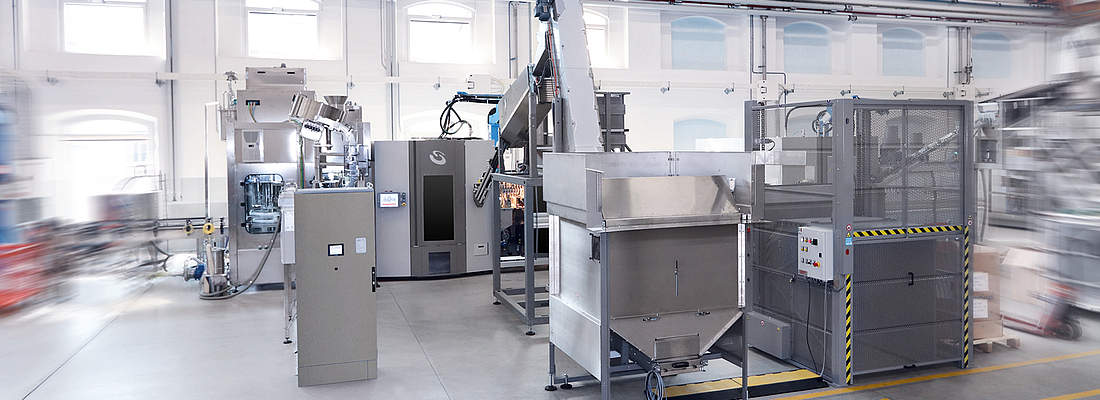
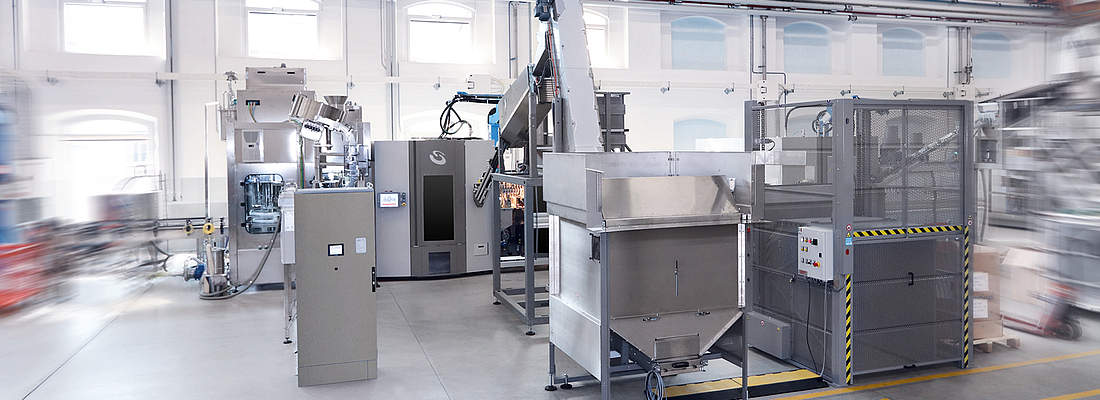
The environment has become a collective asset that everyone must take care of and this aim can be achieved by investing in industrial plants equipped with “green” technology, which save energy and reduce the environmental impact of production.
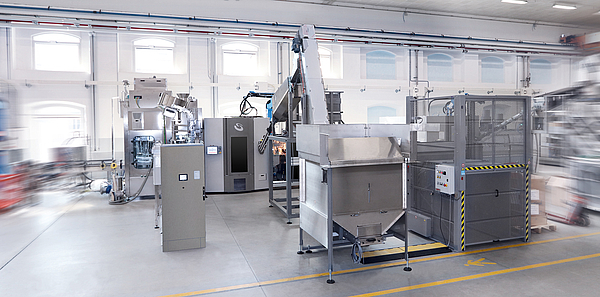
Companies in the food and beverage industry are reviewing their production processes to make them as ecosustainable and competitive as possible by making use of “smart and green” technologies of industrial automation and recyclable and biodegradable packaging. The sustainability of entrepreneurial activity is a demanding and strategic choice, made up of large and small objectives that are achievable thanks to a particular cultural attitude and continual investments, in new plants equipped with IoT (Internet of Things) technology, that allow the machinery to improve and adapt independently to the new production requirements of the XXI century.
