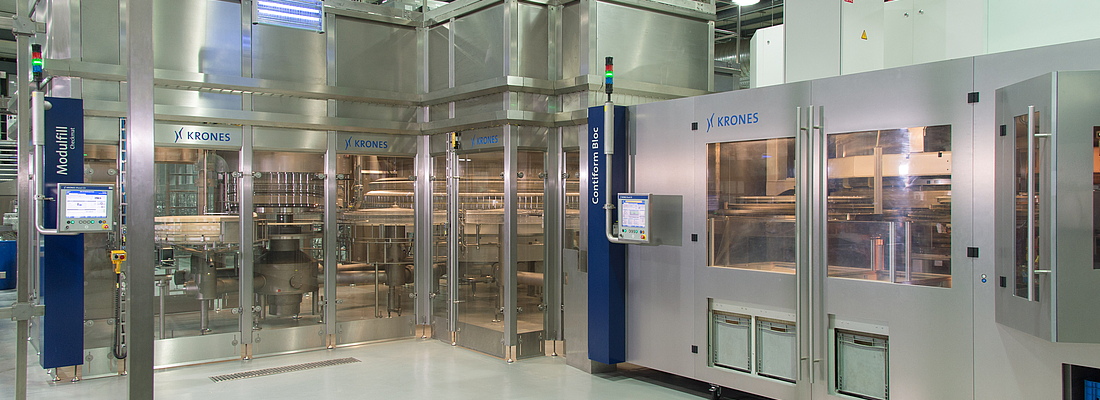
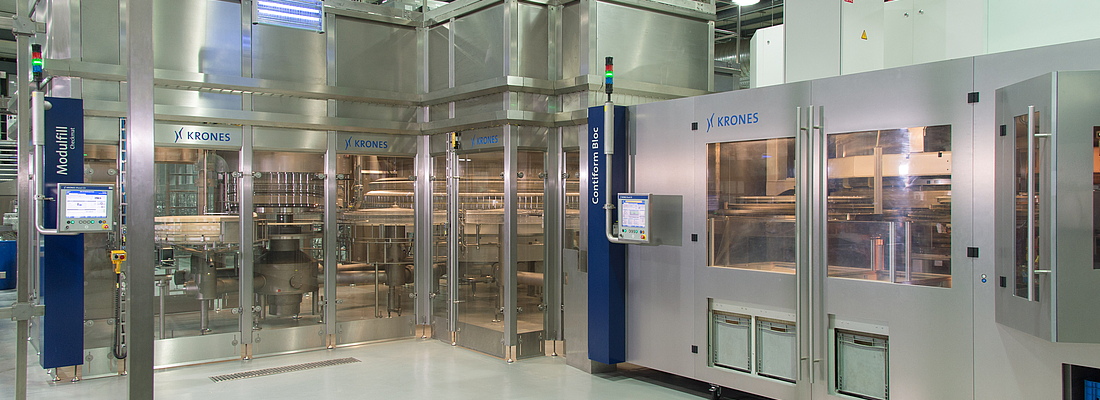
The block concept for aseptic lines, in particular, has proved a coruscating success
When it comes to filling almost all kinds of beverages, block-synchronisation of several machines within the line is nowadays an acknowledged prerequisite. There are good reasons for this, of course, since the advantages involved are many and various. The block concept has proved particularly popular as a blow-moulder/filler combination in PET lines. The figures speak for themselves: since the debut of aseptic PET filling technology at Krones, two-thirds of all aseptic fillers have been block-synchronised with a blow-moulder, while for the period since 2013 this rises to over 90 per cent. Worldwide, there are meanwhile over 370 Krones aseptic lines up and running – more than from any other vendor.
It was back in 1970 that Krones built the first block-synchronised machine, linking a filler to a labeller. This means Krones can draw upon almost 50 years of experience in block-synchronisation. The first conventional blow-moulder/ filler block followed in 2001, and shortly afterwards, in 2004, the principle was adopted for aseptic filling technology as well.
