With nearly 25 years of experience in PET stretch blow molding industry, PET Technologies has undergone significant transformations and expansions over the years. The company continues to evolve, innovative solutions for PET bottles manufacturing come to the market.
Brau Beviale 2023
PET Technologies to bring its latest developments to BrauBeviale 2023
PET Technologies will participate at Brau Beviale 2023 with the newest APF-Max 2 blowing machine on their booth.
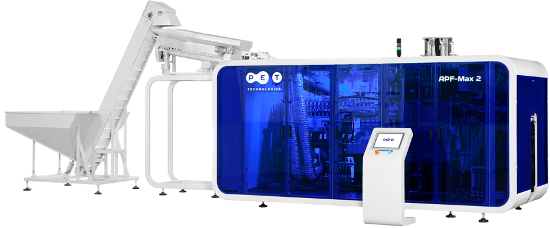
Machinery is king. The APF-Max 2 is a two-cavity machine from APF-Max series of blow moulding machine, designed to produce PET bottles ranging from 0.2 to 2.25 liters, with an output capability of up to 3,500 bottles per hour. It's the perfect solution for those either embarking on their manufacturing journey or transitioning from semi-automatic machines to higher productivity with a linear machine.
The APF-Max 2 blow molder distinguishes itself with a range of unique features that make it stand out among other similar machines. Notably, it offers quick changeover capabilities, facilitating the transition between preform types ranging from 18 to 38 mm with remarkable ease. To ensure precision and consistent quality during the molding process each mold cavity benefits from a set of valves. The machine's patented mold closing system and automatic temperature regulation further contribute to its efficiency and reliability making the APF-Max 2 a top choice for modern manufacturing needs.
Advanced heating system. One of the main features of APF-Max 2 is it’s NIR preform heating system. PET Technologies was among the first companies that adapted NIR heating to the linear PET stretch blow molding machines. The innovative series of blow molders APF-Max is among the first SBM machines of linear type where it was implemented!
The advantages of NIR heating system for PET bottles production:
- Uniform temperature distribution between the inner and outer parts of preform wall
- Reduced heating time
- Compact heater size
- Reduced energy consumption of blow molder.
The heating process is faster in comparison with the conventional infrared (IR) system. It reduces energy consumption and permits to design a smaller (shorter) heater of the APF-Max 2. The equipment has smaller footprint and is easier to transport.
The moulds shine bright. Situated across a sprawling 9000 m2 area, PET Technologies boasts a full production cycle on its plant, featuring over 140 metal working machines and two dedicated R&D departments.
PET Technologies tackle many spheres of PET bottle production, one of which is blow moulds manufacturing. Some of blow moulds produced by PET Technologies will be exhibited.
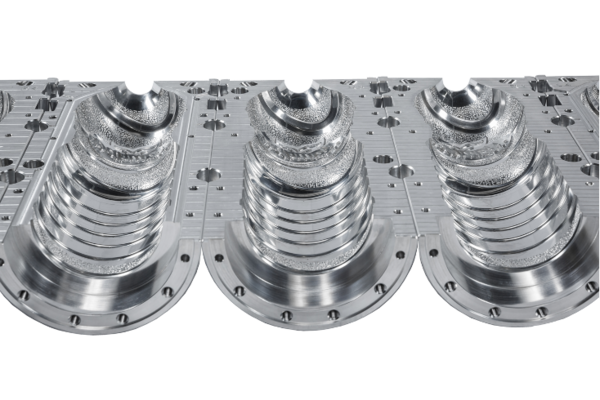
PET Technologies utilizes duralumin alloys of German origin. These alloys exhibit exceptional hardness, reaching up to 100HB. This particular type of aluminum possesses unique mechanical properties, offering an optimal balance between hardness and plasticity, making it ideal for withstanding shock loads.
The moulds production facility is equipped with advanced 4- and 5-axis CNC machining centers from renowned manufacturers like Deckel Maho (Germany), Doosan (South Korea), and Micron MILL (Switzerland):
- Achieving a remarkable level of automation (resulting in cost reductions);
- Ensuring exceptional precision and processing speed;
- Enabling the production of products of any complexity.
