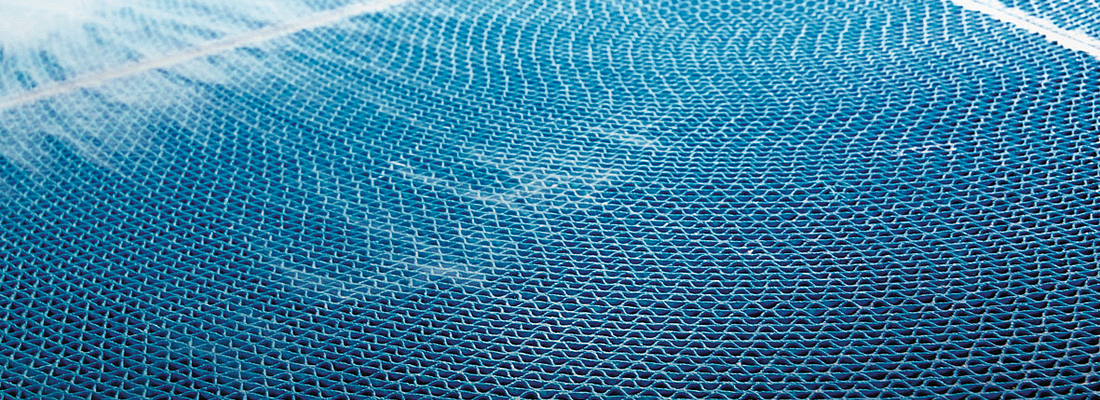
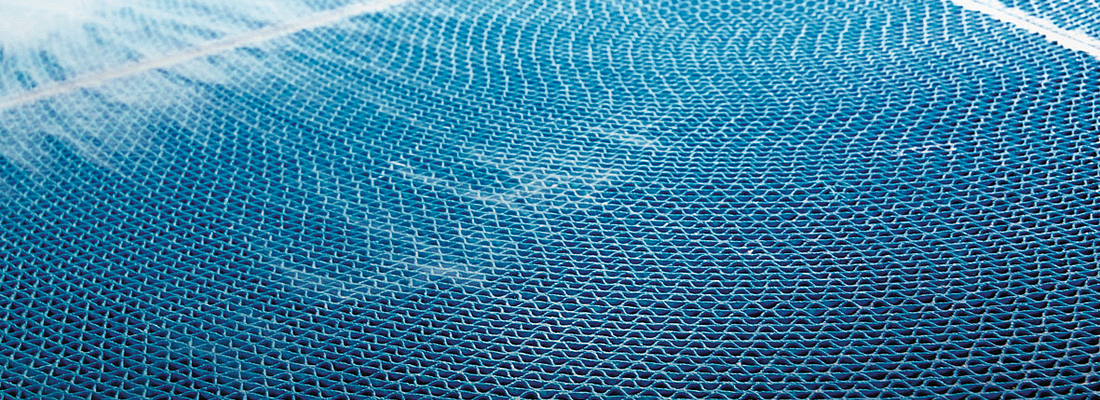
Industry 4.0 is right now the current trend of automation and data exchange in manufacturing technologies and meets as well the material handling process. Therefore Eisbär is going new steps and focused to be a main part in this particular structure to communicate and cooperate with every part of the complete process.
Innovative Systems for Drying
In the field of auxiliary equipment, Eisbär manufactures systems to improve quality and productivity for the plastics industry, specializing in products to avoid condensation on moulds, drying of plastic resin and the process of PET flakes.
New Development in Material Drying for low throughputs - “Plug & Play”
Granule drier as „All-in-one-solution“ for 50 to 200 kg/h
(fig. 1).
-Screw on, plug in and start
-Electric power supply only
-Lowest energy consumption
-No water connection
-No installation on-site
-Nearly service free
-Highest availability
-WLAN connectivity to your mobile device
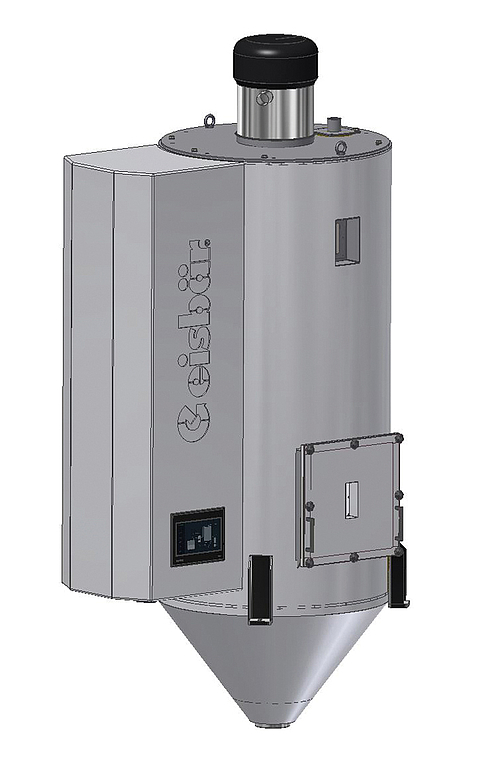
Fig 1: “Plug and Play” Unit - Material drier plugged on the drying hopped
Continuous Drying Process for Granule
Efficiency, reliability with an energy saving of up to 20% compared to conventional driers: That is how renowned manufacturers of plastic parts around the world characterise the Granule Driers from Eisbär Trockentechnik GmbH.