HIGH POTENTIAL SAVINGS
The advantages of block-synchronisation – particularly for aseptic machine technology – are obvious:
- The elimination of air conveyors means that after being blow-moulded the bottles are no longer exposed to their surroundings, but fed directly to the filling process.
- Aseptic products are filled in visually upmarket bottles. Thanks to the absence of air conveyors, clients enjoy enhanced flexibility in terms of container design; the bottles remain undamaged during transport.
- In conjunction with preform treatment, lightweighting is possible.
- Extremely short process windows mean extremely low residues of the sterilising agent, maximally 0.5 parts per million, though in practice they are often not even measurable.
- Thanks to ideally harmonised processes, speeds of up to 63,000 bottles per hour can be achieved.
- Servo-technology enables the filler and the blow-moulder to be operated separately if necessary.
The potential savings by block- synchronisation in aseptic lines are impressive:
- 18 per cent less CAPEX (capital expenditure)
- 30 per cent less footprint
- 30 per cent less steam consumption
- 33 per cent less low-pressure air consumption
- 33 per cent less power consumptio
HARD FACTS:
- All aseptic systems from Krones operate for up to 168 hours at a time without a cleaning phase being required.
- The Contipure AseptBloc DA can be completely cleaned and sterilised in just 1.5 hours.
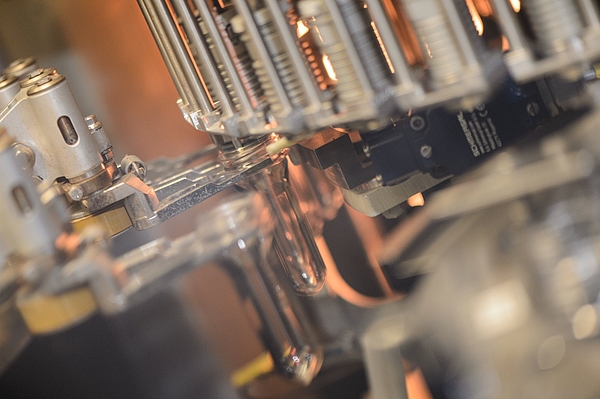
Fig 2: What’s ingenious about the Contipure sterilisation system is that it’s not the fully blow-moulded containers that are sterilised, but the preforms beforehand.
SMART TECHNOLOGY
Here’s a typical case involving the Contipure AseptBloc DA: aseptic filling of NFC juice in PET containers – this idea has enabled the Brazilian fruit juice producer Natural One to conquer the market within just two short years. Production on the aseptic line began in early 2016. In the eyes of Valdenir Soares, who at Natural One is responsible for New Business Development, this success was very closely attributable to the new Krones line featuring the Contipure AseptBloc DA technology. “We measure time in two epochs: the time before Krones and the time with Krones,” says Valdenir Soares. “Because this technology has enabled us to faithfully translate our idea of natural juices into fully functional reality. Stretch blow- moulding and filling on a single machine – that’s simply brilliant, especially when – as is the case in the Contipure AseptBloc DA – it’s already the preforms that are sterilised,” he explains.
What’s ingenious about the Contipure sterilisation system is that it’s not the fully blow-moulded containers that are sterilised, but the preforms beforehand. Directly after being heated, they are treated with gaseous hydrogen peroxide (H2O2) in a sterile zone – externally, internally and at the neck finish. This ensures that the sterilisation performance stipulated for high-acid beverages is achieved at all times.
SENSITIVE BEVERAGES OUTSIDE THE COLD CHAIN
The Belgian contract bottler Konings Drinks uses a line featuring a PET-Asept D dry-aseptic block. This means it can now also bottle sensitive beverages outside the cold chain. “We ran some in- depth comparisons for the technologies available on the market. From these, one thing emerged quite clearly: Krones’ PET-Asept D dry-aseptic system offers us maximised flexibility at format change-overs,” says Luc Nulens, one of the four proprietors of Konings Drinks and its Managing Director.
And at Konings Drinks this can be expressed in specific figures:
- A format change-over including CIP/SIP cleaning, takes 2.5 hours. By way of comparison: with older aseptic systems, this time can be up to twelve hours.