Packaging sustainability
Packaging sustainability is a key issue, in particular for the beverage industry, in which more and more questions have been raised about the material to be used for safe packaging, with limited impact on the environment.
Recent studies have shown the benefits arising from the use of plastic bottles, since this solution is unbreakable, safe, with great barrier properties, lightweight and above all recyclable! In comparison with other packaging materials, such as glass or aluminum, PET has a good environmental profile, mainly thanks to its lightness that translates into less material to produce, less material to dispose of, less energy used to manufacture it and less fuel used for transporting packed products. Thanks to its recyclability and its great weight-capacity ratio, many producers of mineral waters and soft drinks promote and re-evaluate PET and r-PET as convenient and win-win solutions from the environmental sustainability point of view.
The use of r-PET (recycled PET) for manufacturing new bottles is the core of the concept of circular economy, that consists of collecting materials after they have been used and processing them, so that they can be reused or recycled. Every time a PET container is recycled, its oil reserve is recovered and reused, eliminating the waste and reducing the packaging environmental impact, provided that efficient systems for managing waste and recycling exist. rPET is processed on SMI stretch blow moulding machines in stand alone version or integrated with an electronic filling and capping module and shows no significant restrictions in terms of quality, safety and workability.
The case of Eaux de Volvic
When we talk about water purity, it is inevitable to think of the accurate work carried out by the Societé des Eaux de Volvic, company part of the Danone Group that has continuously invested in new solutions for preserving the quality.
To achieve these goals, the company decided to invest in high tech machines and installed a SMI’s ECOBLOC® ERGON HC integrated system for stretchblow moulding, filling and capping 8 L containers, with a square bottom, in 100 % recycled plastics (rPET).
________________________________________________________________
''Companies in the food and beverage industry are reviewing their production processes to make them as eco-sustainable and competitive as possible by making use of “smart and green” technologies of industrial automation and recyclable and biodegradable packaging.'' - Pietro Volpi - Marketing Manager SMI
__________________________________________________________________
Designed to ensure respect for the environment, the new eco-friendly bottle is the result of joint work between the specialists at Danone and at SMI, which has allowed to develop a preform able to guarantee the constant resistance of the container during the stretch-blow moulding process.
By using recycled PET in beverage bottles, every company can contribute in respecting the environmental and in developing an eco-friendly bottle suitable for the circular economy.
The complete Volvic production process was designed so that every step of the bottling is kept under constant control, because it is here that the water, coming from the deep underground, comes into contact with the external environment and is at a greater risk of contamination which would compromise the sensory, chemical, physical and microbiological properties. The Société des Eaux de Volvic SA, also, pays particular attention to everything that concerns sustainable development, environmental respect, product quality and purity, for this reason the whole bottling, packaging and distribution process was designed around these values and the machine supplied by SMI was integrated with sophisticate inspection systems, which, starting with the preforms, carry out a long series of checks to maintain the quality and purity of the spring water.
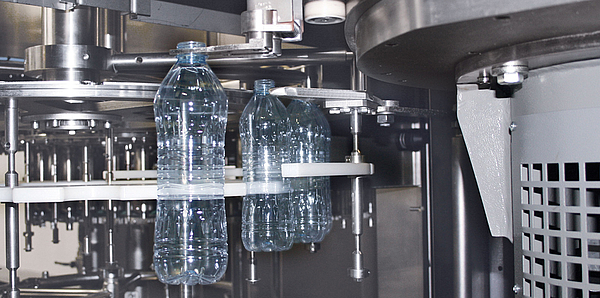
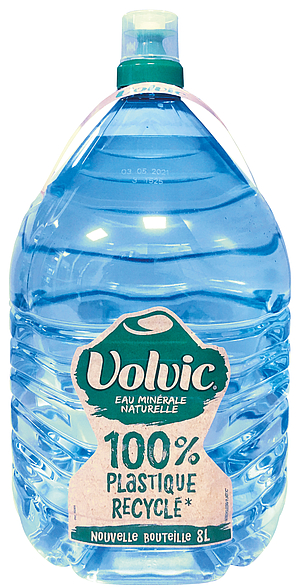
Smart and green technologies
Main advantages of the integrated system of ECOBLOC® ‘s series:
- compact, flexible solution for stretchblowing, filling and capping bottles in PET, with the advantage, in terms of reducing production costs, as the system does not need a rinser, nor conveyors between the blower and the filler or accumulation
- isolating system between the “dry” area of the blower and the “wet” one of the filler, through a jet of high pressured, sterile air in excess of 5Pa, which guarantees a clean, hygienic filling system. The air flow, through 4 units of Galvani filters (HEPA filters) situated on the top part of the filler area, spreads around all the interested area to avoid contamination, acting as a “clean room”. In addition, the filling valve is controlled by an electronic flowmeter.
