Featuring 1,700 m² of machine floor space, the ENGEL technology centre is a plastics processing operation in its own right and one of the most modern in the world. “We ourselves are the first users of all newly developed inject 4.0 technologies,” says Engleder. ENGEL already bundles a large number of its products and solutions for the smart factory under the inject 4.0 banner. The portfolio is continually being expanded. Numerous new inject 4.0 products are also in the development pipeline for K 2019. “The aim of inject 4.0 is to leverage the full potential of machines, systems and technologies in order to strengthen competitiveness, act more flexibly and master the increasing complexity of production,” Engleder points out. “With the new possibilities offered by our customer technology centre, we are able to demonstrate in a particularly vivid and tangible way how this great potential can be leveraged not only completely, but also efficiently and economically, in line with the individual requirements of the processors.”
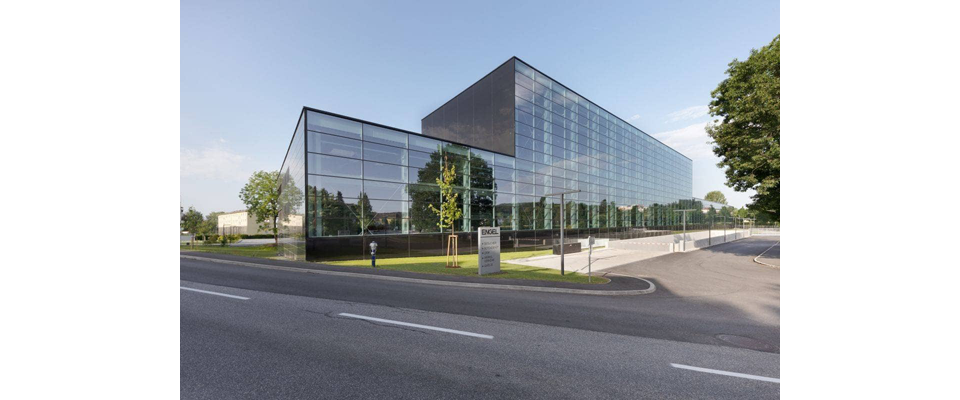
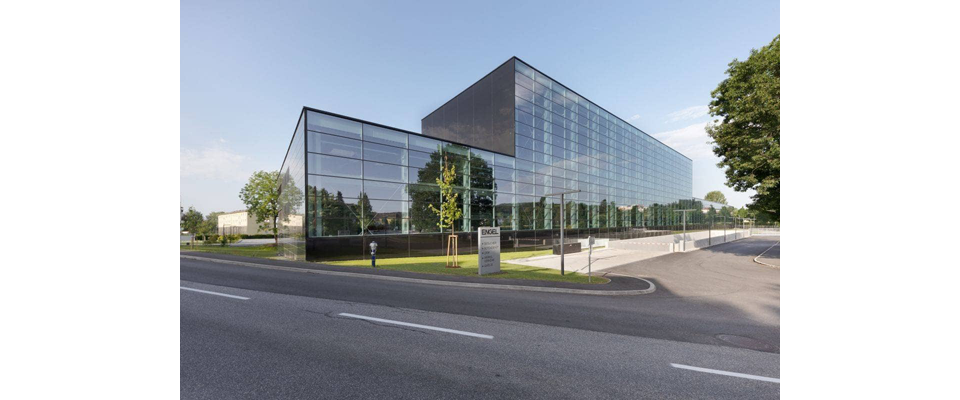
The new ?ENGEL Technology Centre. Innovation at heart? is connected to the ENGEL Group's other worldwide customer technology centres. The possibilities of the innovative inject 4.0 technologies can thus be conveyed in a practical and tangible manner. (ENGEL Group)
Launch
New ENGEL technology centre makes the smart factory a tangible experience
ENGEL AUSTRIA has launched its new “ENGEL Technology Centre. Innovation at heart” at its headquarters in Schwertberg, Austria. “We have created our own pilot plant for vertical integration in injection moulding and can thus support our customers even more comprehensively on their way to implementing the smart factory,” says Dr. Stefan Engleder, CEO of the ENGEL Group. The new customer technology centre is the heart of the latest expansion at headquarters.