- Konings calculates 30 minutes for a product change-over pure and simple, without intermediate flushing, and the figure is a mere ten minutes when the only thing required between two different products is to drain the pipes.
- Konings schedules one format change-over per day on average, and one product change-over roughly every eight hours.
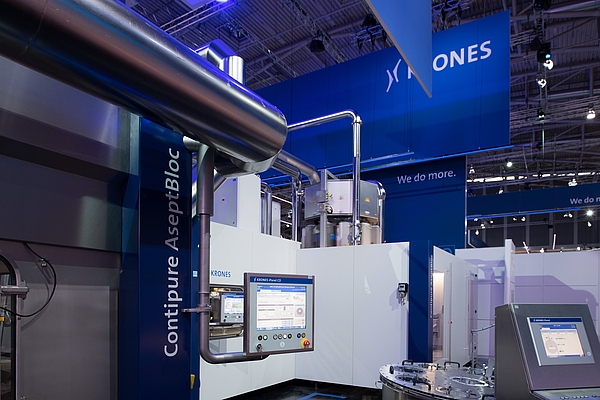
Fig 3: The Contipure AseptBloc E renders germs harmless when sterilising the preforms using accelerated electron beams. This innovative aseptic block is currently undergoing a field test at a German beverage producer.
PREFORMS PHYSICALLY STERILISED USING ELECTRON BEAMS
One brand-new innovation at Krones is the Contipure AseptBloc E. Hitherto, the predominant choices for aseptic lines in the beverage industry were chemical processes featuring hydrogen peroxide or peracetic acid as the sterilising agent for decontaminating PET containers or preforms. But there are alternatives: Krones is the first machinery manufacturer to be currently conducting a field test at a German beverage bottler to demonstrate the performative capabilities of a physical sterilisation process under production conditions. The newly developed Contipure AseptBloc E renders germs harmless when sterilising the preforms by means of accelerated electron beams – an innovative method that has proved to be exceptionally effective, with a killing rate of log 6.
- Since the Contipure AseptBloc E utilises a purely physical process for sterilisation, consumption levels for water, chemicals and evaporation energy are minimised compared to conventional aseptic lines. This also has a microbiological benefit: during actual production, the system consumes no water at all, thus depriving microbiological organisms of a potential habitat. The actual power consumption for using electron beams is in a low range.
- Following treatment of the preforms with electron beams and subsequent stretch blow-moulding, there is no longer any need to rinse the finished bottle with hot media.
- Blowing out the preforms before treatment can also be dispensed with.
- The aseptic block is suitable for both low- and high-acid products.
The Contipure AseptBloc E, as an alternative to chemical sterilisation processes, thus poses minimal requirements for the utilities involved.
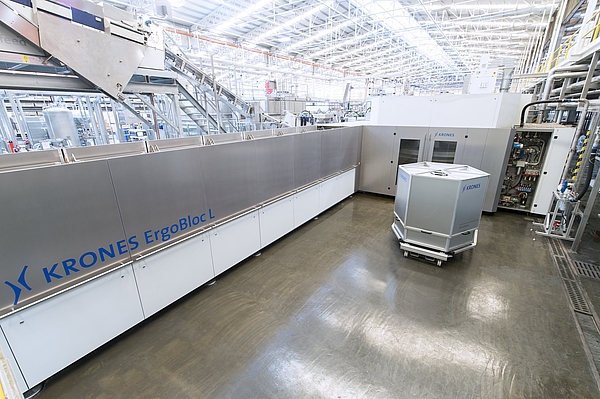
Fig 4: The ErgoBloc L wet-end block achieves an output of up to 81,000 containers per hour – and needs up to 70 per cent less space than conventional lines for this.
