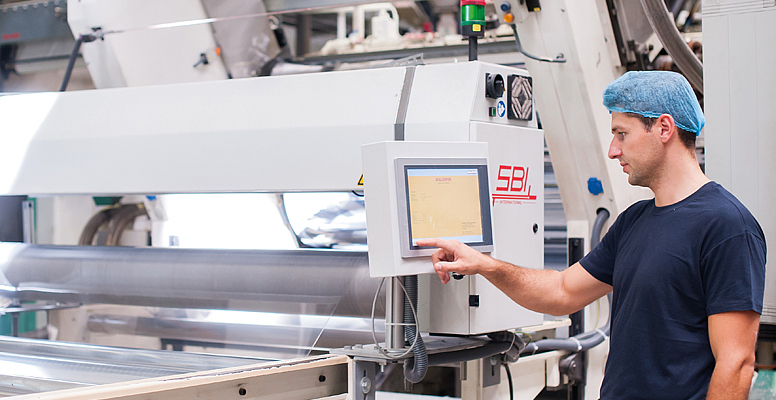
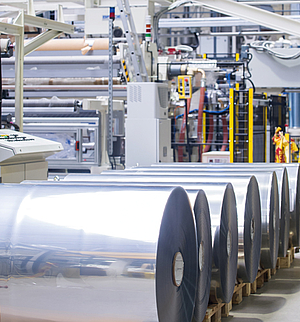
RETAL creates responsible alternative to black carbon masterbatch films
Popular in non-food and food-grade packaging for meat, fish, dairy and ready meals, black and metallized films are currently very difficult to recycle as the infrared is absorbed by the carbon instead of being reflected towards the sensor, rendering the material invisible. As part of a global circular economy strategy, RETAL Baltic is installing a state-of-the-art line to process more r-PET and PET scraps, and is gradually moving away from black masterbatch with carbon to create more circular black and metallized films that are easily recognized in standard recycling sorting facilities.
Investment in the new extrusion line at RETAL Baltic means the global plastic packaging manufacturer is continuing to provide greater volumes of rPET film, with 100% rPET films now able to be produced. Robertas Grizas, RETAL Baltic’s APET Production Development Manager, says, “We want to ensure that we are maximizing the value of plastic waste, both post-industrial and post-consumer. By investing in this new extrusion line – which can process all types of PET scrap, we can produce food-grade black and metallized rPET film that can be recognized by recycling sorting equipment as it uses an alternative to black carbon masterbatch, and we can also use up to 100% rPET flakes in its manufacture.”
As thermoformer and brand owner customers increase their demands on the sustainability credentials of their packaging, global plastic packaging manufacturer RETAL is proud to move forwards alongside them. Grizas continues, “There’s no need to incinerate or send black and metallized films to landfill anymore as RETAL can effectively reprocess it back into production for food-grade packaging for global brand owners.”
The new RETAL Baltic extrusion line will further boost the company’s commitment to the circular economy by processing waste from multilayer films as well as the black and metallized films. Grizas adds, “RETAL has acquired the technology to use hard to recycle post-industrial waste that we collect from our customers. RETAL produces transparent and colored films, including black and metallized, and though there has been a tendency for thermoforming customers to prefer transparent films to colored and metallised, now RETAL can help with their post industrial waste to be processed it into food-grade films. It is crucial to keep black rPET in the plastic packaging value chain as it allows for all colours of scrap to be mixed when reprocessed into rPET and promotes its use, so RETAL is delighted to be creating more circular black rPET film.”
RETAL’s Sustainability Director Emmanuel Duffault appreciates that this latest investment is another positive step in the company’s progressive position on developing and producing more sustainable and circular plastic packaging. Duffaut says, “By investing in new technology that can efficiently process up to 100% rPET flakes and by improving the recyclability of our products using non-carbon black masterbatch, we are further illustrating our commitment to providing thermoformers and brand owners with plastic packaging that combines convenience with sustainability.”
Near infrared masterbatch for recycling black and coloured plastics
Gabriel-Chemie | Gumpoldskirchen | Austria
Plastics‘ recycling in the EU has increased by almost 80 % since 2006*. During the same period, landfill disposal has significantly declined by 43 %. The problem when it comes up to recycling is the fact that some black and coloured plastic items do not get recognized by detecting/sorting machines. That is why these pieces are still disposed as landfill or incinerated to produce energy. So the common use of carbon black still issues the big challenge with it.
The reason resides in the fact that sorting machines usually work with near-infrared (NIR) sensors. However, plastics items that contain carbon black absorbs the light signal instead of reflecting it, and the product is not detected, thus not sorted and end up its service life as landfill mass or as an incineration mass.
