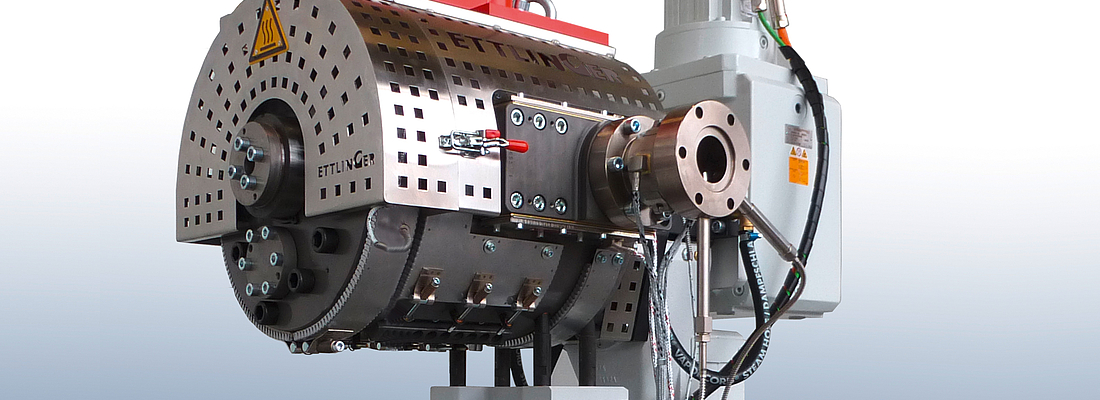
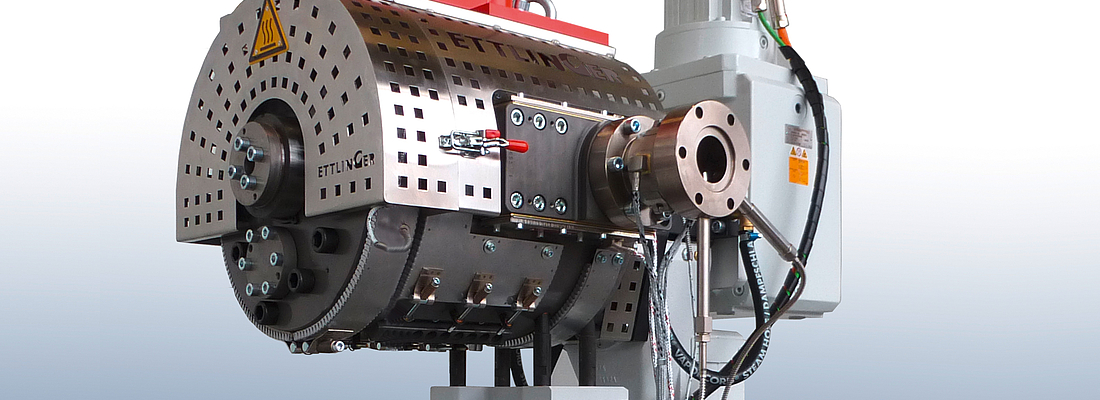
Extrusion application
RPET – efficient, stable production despite decreasing quality - Continuous melt filtration at volume and pressure constant operation
In many extrusion applications RPET from bottle flakes is used today: PET film for thermoforming packaging products, PET strapping band, PET fibers for carpet and other nonwoven products. Production reality shows, that even with huge efforts for the preparation of the PET material and supposed to be clean material, still contaminations are present, which lead to poor product quality, interruptions and down times in the running production. Solid particles and black specks in the film, tearing off of the straps during stretching, fast blinding spinneret filters, contaminations in the pellets are only a few to mention.
The problem
But why it is not possible to solve these problems with existing screen changers? A screen mesh takes contaminations from the melt. The contaminations accumulate in front of the screen mesh and blind it more and more. The pressure in front of the screen mesh increases. As a consequence of the higher pressure, soft, flexible contaminations slip through, whereas the flexibility of the wires of the mesh allow also solid particles to be pushed through at higher pressure.
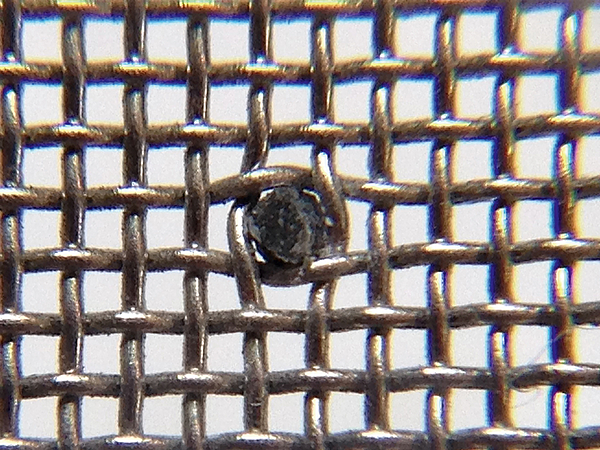
Case study: Thermoforming film for food packaging from PET
A customer, producing thermoforming film for food packaging from PET, uses PET bottle flakes, depending on the quality of the flakes coming from different suppliers, between 10-40%. Lower quality material can only be used at a lower percentage level. Even then, with a pressure of 90 bar in front of the installed backflush screen changer, off spec and waste production occurs. The optical quality control system records a significant increase of black specks and partially bigger solid particles. A backflush at an earlier state would avoid an increase of pressure up to the critical limit, however especially higher contamination contents or poor quality materials would mean a high backflush frequency in that case. And every backflush sequence is followed by undesirable fluctuations, which can be noticed in pressure drops and the flushing of black specks. This situation is the sum of different restrictions with regard to the use of cheaper PET bottle flakes.
