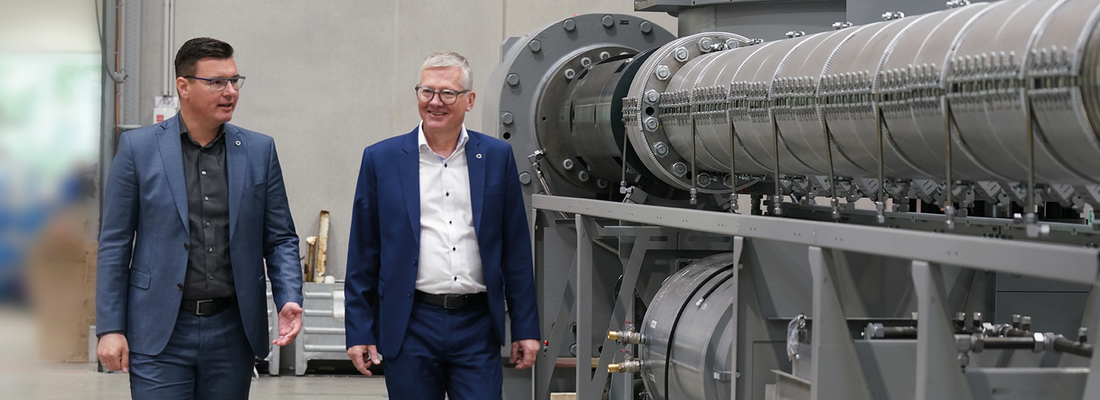
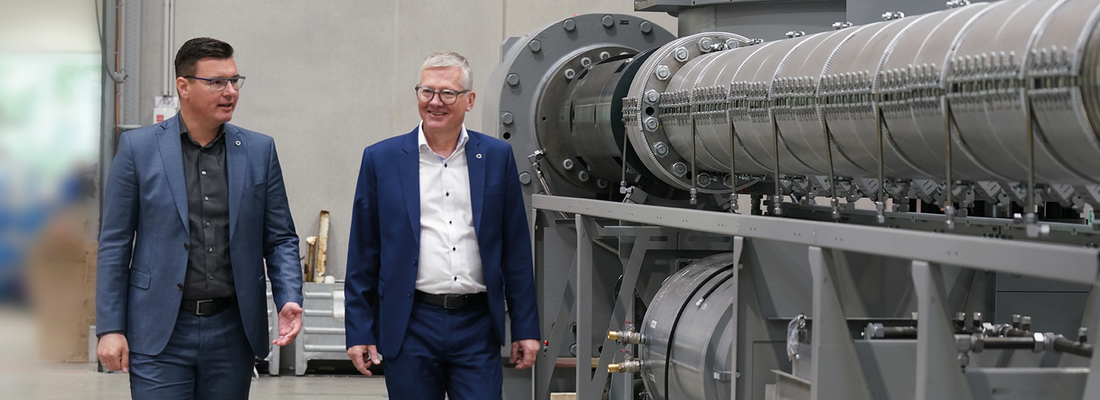
(Photo credit: PETnology)
PET RECYCLING
EREMA: PET Recycling - More than just Mechanical Engineering
Shortly before the big ceremony to mark 40 years of EREMA, which was celebrated with this year’s EREMA Discovery Day, I met Manfred Hackl, CEO, and Christoph Wöss, Business Development Manager Application Bottle, to talk to them about recycling PET. I have known both gentlemen for a long time. About 25 years ago, Manfred Hackl and I gave each other the microphone at PET technology conferences. Back then, PET recycling was always the last topic on the conference agenda. That has changed a lot, and recycling has long played first violin in the orchestra of PET technologies.
When approaching the EREMA site, the hustle and bustle at the loading area could not be overlooked. It was not about a customer system that still had to be delivered on time, but rather about plants and equipment that were relocated to the new EREMA factory in St. Marien. I found that out when I registered in the entrance hall.
With the new location in St. Marien, you have now, 40 years after the company was founded, simply doubled the assembly and testing area.
