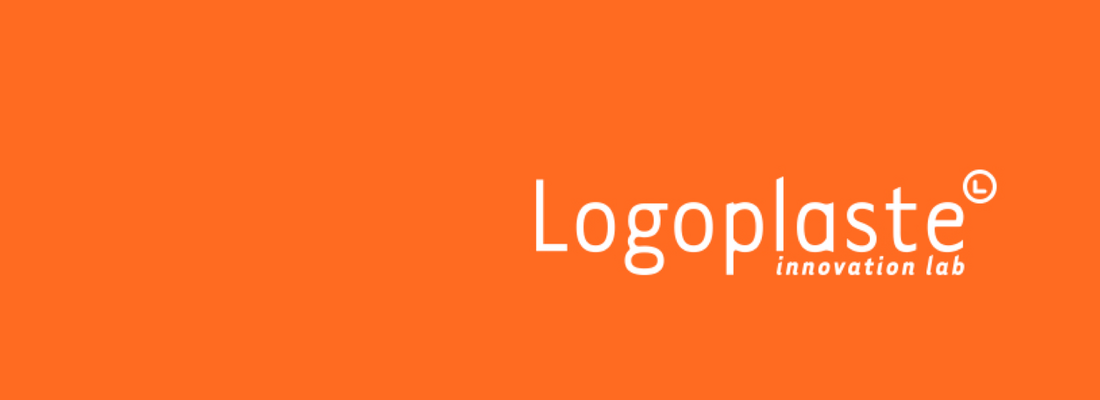
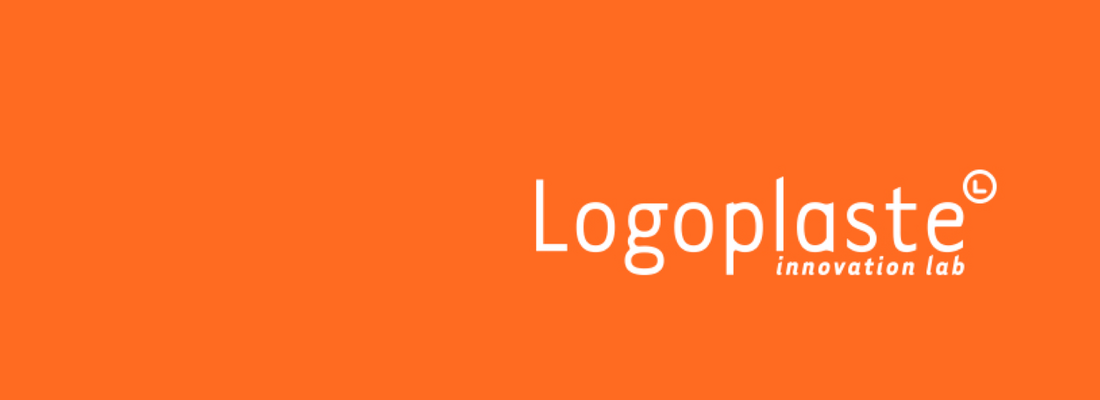
LOGOPLASTE and LOGOPLASTE Innovation Lab have always been involved in almost all of the technologies available on the market, either in terms of pure technical evaluation, industrial implementation, or as a co-partner for technology development.
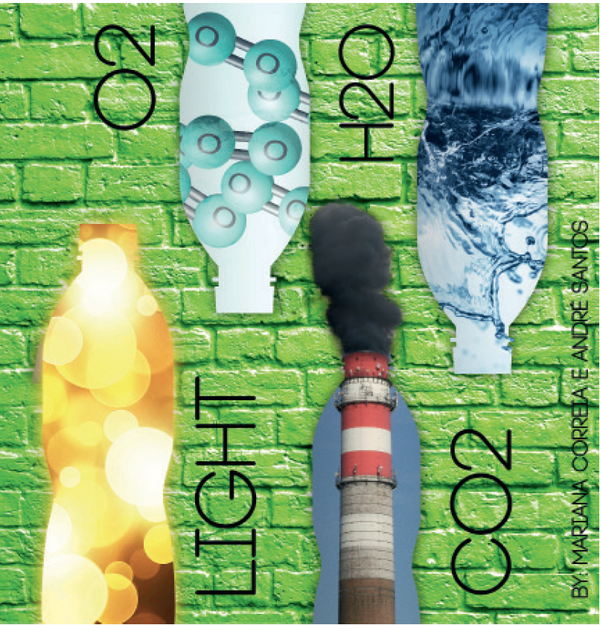
In particular, LOGOPLASTE Innovation Lab is responsible for supporting the evaluation and progress of technology in this field for LOGOPLASTE.
