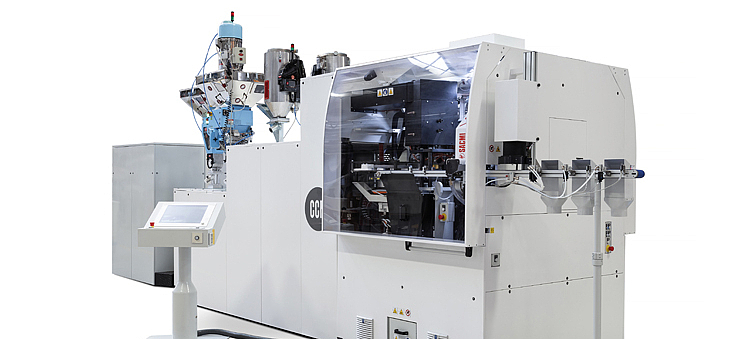
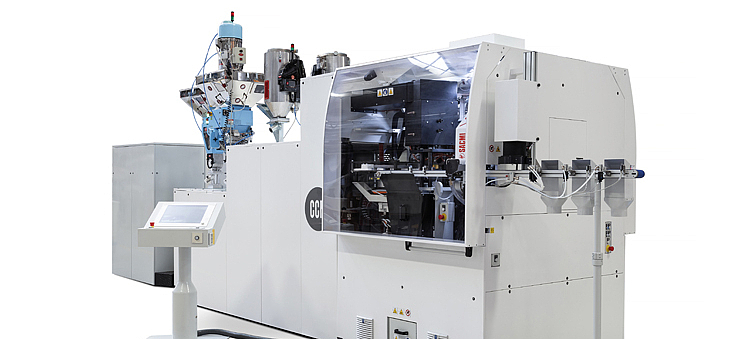
SACMI – new material research and competence in technology to improve sustainability
EU Directive 2019/04 on single- use plastics is set to revolutionise the industry by 2025. The world’s main FMCG (Fast Moving Consumer Goods) makers have already signed the document drawn up by the Ellen MacArthur Foundation and committed to reducing the amount of virgin material in packaging and increasing returnable PET quotas.
Against this background, PET - the raw material of the circular economy par excellence - forms the core of SACMI’s development plans. Several new technologies are now market-ready, all designed to serve a dual purpose: to make the most of each individual solution in terms of sustainability and to enhance consolidated technology - already widely acknowledged and appreciated on markets - so bottlers and converters have the option of heading down the sustainable plastics route.
The 100% recyclable PET is becoming more and more important in the plastics industry, both in terms of its own superiority over other plastic materials in terms of possible reuse and versatility in all types of industrial packaging. The aim of SACMI is to give a second life to PET through the use of recycled resins and / or through the promotion of the introduction of fully reusable material according to the principles of circular economy.
Continious Compression Moulding (CCM) – From capsule to ...
A pivotal role in new material research (with a sharp focus on sustainability and re-use) is played by CCM, SACMI’s flagship plastic capsule manufacturing technology. SACMI is developing such technology for other applications and materials, for instance single serve products in PET.
CCM merges the versatility and sustainability of this resin with the intrinsic advantages of compression technology, which include the lowest overall running costs on the market and an ability to independently check every single cavitymould directly on the line (even at high speed).
Moreover, this technology reduces onmaterial stress, making it possible to work plastic resins with a higher degree of viscosity.
Continious compression multilayer moulding (CCMM)
Developed and marketed since early 2019, CCM multilayer lies on the cutting edge of SACMI compression technology for the manufacture of multilayer capsules.
Initially focused on the manufacture of single serve capsules (for coffee, tea and other foods and drinks), SACMI’s research into multilayer capsules has gone on to yield further outstanding results, such as a capacity to manage a broad range of materials in a consistent process.
Already the hallmarks of SACMI compression, these advantages have now been merged with decisive progress on the sustainability front. For example, compression works at lower temperatures than other technologies, lowering energy and raw material consumption requirements; another CCMM strength is that manufacturers can use layers made of different materials.
Because a barrier film (EVOH) can be inserted between the different layers, thus-made capsules have extraordinary oxygen barrier properties; the barrier seals in the delicate organoleptic qualities of products like coffee without any need to act on secondary packaging: an advantage for converters and final users alike.
The SACMI CCMM multilayer compression lets producers manage a large number of layers with great flexibility, letting them choose the number and type of layers to insert according to the specific product being packaged. Moreover, compared to alternative technologies, tie layer management is optimised as the tie layer can be managed separately in dedicated layers, reducing required quantities and thus preserving the purity of the polypropylene, at lower cost.