MH: Yes, we just doubled it - sounds much easier than it really is. And at the moment, everything is being commissioned and ramped up. That means that in the last few days, our people have already transported 9,000 pallets - that’s about half of the entire logistics - from the main factory to St. Marien. Thus, for the first time, we are setting up our own completely independent spare parts logistics, which will also serve to better satisfy our customers. A tight hourly cycle - on the way to something new. It’s going well - things are moving. Everything should be ready for the 40th anniversary and our Discovery Day at the beginning of June.
40 years is a long time. How were the beginnings? Did EREMA also start in the garage?
CW: I like the picture of the garage. I still see us a little bit “in the garage”. For me, that stands in a positive sense for our flexible, often unbureaucratic approach when trying out creative ideas - and certainly also for a company management of short, direct paths.
MH: Yes, that’s right. And in fact EREMA’s beginnings were in 1983 in a garage in Leonding, not far from here. I wasn’t there at the time, but I know from the owners’ stories that the first machine was launched in a garage next to the Rosenbauer and Stummer company. One of the first machines was operated by one of our suppliers - who is still one of our suppliers today. He had the necessary connected load to be able to run the system.
Energy was already an issue back then.
MH: Yes, the power supply in our garage was not sufficient.
And today you’re doubling the production area.
CW: With the new facilities, we realize our wish to exclusively enable tests with customer materials on production and test equipment in the Customer Center. And from now on we can carry out tests and developments set up by us in a separate R&D center. This will enable us to realize innovations for the market faster and more efficiently.
MH: We will be better able to meet two requirements: on the one hand, customer materials tests, also as sales support, and on the other hand, we have more room for - let’s call it basic research. In the future, we can better deal with the challenges of the market, for example by testing a wide variety of materials and different systems, from textiles to fibers to trays. We are now bringing back the pilot plants and the various extrusion lines from the outsourced halls - close to the development department.
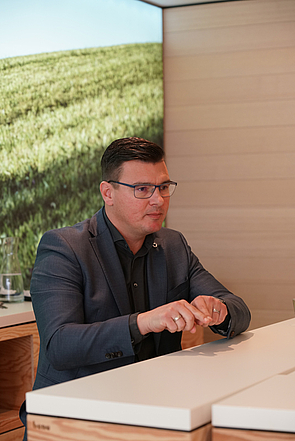
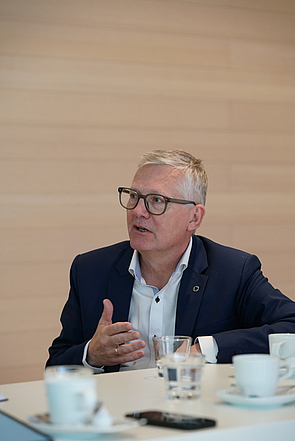
If you look back on a company development like yours, then you are naturally inclined to say that those were great times. But as always, if you don’t have any downs, you don’t have any ups either. What were the highlights, the challenges - economically or technologically - and were there any low points?
MH: We personally also have a long history with EREMA. Christoph Wöss has been with EREMA for 22 years, so he has been with us for more than half of our company’s history. I have been with the company for 28 years. For me, and I think Christoph agrees: it’s been a great, continuous learning experience. Things don’t always go uphill in a development phase. We engineers suffer technical setbacks, and this also happened to our team. We have learned and built up know-how from each single failure. In this respect, the direction has always been the same: the ups and downs have brought us, and therefore our customers, extremely far forward - technologically and entrepreneurially.
Which example can you think of spontaneously?
MH: One from the early days of PET. Around 2002 we built the first PET line for sheets in cooperation with the Kuhne company. But it didn’t sell. At the time, bottle-to-bottle recycling started making headlines, but the thermoformers could not imagine feeding recyclates inline via the melt to the end product. It was too early for our technology. We carried out a relaunch five or six years later, and the time and the market were open for this product.
Our industry is driven by sustainability and cost pressure. A system has its chance when it precisely meets these requirements.
