

(Photo credit: Otto Systems)
LARGE PREFORMS
New HOD-Series by Otto Systems - Setting new standards in preform production for large volume containers
Economic Production for a Growing Market
The introduction of the HOD-Series by Otto Systems is a response to a critical market need for efficient and economical production of large volume containers. Existing solutions have often fallen short in meeting the specific requirements for such applications, leading to inefficiencies and higher production costs. Otto Systems, based in Uznach, Switzerland, has addressed this gap with a system that stands out due to its compact design and high productivity.
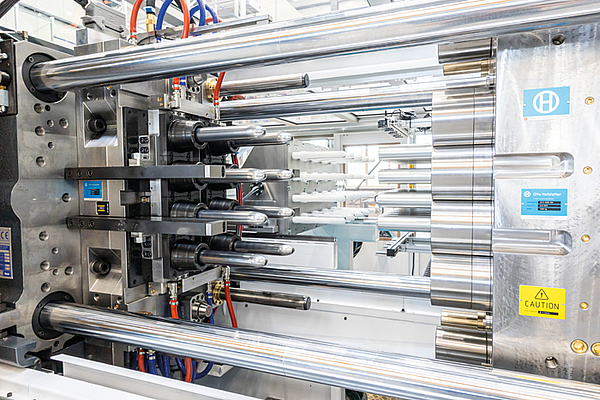
Innovative Design Features
The HOD-Series is characterized by several key design features that set it apart from traditional solutions:
- “EXTended” Clamping Unit with Electrically Driven Toggle Mechanism: Otto Systems employs a unique outward-bending toggle mechanism. This principle not only enables highly dynamic movements with minimal energy consumption, but also allows, by extending the toggles, the columns, and the machine bed, an opening stroke of almost one metre on a 160-ton platform, which is not possible with conventional inward-directed toggles due to space limitations. This gives the HOD-Series clamping unit a unique compactness, tailored to the required clamping force and the “EXTended” stroke for large container preforms.
- Smart Configuration of Mould and EOAT PostCooling: The row spacing of the insert groups in the mould creates space for the post-cooling stations in the EOAT take-out plate - the more cooling stations, the wider, more complex, and expensive the mould becomes. With the large insert groups for HOD-preforms, the mould width with row spacings for 3 or 4 post-cooling stations in the EOAT would far exceed the horizontal column spacing of the 160t clamping unit. Therefore, Otto Systems engineers, in collaboration with colleagues from Otto Hofstetter mould manufacturing, have designed 2-row, super-compact HOD-Series moulds that fit optimally in width into the EXTended clamping unit of the HOD-Series.
- Fully Integrated Robot with New 2+2 Station Post-Cooling: The limitation, given by the mould, to 2 cooling stations can be enhanced to 4 postcooling cycles through the cleverly chosen layout of the take-out plate. In this case, the EAOT is duplicated in width and equipped with a total of 8 rows of water-cooled sleeves, allowing 2+2 postcooling stations. This principle, combined with the proven Pick-Blow-Combi (internal preform air-cooling in all post-cooling stations), offers the most efficient cooling for optimal preform shaping and enables the fastest cycle times even for heavy and thick-walled applications.
- High-Performance Plasticising: The HOD injection unit is characterised by an optimal balance of plasticising and injection performance. The key developments here are the plasticising screw, which homogeneously plasticises exceptionally large shot weights, and the so-called Time Safe Unit (TSU). The TSU holding pressure module handles the distinctive and long holding pressure for large preforms. This allows the screw to ensure large dosing strokes at moderate rotational speeds with ideal residence time. This system configuration is extraordinarily compact and guarantees optimal process conditions.
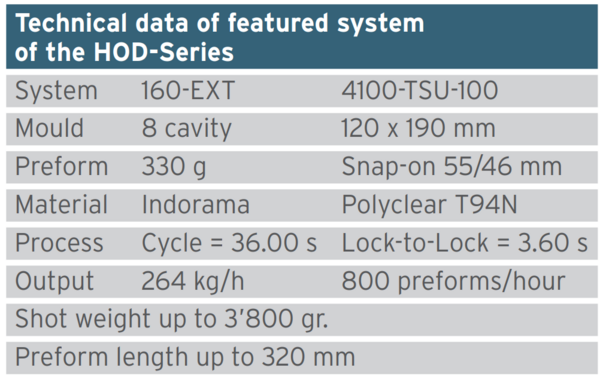
Strategic Focus on Special Applications
With the HOD-Series, Otto Systems has clearly demonstrated its commitment to developing customized solutions that meet specific customer needs economically. The system fills a significant gap in the market, catering to special applications with the highest technological standards. Every detail of the HOD-Series configuration reflects a deep understanding of the demands of these applications, ensuring optimal performance and efficiency.
