The machine technology in the field of the two stage stretch blow moulding process faces the challenge of producing increasingly complex hollow bodies while saving production costs at the same time. New approaches in the development of the heating stage like laser heating or microwave heating meet these challenges. Both technologies reduce the energy consumption compared to the common IR heating and furthermore, in case of the laser heating, allows sharper temperature profiles which enable more complex hollow body structures [URL18a]. In this context, this article is intended to provide a brief overview of these technologies.
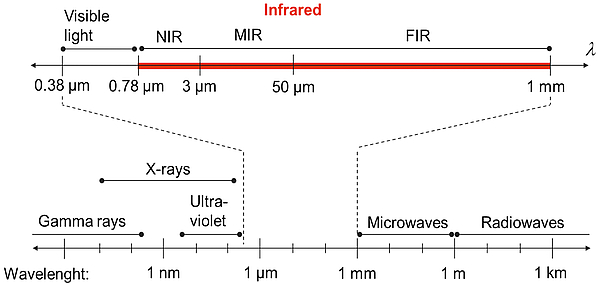
Fig 1: Electromagnetic spectrum and wavelengths of NIR infrared and microwaves
RELEVANCE OF THE HEATING PROCESS FOR THE PROPERTIES OF HOLLOW BODIES
In the two stage stretch blow moulding process, an injection moulded preform is formed into a hollow body in the thermo- elastic temperature range [THG06]. This process leads to a hollow body with a certain material distribution that is the decisive factor for the quality determining properties as stacking strength or the haptics of the hollow body [App05]. The material distribution of the hollow body is decided through a large extent by the preform geometry and the temperature distribution of the preform during the forming process. The more complex the hollow body is, the more important the temperature profile becomes. Considering simple rotationally symmetric bottles with a uniform shape in their bodies, a homogeneous temperature distribution in the preform body might be sufficient to get a homogenous material distribution in the bottles body. In this case, the preform geometry has a dominant effect on the material distribution of the bottle prior to the heating process. Considering complex geometries, e.g. flat oval bottles, the rotationally symmetrical moulding process of the preform results in an early mould contact on the flat side of the mould and in a significantly delayed mould contact in the narrow sides of the mould [THG06].
In this case, preferential heating is used where a temperature profile is applied in circumferential direction on the prefom that leads to a homogenous material distribution in the bottle. The heating process has a strong influence on the material distribution of the bottle. Preferential heating enables a temperature profile in circumferential direction but due to the diffuse radiation of the infrared heaters the temperature profile in axial direction is rather vague. The beamed radiation of a laser offers the possibility to heat small areas of the preform, which allows a sharp temperature profile in axial direction and thus more precise adjustment of the material distribution that improves eventually desired properties of the hollow bodies.
FOUNDATIONS OF INFRARED, LASER AND MICROWAVE RADIATION HEATING OF PET PREFORMS
The aim of the preform heating is an equally distributed temperature inside the preform. The advantage of heat radiation compared to heat conduction and convection is, that the energy is absorbed inside of the preform and not only on its surface. In case of PET, the absorption behaviour depends strongly on the wavelength of the radiation.
Figure 1 shows the electromagnetic spectrum with the electromagnetic radiation and the corresponding wavelengths. According to ISO 20473 [NN07] infrared radiation can be subdivided into Near-infrared (NIR), Mid-infrared (MIR) and Far-infrared (FIR). The wavelength range for NIR is 0,78 ?m to 3 ?m. According to Wien’s displacement law the temperature range of a black body that is emitting NIR radiation are 3864 K to 966 K. In case of MIR, the wavelength range for NIR is 3 ?m to 50 ?m and the temperature range of a black body that is emitting MIR radiation is 966 K to 50 K. The temperature of the tungsten filaments in the heating stage of a stretch blow moulding machine is above 2000 K and thus the major share of the radiation is in the range of NIR.
The wavelength range for microwaves is 1 mm to 1 m. Microwaves offer a large field of application as radar, satellite communication and wireless networking technologies such as Wifi. With an increase of the intensity level, it can be used for thermal heating. The microwave heating is performed in the wavelength range of 10 cm to 1 m [NN84]. Compared to infrared radiation, the penetration depth is much greater in the range of the microwaves and thus a larger share of the radiation is absorbed inside the preform.
A laser is a device that emits light through a process of optical amplification based on the stimulated emission of electromagneticradiation.Theelectromagneticradiationofa laser occurs on a precisely defined wavelength. Depending on the type of the laser, possible wavelengths are from 100 nm to 1 mm and thus from ultra violet to Far-infrared. In case of preform heating, solid state and gas lasers are available in the range of NIR and MIR [Web99].
The wavelength of the radiation is important for the absorption behaviour as the transmittance of PET depends to a large extent on the wavelength. As stated at the beginning of this section, the radiation is absorbed inside of the preform and not only on its surface. The absorption rate of the radiation inside the preform can be described by the law of Lambert- Bougier in Eq. 1.
