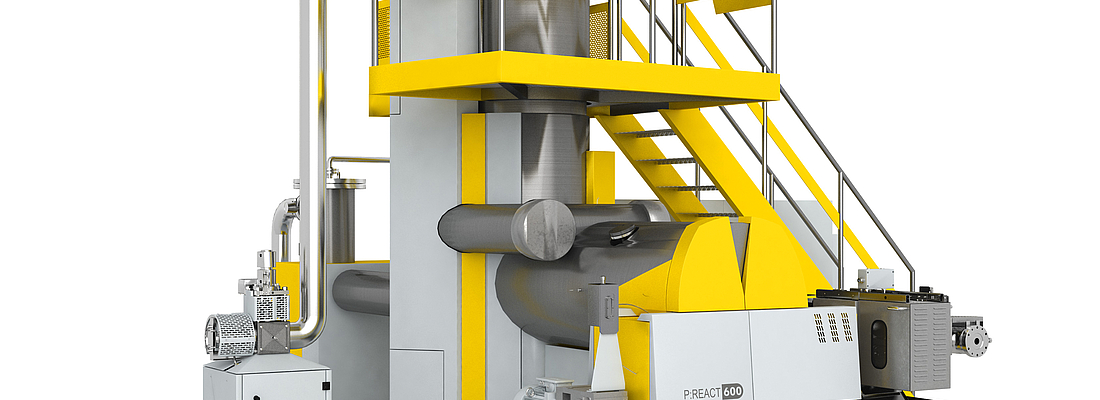
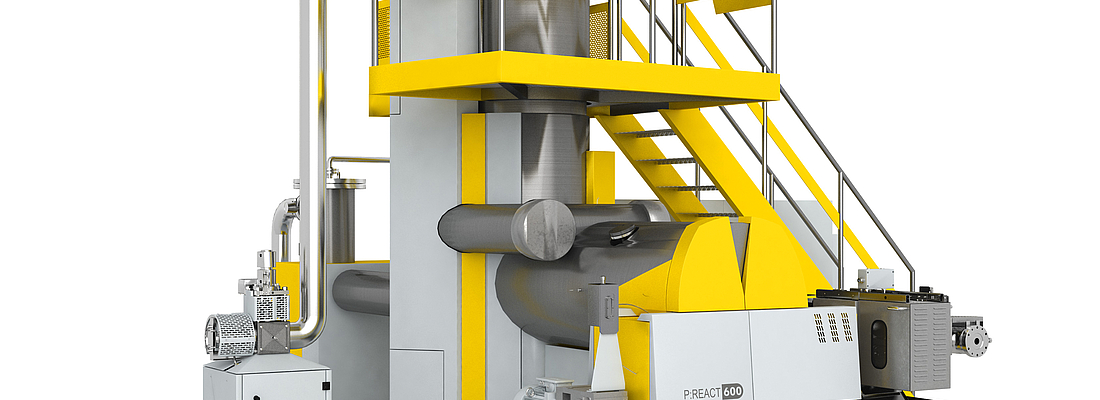
Introducing new technology in the field of plastics-recycling has always been the aim of Next Generation Recyclingmaschinen GmbH from Austria. The LSP process (Liquid State Polycondensation) for PET recycling combines the increasing of Intrinsic Viscosity (IV), excellent decontamination properties with low energy consumption.
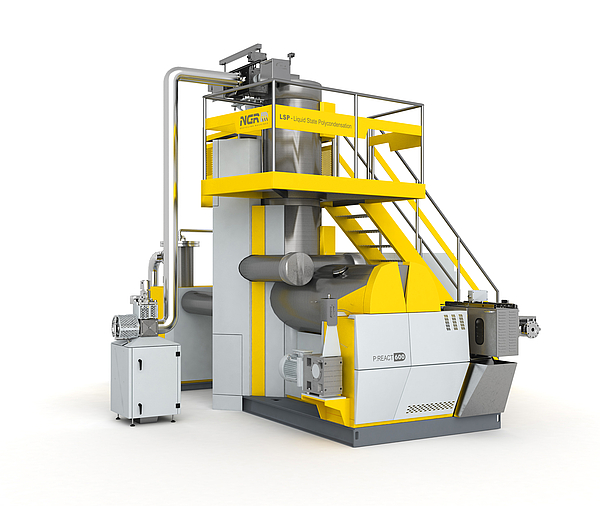
PET is a material broadly used in food-packaging, such as for soft-drink-bottles or PET-trays. In this field the global annual consumption reaches some 20 million tons. The PET fiber business is approximately double as big. Reasons enough to rethink the general approach of recycling the material and starting to take full advantage of the PET-properties by designing a new process.
