SFP 30 ERGON packer meets the needs of flexibility, versatility and environmental sustainability for the packaging of packs in film only in several configurations 2 x n, by using the cold stretch film.
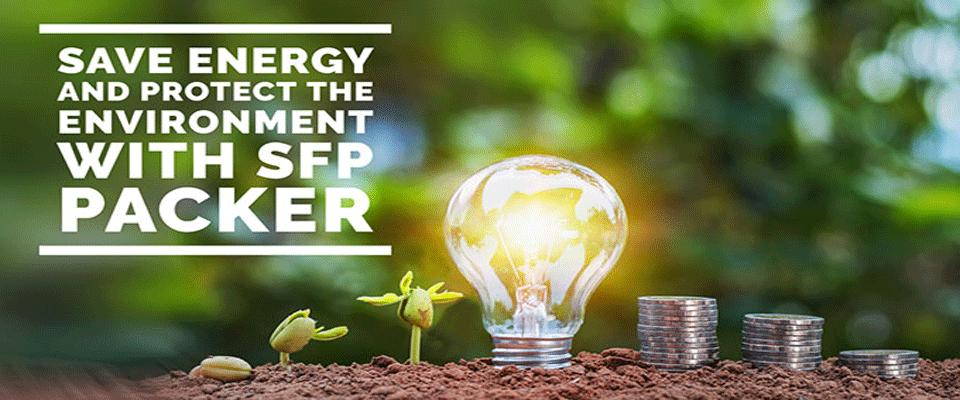
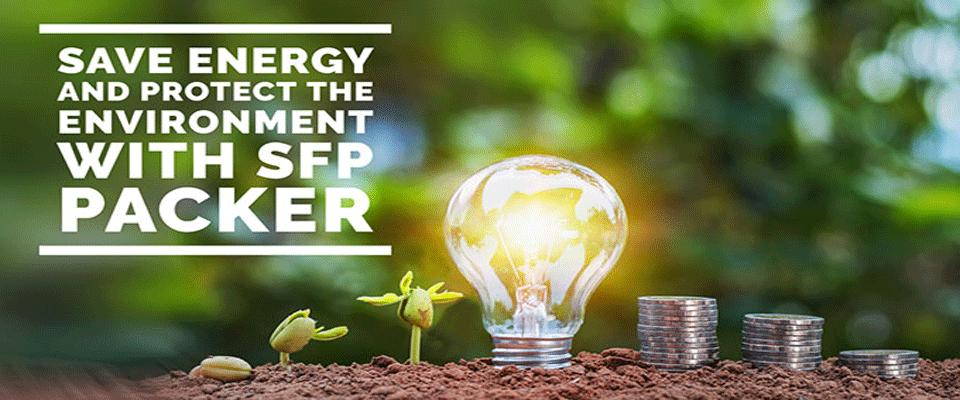
(Photo credit: SMI)
Stretch film packer
SMI: Save energy and protect the environment with SFP Packer
Environmental sustainability plays a key role in the investment choices of those who choose plants and machines for large-scale production in compliance with the standards for the territory safeguard and energy saving.
Thanks to continuous investments in research and development of new technologies, SMI has recently launched on the market a new stretch film packer, called SFP 30 ERGON, that perfectly combines the need to reduce the use of plastics and energy consumption in the packaging plants for the food & beverage industry.
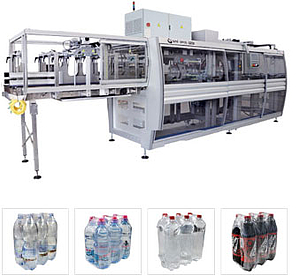
Advantes of the SFP series
- less packaging material used (-30/40 % vs. traditional shrink wrappers): 10 micron thick stretch film is used for the packaging
- energy saving: there is no heating tunnel with electrical resistances
- stable and resistant packs thanks to the double cross wrap of film around the group of containers to be packed
- easy machine access: ergonomic design of the system, typical of the ERGON range
- MotorNet System® automation and control based on Sercos filedbus
- operator panel with 7’’ interactive touchscreen display with interface in 32 languages and simple and user-friendly controls
- motors equipped with built-in digital servo-drivers: solution that generates less heat inside the electrical cabinet, thus reducing energy costs of heat waste and air conditioning fitted on the machine
- fewer CO2 emissions: more benefit for the environment
- aesthetic advantages: the bull eye, typical of the packs made in film only, has a reduced size and is on the short size of the pack
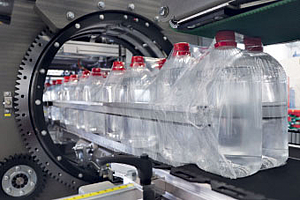
Easy packaging
On the machine infeed belt, a specific system of motorized oscillating guides correctly channels the loose containers towards the pack formation area.
Then, a mechanical system, composed of a synchronized press with compensation bars, group the containers in the desired format. The packs created proceed short size leading.
Resistant packs
The use of brushless motors in the film unwinding phase ensure a precise adjustment of the tensioning.
The film double cross wrapping system ensures resistant and long-lasting packs: the first reel wraps the pack clockwise, while the second one wraps it anticlockwise, thus performing a crossed wrap around the containers in transit.
Thanks to an innovative vertical heated resistance system, controlled by a brushless motor, the film cutting operation happens in two phases: in front of and behind the pack in transit.
The comPETence center provides your organisation with a dynamic, cost effective way to promote your products and services.
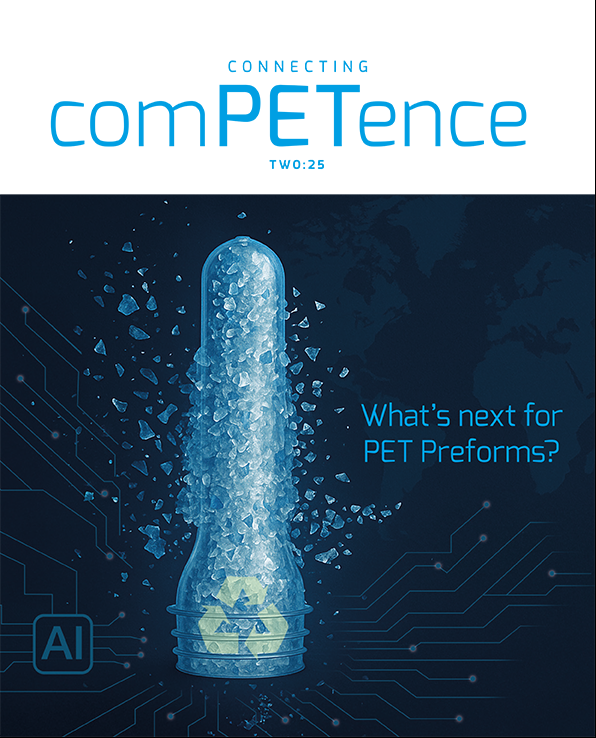
magazine
Find our premium articles, interviews, reports and more
in 3 issues in 2025.