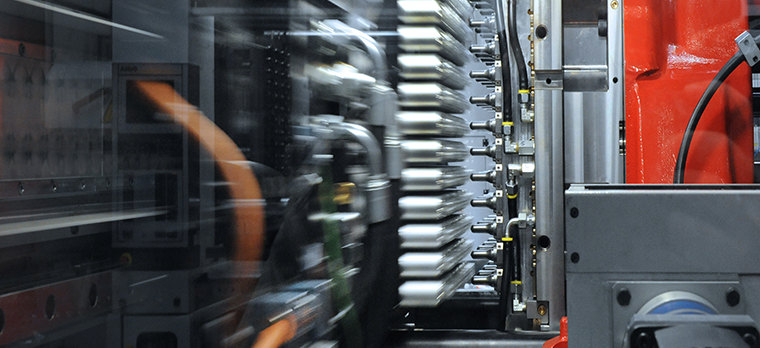
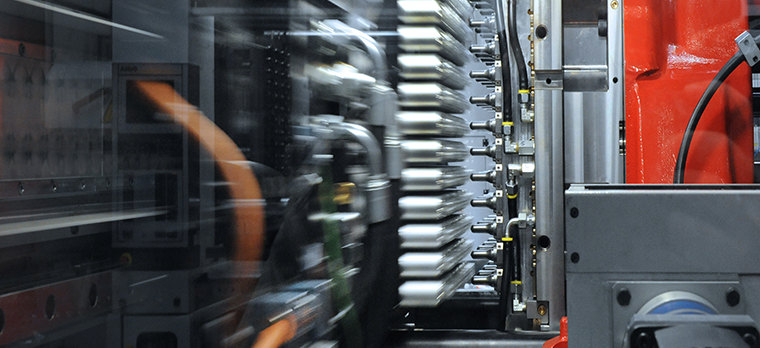
A new IPS 220 - part of a fully automated production centre, web-connected to maximise performance and efficiency – has been successfully installed and started up. The result: the highest-performing and lightest milk bottle preform on the Italian market and, with “SACMI Total Care”, an Industry 4.0-oriented approach to production and service.
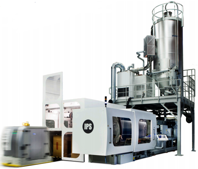
A new IPS 220 - part of a fully automated production centre, web-connected to maximise performance and efficiency – has been successfully installed and started up. The result: the highest-performing and lightest milk bottle preform on the Italian market and, with “SACMI Total Care”, an Industry 4.0-oriented approach to production and service.
Sacmi-developed innovation has won over Parmalat (Lactalis Group), which has now chosen the IPS (injection preform system) platform to renew its Piana di Monteverna (Caserta) plant. Here, as of today, PET preforms are being manufactured for the milk sector, providing the lightest. highest-performing 1-litre bottles on the Italian market.
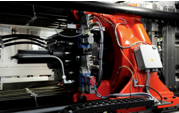
Developed with the clear aim of offering customers a complete, integrated platform that stands out from alternative solutions on account of its user-friendliness and fast, easy size changeover, the IPS 220 features some great design innovations on the mould clamping unit which - thanks to intense design work involving FEM techniques to optimise mechanical inertia - ensures ultra-fast lock-to-lock times, thus shortening preform production cycles.
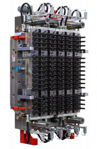
A key feature on the solution installed by Parmalat is the all-Sacmi mould. This complete 48-cavity injection mould (hot half and cold half) stems from painstaking in-company design of each component and is characterized by optimized channels inside the hot chamber, plus high-efficiency cooling circuits; the latter facilitate heat exchange to provide ultra-high performance production cycles, as already demonstrated during the simulation and testing carried out jointly by the Sacmi Research Center and the Parmalat R&D facility.
The plant supplied to Parmalat is no mere machine. One of the key factors in the Group's investment choice was "SACMI Total Care", the SACMI system that, thanks to advanced system-integrated web-connected sensors, allows remote, predictive performance and process monitoring, anticipating problems and providing appropriate solutions (e.g. sending spare parts and troubleshooting the most common issues on the line) without having to send a specialised technician on-site. Fully integrated and connected - from press to dryer, refrigeration systems to compressor - the system can be monitored both remotely and from any device connected to the corporate network, anticipating every possible need (spare parts provisioning, maintenance tasks) and minimizing production downtimes.
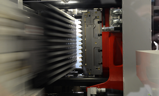
The result, an intelligent production model that looks to "Industry 4.0", the strategy that – via the use of advanced sensor systems and IT technologies – provides an innovative approach to product and service, ensuring the cream of Italian industry has a decidedly bright future.
Photos: SACMI
The comPETence center provides your organisation with a dynamic, cost effective way to promote your products and services.
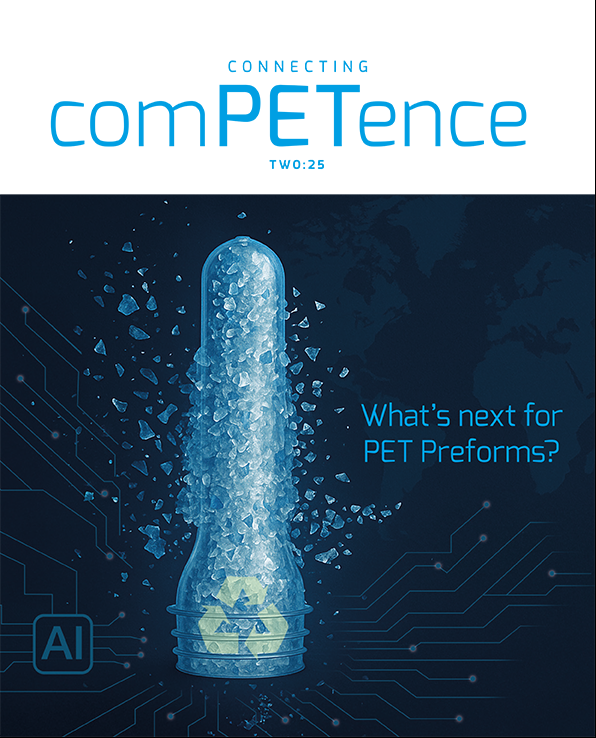
magazine
Find our premium articles, interviews, reports and more
in 3 issues in 2025.