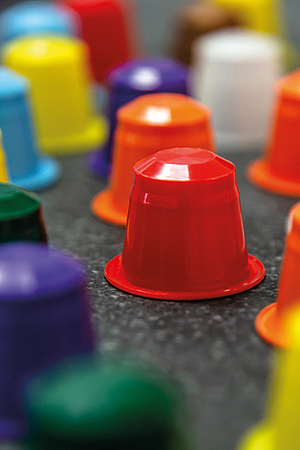
Injection Prefrom System (IPS), when sustainability comes ‘as standard’
Sacmi IPS provides the added value of being able to give PET a ‘second life’ via the use of recycled resins, thus aiding full re-use of the material; IPS is also a wellestablished preform production platform that’s popular with manufacturers on account of its versatility, productivity,
user-friendliness and low running costs. With SACMI IPS, in fact, customers can use standard machines to make preforms consisting of up to 100% rPET and use PET in recycled flake form in quantities of up to 50%. Manageable via standard hot runners, without having to make any changes or modifications to the machine, this feature enhances the outstanding sustainability and efficiency already provided by SACMI through its development of ever-lighter, higherperforming preforms and capsules.
More specifically, the SACMI IPS platform is available in versions with up to 128 cavities. Alongside the IPS220, developed to meet strong demand for size changeover flexibility in the bottling industry, stands the larger IPS400, developed to maximise compatibility with all commercially available moulds. With IPS, the possibility of boosting the ‘returnable PET’ quota via a standard process means customers can count on a tried and tested platform and a full SACMI assistance package before, during and after the sale.
Compression Blow Forming (CBF)
Compression manufacturing PET containers via the innovative CBF process is now a reality. With a pioneering single-stage process in which SACMI combines the best and most appreciated characteristics of alternative technologies (e.g. EBM and IBMISBM), CBF is particularly advantageous to dairy & pharma manufacturers as it lets them manufacture containers economically using a process that is precise, highperformance and versatile.
New developments for 2019 include the possibility of using, alongside traditional PS and PE resins, PET (the resin best suited for re-use/recycling in full) to form containers. Key areas of application include the dairy sector, but also pharma which – albeit within the confines of strict regulations – permits the use of PET to package syrups.
Again, in terms of versatility and consumption/cost optimisation, the SACMI CBF process is extremely linear (compression-made container preforms are stretch-blown immediately, accelerating the process and simplifying logistics). It can also be integrated on lines together with other SACMI machines, or even third party solutions, thanks also to its small footprint.
Computer Vision - the new frontier of A.I.
As per SACMI tradition, all machines are designed to be equipped with dedicated vision systems. As of today, SACMI offers direct, in-line PET preform quality control using polarized light thanks to a Computer Vision system with ground-breaking Artificial Intelligence algorithms.
Impossible to execute with traditional applications, the in-line identification of abnormal stress on preform surfaces using polarized light is supervised by a patented SACMI control system. Capable of ‘selflearning’, the system independently self-adjusts, lending workers a helping hand and simplifying ever-more complex product inspection procedures.
Starting with PET – the most promising raw material in terms of sustainability – SACMI aims to extend the new Computer Vision–Artificial Intelligence philosophy to all machines/businesses/industries. Indeed, the underlying principle of the new SACMI PVS (preform vision system) is its applicability to other types of control and/or stages of the production process.
Ultimately, SACMI’s goal is to simplify and extend the vision concept thanks to ground-breaking algorithms and digital control of the different manufacturing stages. In doing so, SACMI will have taken another big step towards maximising customer satisfaction and optimising all-round product quality and process efficiency.
The comPETence center provides your organisation with a dynamic, cost effective way to promote your products and services.
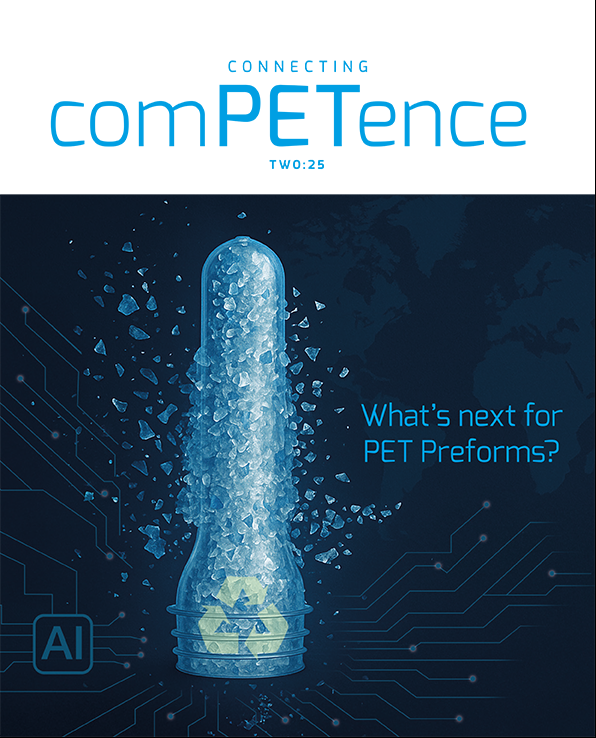
magazine
Find our premium articles, interviews, reports and more
in 3 issues in 2025.