Improving PET-properties in the Liquid State
As all polymers, also PET consists of polymer chains. The length of the chains determine the strength of the material and the viscosity (measured as IV-Value). Each step in processing the material (fiber spinning, film extrusion, injection molding, etc.), leads to “breaking” some of the chains apart, thereby causing the material strength being reduced and the viscosity of the material being lowered towards easier flowing. Due to the petrochemical manufacturing of PET – so called polycondensation – the polymerchains can be restored in length again. The traditional method of achieving this is “Solid State Polycondensation” (SSP). Crystalline pellets or PET bottle flakes are here heated to about 200 to 240°C and kept at this temperature for several hours, allowing an increase of the IV by approx. 0,01 to 0,02 dl/g per hour resp. 0,05 to 0,06 dl/g in the case of flakes. The “Liquid State Polycondensation” (LSP) on the other hand takes advantage of the material being at a higher temperature range (270 to 280°C) and therefore an increased reaction-speed of the polycondensation. The LSP-Process can increase the IV-Value by 0,01 to 0,02 dl/g within minutes and keeps the desired IV within a narrow range of 0,015 dl/g.
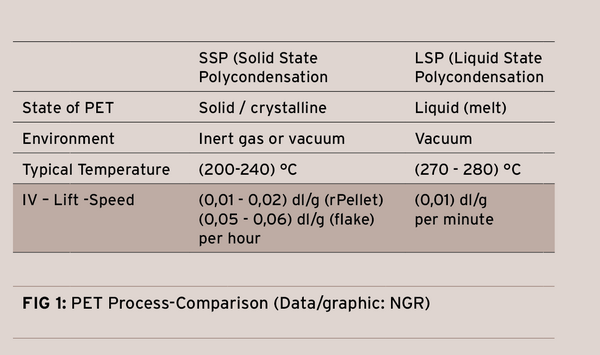
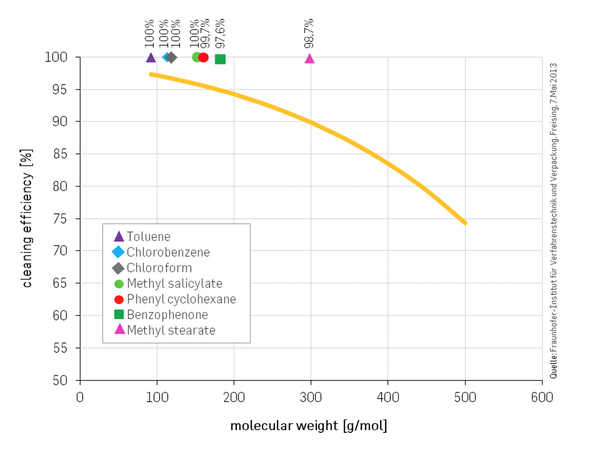
FIG 2: Decontamination Performance of the LSP-Process
(Data: Fraunhofer IVV)
FDA Non-Objection-Letter for 100% Food Application issued
The backbone of the LSP-Process is the P:REACT. In this reactor the surface/volume-ratio of the molten PET is increased by forming strands, furthermore high performance vacuum is applied. This configuration enables easy decontamination of the material from harmful chemicals and makes the LSP process most suitable for food-contact. A “challenge-test” conducted by Fraunhofer IVV/Germany provides the required scientific evidence for the decontamination-performance of the process. In this test PET bottle flakes are purposely contaminated with various different chemicals. These flakes are then recycled by the LSP-Process and the remainders of the chemicals are analyzed by Fraunhofer. The graph shows the cleaning-capacity of the LSP-Process being close to 100%. The yellow curve indicates the requirements by EFSA (European Food Safety Authority). Based on these tests FDA has issued the No-Objection-Letter for applications in 100% food-contact in November 2013.
