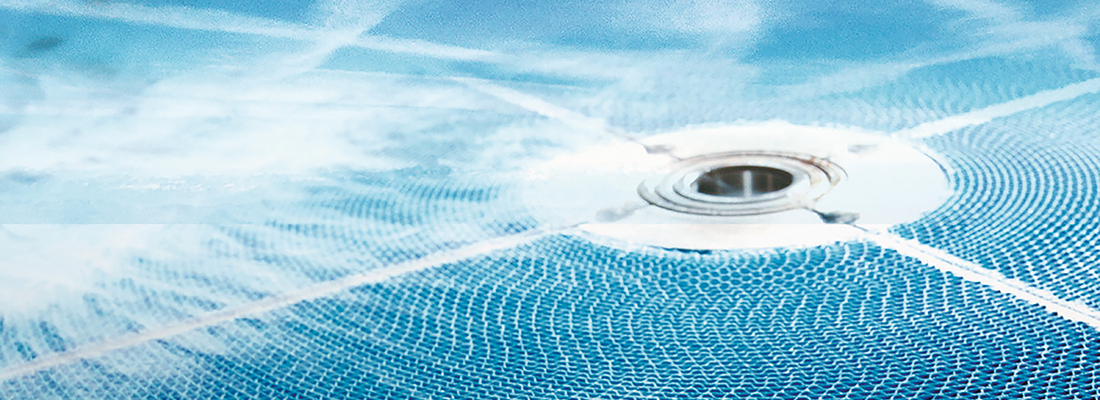
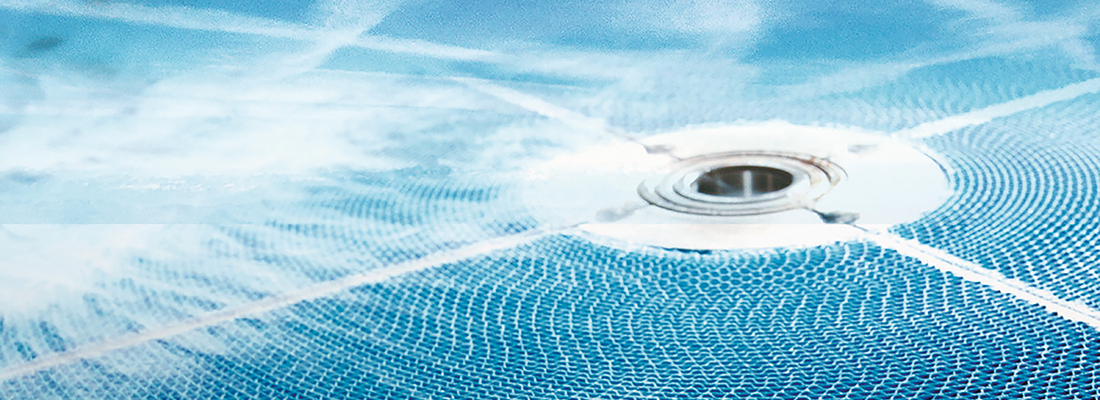
Innovative systems for drying plastics
PLUG & DRY - material drying all-in-one-solution
In the field of auxiliary equipment, Eisbär manufactures systems to improve quality and productivity for the plastics industry, specializing in products to avoid condensation on the moulds, drying of plastic resin and the process of PET flakes.
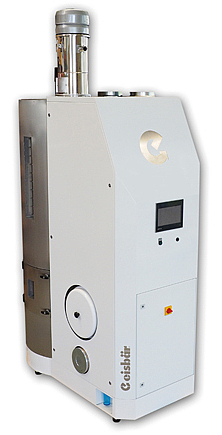
Continuous drying process for granule
Efficiency, reliability with an energy saving of up to 20 % compared to conventional driers: That is how renowned manufacturers of plastic parts around the world characterise the Granule Driers from Eisbär Trockentechnik GmbH.
Manufacturers are aware of the insufficient or incorrect drying. The results are the production of scrap and impair the quality of the product which leads to costly complaints. The production of high-quality products are the top priority objectives of the plastics processor. For these reasons, it demands a controlled drying process with high operational reliability. The continuous and energy-saving drying from Eisbär satisfies precisely these demands.
Eisbär Plug & Dry – new development for low throughputs
Space for installing material drying systems is expensive and often limited. Eisbär Plug & Dry is an all-in-one-solution for efficient material drying. Power connection and material supply line is all that is requested to start the process as this system is running without cooling water. The energy-efficient compact module Plug & Dry for drying PET granules and flakes consisting of material dryer, drying hopper and material conveyance is characterized by compact design and offers a multitude of advantages. Highest efficiency for low throughputs (25 to 200 kg/h) combined with lower space requirement compared to conventional drying systems.
