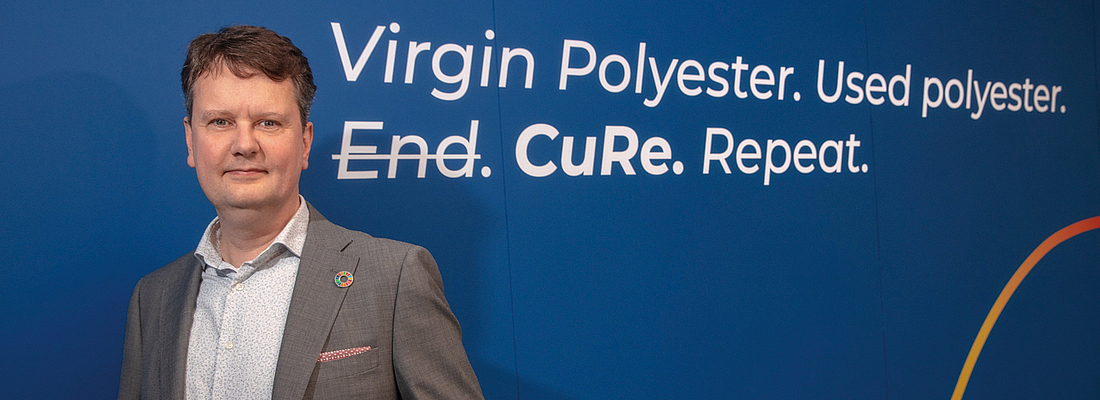
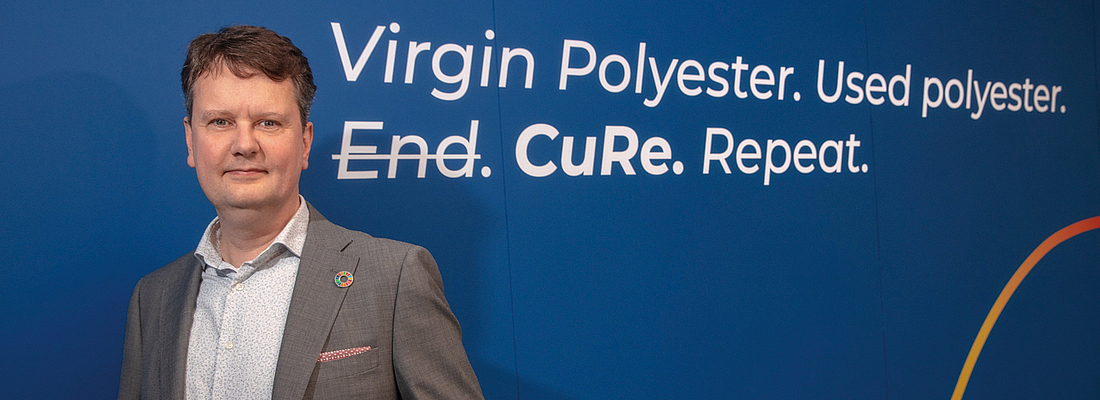
Josse Kunst, Chief Commercial Officer at CuRe Technology. (Source: CuRe Technology)
Polyester recycling
Polyester recycling is a hot topic - CuRe Technology
Interview by Dr. Otto Appel with Josse Kunst, Chief Commercial Officer at CuRe Technology - Polyester recycling is nothing exciting in and of itself. The chemistry is simply reversed: Depolymerization means the reversible reaction of the polyester production. This has been done since the 1960s. And then with CuRe Technology, a start-up in polyester recycling comes along. What does CuRe do differently, and how? We wanted to know that from Josse Kunst, Chief Commercial Officer at CuRe Technology
What is unique about the depolymerization approach of CuRe Technology?
JK: It’s actually relatively easy. The traditional methods of depolymerization are very energy-intensive. The end product of classic depolymerization processes is monomers. Our goal was: to break down polyester in an energyefficient way and as sustainably as possible. We asked ourselves: When is how much energy used and where? This is how it works: to break down polyester by 80 per cent you only need 20% of the energy. For the last 20%, you need 80% of the energy. So we stop with CuRe when 80% is degraded. And unlike traditional processes, we don’t sell intermediate products, but we process them further: we keep them at a high temperature, clean them at a high temperature and then use them to make polyester again. Our end products are not monomers, but rPET polymers that our customers use as raw materials. We produce them “fit for use” matching the requirements of the new applications the rPET will be used for.
You not only save process energy, but also combine steps that, in other processes, take place separately from one another and at different locations.
JK: Yes, these are the aspects that make our process more sustainable. Most of our competitors produce BHET, PTA, MEG or DMT. The monomers are sold, transported and processed into polyester again at another location. The disadvantages are obvious: you take all of the energy from the product, cool it down and have to transport it. That makes no sense for reasons of cost and environmental protection. In addition, in this process, you cannot control what happens in the next step. In the vast majority of cases, the recycled material is mixed with virgin material. So the final polyester is only partly made of waste, by far not 100%. This is not a real breakthrough in our view of a circular economy.
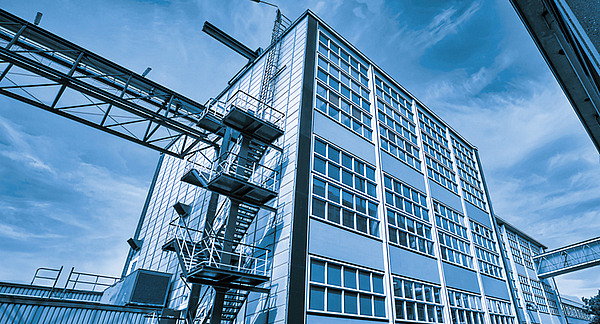
Is CuRe only suitable for certain types of polyester?