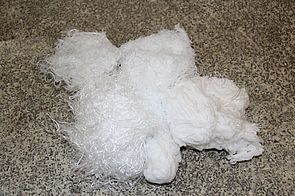
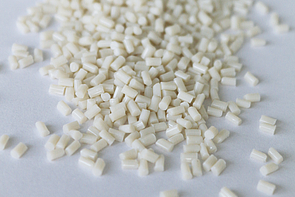
FIG 3: Input material PET scrap from spinning / rPET-pellets after recycling
P:REACT demonstrates outstanding performance
The first P:REACT unit was installed in March 2015 and is producing rPellets from fibre scrap. The PET-fibres are collected from various points in the spinning process and contain up to 15% of spin oil.
A shredder-feeder-extruder combination provides the PET melt and a first degassing. As the PET melt is introduced into P:REACT the IV is lifted from 0,62 dl/g to 0,66 dl/g within a variation of less than +/- 0,015 dl/g. The required elimination of the spin oil content comes automatically with the high decontamination performance of the unit. The equipment owner reuses the rPellets from P:REACT in his spin process simultaneously with virgin PET without any spin process adaption.
The simplicity of P:REACT involves only two parameters of control: the level of vacuum and the residue time of the molten PET inside the equipment. The IV is measured inline and provides a signal for the automatic control of the machine parameters. This together with a simple reactor configuration ensures easy operation and low maintenance costs.
Highest Energy Efficiency
P:REACT works extremely energy efficient, as the reactor only requires energy for maintaining the heat-level of the molten PET. Energy measurements at P:REACT show a specific consumption of only 0,12 kwh/kg including pelletizing. Below figures reflect the processing of PET fibers at IV of 0,62 dl/g, an output of 350 kg/h on a shredder-feeder-extruder combination. The rPellets are showing an IV of 0,70 dl/g.
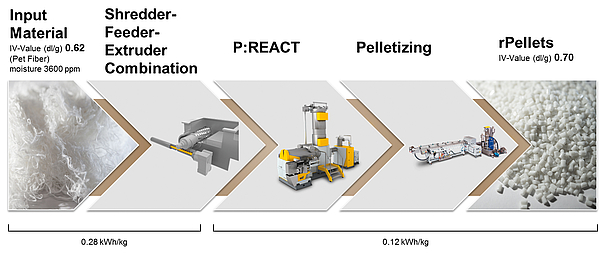
FIG 4: Processing example
Versatile application of P:REACT for recycling of PET products from various sources
In the upcoming months more P:REACTs are to be installed. For example, one unit for in-house recycling of thermoforming skeletons with an output of 2,000 kg/h and another stand-alone unit for used PET-carpet recycling.
Extensive tests on the processing of bottle flakes, preforms, PET-woven, etc. have demonstrated the capabilities of P:REACT to be most versatile. In the case of recycling PET-bottle flakes, tests have shown the system to be suitable for exceeding brand owner specifications.
The comPETence center provides your organisation with a dynamic, cost effective way to promote your products and services.
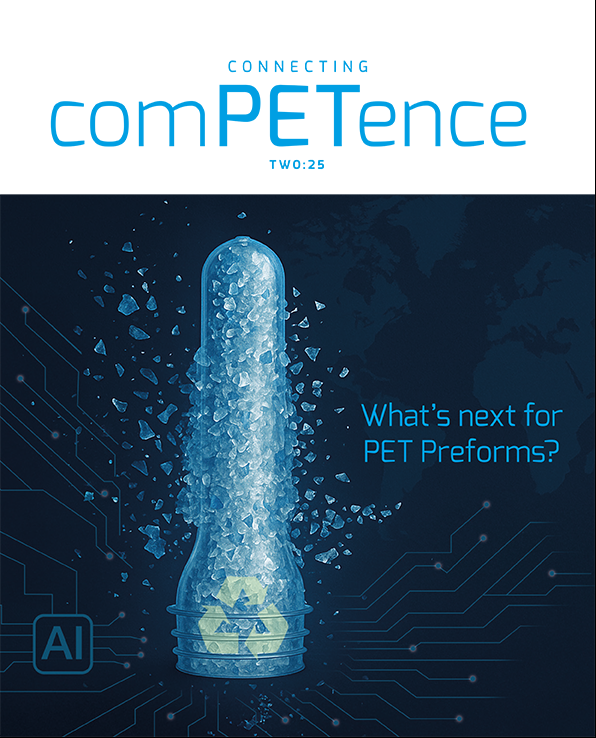
magazine
Find our premium articles, interviews, reports and more
in 3 issues in 2025.