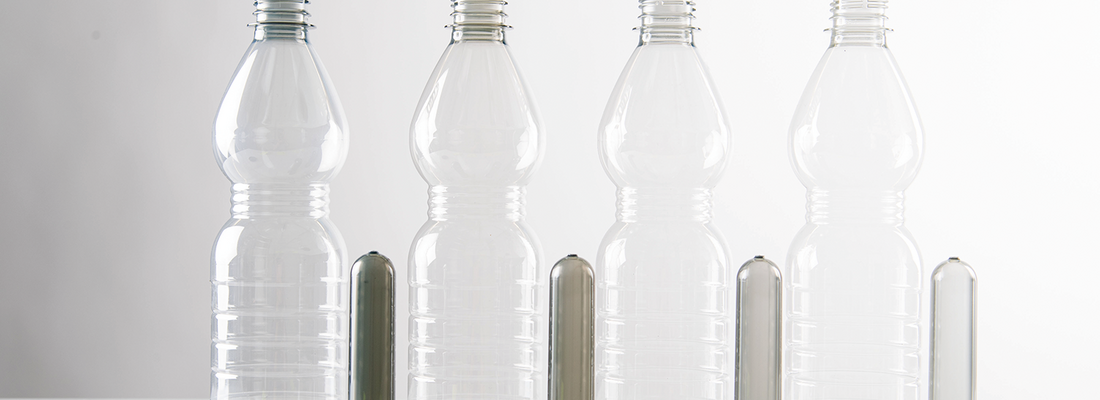
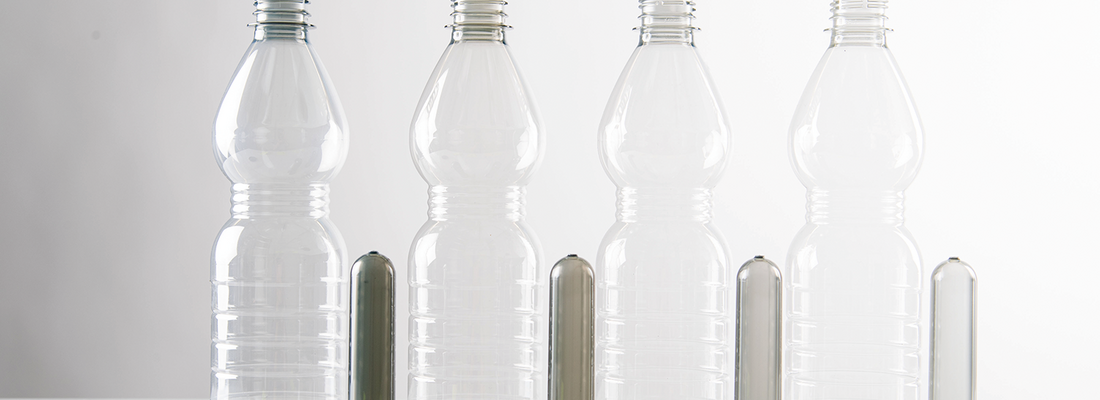
Photo credit: Krones
PET RECYCLING
rPET – The Future PET - Design for Recycling
In 2019, PET got into discussion. Main aspects of the criticism were firstly the littering of our environment, and secondly the excessive resource utilization and for example our throwaway mentality. Of course, many millions of PET bottles do not get reused or disposed correctly. Whether this is due to the lack of political rules or to insufficient awarenessraising among the populace, to patchy infrastructures or gaps in the flow of reusable materials – it is a condition that nobody can possibly wish for and that has to be urgently changed. One point, that often gets ignored in the emotional debates, is that PET is a plastic that can be 100 per cent recycled in a bottle-to-bottle process.
Krones AG, too, is making its contribution here. For PET, Krones has since 2009 already been closing a beverage bottle’s life-cycle by means of its MetaPure technology. The portfolio includes the company’s own modules for washing and decontaminating. The MetaPure solution is already running for example at customers’ sites in Bangladesh, Japan, Africa or the USA. And one trend can be seen: The use of recycled PET rises. The reasons behind are the awareness of environmental needs and also various regulations, that have been lately rendered mandatory especially in Europe but also worldwide.
But is it really possible to process rPET the same way as virgin PET? In a research project, experts at Krones wanted to find an answer on this question.
“In purely chemical terms, rPET is not any different from PET. The challenges involved are rather to be found in the quality of the input material. Correspondingly, if the input material is made of good quality, there are no unambiguously anticipated restrictions in terms of processability, of the kind possibly encountered with other materials,” describes Aurélie Börmann, from the PET Packaging Development and Consulting department at Krones.