The goal of this involvement has always been to be a market leader and to be aware of the best solutions for different packaging requirements (light, O2, CO2, and water vapor).
The information shared here reflects interactions with resin suppliers, master batch suppliers, additives, industrial equipment/technology suppliers, end users, universities, associations, and brand owners.
This article has the objective of sharing some of the principles and ideas that drive LOGOPLASTE’s position in the market. It is the second paper produced by LOGOPLASTE Innovation Lab in this field and complements the last internal document produced 3 years ago.
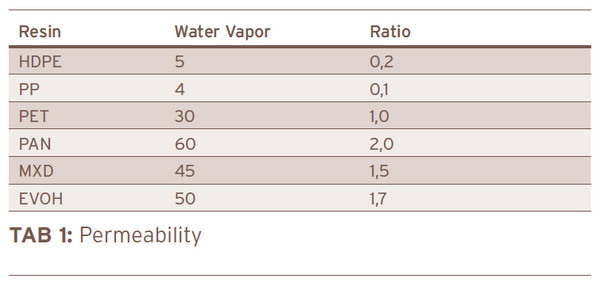
Barrier needs? Not much has changed!
The main needs for barriers are linked to the “Fabulous Four”:
-Oxygen ingress
-Water vapor (ingress/loss)
-CO2 loss
-Light protection
Oxygen ingress
This includes juices, dairy products with added juices or vitamins, water with added juices or vitamins, some energy drinks, etc.
Water vapor (ingress/loss)
Here we can point to many products. With the exception of products like powders, this is a field that most people tend not to have direct experience with. Most products are overfilled to ensure that over the shelf life of the product, the consumer is buying the quantity indicated on the label. This is particularly true for PET as the permeability is substantially worse than HDPE or PP (Table 1).
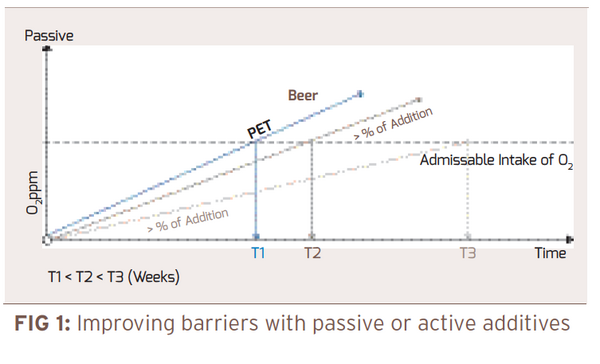
In some products, overfilling can range from 5 to 10%, depending on the specific shelf life of the product. For products with a higher value than water, this can make a big difference.
CO2 loss
In this range of products, we normally talk about CSDs.
Light protection
This includes products that are sensitive to light/UV radiation. Milk is probably the most interesting at the moment, and we will take a closer look at this subject later. While there may be some “specialties” or products where other factors must be considered, these four factors cover most of the critical aspects from a bottle perspective.
Barrier behavior – The basic principles
In term of O2 and CO2 barriers, the principles are very simple.
The following types of barriers are typical:
Passive: mono material / combination of materials (blends, multi-layer or additives) / coatings
Active: blends / multi-layer
Passive + Active (possible combination of the above)
The behavior of the above combinations can be illustrated in a schematic way highlighted in figure 1 and figure 2. The graphs show the behavior for O2 barrier application. For CO2, the principles shown in the Passive Graph are basically the same .