Gabriel-Chemie introduces a professional solution for NIR-detectable and sortable
thermoplastic masterbatch colours. The NIR reflective masterbatch is made by using special pigment formulations which enable the correspondent sorting and recycling, is food contact approved and even laser markable.
So far, black and dark coloured plastics have had a major problem: the carbon used for darkening plastics absorbs a large part of the radiation in the visible and in the infrared wavelength range. Therefore, it has not been possible to obtain a sufficient signal from black and darkcolored plastics so far, and consequently it was not possible to differentiate and sort them into plastic types.
The masterbatch can be extruded, blown or moulded by injection, compression, etc. Solutions made with Gabriel-Chemie’s NIR masterbatch have no lower mechanical properties than products made by carbon black-based products.
With the use of our NIR detectable masterbatch, black and dark coloured plastic articles can be properly sorted and recycled using NIR sensor technology. (Photo credit: Gabriel-Chemie)
Diego A. Karpeles, Corporate Brand Manager, affirms: “Our masterbatch solutions are the perfect choice for plastics that are intended to be reused or recycled and they can be produced applying the ISO norms 9001,14000 (environmental management), 22000 (food contact materials) and even 13485 (medical devices).
By offering NIR-detectable masterbatches we are going a strong-paced step towards increasing environmental sustainability”.
____________________________________________________________
*(Source: Plastics, The Facts 2018, Plastics Europe, Association of Plastics Manufacturers, AISBL)
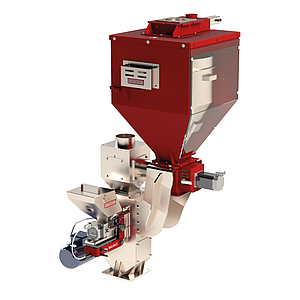
Movacolor makes the use of non-repalletized regrind in standard injection molding machines and extruders possible
PolyOne | Avon Lake, OH | United States
The latest innovation by Movacolor is the unique MCHigh Output 2500R. The MCHigh Output 2500R of Movacolor allows plastic processors to use a high percentage low bulk density regrind up to 75%, without compromising the consistency of the end product.
The drive to use more regrind in high end plastic products is increasing rapidly. Some brand owners are setting their goals at 50% or higher. International laws are following and pushing the rest forward. An excellent development, but it creates a lot of problems for many plastic processors. Their injection molding machines or extruders are not designed to cope with large amounts of non- repalletized flakes.
Repalletizing regrinds, like R-PET, can solve this problem partly but the re-palletization process requires a lot of energy, destroys part of the sustainable goals and increases the cost. Replacement of screws or complete extruders is very seldom economically feasible. A better solution is to use specialized upstream equipment to allow large amount of nonrepalletized regrind to be used in standard extruders.
Especially for this reason Movacolor has developed the MCHigh Output 2500R. This system allows low bulk density regrind, such as bottle flakes, to be dosed at rates of around 700 kg/hr. The unique combination of the static and dynamic mixer can mix up to 75% of flakes into the main material. This allows plastic producers to achieve the required use of regrind easily, without the need to use re-pelletized material.
The MCHigh Output 2500R of Movacolor is fully gravimetric controlled and because of the compact, integrated hopper loader, the height of the total system is limited to fit in almost every standard factory. It can be used for dried materials up to 180 degrees Celsius. Like every Movacolor system, this system is modular build and can be extended with 1 or 2 gravimetric dosing stations, allowing to dose color and additives in line.
The color and/or additives can automatically be compensated for the amount of regrind if required. There is also the possibility to install magnets in this system. The complete system is controlled by the standard Movacolor 8” touch screen controller and is able to communicate with almost every system. The OPC-UA communication protocol makes it fully Industry 4.0 ready.
This special dosing system and other products will be on displayed at K 2019 in Hall 11, Stand D58.
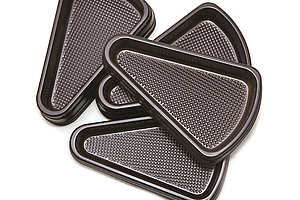
New black colorants: Polyone support circular economy, turn former waste into recyclable packaging
PolyOne | Avon Lake, OH | United States
PolyOne launched a new portfolio of infrared- detectable black colorants for plastic packaging, which will allow formerly unrecyclable black waste plastic to be properly sorted at recycling facilities. These colorants will help black packaging support the circular economy by enabling them to be recycled rather than landfilled.
OnColor™ Infrared Sortable Black for Recyclable Packaging contain no carbon black pigment, permitting the automatic optical sorting sensors used in many waste management plants to detect black polymers and sort waste into the correct recycling streams.