MH: We can report something similar from the history of our VACUREMA technology. We were pioneers in bottleto-bottle recycling. Around 2000/2001 we sold three systems in Europe in one fell swoop. These were all 500-600 kilogram plants. In the beginning, of course, we needed more commissioning time to find the ideal settings for our customers. The lessons learned from this, in turn, led to the improvement of our systems, and we were rewarded with increased demand. Another incentive was the competitive situation in recent years, when many new technologies pushed their way onto the market. Our response was the VACUNITE technology in 2018 - which enabled us to defend our position as the market leader. And today, we have reached the point where we offer a wide variety of technologies: Flake treatment, inline end products, VACUREMA Prime and Basic, VACUNITE, LSP technology, fiber technologies. I would say: We play the entire keyboard.
CW: Depending on the input material and end application, we have a wide variety of options today. We can not only offer the right technology for the specific application, but also create a reasonable basis with figures, data and facts to make the right decision with the customer.
MH: One of our customers, who runs different technologies from us, recently said the following: I can transform different materials into various applications, I have enormous flexibility and can therefore offer the best for the applications of my customers’ use cases. Last but not least, the market has also spurred us on to this range, namely to expand our product range with other technologies.
_______________
''We play the entire keyboard.'' - Manfred Hackl
_______________
How do you experience the further development of your customers?
MH: Overall, customers are focusing on either bottle-to-bottle or tray-totray. Mixtures of both are rare. Some customers are open to recycling other polymers. And EFSA also wants to open up multiple cycles. Look at caps. The new Regulation (EU) No 2022/1616 gives us the opportunity to start developing technologies for circularity. We are looking at this with our customers.
CW: Secondary material flows will be the focus in the coming years: LDPE, HDPE or PP. We already have ideas on technologies to keep these materials in the loop. What we have developed for PET over the last 20 years, we now have to implement much more quickly for polyolefins. Behind this are many tasks on both sides, the providers and the approval authorities. But we must be quick now; we don’t have the time like with PET. Many challenge tests have to be carried out, Design for Recycling is still in its infancy. And EFSA wants to know everything about the contamination and decontamination of the material.
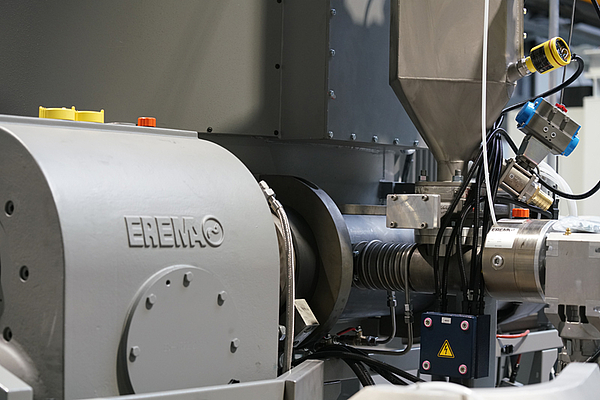
Is it possible that approval may take more time than development?
CW: It’s easier and faster, and, in my view, no less secure, with the FDA. The FDA responds faster to an application and the approval process is more stringent and effective. A major difference, and one that is crucial for me, is the nature of the approvals: With the FDA, they have always been technology-based. That means that we as a provider apply for and receive approval for XY technology, which we hand over to the customer, who can then work with it directly. EFSA used to issue approvals to the operator. In detail, this means that each operator had to obtain approval for the XY technology individually. In figures: We serve about 150 operators in Europe - which means 150 approvals for the same XY technology, again and again. Such a procedure with usually many queries can take several years. If, during this time, there is a change of personnel on the part of the authority, the procedure may be delayed even further.
Can a customer with a purchased and installed system get into trouble because of this?
CW: That was the crux of the matter. In an extreme case, a recycler produced a food-grade material and could not sell it because it was not licensed. Brand owners were strict: no business without a certificate. In between, it was said that national law applies as long as the EU approval is unavailable. But national authorities, of course, didn’t want to take any risks: “We comply with EFSA.” It took enormous efforts to obtain individual approvals limited to one year. Last year in October, EFSA presented their revision: Now, as a technology provider, we are allowed to license our customers.