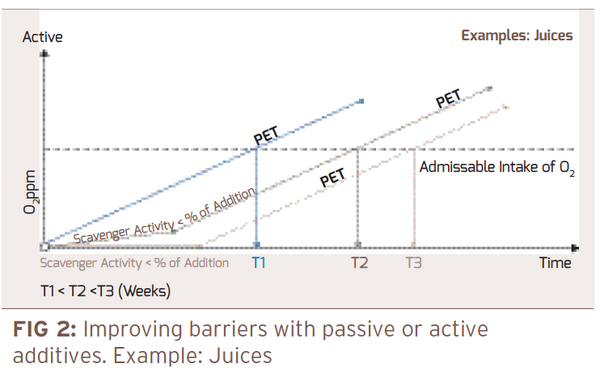
Active barriers (mono and multi-layer)
Here the additives typically added to the structure of PET will “capture” the oxygen. The most interesting feature of these additives is that they typically capture oxygen that is trying to enter the bottle, but there are other factors that can influence:
-the PET structure
-the filled product
-the head space
This is obviously worth noting, as it enhances the performance of barriers to 02. It is also the reason why this technology is preferred for products that are sensitive to 02.
Active + passive barriers (mono and multi-layer)
For some applications, combining both additives can produce interesting results. This is why we also find some products with barrier performances as described in Figure 3.
These three combinations are basically the main solutions available on the market, delivered on different technological platforms. Let’s now take a look at what is new and what can make a difference.
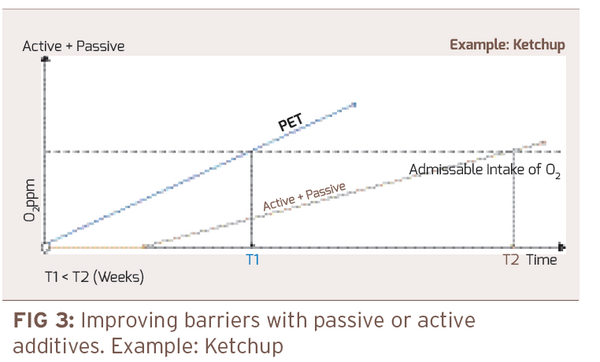
What is new in barrier technologies?
The most relevant and interesting developments are:
-Light barrier applications for dairy products
-New generation platforms for multi-layer
-New materials
Light barrier applications
There have been very interesting developments in this field in recent years. The first real industrial volumes have started to appear, and many different solutions are emerging as alternatives to the traditional TETRA BRICKs used for milk. Particularly for the UHT market, we are reaching a point where some of the solutions are cost competitive against BRICK and EBM 3 layers (the traditional white/black/white). Today, three PET solutions are being used for UHT Milk. Each of the solutions has pros and cons, and there is no universal solution (Figure 4).
Some notes on the three different processes (Table 2).
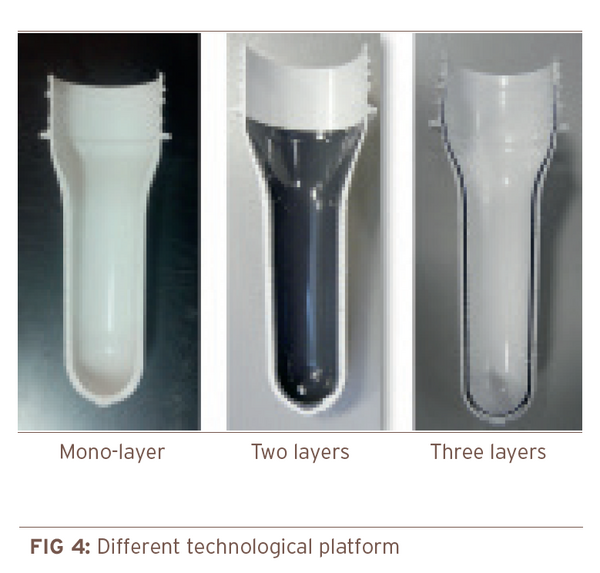
Each industrial case should be considered individually, and the specific details of each project will dictate the most appropriate solution (Figure 5).