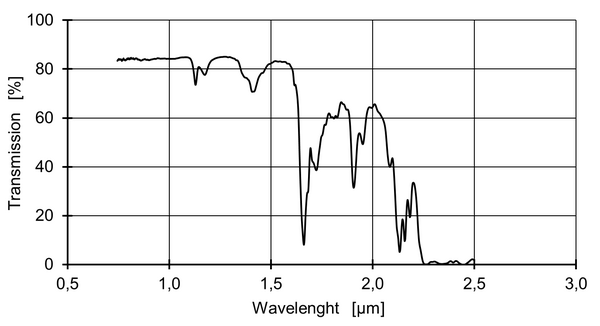
Fig 2: Transmission spectra of PET measured on a sheet
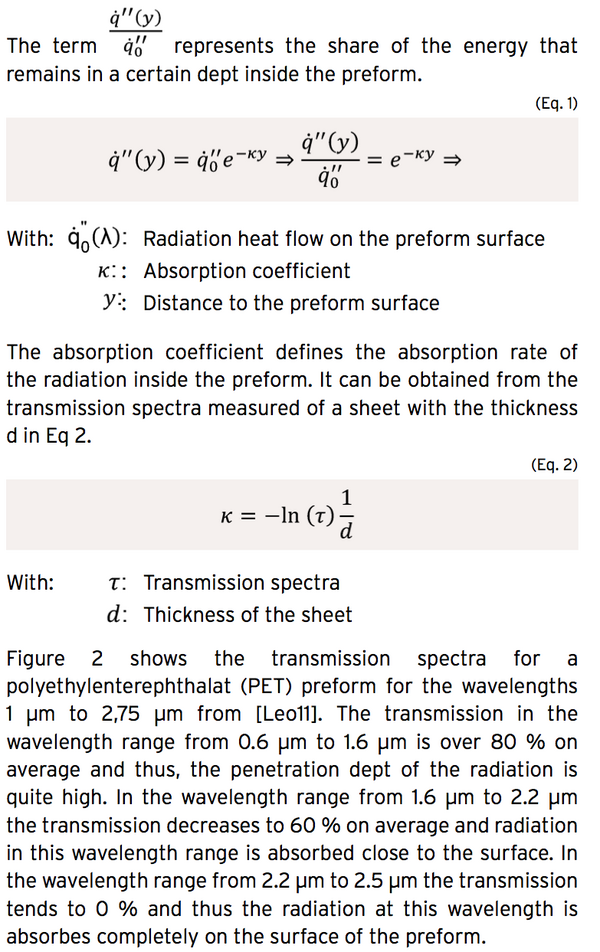
The share of the energy, that remains in a certain dept, considering a transmission rate of 80 %, 50 % and 2 % is shown in Figure 3. In case of a transmission rate of 2 %, the radiation is completely absorbed in the first quarter of the preform. In case of a transmission rate of 80 % and 50 %, the share of energy that is absorbed uniformly along the thickness of the preform, but at a transmission rate of 2 %, almost the whole share of energy is absorbed in the first half of the preform.
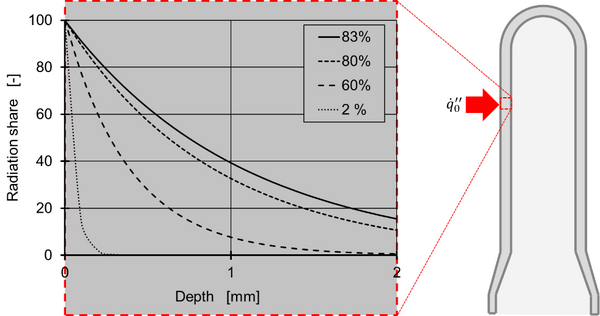
Fig 3: The share of the energy, that remains in a certain dept
Figure 4 shows the transmission spectra in combination with the radiation intensity emitted from a black body at 2400 K. This corresponds to the temperature of a tungsten filament from an infrared heater [THG06]. The amount of energy emitted by this body is according to Boltzmann’s Law 1,88·106 W/(m2?m). The amount of energy emitted in section 1 and 2 is 1,6·106 W/(m2?m). Thus according to Figure 3, 85 % of the energy penetrates into the preform, but in section 3 at least 10 % of the energy is absorbed in the first half of the preform.
The heating process is illustrated in Figure 5. The temperature on the preform surface increase most strongly, since a significant share of the radiation is absorbed near the surface. In a stretch blow moulding machine, this heat is dissipated through convective cooling during the heating process. This cooling procedure offers a large energy saving potential. According to Figure 4, in IR heating 85 % of the energy penetrates into the preform and are uniformly absorbed along the thickness. But, at least 10% of the radiation is absorbed in the second half of the preform near the surface.