MH: That also goes back to Christoph’s personal commitment over several years. But no sooner has this step been simplified than the next complication arises. But before I let Christoph explain, let me say one thing: As always, there are two sides to the coin: Dealing with approvals costs us human resources and time. Today, we employ a team of three with food contact requirements - which Christoph used to do on the side. In return, we are now very experienced and can quickly get our customers to the point where they can produce and sell. And last but not least, these are all learnings that make us fit for future challenges.
CW: What Manfred Hackl is just hinting at is an aspect whose importance we must not underestimate. With the required detailed description and proof that our processes work properly, we find ourselves in patent law territory. Since everything is published online, as a technology provider, you have to meticulously label what is “strictly confidential.” So we and our competitors must be cautious about what and how we communicate. And, this is new: Unlike the FDA, EFSA has national authorities conduct audits of plant operators. Before the actual audits, a so-called “compliance monitoring summary sheet” has to be filled out. In other words, we must prepare a paper showing how our plant works, which parameters play a role etc. We had a first audit of this kind at a German customer with the national authorities, including eight employees from TÜV. You can imagine: It’s not just experts in mechanical engineering to whom we have to explain the plant and the food suitability of the product. That’s how it works in all EU countries - with many different and unequal teams.
_______________
''When I first saw the screw, I thought something was wrong. “Everything as planned,” so the feedback from the CNC machining department.'' - Manfred Hackl
_______________
There is no question that food contact requires special attention.
CW: Despite all the effort, I also see an advantage: We prepare facts in such a way that non-specialists can get a clear picture and obtain a basis for decisionmaking. This approach promotes an understanding of plastics recycling in general - and maybe even helps us with regard to end users and the reputation of our plastic packaging.
MH: And if you think back, 20 years ago, no one would have imagined that rPET would become such a standard and be supported by everyone.
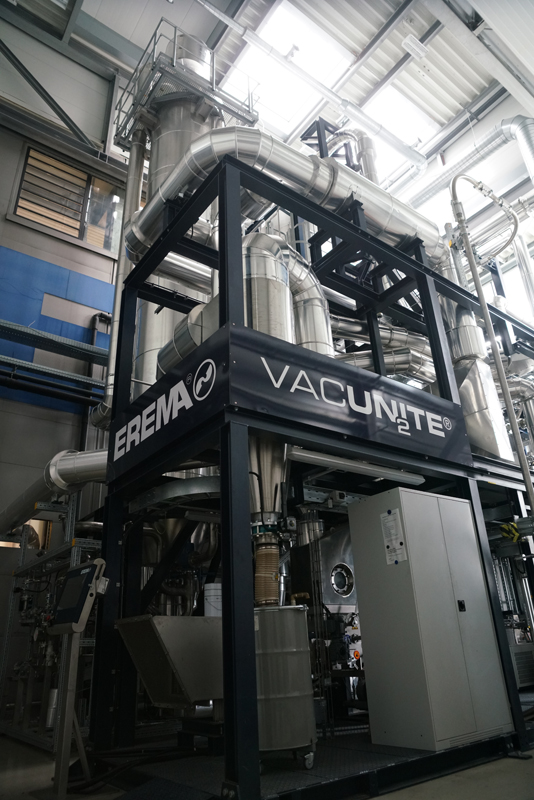
When you say “support”, do you mean that the gray color of PET bottles, which indicates rPET, is even preferred today? High transparency used to be the measure of all things.
MH: Gray is definitely more accepted today. But: We would prefer gray to be perceived as a quality and distinguishing feature for the material quality. The more transparent, the higher the quality.
Which of your technology achieves the best transparency?
MH: It spurs us on as a technology provider to develop new technologies that preserve color or transparency in the best possible way, even in many cycles with a high proportion of recycling material. Our customers report that they achieve by far the best color result on the VACUNITE.