JK: No, and that’s what’s refreshing about our business model. We don’t just operate our new CuRe recycling. Because we are in a consortium with recycling innovators and experts we also offer mechanical recycling and waste treatment know-how. We see ourselves as a consortium that provides a one-stop-shop experience for people who want to close the polyester loop. We want to start with every type of used polyester and turn it into every kind of polyester quality.
Josse Kunst: ''We see ourselves as a consortium that provides a one-stop-shop experience for people who want to close the polyester loop.''
Do you have an example for us that illustrates the range?
JK: It is interesting when clothing brands contact us. They often find it complicated to organize a closed loop as you need to shred clothes, you need to know how to mill them, how to agglomerate them etc. They do not have objective data whether chemical or mechanical recycling is appropriate. Nor do they know that mechanical recycling would be possible if they changed the clothing design a little. We can help them with such questions.
Can the customer choose between different processes?
JK: Yes exactly. Many of our market competitors only cover one step in the process with their portfolio. We try to offer the optimal solution for every incoming feedstock. We want to provide a kind of rational decision tree - depending on the quality of the products and the most economical recycling method for these products. We don’t push our customers in any particular technological direction. If a customer needs food-grade material, we end up offering a recycled food contact grade polyester. And a recycled polyester made from carpets may be the feedstock especially for carpets’ manufacture. These are entirely different requirements. The factories will look different depending on the routes you choose.
Can polyesters from different sources be processed using the same technology?
JK: In our modular approach, we choose the purification method depending on the type of infeed and the quality we want to achieve in the end. That’s pretty unique. No, we don’t limit ourselves to just one purification method. We want to have six or seven different techniques. The ideal case is product recycling: beverage bottles should become beverage bottles again. The same applies to PET trays, carpets or clothing. That would be the most sustainable of all ways.
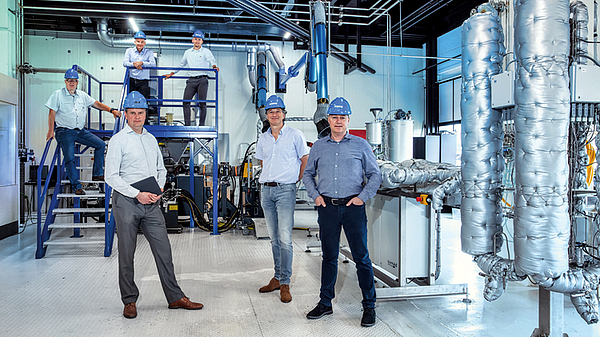
How do you get colours out of beverage bottles, for example?
JK: The hardest and most difficult part is actually getting out the contaminations, and colours are just one of the contaminants - there are barriers, oxygen scavengers, and all those other things. We are now screening every different kind of additives to find the best purification route to take. What we can share here is that we need an optimized recycling strategy for each of these contaminants.
Josse Kunst: ''The hardest and most difficult part is actually getting out the contaminations, and colours are just one of the contaminants - there are barriers, oxygen scavengers, and all those other things.''
How mature is the CuRe Technology?
JK: We are currently in the pilot phase, on a pilot scale. The pilot plant is like a mini factory with 500 t per year and can be in use 24/7. In Emmen in the North of the Netherlands, we also have an existing plant originally built to produce virgin polyester. It is a 25 kiloton plant. We have started engineering to convert it to the CuRe process, to reach 25 kilotons of CuRe rPET in 2023.
What are your further expansion plans?
JK: After we have completed the 25-kiloton factory in the Netherlands, we will roll out the concept on a large scale together with our shareholders and other parties.
Can your work also lead to a change of mood in society? Can it improve the acceptance of plastics?
JK: That would be important. Currently, polyester recycling is still too much lumped together with the chemical recycling of polyolefins. The benefits of the reversible polymers are not well understood by the general public. We hope that we can do our part - and we also hope for support, for example from you as PETnology.
The comPETence center provides your organisation with a dynamic, cost effective way to promote your products and services.
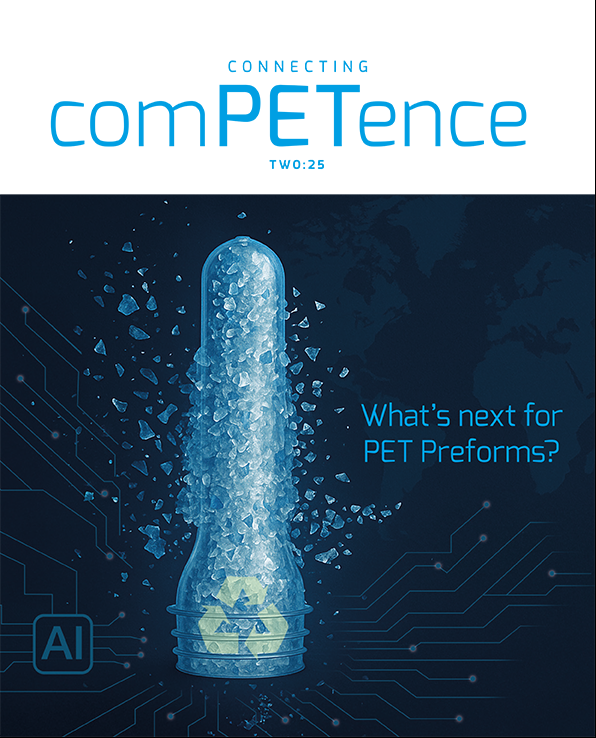
magazine
Find our premium articles, interviews, reports and more
in 3 issues in 2025.