the rPET reclaimers in the US value chain. This group is an eclectic mix of scale and technologies when compared to the more consistent of MRF operations. There are ~30 rPET reclaiming operations that have a combined wash capacity of 1.2 MMT. We believe they also have a combined capacity for ~680 KMT of FDA LNO (Letter of No Objection) grade rPET. Like MRF’s, rPET reclaimers have the capacity to process more rPET if the feedstock bales are available and the economics support expanded operations.
In 2019, the US rPET reclaimers provided ~770 KMT of finished product (rPET resin) to the industry. These materials could be broadly segmented as LNO and non-LNO, but there are other characterizations such as IV, form, and color. There are several effective ways to prepare, clean, process, and repelletize PET….so there are some degrees of differentiation in the technologies. Our view is that the US reclaimer industry has recently operated at above 70%. In 2019, the average rPET content of a US container was ~8%. This matters greatly because reaching a 25% average recycle content goal is going to require a lot more feedstock from consumers AND the required conversion into a usable rPET products. Reclaimers capabilities and capacities are essential to success in reaching the 2025 content targets. SBAcci estimates that an additional 500 KMT – 800 KMT of PET will need to be collected and processed to support the 25% average content goal. Growing by this volume would certainly be impactful to a reclaimer industry with a ~1.2 MMT wash capacity. That is a lot of growth in a short period of time.
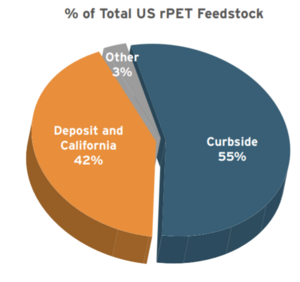
That brings us back to the pending “Battle for the rPET Bales” and the realities facing the US rPET recycling system. Domestically, we have some very efficient and strong recycling processes. If we were going to call out a core weakness, then it is in participation. We have too few people committed to plastics recycling and the US has too many regions with very low rPET volumes. We need more feedstock to work with.
The value chain for PET recycling has grown as brands have committed to higher rPET packaging content. Advanced Recycling, or “chemical recycling” is just on the horizon with multiple announcements for new capacity. These new, high tech operations are exciting opportunities to convert rPET feedstocks into prime quality chemicals….monomers or molecules. Advanced Recycling processes could use feedstocks that are unsuitable for mechanical recycling. And we should expect that others are looking to enter the world of PET recycling after seeing recent demand commitments from brands, and the possibility of regulatory mandates for rPET content. So, the landscape for processing rPET is changing rapidly. Hence, the “Battle for the rPET Bales”.
The current rPET collection and processing system in the US is at something of a balanced state. Supply and demand are relatively stable. Recent swings in vPET pricing have made rPET less financially attractive with a ~20% gap in pricing, but that premium is seen as temporary. The pending industry ramp up to an average package content of 25% will challenge the current system. Particularly the early steps in the value chain and rPET supply process. Competition for rPET feedstock sourcing will escalate as current and pending users grow demand. We will segment these rPET feedstock users as four separate competitive groups: Vested, Opportunistic, New Entrants, and Mandated.
First is the group of “Vested” rPET consumers. These are PET consumers that are vertically integrated into recycle content, either by strategy, FFU, or requirement. Either way, they rely on rPET for commercial and strategic reasons that vPET cannot satisfy. Vested groups include vertically integrated operations in products like fibers and strapping. Our research shows that Vested users have the motivation and strength to fight for their share of rPET supply and to win. If we look at the 900K MT rPET product stream from 2019, the Vested group could consume as much as 320 KMT or about 35% of the current US stream. Again, it will be tough to displace their demand for rPET bales.
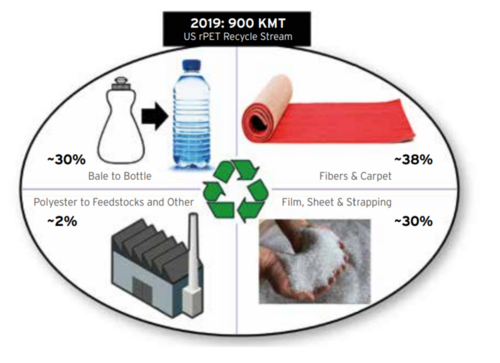
Next is the “Opportunistic” rPET user. This group has the ability to move in and out of rPET content without consequences. If rPET is readily available, priced attractively, and has finished goods demand…then they are a buyer. If the economics or supply are not favorable, then they may select to use more vPET.