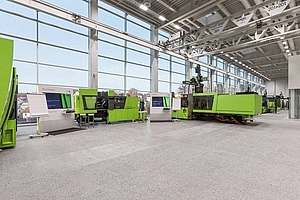
Process optimisation across multiple locations
Vertical integration describes the integration of all machines, systems and manufacturing processes within a company or manufacturing network into a superordinate control system. The ENGEL technology centre provides particularly practical demonstrations of integration beyond the boundaries of a single location, as it is connected to the technology centres at ENGEL’s plants and subsidiaries worldwide. “From Schwertberg, we can monitor and remotely maintain the production cells in Shanghai, Mexico or Hanover, for example,” says Engleder. Key products for this are the ENGEL e connect customer portal and TIG authentig. The MES by ENGEL subsidiary TIG uses a cloud solution to make all machine parks within the production network transparent. This means that, for example, machine utilisation can be optimised across multiple locations.
First user of the latest technologies
In addition to transparency, intelligent assistance systems make a major contribution towards boosting production efficiency in the smart factory. All the machines in the new ENGEL technology centre are equipped with a wide variety of assistance systems from ENGEL's iQ product family. In addition to iQ weight control, iQ clamp control and iQ flow control, which have been very successfully established in injection moulding companies for some time now, the brand-new iQ systems, which ENGEL will be presenting at K 2019 in Düsseldorf in October, are deployed at the technology centre at a particularly early stage. “Innovation at heart” is not only part of the new technology centre's name, but also the guiding policy. “At the technology centre, we show what is possible today and what we will make possible in collaboration with our customers in the future,” emphasizes Engleder. One of the forward-looking projects focuses on establishing a knowledge database which pools expertise and experience within the group. “In the future, knowledge databases will empower us to solve the challenges of injection moulding practice even faster and more purposefully,” says Engleder.
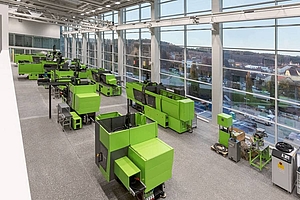
Horizontal connectivity: the next step
Digital transformation is another forward-looking topic. The individual vertical platform solutions are connected with each other horizontally along the value chain. Where vertical networking is about function-related and mostly domain-specific optimisation of the individual stages in the value chain within a company, horizontal networking allows processes to be optimised across functions along the entire value chain. A pilot factory for this was opened in Linz at the beginning of June. The aim of the LIT Factory is to use digital system models to research and further develop product creation processes along the value chain – from materials to product development, and from production to recycling. In addition to ENGEL, 24 other companies, primarily from the Austrian and German economic areas, are involved in founding and establishing the LIT Factory. “Thanks to participation from various disciplines such as mechatronics, IT or environmental technology, and to the support of various industrial partners, it is possible to cover the plastics industry's entire value chain in a single factory. The resulting synergies, for example, the joint use of research results, contribute significantly to the further development of digitalisation competency,” says Stefan Engleder.
The comPETence center provides your organisation with a dynamic, cost effective way to promote your products and services.
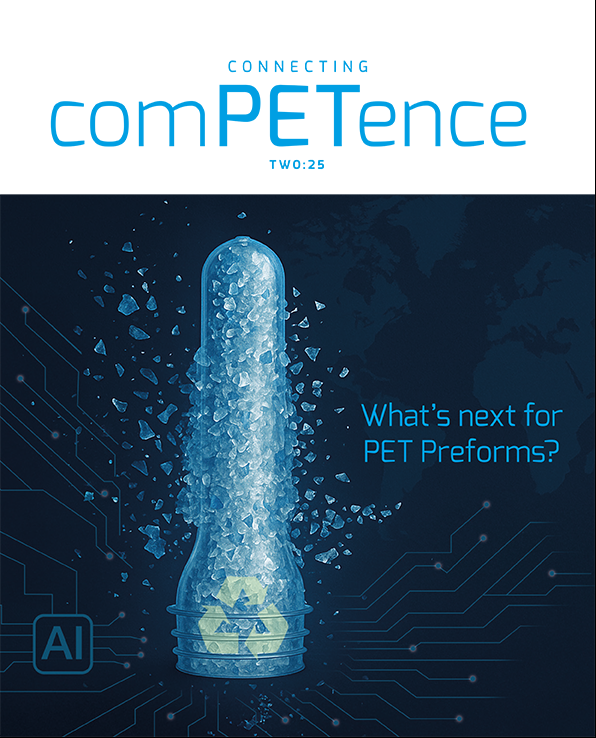
magazine
Find our premium articles, interviews, reports and more
in 3 issues in 2025.