CW: Some customers blend rPET with additives. When discussing this in different forums, I call it a “friendly disagreement.” Let’s look at additives that compensate for the inherent color change. Here’s the problem: Each additive has a negative impact - to whatever degree - on recycling in the loop. Gray haze occurs when these percentages are pushed up - such as in Germany with the addition of the AA scavengers - and we see problems with IV increase. Our principle in developing our equipment is that you don’t need to add any additives and that the physical and optical properties of the rPET material only come from the purely mechanical recycling process. In my view, anything else is strategically wrong regarding process engineering for recycling.
MH: The right and sustainable way is to do without additives. We have to strengthen this approach, otherwise we will limit ourselves at some point, and new problems could arise that we cannot yet assess or know about. But the additive manufacturers are also working on the issue, and compared with 20 years ago, we are on the right track. But all those involved in this cycle have their own interests, of course.
What is the biggest change over the past 40 years?
MH: The original machine builder EREMA was an engineering forge. Today, we combine engineering knowhow and polymer expertise. We have many young employees specialized in engineering chemistry. We have established a food contact team for PET, and our laboratories provide detailed analysis. Our after-sales team accounts for about 10% of the workforce, and we have a decoupled supply chain between production and after-sales. EREMA is now a group of companies combining technology development, manufacturing, plant engineering and service provision. With KEYCYCLE, for example, we can offer Feasibility and Greenfield Studies as well as turnkey solutions that cover the entire recycling process including sorting, washing and extrusion. But there is also an increasing demand for de-inking solutions in the tray-to-tray sector. So you see, our drive to find the best technical solution to any plastics recycling challenge is just as strong as it was 40 years ago. Therefore, it is a matter of course for us to network and push for common solutions at both European and international levels. Christoph Wöss, for example, is a board member at Petcore, so he can transport our input and help shape the future in Brussels.
CW: When we talk about what has changed, it also relates to upscaling. We have realized a doubling of throughput about every 5 to 10 years. About three years ago, we were supposed to achieve 4 -5 t/h throughput. We quickly realized that it was not sufficient to extrapolate existing technologies one-to-one. We were lucky to be able to build on a development that we had initiated earlier. Starting from this platform and with additional engineering solutions, we created the EcoGentle technology. Feed and screw geometry were adapted, resulting in an entirely different melting process that allows even large throughputs to be gently melted with one screw. We benefit from the fact that we preheat very homogeneously in our reactor, can thus feed the singlescrew extruder hot and achieve these throughputs with the geometric design of the screw.
MH: It was always said: That’s not possible. Low melt temperature at high throughput has always been synonymous with deep-cut screws - with the problem that the melting performance could only be achieved through high friction with the inherent risk of overheating and degradation. Today we have it: the EcoGentle with 6t/h at a melt temperature of 285°C. More figures: We have reduced energy consumption by 12%, the average temperature by 10°C, and the AA content even by 50%.
Can your customers retrofit EcoGentle?
CW: The machines for high outputs have the EcoGentle technology as standard. And yes: retrofitting is possible; the customer needs the new screw and the redesigned material infeed. In economic terms, this only makes sense for large machines.
CC: How do you achieve the big savings?
MH: The secret here also lies in the screw design. When I first saw the screw, I thought something was wrong. “Everything as planned,” so the feedback from the CNC machining department. The screw is simply ingeniously “different”. It is an impressive combination of different expertise, simulations, new approaches, and working methods that have led to this success. The positive result lies in the completely different melting behavior.
CC: That reminds me of the development of the blowing capacity of stretch blow molders. It was once said that the limit was 2,000 bottles per hour and station. Now it’s almost at 3,000 bottles per hour. The question to EREMA: When will the 10,000 rPET line be available?
CW: We have indeed discussed this many times. The extruder, as the new development shows, is not the limiting factor. The challenges lie in the reactor size, also for logistical reasons. In addition, it would need new gearboxes and water-cooled motors. We are working today with motors of ~600 kW max and normal voltage. Larger plants would need 900 kW to 1 MW. That’s where the power supply at the customer’s facilities comes into play. All in all, that’s quite complex.
MH: The material flow would also have to be secured and the washing plants, which today have an output of 4 -6 t/h, would have to be adapted.
