There’s an appointment at Düsseldorf that can’t be missed. The K 2010 exhibition, an international trade show dedicated to technologies for processing plastic and rubber materials, will take place from October 27 to November 3. This exceptional showcase, at which SACMI will participate with its 800 m2 exhibition stand (Hall 15 stand B06) will be used to display the protagonists of Sacmi Group’s latest creations.
The spotlight will be pointed at the new SBF technology, which will be previewed for the beverage sector. SBF, meaning Stretch Blow Forming, is a machine that blow molds PET bottles with fascinating technical innovations.
Twelve models with a number of blowing stations ranging 6 to 30, and several new items, will be presented, starting with a dual cavity mold capable of producing two half-liter bottles or one 1.5-2 liter bottle, with a quick format change-over system. The stretching rod with electro-mechanical control, allows the stretching speed to be adapted at any time to the type of bottle being processed regardless of the machine speed, while the brushless electric motor that supplies power to the stretching rod permits high speed machine operation that is controlled at the same time, blowing bottles of different formats (which can also be complex) simply and effectively.
Thanks to the SBF, Sacmi can be considered the ideal partner for any type of bottling line, by adapting blowing productivity to filling, while various solutions, such as methods of inserting pre-forms into the molds and managing compressed air for blowing, provide numerous advantages in terms of process efficiency and consumption optimization. Among the main “pluses” provided by Sacmi’s SBF is the possibility of being integrated upstream with PAM (Pre-form Advanced Molding), Sacmi’s exclusive system for producing compressed pre-forms. The bottling machines can then be installed downstream from the SBF.
SACMI proposes the ultimate challenge in the world of compression and closure production by offering a compression machine capable of producing 2000 pieces a minute with a cycle time of 2.4 seconds. This incredible machine is the CCM80S, which completes the CCM (Continuous Compression Molding) model range of machines with 12 cavities and up.
The machine provides all the advantages of compression technology: product quality, low energy consumption and operation costs, quick powder changes, and an optimum price/performance ratio. One must also keep in mind that the rates of the latest generation of bottling lines are always increasing, therefore requiring caps with dimensions that remain the same constantly, and a level of quality that only compression can guarantee. These characteristics are found naturally in SACMI’s offer, making the CCM80S a product of excellence for this sector.
The CCM80S is the production instrument with the highest levels of performance for companies that manage high volume production lines, providing a relatively reduced investment, thanks to its perfect balance with the other machines already included or that may be included on the line, especially with machines used for folding or cutting safety bands.
The CCM80S was designed to optimize energy consumption, an aspect that is always more essential as time passes. It is equipped with new extrusion control systems that adapt energy consumption to the speeds used (which depends on the type and shape of the cap), resulting in an additional reduction in individual cap cost. This can be considered a “variable consumption system” (as best can be described) that therefore optimizes machine use in any production situation and allows the CCM80S to fit perfectly into the new SACMI machine range studied for increasing quality and productivity even more, while reducing energy consumption and the relative environmental impact.
Amongst SACMI’s other inventions displayed will be the CBF12 (Compression Blow Forming), a state-of-the-art machine that performs the plastic transformation process based on continuous resin extrusion, combined with the compression and blowing process, which allows plastic granules to pass to the container in a single cycle regardless of the type of resin used. This solution adds together all the advantages of a single-stage process with the advantages of the compression molding technology developed by SACMI.
A machine that inspects caps, the CHS series, will also be on display at the exhibition. This machine was made for installation on compression and injection lines downstream from the new linear system for orientating ORCS 160 caps. The CHS represents the ideal solution for complete cap inspection (inside and outside), thanks to its modular structure that permits the machine to be set-up according to the customer’s specific quality control needs. The success of the CHS machine line, launched at the end of 2009, exceeded expectations from the start with over 40 units sold all over the world.
The new linear system for orientating ORCS 160 caps can be found upstream from the CHS at the exhibition. Highlights of this system include an updated machine layout that optimizes space, a particular cap orientation process that, after being picked up by an innovative and silent brush lifter, slides the caps down onto the counter-rotation belt until they reach the pick-up zone, where they are turned over by a cylinder-shaped horizontal axis brush and moved in a continuous line through a transport channel.
Some of the main advantages offered by the ORCS system are efficiency, reduced consumption, silence and flexibility.
Mechanical parts move the caps to be orientated, completely eliminating compressed air, while the format change is simply handled by only 2 adjustment screws. Another special characteristic of the machine is the capability of orientating caps in only one movement, reducing friction to a minimum, and therefore dust production as well.
As far as the plastic sector is concerned, Negri Bossi will present the latest technologies for plastic molding and injection systems, as well as for production line automation.