Detection and sorting of carbon black-filled plastic waste in material recovery facilities is a vexing issue for the packaging and recycling industries, because the equipment relies on the reflectance of near infrared (NIR) wavelengths. Carbon black makes it impossible for the equipment to identify the waste, which must then be sent to landfill or incineration.
PolyOne’s new black colorants address this issue by eliminating carbon black and enabling black plastics to be sensed, sorted, and recycled efficiently. They can also help brand owners to retain current black packaging that was deemed unrecyclable. OnColor™ Infrared Sortable Blacks for Recyclable Packaging is available in both liquid and solid form in a range of eight black shades as well as custom colors.
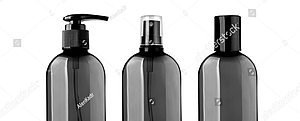
Clariant Additive Masterbatch makes black plastic packaging ‘visible’ to sorting systems
Clariant | Muttenz | Switzerland
New Clariant CESA®-IR additive masterbatches are now available to make dark-colored plastics visible to the nearinfrared (NIR) sensors used in automated polymer sorting systems. While many companies use black packaging to brand their prestige products, the problems it poses in recycling systems has led to calls for black to be phased out of the palette. The new masterbatches help to resolve that issue and allows increased recycling rates in Europe and elsewhere.
The new product range is part of a ‘Design for Recycling’ program at Clariant. Recognizing that recycling is the foundation of a Circular Economy, Clariant Masterbatches and its Packaging Market group, is mobilizing substantive resources
across the packaging value chain to ensure that an ever-higher percentage of plastic packaging is recycled.
In most automatic sortation systems, infrared light is beamed onto packaging materials and, because different polymers reflect that light differently, NIR sensors can discriminate between high-density polyethylene, low-density polyethylene, polypropylene, polyester and various other commonly used polymers in today’s packaging. Unfortunately, the carbon black pigments typically used to make black plastics absorb all or most of the NIR light shone at them. As a result, the sorting sensors cannot even “see” the black packaging, much less sort one polymer from another.
“As a result of this phenomon,” explains Alessandro Dulli, Clariant Masterbatches Global Head of Packaging, “much of the dark-colored materials entering the recycling stream has not been recovered. For that reason, many brand owners have been pressured to move away from black for environmental reasons. In close collaboration with these brand companies and as a leader in sortation technology, Clariant has developed a way to achieve a persuasive black color in plastics without compromising the essential detectability during recycling process.“
Specific CESA-IR formulations have been developed to enable IR-detectability of black HDPE and LDPE in injection and extrusion blow-molded products; black polypropylene (PP) in films and injection-molded products; and black PET and C-PET in sheets and film. In testing conducted by Tomra Systems ASA, a Norwegian company that is a leader in the field of instrumentation for recycling solutions, polypropylene (PP) containing carbon black was essentially indistinguishable under NIR radiation from background surfaces such as a conveyor belt.
However, the same material made using another coloring system including CESAIR additive masterbatches was readily detectable, with reflectivity levels approaching those of uncolored PP.
The comPETence center provides your organisation with a dynamic, cost effective way to promote your products and services.
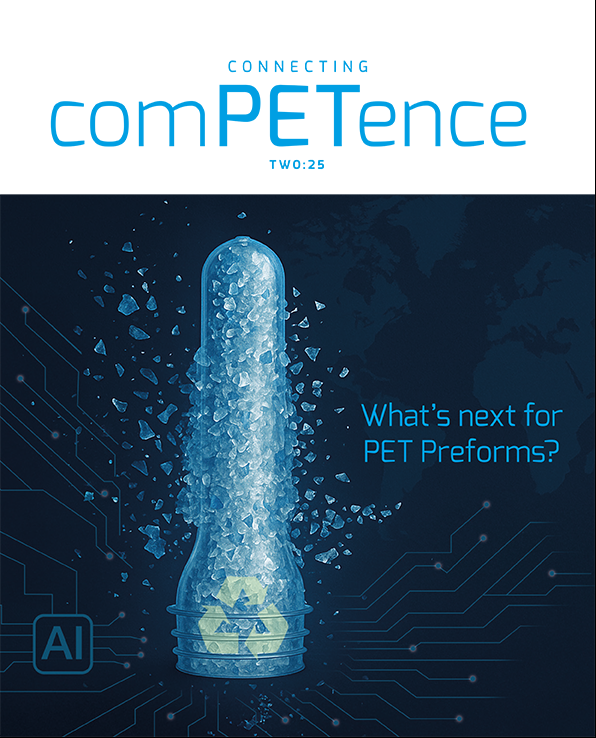
magazine
Find our premium articles, interviews, reports and more
in 3 issues in 2025.