CW: Let’s not forget the impact on the markets themselves. Our first customer for the EcoGentle plant in Mexico runs a total of about 8 t/h. This very high demand impacts the entire Latin American continent: the customer has almost “emptied” the market to utilize its washing and recycling plant to capacity. This dynamic also affects pricing.
What is EREMA’s position on chemical recycling?
MH: Our strategy is definitely not to enter into classic chemical processes. But: Many chemical processes require melt preparation beforehand. With our CHEMAREMA series, we combine our mechanical recycling know-how with the chemical recycling requirements. We optimally prepare the material for the chemical recycler - whether polyolefins or PET - that’s it.
CW: Polyolefins can be recycled by pyrolysis, PET by depolymerization. From a mechanical engineering point of view, we are absolutely in our profession with these technologies. We are already working with the most renowned developers and companies from the chemical recycling sector. The EcoGentle technology again benefits us in this field, as the chemical recycling processes require high throughputs.
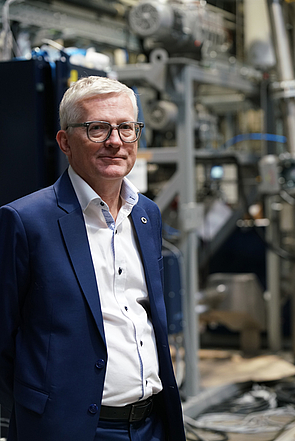
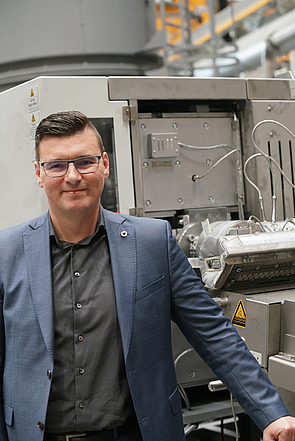
Do you think chemical recycling of polyesters is more suitable for textiles and fibers than for trays and bottles?
CW: The industry is ambivalent about this. In principle, chemical recycling is seen as an addition, especially for opaque or extremely colored, non-transparent PET materials or multilayers that cannot be processed using mechanical recycling processes. Mechanical recycling already reaches its limits for trays with different layers, especially if the requirement is to keep the material in a circle. Chemical depolymerization processes are of interest here. The economic viability and upscaling to large throughputs still have to be proven.
_______________
''We prepare facts in such a way that non-specialists can get a clear picture and obtain a basis for decisionmaking.'' - Christoph Wöss
_______________
What future do you see for chemical, biological or enzymatic recycling?
MH: For PET, I find it hard to imagine the success story of bottle-to-bottle recycling being repeated in chemical recycling or even replacing mechanical recycling processes. Circular PET is the pioneer of the plastics industry and is now a well-functioning business model. We see the new techniques more where mechanical recycling reaches its limits. With polyolefins we are not as far along as we are with PET, although a lot has been caught up in the last three to four years, and today many applications exist and work well in the recycling sector that were inconceivable a few years ago. From our point of view, there will be both in the future, but it is important that mechanical recycling has priority since it has significantly less CO2 footprint, for example.
CW: I am concerned with the issue of mass balance in chemical recycling. When the monomers produced by chemical recycling are further processed, it is no longer possible to determine to what extent the (PET) polymer produced consists of petroleum-based or chemically recycled components. It can even happen that a product label shows 100% recycled material from chemical recycling. From a purely accounting perspective, that would be possible. From a technical point of view, the product can still consist of 100% virgin material. Roughly comparable to electricity: You cannot say where it came from at time X - from the hydroelectric power plant next door or a gas-fired power plant anywhere. This consideration harbors the danger of greenwashing. We’re hotly discussing that, even at Petcore.
MH: Our industry has to deal very sensitively with procedures that could be interpreted as greenwashing - if only to avoid jeopardizing any successes that have been achieved. Especially with regard to consumers. Let’s imagine a virgin material plant that would replace 1% of the crude oil used with “oil” from pyrolysis: This plant would de facto produce material with 1% recycled content. Sounds neither “green” nor sustainable, but it would be honest.