BLOCKS FOR NON-ASEPTIC FILLING AS WELL
Blocks are, of course, available not only for aseptic filling; there are other ariants designed for “normal” filling modes:
- Contiform Bloc BF: stretch blow - moulding machine and filler/cappe
- Contiform Bloc BL: stretch blow - moulding machine and labeller
- Contiform Bloc BFL: stretch blow- moulding machine, filler and labeller, Plus
- ErgoBloc L – wet-end block featuring blow-moulder, labeller and filler with prelabelling of the freshly blow- moulded PET bottles before they are filled, and
- ErgoBloc LM with stretch blow- moulding, labelling, filling and capping – specifically for the requirements of still-water bottling
The Contiform Bloc can handle all products offered on the market in non- returnable PET containers, and its capabilities cover everything required for handling liquid products in PET bottles, from aseptic filling processes to hot and cold-filling. With the aid of the networked control system and the servo-drive concept, the individual machines can be swiftly decoupled from each other in stop situations. This enables lengthy ramp-up phases to be avoided at restart.
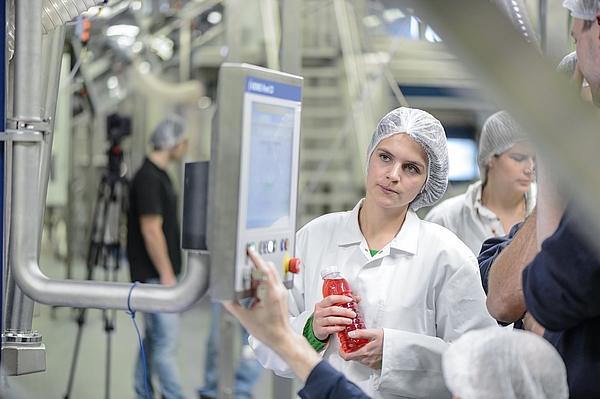
Fig 5: The Belgian contract bottler Konings Drinks uses a line featuring a PET-Asept D dry-aseptic block.
RATINGS OF UP TO 81,000 CONTAINERS PER HOUR
When it comes to speed per square metre, the ErgoBloc L wet-end block is way out in front: it achieves an output of up to 81,000 containers per hour – and needs up to 70 per cent less space than conventional lines for this. It combines the following functions: stretch blow- moulding, labelling, filling and capping, and handles both still and carbonated beverages.
To match its plant to the latest state of the art, for example, the mineral water bottler Aguas de Fuensanta in the north of Spain has installed an ErgoBloc L. The system handles 21,000 bottles per hour referenced to the 1.5-litre containers, and has replaced an old, conventional wet end. “One aspect of major importance in this project was the line’s felicitous layout,” emphasises Plant Manager Nicolás Villarejo Ardisana.
The ErgoBloc L is accommodated in a separately enclosed cleanroom with filtered air. “Thanks to this layout, we were able to install the ErgoBloc L without interrupting the entire production operation. For linking the new block up to the dry end, the line was halted for only five days. This short time window was especially important since commissioning took place in summer, that is to say during the peak season,” he adds.
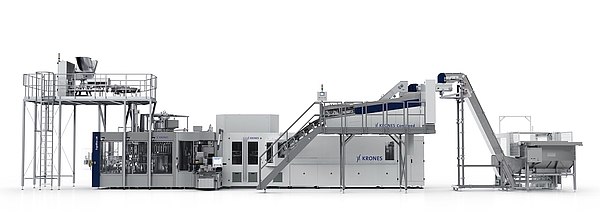
Fig 6: The new Krones ErgoBloc LM wet-end block has been conceived as a holistically harmonised machine right from the start. It groups together the control system, the drive and the operator interfacing in one central unit
“OPTIMUM EFFICIENCY AT HIGH SPEED ON A MINIMISED FOOTPRINT”
The new Krones ErgoBloc LM wet-end block goes one step further. It breaks with the previous approach of concatenating several individual machines to form a complex whole. Instead, it has been conceived as a holistically harmonised machine right from the start. Essential functions like control, drive and operator interfacing have been grouped together in a central unit. This not only reduces the capital investment costs and footprint for the block, but also significantly downsizes the workload involved in maintenance and operator control. The ErgoBloc LM can be operated in its entirety by a single employee. With the electronic PFR valve for stepless regulation of the filling velocity, it is predestined for filling still water. It combines the functions of stretch blow-moulding, labelling, filling and capping at speeds of up to 55,000 containers per hour.