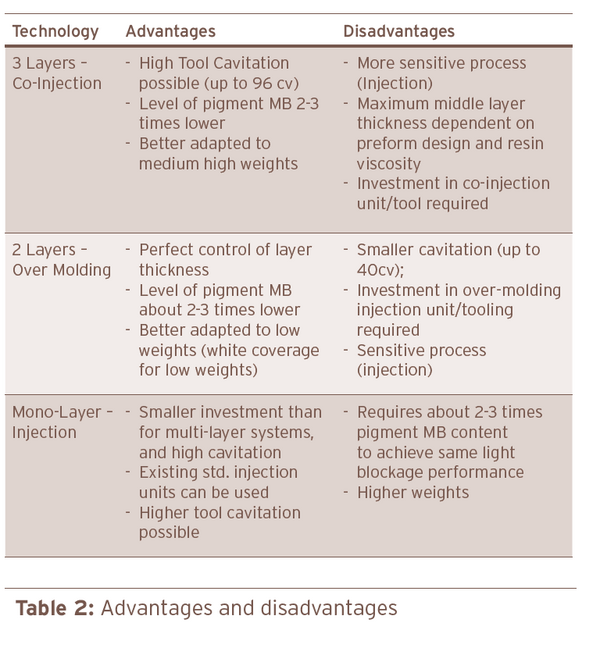
There are some parallel points that will determine the future of this market for PET:
-Concentration of volumes of production in the milk market
-Sustainability and recycling streams
-New generation platforms for multi-layer
-New materials
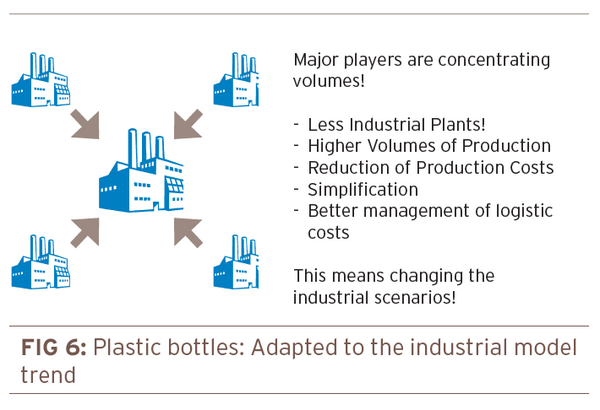
Concentration of volumes of production in the milk market
This obviously favors PET, as higher volumes support the use of PET Technology. The reasons for this can be attributed to:
-Higher outputs
-Simpler technology
-Fewer people and less space required
Sustainability and recycled streams
This is where we see difficulties for PET. We all know that PET is a fantastic material that has a consolidated waste stream for recycled material. Today the recycled stream cannot adequately deal with mono (dark white) and multi-layer (white/black) solutions and is resistant to integrating them or creating a dedicated stream for these types of bottles. The recycled stream today only focuses on systems for clear and translucid containers.
As a result, PET containers for UHT milk are being penalized by the Green Dot in some countries.
We do believe, however, that by further developing the recycled stream, the technology can deliver a fantastic solution in terms of quality and cost. To be clear, the problem is not that the containers are not recyclable, but rather that the current recycled stream does not know what to do with them.
The containers remain fully recyclable!
The market and lobbies will dictate the next steps and determine whether or not a parallel recycled stream will be created.
New generation platforms for multi-layer
Multi-layer is not new, but we are finally seeing something different entering the market. The main thing to note is how the technology is developing in terms of control, adding extra benefits over what was considered the standard on the market. The new systems claim to deliver higher control in terms of barrier variability, which could potentially deliver savings of around 20%. This is huge and could open doors to many new products that are suitable for working with barrier content.
The example in Figure 7 shows a comparison for barrier content of 5%.
It has been shown that when comparing most solutions for blends against multi-layer solutions, there is two to three times less barrier material in multi-layer than in mono layer. If the initial results correlate with the industrial results, this advance will allow us to increase the difference between blends and multi-layer, which will obviously encourage interest from the market.