CW: I also think the wording in America is problematic: chemical recycling is called “advanced recycling” there. This suggests that chemical recycling is more effective and all recycling technologies developed before chemical recycling are obsolete. End users would consider products made from material derived from chemical recycling to be of higher value than those from mechanical recycling. However, the true proportion of recycling can only be quantified for material derived from mechanical recycling. Something like this can become a boomerang for the PET industry via the end customer.
Material production and recycling are moving ever closer together. Is the material manufacturer becoming a recycler?
MH: We already have real projects and inquiries. It could go in the direction of so-called hybrid solutions. In other words: 10 to 30% post-consumer flakes could flow into the virgin material stream. In addition, there are of course also material manufacturers who specifically acquire recyclers and thus increasingly cover this segment.
CW: 33 Mt of virgin material for packaging is produced per year, which goes hand in hand with extreme overcapacity. According to my information, there is currently 9 Mt of overcapacity. 50% of this overcapacity comes from China. That’s why we are being flooded with cheap virgin material right now.
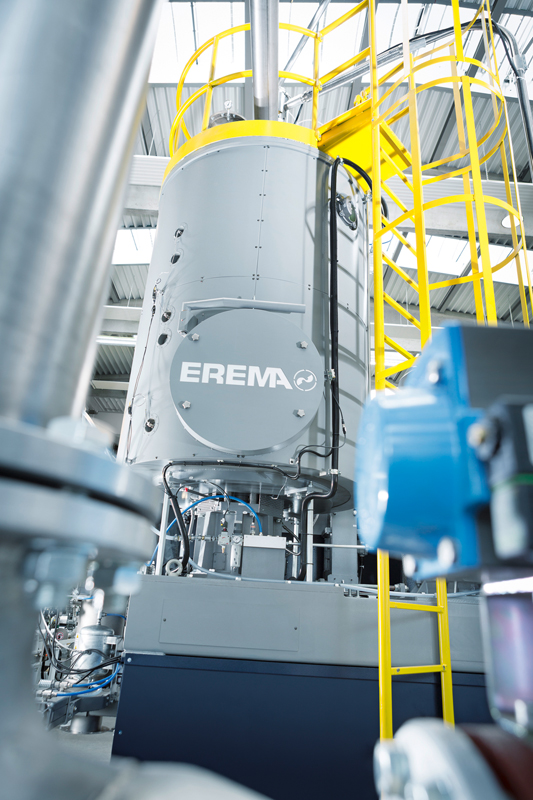
What is the total throughput for rPET across all plants in mechanical recycling?
CW: EREMA customers currently have a production capacity of around 4 Mt per year on around 390 systems sold. This gives us a strong position in the various markets with market shares of between 40 and 70%. Globally we are around 51%. We clearly see ourselves as the market leader here.
Do you see competition emerging in China for recycling plants, which could open up a potential market not only in China but also in Europe or worldwide, similar to electromobility?
MH: I don't see that at the moment. After a four-year break, I could get an impression of the market at this year's Chinaplast. At the moment, the supply in our segment is relatively modest. In Chinese plant engineering, recycling is not yet a top priority. You can't compare that with injection molding or e-mobility. However, Chinese plastics engineering, in general, has made a big leap forward, especially in injection molding. Fortunately, the recycling extruder's position is at the end of the plastics process chain, so there is a great deal of variety in terms of what such a system must be able to process. But one thing is clear: We have to keep a close eye on this market situation. As already mentioned, plastics recycling is no longer purely mechanical engineering. We have essential added value in our portfolio for our customers. We are aware of this, and we have to communicate it.
CW: The China FSA is currently working on approving rPET for direct food contact. So far, this is not allowed. China is now collecting information worldwide on how this works - to finally adapt the processes for their country. It is expected that the China FSA will approve rPET for food contact in 2024/25. You always have to keep in mind that in China, 70- 80% of virgin PET is manufactured using European technology. And there are already projects where only the core technology is purchased. That means: Once food contact rPET is approved, a lot will happen quickly. We must monitor these developments very closely.