The system offers no limits regarding ambient conditions using a closed circuit for continuous and rapid material drying. The adsorption drying technology offers user-optimized design and easy maintenance. The continuous drying process, lowest energy consumption and long life are basic advantages of the system to ensure optimal material drying.
Performance is in the air
The heart of the continuous material drying process is the slowly rotating adsorption wheel with its multitude of honeycombed, axially aligned tunnels. The inner walls of the tunnels are lined with a desiccant. As it flows through the lower half of the adsorption wheel, the process air is dehumidified by the dessiccant. During the next quarter-turn, hot regeneration air flows through the tunnel and in turn dehumidifies the desiccant In the next quarter-turn, the adsoprtion wheel is cooled to operating temperature and is then able to dehumidify process air again.
Simple user interface
To operate the system there is a touch panel with graphics capabilites (fig. 2). On a series of monitor pages, the operator can call up operating parameters in different languages, such as for instance processair dew point, filling level in the drying hopper, delivery capacities, valve status or process temperatures. On this monitor pages you can also adjust process set points and alarm settings. After selecting with the cursor, the monitor displays the type of error, the time at which it occurred and a fault signal number. The dryer can also communicate over Ethernet (Profibus or ISO on TCP/IP) to a MES (Manufacturing Execution System).
Service friendly and highly reliable
The two radial fans with direct drive and the low speed adsorption wheel are the only moving parts of the system. This also reduces the costs of servicing the plant. There are only filterts to be cleaned as required.
Advantages of the Plug & Dry system:
- All-in-one-system
- Screw on, plug in and start
- Power connection and material supply line is all you need!
- Compact design.
- Low space requirement.
- No refrigerating technology (environmental protection).
- No cooling water required (system without cooler).
- Closed circuit for process air - continuous and rapid drying process.
- No limits regarding ambient conditions and dew point.
- Clearly structured visualisation of all operational data for efficient control.
- Compatible for communication over Ethernet to a MES.
- Lowest energy consumption.
- Easy maintenance.
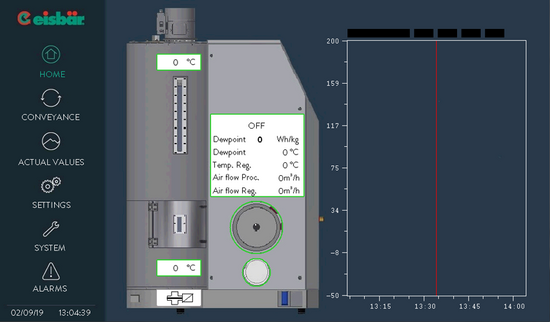
Fig 1: Touch panel
Experience and knowledge
The experience of Eisbär as an established manufacturer with extensive practical knowledge and focus in understanding the customer requirements is an outstanding strength. The customer therefore has a flexible partner with Eisbär for new, competitive and energy-efficient tailor-made system solutions. Another important Eisbär competence is digitalisation and clearly structured visualisation as well as data connectivity of all operational data for efficient control and maintenance.
The comPETence center provides your organisation with a dynamic, cost effective way to promote your products and services.
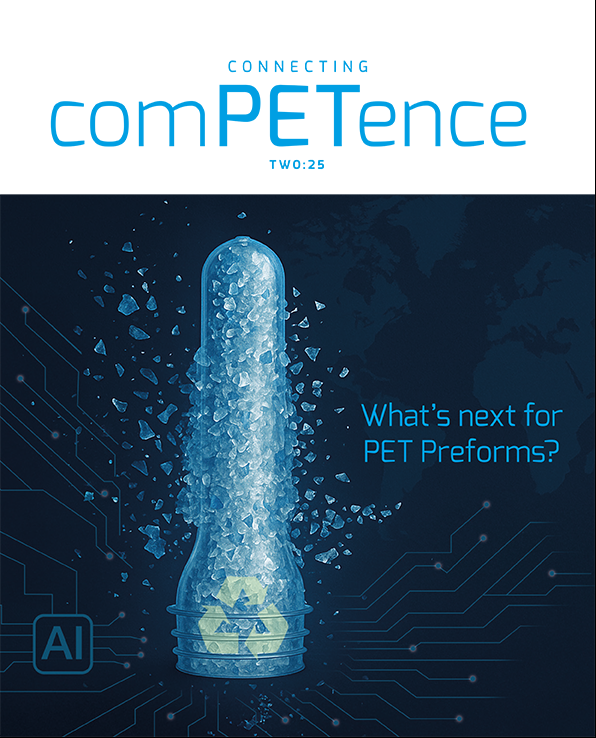
magazine
Find our premium articles, interviews, reports and more
in 3 issues in 2025.