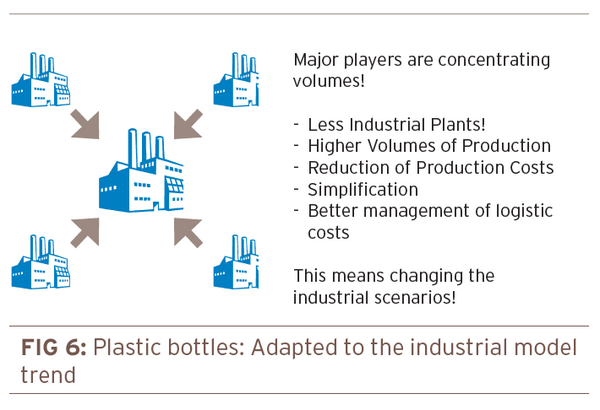
New materials
Expectations are high for PEF as a replacement for PET in products that require higher barrier performance, but there appear to be difficulties involved in producing PEF on an industrial scale. Due to the limited information available and limited access to the material because of the high costs involved in producing it on a lab scale, it seems that we will still have to wait until the promise of an alternative material can be realized
What is new is the high level of technology and the capacity to model the performance of PET in a way that best fits the requirements.
A great improvement since the first PET bottles, which was not so long ago…
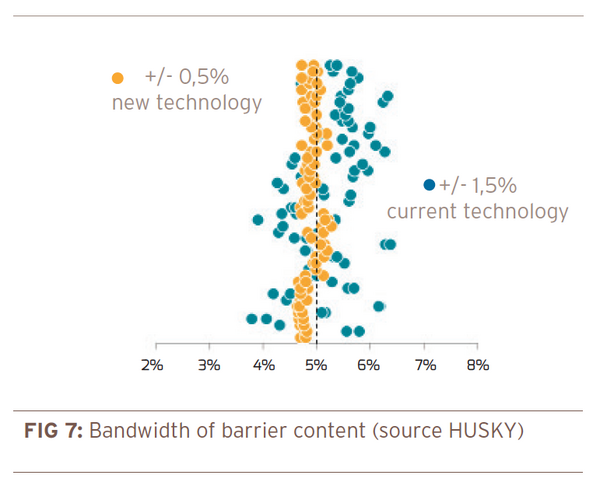
The comPETence center provides your organisation with a dynamic, cost effective way to promote your products and services.
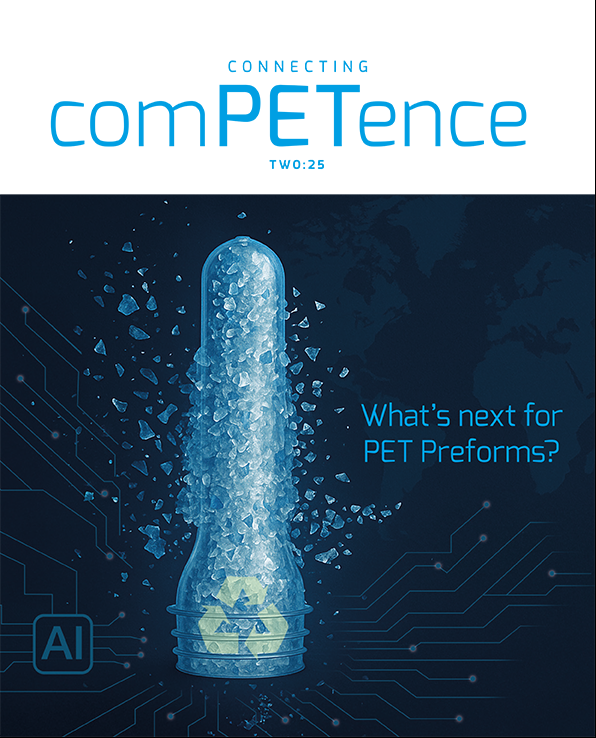
magazine
Find our premium articles, interviews, reports and more
in 3 issues in 2025.