This infrastructure permits PET Technologies to produce molds for all European brands of rotary and linear blow moulding machines. It has converted us into an authorized partner of global brands!
Design is in the details. The booth visitors will get inspired with unique ideas for bottle design developed by PET Technologies. The bottles are not only attractive but also technological. We help our customers to combine lightweight with high resistance, sophisticated decoration elements with adequate blow molding properties.
Design is a technology. Time flies and technologies improve day by day, so you have to be sure your product is unique and outstanding on the shelf to be chosen by the end-user. The combination of designer solutions, modern engineering, and laboratory tests distinguish PET Technologies from other designer agencies significantly and allows to create high-tech and functional design.
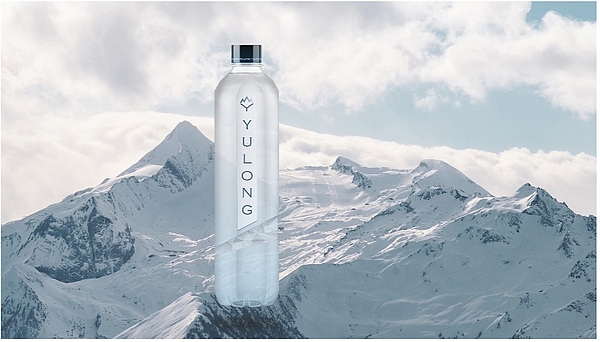
Simplicity or complexity, soft lines or sharp angles. PET Technologies designs it for your product and target market. Laboratory tests will save you a lot of time and money by improving the bottle design to the point where it not only looks fabulous, but also is strong enough to take
care about your product and resist transportation challenges.
Stages in the bottle design project implemented by PET Technologies:
- to carry out market research and to visualize the design by artist;
- to develop a technical drawing, keeping in mind the characteristics of the PET stretch blow moulding process;
- to make prototyping and produce samples of bottles;
- to carry out laboratory tests and check the physical properties of the bottle;
- to send samples to the customer for bottle trials on the filling line and test the market with target audience;
- to manufacture set of moulds for the blow moulding machine.
PET Technologies at Brau Beviale, November 28 to 30, 2023: Hall 7-646
https://pet-eu.com/
The comPETence center provides your organisation with a dynamic, cost effective way to promote your products and services.
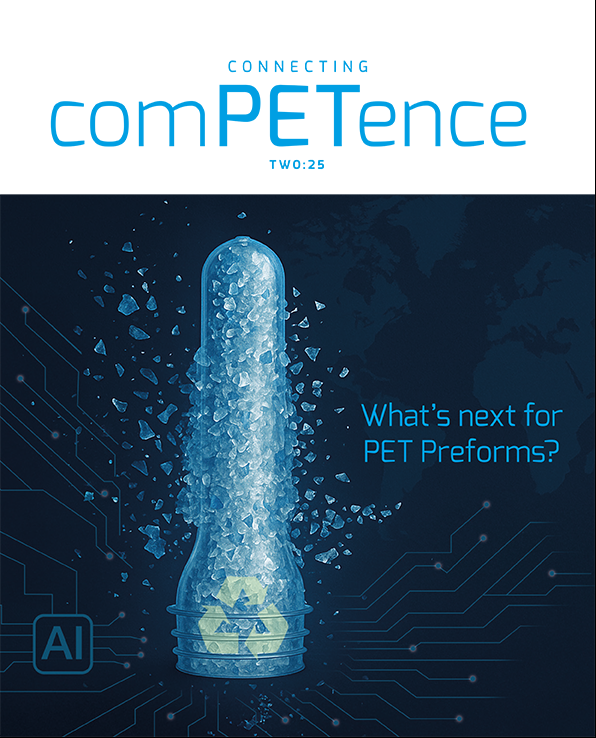
magazine
Find our premium articles, interviews, reports and more
in 3 issues in 2025.