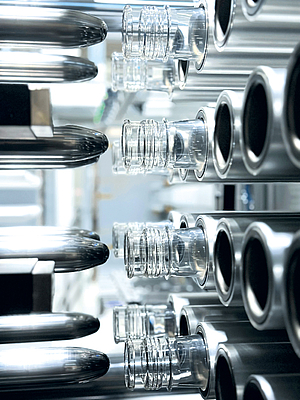
Expanding Product Portfolio
Otto Systems’ current portfolio includes the PET-Series and the HOD-Series. The PET-Series, designed for high-speed applications, is a flexible and modular system based on 160-, 240- and 320- ton platforms. It boasts the fastest cycle times and lock-to-lock times of less than 2 seconds. This series is also compatible with the moulds of the Top-Entry generation, ensuring continuity for existing customers.
The HOD-Series, on the other hand, is the world’s first system specifically developed for the large volume container market. The 160-ton system meets all the technical requirements of this demanding sector, and plans are already in place to introduce a 240-ton system for HOD-preforms up to 400 mm in length and shot weights of up to 9’900 gr. This expansion underscores Otto Systems’ commitment to innovation and meeting market needs.
Turnkey Solutions from Otto
Collaborating with Otto Systems means benefiting from over 40 years of experience in PET preform production, thanks to their close cooperation with Otto Hofstetter AG. This partnership ensures comprehensive support from the initial idea through to the production-ready system. Otto Systems offers complete, turnkey solutions, leveraging Hofstetter’s extensive expertise and research and development capabilities.
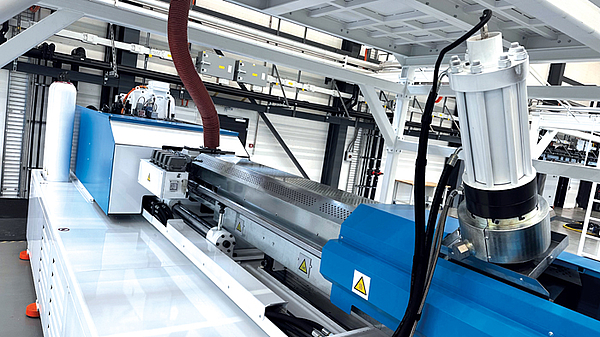
Conclusion
Otto Systems has set a new benchmark in the preform production industry with the launch of the HOD-Series. By focusing on compact design, high productivity, and tailored solutions for special applications, Otto Systems addresses a critical gap in the market. The strategic partnership with Otto Hofstetter AG further enhances their offering, providing customers with innovative, efficient, and economical production solutions. The HODSeries is poised to become the go-to solution for large volume container production, marking a significant step forward in the industry.
The comPETence center provides your organisation with a dynamic, cost effective way to promote your products and services.
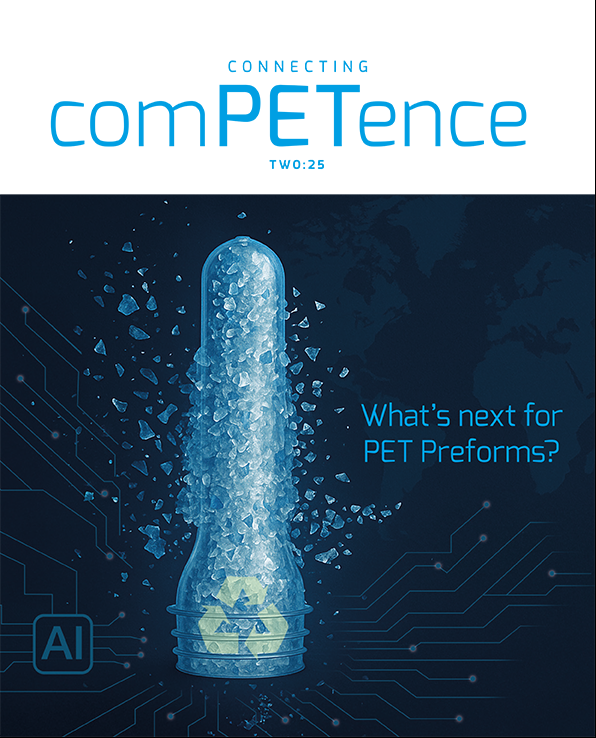
magazine
Find our premium articles, interviews, reports and more
in 3 issues in 2025.