SACMI presents its latest innovations for the beverage industry at K 2010
There’s an appointment at Düsseldorf that can’t be missed. The K 2010 exhibition, an international trade show dedicated to technologies for processing plastic and rubber materials, will take place from October 27 to November 3. This exceptional showcase, at which SACMI will participate with its 800 m2 exhibition stand (Hall 15 stand B06) will be used to display the protagonists of Sacmi Group’s latest creations. The spotlight will be pointed at the new SBF technology, which will be previewed for the beverage sector. SBF, meaning Stretch Blow Forming, is a machine that blow molds PET bottles with fascinating technical innovations. Twelve models with a number of blowing stations ranging 6 to 30, and several new items, will be presented, starting with a dual cavity mold capable of producing two half-liter bottles or one 1.5-2 liter bottle, with a quick format change-over system. The stretching rod with electro-mechanical control, allows the stretching speed to be adapted at any time to the type of bottle being processed regardless of the machine speed, while the brushless electric motor that supplies power to the stretching rod permits high speed machine operation that is controlled at the same time, blowing bottles of different formats (which can also be complex) simply and effectively. Thanks to the SBF, Sacmi can be considered the ideal partner for any type of bottling line, by adapting blowing productivity to filling, while various solutions, such as methods of inserting pre-forms into the molds and managing compressed air for blowing, provide numerous advantages in terms of process efficiency and consumption optimization. Among the main “pluses” provided by Sacmi’s SBF is the possibility of being integrated upstream with PAM (Pre-form Advanced Molding), Sacmi’s exclusive system for producing compressed pre-forms. The bottling machines can then be installed downstream from the SBF. SACMI proposes the ultimate challenge in the world of compression and closure production by offering a compression machine capable of producing 2000 pieces a minute with a cycle time of 2.4 seconds. This incredible machine is the CCM80S, which completes the CCM (Continuous Compression Molding) model range of machines with 12 cavities and up. The machine provides all the advantages of compression technology: product quality, low energy consumption and operation costs, quick powder changes, and an optimum price/performance ratio. One must also keep in mind that the rates of the latest generation of bottling lines are always increasing, therefore requiring caps with dimensions that remain the same constantly, and a level of quality that only compression can guarantee. These characteristics are found naturally in SACMI’s offer, making the CCM80S a product of excellence for this sector. The CCM80S is the production instrument with the highest levels of performance for companies that manage high volume production lines, providing a relatively reduced investment, thanks to its perfect balance with the other machines already included or that may be included on the line, especially with machines used for folding or cutting safety bands. The CCM80S was designed to optimize energy consumption, an aspect that is always more essential as time passes. It is equipped with new extrusion control systems that adapt energy consumption to the speeds used (which depends on the type and shape of the cap), resulting in an additional reduction in individual cap cost. This can be considered a “variable consumption system” (as best can be described) that therefore optimizes machine use in any production situation and allows the CCM80S to fit perfectly into the new SACMI machine range studied for increasing quality and productivity even more, while reducing energy consumption and the relative environmental impact. Amongst SACMI’s other inventions displayed will be the CBF12 (Compression Blow Forming), a state-of-the-art machine that performs the plastic transformation process based on continuous resin extrusion, combined with the compression and blowing process, which allows plastic granules to pass to the container in a single cycle regardless of the type of resin used. This solution adds together all the advantages of a single-stage process with the advantages of the compression molding technology developed by SACMI. A machine that inspects caps, the CHS series, will also be on display at the exhibition. This machine was made for installation on compression and injection lines downstream from the new linear system for orientating ORCS 160 caps. The CHS represents the ideal solution for complete cap inspection (inside and outside), thanks to its modular structure that permits the machine to be set-up according to the customer’s specific quality control needs. The success of the CHS machine line, launched at the end of 2009, exceeded expectations from the start with over 40 units sold all over the world. The new linear system for orientating ORCS 160 caps can be found upstream from the CHS at the exhibition. Highlights of this system include an updated machine layout that optimizes space, a particular cap orientation process that, after being picked up by an innovative and silent brush lifter, slides the caps down onto the counter-rotation belt until they reach the pick-up zone, where they are turned over by a cylinder-shaped horizontal axis brush and moved in a continuous line through a transport channel. Some of the main advantages offered by the ORCS system are efficiency, reduced consumption, silence and flexibility. Mechanical parts move the caps to be orientated, completely eliminating compressed air, while the format change is simply handled by only 2 adjustment screws. Another special characteristic of the machine is the capability of orientating caps in only one movement, reducing friction to a minimum, and therefore dust production as well. As far as the plastic sector is concerned, Negri Bossi will present the latest technologies for plastic molding and injection systems, as well as for production line automation.
The comPETence center provides your organisation with a dynamic, cost effective way to promote your products and services.
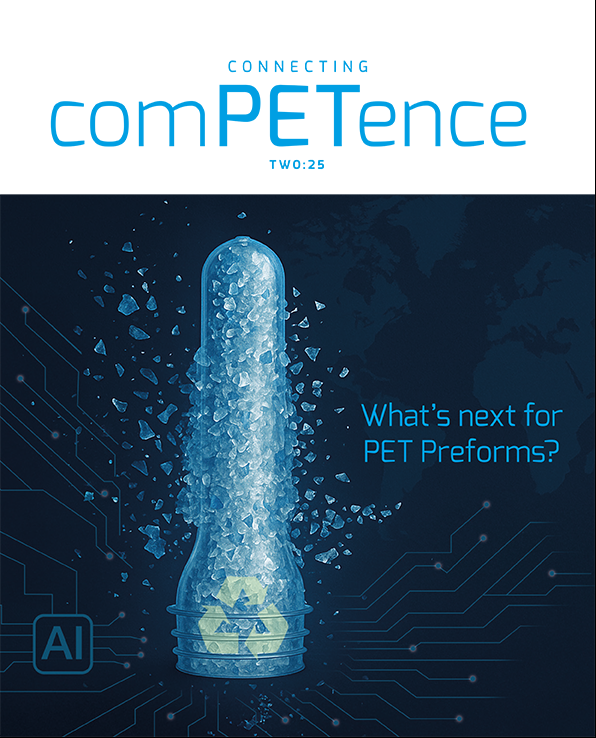
magazine
Find our premium articles, interviews, reports and more
in 3 issues in 2025.