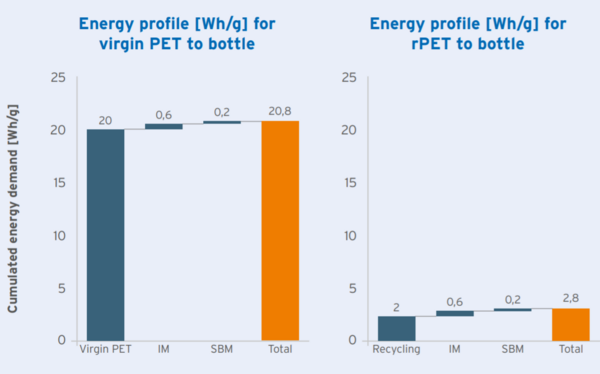
Energy consumed in the production of virgin PET right up to the finished bottle (left) and in the recycling process of the used bottles collected right up to producing a new PET bottle (right)
IM: injection moulding; SBM: stretch blow-moulding
The recycled material Krones used during the trial was produced mainly from bottles and possibly also from display trays that had previously been used for food and beverage packaging. Besides, a small proportion (< 5 %) could also be accounted for by non-food containers, like PET bottles for soap, detergents, etc. The origin was from European Countries, like the Netherlands, who possess a PET deposit system with very high return ratios. The advantage is that what’s involved here is possibly a very pure closed cycle with only a few contaminants. This had a beneficial effect on the results since the scrap rate was close to zero per cent.
To run a series of trials, Krones expert used a modularised mould, which was able to handle different types of container geometries – starting the range of simple to ultra-complex and out-of the-ordinary container geometries. The goal: examining the material, the process settings, the bottle performance, possible design restrictions, and product safety with a rising proportion of recycled PET.
“design from recycling” and “design for recycling”
By running tests with disparate container geometries, Krones has been able to check if there are restrictions in terms of container design and whether the bottle’s mechanical performance changes when rPET is added to the preform. Changes in this context could, for example, include a more viscous behaviour in the stretch blow-moulding process, different reshrink characteristics of ageing containers or visual impairments like what are called black specks, which are caused by plastic types other than PET and further impurities encountered as contaminants in the PET recycling flow. So that means: bottles have to be designed from recycling and for recycling.
Visual impairments also include coloration changes in the PET material caused by the recycling process. Containers made of rPET might appear somewhat darker, yellower or sometimes somewhat greyer. This change in color, the so called “yellowing” can be concealed by adding blue or green pigments. Some producers of rPET already use that method. But when it comes to the discussion of sustainability of PET bottles, the coloring might also be a selling point, as consumers recognize that a container is made of recyclate.
“It would be desirable, of course, if the material flows did not contain any contaminants of that kind in the first place – this could be assured either by suitable collection systems, of the type we have in Germany in the shape of the reverse vending machines, or by regulatory exclusion of certain materials for bottle dress and closure. The questions of whether – and if so – what influence these plastic contaminants have on the food safety of the product filled have been analyzed by different research institutions and found to be non-critical,” explains Aurélie Börmann. But this does not mean, that beverage companies need to be afraid of their brand presence. Nowadays the inspection technology in machines and lines is able to detect and to reject any contaminated preform or bottle at an early stage. The preforms or bottles, which were removed can easily be passed to a further recycling process. Admittedly, experience has shown that this increases what is called the scrap rate – but the material concerned is not lost, and the additional energy needed remains very small as compared to using virgin PET.
The energy profile in that cases is surprisingly low, which shows an illustration of the energy consumption during the production of virgin PET and the production and conversion of containers made of rPET.
But what’s next?
“rPET has been processed on Krones blow-moulders for years now and shows no significant restrictions in terms of processability, quality and food safety,” states Aurélie Börmann. “The consumption of fossil resources should be continuously lowered, and the use of rPET should increase. By using more recycled PET in beverage bottles, we can contribute our share to transforming the market and getting it closer to a closedloop economy”. When it comes to the trial series, Krones succeeded in proving that all bottle geometries complied with the container specifications to an equally good effect, irrespective of the rPET content. Krones now wants to take the next step and consider to what extent the material can be stressed, and what behaviour the process windows will show for lightweight containers. Besides,in cooperation with the Fraunhofer Institute more trials on product safety will be conducted.
The comPETence center provides your organisation with a dynamic, cost effective way to promote your products and services.
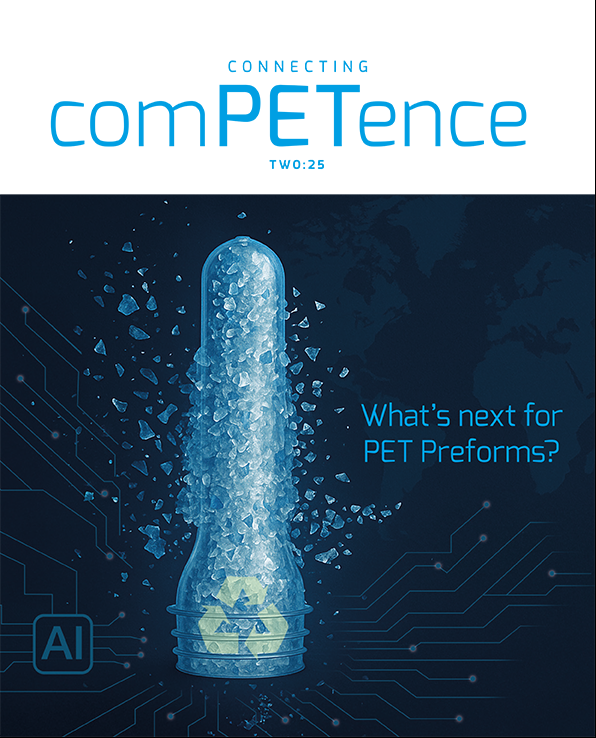
magazine
Find our premium articles, interviews, reports and more
in 3 issues in 2025.