Do you also claim technological market leadership?
MH: Absolutely, for a number of reasons. We talked about our wide range of technologies. There is the SSP technology on the flake with the VACUREMA product range and on the pellet with the VACUNITE, both patented and modern technologies with numerous advantages. We also have an edge thanks to our filter expertise, product range, and Blueport digitalization platform. Overall, I base our technological lead on three points: safety and quality of the customer product, energy consumption and - last but not least - the color. Nevertheless, we must continue our work intensively and ensure that we are not overtaken in the global competitive environment.
The challenges will remain for you and for us, and there will be no boredom at EREMA. Congratulations on the company anniversary and thank you for the interesting conversation.
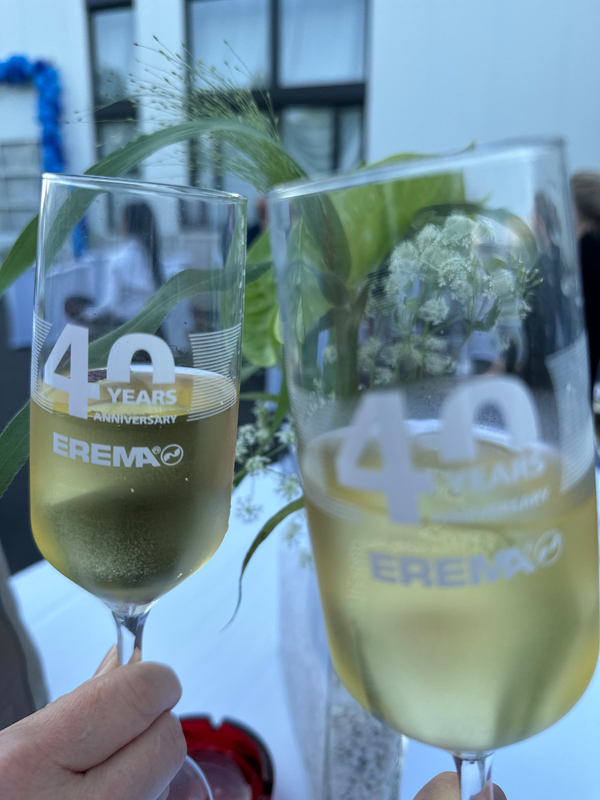
The comPETence center provides your organisation with a dynamic, cost effective way to promote your products and services.
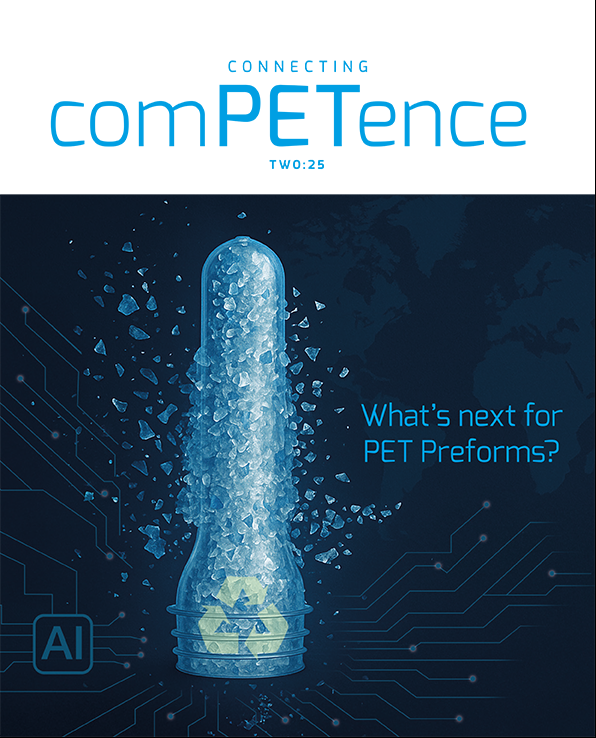
magazine
Find our premium articles, interviews, reports and more
in 3 issues in 2025.