From an economical point of view, the customer is questioning himself, how to remedy this shortcoming and to achieve the target for the use of a much higher percentage of bottle flakes up to 80 or even 100%, without any negative influence on the production efficiency.
The solution is a self-cleaning filter, which operates pressure, process and volume constantly, that covers varying material qualities with much higher contamination contents then so far possible, without stressing the production process. If this filter is running continuously for several weeks without operator assistance, an investment for this filter returns very fast.
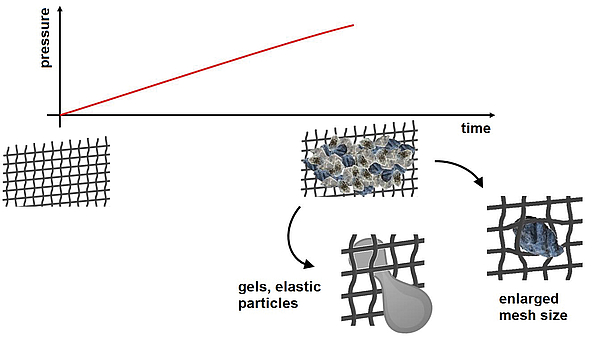
FIG. 1: Blinding screens cause particles being pushed through
Self-cleaning melt filter with rotating filter
Ettlinger Kunststoffmaschinen GmbH provides with their ECO melt filter the exact solution that was specially developed for this purpose. The rotating filter drum and its permanent cleaning allow a high contamination content within the bottle flakes and despite a continuous production without interruptions for several weeks.
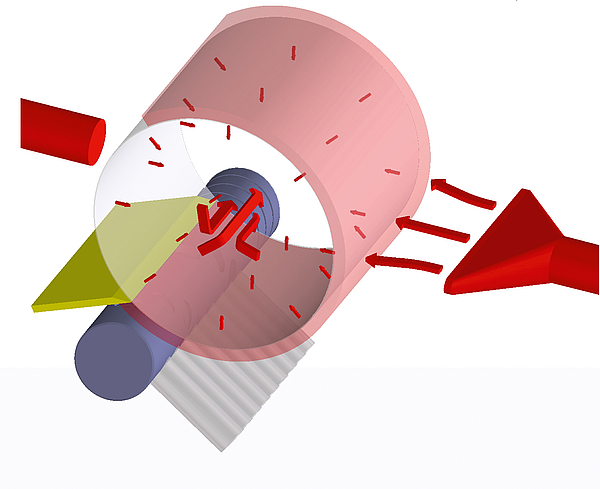
FIG. 2: ECO optimized melt flow
The ECO melt filter is based on the long time proven technology of the Ettlinger recycling melt filter ERF. The central element is the rotating cylindrical filter screen, with millions of conical, lasered borings, available in graduated filter fineness. When passed through by the melt, the contaminations are hold back on the surface of the filter drum, the filtered melt flows to the center and is conveyed to downstream equipment of the extrusion line. The filter drum, which is driven by an infinitely adjustable servo motor, takes the contaminations on the surface continuously to a scraper by its slow speed rotation.
At this point the scraper takes off the contaminations and forces them to the discharge shaft, which moves them out of the filter system to the atmosphere. The rotation speed of the shaft is also infinitely adjustable according to the current contamination content. Upon this new discharge shaft design concept, it is possible to process even low viscous materials like PET. As well the flow design of the ECO melt filter was modified. The more equal and smooth flow across the complete width of the filter drum, comparable to a film die, was achieved by a hanger distribution design.
Analog to the advantages of the ERF, also the ECO removes all contaminations with every turn from the filter screen surface. A blinding of the screen by accumulated contaminations, as it happens to conventional screen changers (even with backflush option) and their static screens, is generally prevented. The ECO solves the serious disadvantage of the pressure increase because of the blinding screen by the continuous cleaning of the filter screen surface. This continuity is reflected in the constant pressure of the whole process, at the extruder outlet as well as to the downstream equipment.
The time course and the relation of the melt pressure in front and after the filter screen are important parameters for the control system of the filter system. In case the contamination content is varying, the rotation speed of the filter drum and the discharge shaft, both are adjustable independently, are adapted to the new situation. Because the filter offers a constant open filtration area during production, it works in a process safe and stable condition. Due to this, this filter separates difficult to filter particles like paper and paint but also rubber and silicon or very fine aluminium particles. Thus the ECO melt filter opens new possibilities to increase the use of significant cheaper recycling material or, at least, to replace virgin material at 100%, if the final product allows.