“New Entrants” is a really interesting group. These include Advanced Recycling and potential new mechanical recycling builds. For the US, this could also include exports to non-US entities, such as global brand specifying shipments to Europe. This group could put a lot of pressure on US rPET feedstocks. We have seen the announcements of new PET Advanced Recycling builds from Indorama (40 KMT), BP and Eastman with undisclosed capacities. If BP and Eastman build at typical chemical facility scale, then we might have an additional 140 KMT – 180 KMT of rPET feedstock demand, just from these new operations.
Finally, the “Mandated” group. This is a placeholder of sorts for possible future regulatory demand and possible brand mandates for specific rPET content. The premise is that certain states or even a Federal-level action will REQUIRE a specific level of rPET content or else a package with low rPET content is penalized. Legislation like this could drive rPET demand up very rapidly. Related, the potential impact remains to be seen of external demand pressures like the efforts of the Consumer Brands Association to address the pricing gap between virgin and recycled PET.
''These market forces are shaping “The Battle for the rPET Bales”. The reality is that today’s rPET system for the US operates satisfactorily with our ~30% rate with an average of 8% rPET content.'' - Steve Lyons
These market forces are shaping “The Battle for the rPET Bales”. The reality is that today’s rPET system for the US operates satisfactorily with our ~30% rate with an average of 8% rPET content. But the US system is facing pressure from content targets, feedstock demand for new entrants, and possible legislative activity. Therefore, we must have an increase in the national participation rates….and particularly in non-deposit states. It’s hard to estimate what level of PET recycling participation is achievable without a national Mandated Deposit Law, but actions have to be taken to grow returns as the demand for rPET content escalates over the next ~66 months we have until year end 2025.
There are options to increase the rPET supply and make more bales available, including:
- Finding low cost options for MRF’s to reduce PET yield loss
- Getting better quality bales with less non-PET content to reclaimers
- Designing PET packages to reduce sorting loss
Beyond incremental improvements in the current stream, we could seek to activate new polyester feedstocks that have not been attractive to mechanical recyclers. For instance, clamshells could add to rPET supply. The inherent feedstock flexibility of Advanced Recycling could open doors for PET based materials with a #7 resin identification code to be recovered.
The bottom line is that we are seeing a tremendous and positive effort to improve PET recycling with strong Brand commitments made to higher rPET content in packages. Growth usually brings challenges. The timeline for reaching 25% average content is going to pressure-test the current US rPET systems. Activating a new set of US recyclers is essential to reaching value chain targets. If higher PET recycle rates cannot be done by civic motivation, it may be achieved through monetary mandates. There is some capacity available for growth at MRF’s and reclaimers, but not enough to meet all possible demand at 25% average content. Advanced recycling and other “New Entrants” will need feedstock in place within a few years and those volumes could be significant. And…profitability of PET reclaiming must be sufficient to justify investment, or the burden will be shifted to others in the value chain.
So, “The Battle for the rPET Bales” will test the US rPET system, but the drive of the Brands for content and the ingenuity of the value chain partners will find a way to grow the total supply. It is an exciting time to be involved with rPET, and I look forward to the positive solutions for rPET growth we expect to see.
The comPETence center provides your organisation with a dynamic, cost effective way to promote your products and services.
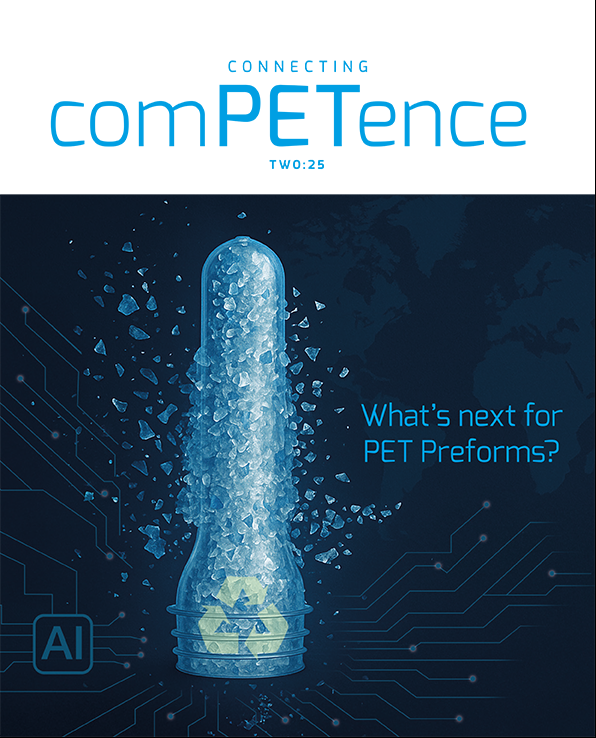
magazine
Find our premium articles, interviews, reports and more
in 3 issues in 2025.