- application of various accessories to guarantee that the filling system is extremely clean and easy to sanitize with advanced cleaning systems
- innovative preform suction system, situated on the oven in-feed star, to remove any tiny impurities that could be on the inside of the preform itself. The air that is inserted into the suction system is filtered, and is part of the air recovery system that comes as standard on all the range of SMI stretch-blow moulders. The system combines blowing air into the preforms with the following vacuum suction process.
- machine integrated with sophisticated inspection systems with cameras to guarantee the quality of the bottled water, monitor the production process and avoid particles and/or impurities being deposited on the inside of the unblown preforms
- the preforms are blown with sterile air in a sterile environment; this sterility is maintained for all the process of filling and capping
- precise and fast operation, thanks to the electronic, operation control, to motorized stretch rods and the use of high efficiency valves with flowmeters
- reduced energy consumption: the stretch-blow module is equipped with a double stage air recovery system, which allows the reduction of energy costs tied to the production of high pressure compressed air
- high energy efficiency, thanks to IR lamps fitted onto the preform heating module
- filler area compatible with COP (Cleaning Out of Place) and equipped with optional system of stainless steel bulkheads to separate the “wet” area of the filler with the “dry” area of the blower during maintenance or cleaning operations. The bulkheads can easily be installed on the filler infeed, with a star on the blower that can be disassembled, and on the out-feed, on the channel of the bottle out-feed.
- electronic components positioned on the inside of the panels to make sure they have greater protection from the damp
- base of the filler area is made in stainless steel 316 and slightly sloped to ensure that any leak liquids go down the drains
- electronic capper equipped with cap orienting during application, system to control correct positioning of cap and a rejection system for over turned caps
- cap sterilization through jets of ionized air on the cap channel
- washable cap accumulation table, in stainless steel, equipped with an optional system to suction the caps to remove any impurities that might have deposited on them while moving along the hopper
- reduced maintenance and running costs of the machine.
Top quality bottle means excellent preform and bottle inspection system
The increase in production speed of bottling lines, the use of lighter containers, and the change in laws that are stricter, in terms of food product quality and integrity, force companies in this sector to use cutting edge technology equipped with advanced inspection systems for preforms, bottles and caps, this way preventing any non-compliance issue or contamination. To satisfy the quality standards of the Danone group, the ECOBLOC® HC ERGON supplied by SMI, is equipped with sophisticated Pressco inspection systems, leader in the inspection sector for containers in PET and reference point for all the companies which, like Volvic aim at having excellent quality standards.
Preform inspection systems verify that no particles and/ or impurities are present in the preform and guarantee different advantages as:
- avoid particles, stains and/or impurities inside the preform, to maintain the quality of the bottled water
- inspection system using three cameras installed inside the oven to check the colour of the preform, the presence of micro-holes in it or any scratch, physical or cosmetic deformation
- If non-compliant preforms are found they are immediately ejected from the production process, avoiding the next production steps; if these defective preforms were blown, it would be a waste of the bottles, generating expensive damage to plant efficiency
- The inspection system installed on the Volvic ECOBLOC® HC allows the complete preform check in all the critical areas and ejects the defective ones in the very first stages of the bottling process.