Philippine Spring Water Resources, the market leader for packaged water in the Philippines, last year ordered no fewer than four lines featuring the new Ergobloc LM. Philippine Spring Water Resources has been a Krones client since 2014 – and already has five ErgoBloc solutions up and running, each rated at 36,000 containers per hour.
The privately owned company has now moved up a gear: the four new ErgoBloc LM systems will each be able to handle 45,000 containers per hour in the future. For Technical Director Crisante Dayao, the advantages of the new technology are obvious: “The ErgoBloc LM is even more compactly dimensioned than the previous ErgoBloc, and we can benefit from the higher output. This time, too, we explicitly opted for complete lines from Krones. Firstly, manual packing would no longer be commercially viable at these speeds. Secondly, we aim to avoid problems in ongoing operation by entrusting the entire job to a single- source supplier,” he explains. So Crisante Dayao can justifiably formulate his expectations as “Optimum efficiency at high speed on a minimised footprint”.
KRONES’ FIRST BLOCK SOLUTION FOR CANS
But block-synchronising individual machines is by no means restricted to filling PET containers, or to aseptic processes. For the first time, beverage producers can buy an all-in-one solution from Krones for filling and seaming cans, using the Modulfill Bloc FS-C filler-seamer block.
The block consists of the Modulfill VFS-C filler and the newly developed Modulseam seamer. The Modulfill VFS-C is a volumetric can filler that’s suitable for both the low and high output ranges. Depending on the container size and format involved, it can handle between 18,000 and 135,000 cans per hour. After being filled, the cans are passed for closing to the Modulseam, where Krones has integrated its long years of experience in filling and closing technology. The two modules have been matched to perfection – so as to work hand in hand. A harmonised operator control concept and a shared touchscreen ensure that type and format change-overs can be performed without any double manipulations or paths. Quick- change handling parts at the filler and seamer, moreover, facilitate fast change-overs to different can sizes.
THE DRY-END BLOCK
Last but not least, a line’s dry end can likewise be transformed into a block. As demonstrated by the ErgoBloc D, a compactly dimensioned package that handles all the worksteps involved from the individual container to the finished pallet. This is made possible by combining several field-proven Krones machines to form a harmonised line. These include:
- a Variopac Pro packer with a shrink tunnel attached
- an Accucase conveyor section
- a Modulpal palletising system with a Robobox grouping station and automatic layer-pad handling
Three components in a single block. This is all that’s needed to pack, group and palletise containers to a high level of excellence.
The comPETence center provides your organisation with a dynamic, cost effective way to promote your products and services.
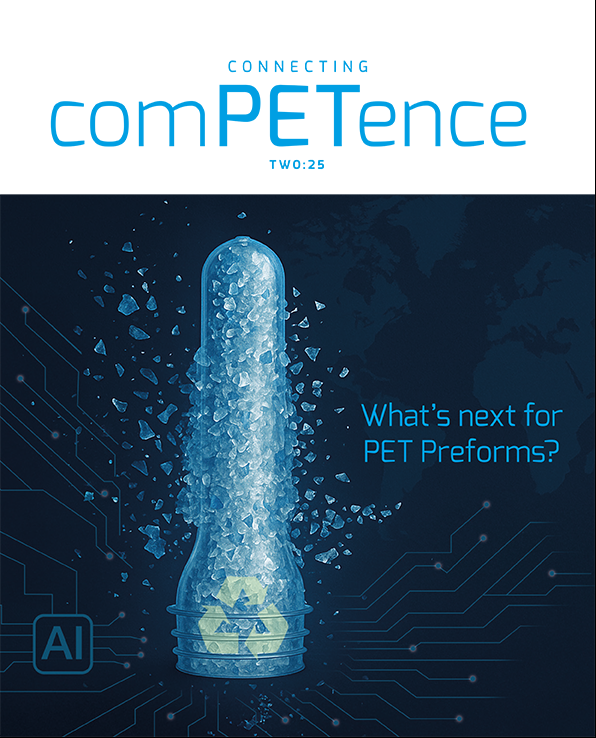
magazine
Find our premium articles, interviews, reports and more
in 3 issues in 2025.