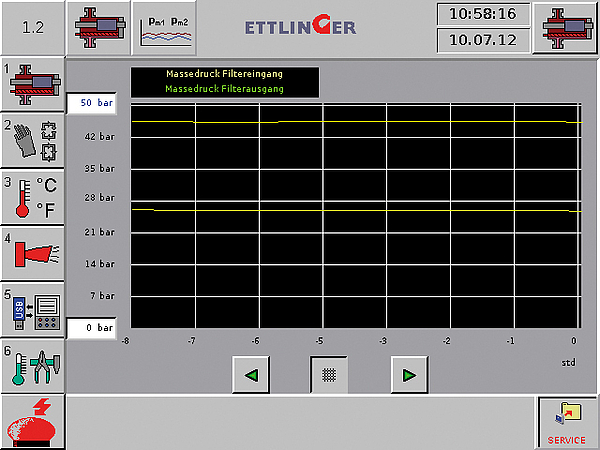
FIG. 3: Constant pressure on inlet and outlet side
...also for existing extrusion lines
The compact design and small footprint of the ECO melt filter allows an easy integration into existing extrusion lines.
The requirements of the customer with the PET thermoforming film application were exactly met. Now he can use 100% bottle flakes, even of poor quality. The pressure level is constant and significantly below the critical limit for several weeks without any operator assistance.
The positive result from the installation of the ECO creates new ideas. The maximum contamination content, the ECO can handle, is at about 1-1,5%. A percentage standard screen changers, even with complex backflush mechanisms, are not able to deal with and therefore never were in focus. Now specific savings in the pre-cleaning process of the bottle flakes, with higher contamination contents, which are removed by the ECO melt filter, can reduce material costs furthermore.
But not only material costs are able to improve the production balance sheet. Another case study:
For a customer, producing PET strapping band, the existing backflush screen changer is the bottle neck of his process. On one hand the pressure increase of the blinding screens causes particles to be pushed through the screens and often causes the straps to tear off. On the other hand the throughput capacity is limited. At a higher throughput the contamination particles would blind the screens even faster, which would request for a higher backflush frequency with all its negative influence.
But not only this limits the maximum throughput capacity of the line. To balance the volume, which is taken from the melt flow and diverted from the backside through the screens to the atmosphere for cleaning, the extruder has to save up a reserve of 10-20%. When starting the backflush procedure, the extruder speed is increased, to have still enough melt downstream despite the amount which is purged outside for backflushing.
By installing the ECO and taking benefit from its continuous cleaning of the filter drum, the limitation for the throughput capacity is removed. An increase of the throughput up to the maximum of the line, that can be easily in a range of 200-300 kg/h more than before, results in an efficiency improvement of the line and means again a faster amortization of the investment for the ECO melt filter.
Which development the market and the quality of PET bottle flakes will take, with the right filter solution the PET bottle flake processors are equipped for the future.
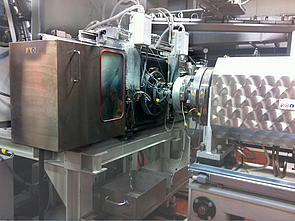
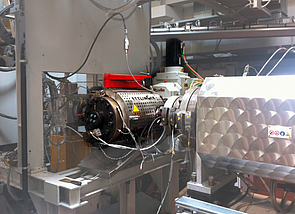
FIG. 4: Replacement of existing screen changer in a PET thermoforming film line
The comPETence center provides your organisation with a dynamic, cost effective way to promote your products and services.
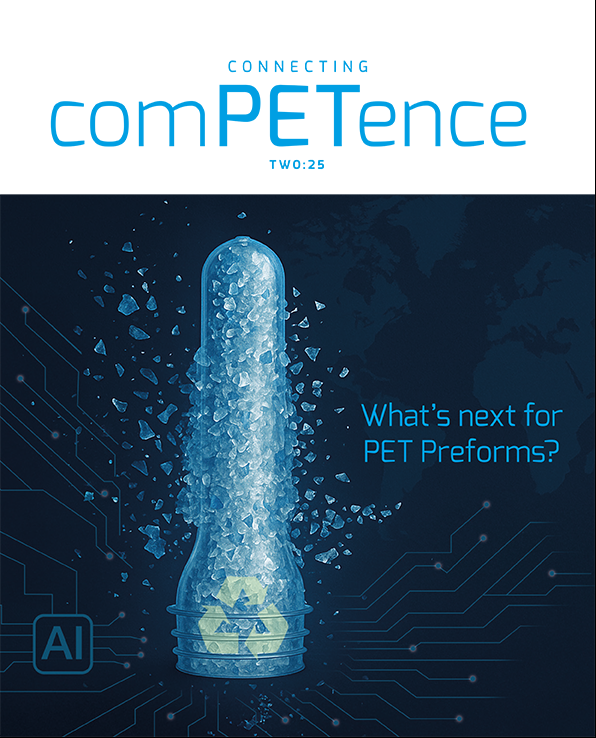
magazine
Find our premium articles, interviews, reports and more
in 3 issues in 2025.