Bottle inspection systems verify the integrity and quality of the mouth of the blown bottle and offer the following advantages:
- system fitted on the blower out-feed star, giving the advantage of inspecting the internal edge and the outside of the mouth of the freshly blown bottle identifying any small breaks or abrasions
- allows defective bottles to be ejected so that only bottles that are up to standard will be filled and capped correctly
- avoids problems with cap application, as it ejects containers with defective mouths before they get to the filling and capping stages
- inspection system equipped with its own operation control panel, that interacts with the POSYC® control system installed on the machine for an improved, more complete analysis of the functional parameters. In this way the blower POSYC® can manage every process on the ECOBLOC® machinery: preform in-feed, oven, stretch-blowing, filler, cap in-feed, capper and all the optional devices for inspections and controls
- the integration of this inspection system inside the blower is advantageous as it allows constant monitoring of the process and the immediate ejection of any defective containers to produce high quality bottles at a reduced cost
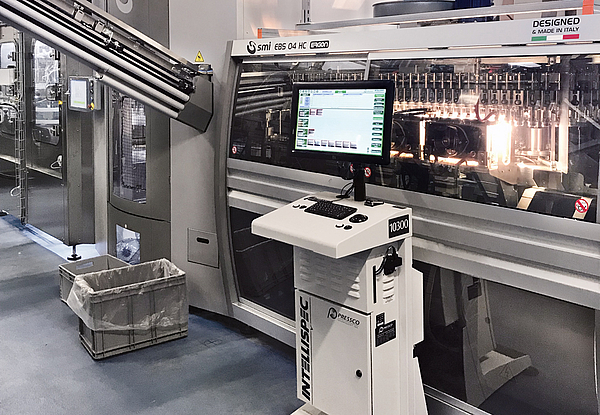
The second life of packaging in a circular economy
Designed especially to give families the possibility to enjoy the uniquely, precious, Volvic mineral water, in a way that respects the environment, the new 8L eco-bottle was created in 100% recycled plastic (rPET) and is 100% recyclable! It is the first totally, recyclable container launched on the market. For Danone, the future of plastic bottles in the beverage industry will move towards rPET and therefore, it is betting on this material. In fact, the water division of the French multinational is a great user of plastic bottles for its products under the Evian, Volvic, Badoit and Salvetat brands, and it is already thinking about bottling them in rPET made from 100% recycled plastic.
The bottle created by the ECOBLOC® ERGON HC EV, supplied by SMI, will be the first 100% rPET water container on sale in France, seeing that 8L containers have already captured 10% of brand value sales, and with an important growth of 13,1% in 2018, the success of the new totally, recyclable format is guaranteed. Creating an 8L PET container in 100% rPET is the result of joint work between the specialists at Danone and at SMI. SMI provided the French technicians with one of their own stretch-blowers, so that they could carry out a series of blowing tests while accurately testing the preforms and bottles, these tests allowed them to regulate the “top load” resistance and the material distribution, a step at a time, developing a specially made preform with a specific shape. The biggest challenge, when using recycled preforms, is to guarantee the constant resistance of the bottle when it is being blown, this operation is very difficult with preforms made from recycled material.
The comPETence center provides your organisation with a dynamic, cost effective way to promote your products and services.
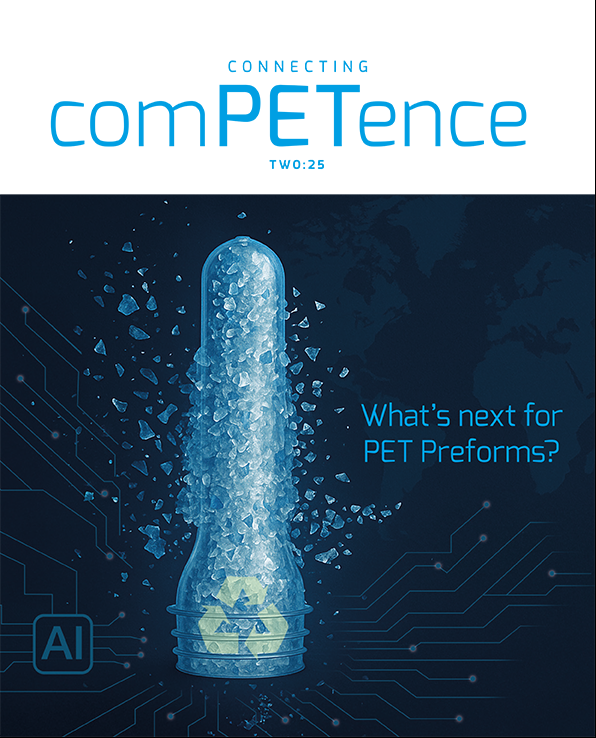
magazine
Find our premium articles, interviews, reports and more
in 3 issues in 2025.