A solid state laser operating with a wavelength of 1 ?m is more effective. In this case, 100 % of the energy penetrates into the preform with a transmission rate of over 80% and thus, less energy must dissipate through convective cooling. Microwave heating works in the same way. The result is a lower energy consumption and a faster heating process since the equalization time of the temperature profile is shortened.
STRETCH BLOW MOULDING MACHINES
The company Sidel, Octeville-sur-Mer, france, presented a stretch blow moulding concept with laser heating at the drinktec 2017. According to Sidel, the new laser oven technology builds on the solid state emitter that is able to emit a focused narrow spectrum. The laser diodes irradiate at low temperatures of 30-40°C without the need for oven ventilation. According to Sidel, these heating modules allow a very compact machine with a potentially reduced oven footprint of up to 60% for optimised line layout and the extensive process window increases packaging opportunities with more freedom in bottle shape design [URL18a].
A solution for microwave heating was presented by the Krones AG, Neutraubling, Germany, in 2011 with the FLEXWave technology, that earned the “Deutscher Verpackungspreis”. According to [URL18b], the microwave technologie offers 50% energy saving compared to common IR-heaters and a significantly reduced heating and cooling time. Furthermore, the technology is very versatile and therefore qualified for preforms with different proportions of recycled PET.
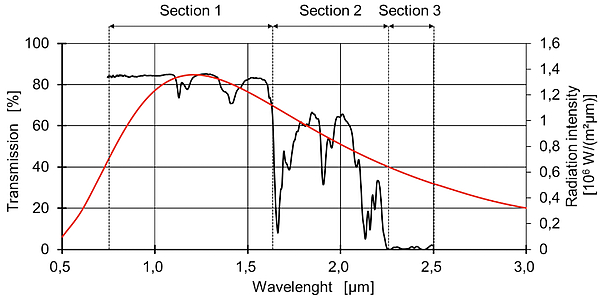
Fig 4: The transmission spectra in combination with the radiation intensity emitted from a black body at 2400 K
CONCLUSION
New approaches in the development of the heating stage like laser heating or microwave heating meet the challenge of producing increasingly complex hollow bodies while saving production costs at the same time. These technologies operate at narrowed or different wavelengths compared to common IR-heaters to achieve higher penetration depths to reduce the convective cooling of the preform surface heating stage. This leads to a lower energy consumption and a faster process since the equalization time of the temperature profile is shortened. In case of laser heating the beamed radiation of a laser offers the possibility to heat small areas of the preform, which allows a sharp temperature profiles and thus a more precise adjustment of the material distribution of the hollow body that improves the desired properties of the hollow bodies.
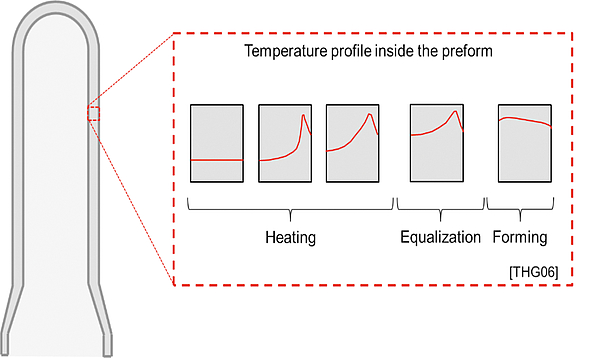
Fig 5: Temperature profile inside the preform [THG06]
The comPETence center provides your organisation with a dynamic, cost effective way to promote your products and services.
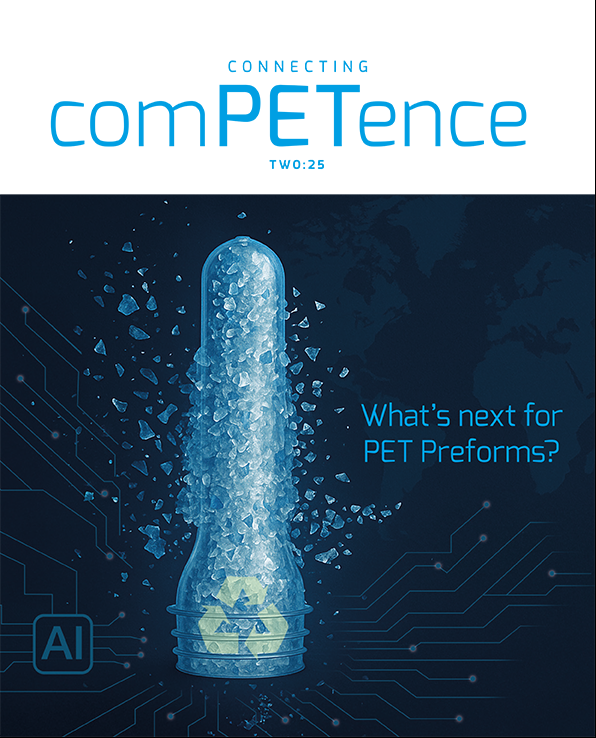
magazine
Find our premium articles, interviews, reports and more
in 3 issues in 2025.