Manufacturers are aware of the insufficient or incorrect drying. The results are the production of scrap and impair the quality of the product which leads to costly complaints. The manufacture of high-quality products are the top priority objectives of the plastics processor. For these reasons, it demands a controlled drying process with high operational reliability. The continuous and energy-saving drying from Eisbär satisfies precisely these demands.
Specific drying of the granule logically increases the quality and efficiency of the production and prevents scrap, production stoppages and customer complaints. Constantly dry raw material is thus included among the essential preconditions for the injection moulding of quality high-class plastic components.
The drying of granulated material with dry air has proven reliable. Various methods are known. With most suppliers, one must switch over between two or more desiccant beds: because while in one of the two, the process air that had previously dried the granule is dehumidified, the other is in turn regenerated. Consequently this process runs intermittently and as a result causes corresponding fluctuations in the dew point of the dry air. In contrast to this, in the Eisbär drier the process runs continuously.
The heart of the continuous material drying process is the slowly rotating adsorption wheel with its multitude of honeycombed, axially aligned tunnels. The inner walls of the tunnels are lined with a desiccant. As it flows through the lower half of the adsorption wheel, the process air is dehumidified by the desiccant. During the next quarter-turn, hot regeneration air flows through the tunnel and in turn dehumidifies the desiccant. In the next quarter-turn, the adsorption wheel is cooled to operating temperature and is then able to dehumidify process air again.
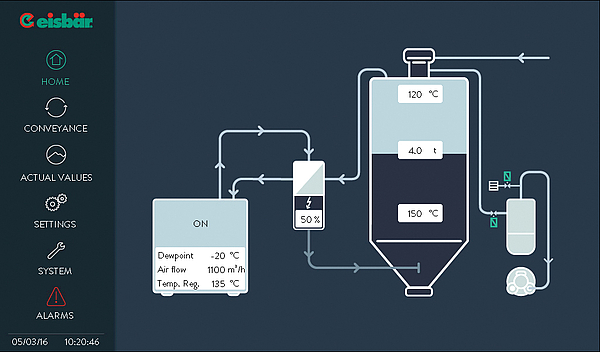
Fig. 2: Display
Simple User Interface
To operate the system there is a touch panel with graphics capabilities (fig. 2). On a series of monitor pages, the operator can call up operating parameters in different languages, such as for instance process-air dew point, filling level in the drying hopper, delivery capacities, valve status or process temperatures. On this monitor pages you can also adjust process set points and alarm settings. After selecting with the cursor, the monitor displays the type of error, the time at which it occurred and a fault signal number. The Help function provides information on how to rectify. Over a potential-free centralized contact, the signal can be transmitted to a higher-level alarm system with lamps, flashing lights, horns etc.
Over another potential-free contact, the plant can be controlled from the injection moulding machine. Thus e.g. during a machine stoppage one can switch to Standby-Mode and perform a temperature reduction. With this method you can save energy and the granule is not too dry and subsequently the material does not become overheated. The system can also be equipped with an Automatic option, which continually adapts the filling level in the drying silo to the granulate throughput. Also as an option, the Material Drier can be networked with a computer or the controller of the injection moulding machine by means of Profibus, Ethernet etc.
The dryer can also communicate over Ethernet (Profibus or ISO on TCP/IP) to a MES (Manufacturing Execution System).
Service-friendly and highly reliable
The two radial fans with direct drive and the low speed adsorption wheel are the only moving parts of the system. This also reduces the costs of servicing the plant. There are only filters to be cleaned as required.
Although the drying of granule with this method represents an innovation, Eisbär has already many years of experience in mould dehumidification. The customer therefore has a competent partner in Eisbär with practical know-how.
PET Flake Processing
We have to address the demand for the use of flake in the standard process of preform production. Sustainability and environmental responsibility is focus in our development of new products. Eisbär and the related new developments are the results of our customer requirements.
The development is focused on:
-Flake Drying & Processing
-Cost Effective distribution of dried and
hot flakes to the IMM
-Low Energy Consumption
-Ease of Operating & Maintenance
All the features described are going into further and future projects Eisbär is being a part of now already. We are a step ahead and our intention to be focused in new developments together with our customers. Some technical highlights and detailed features.
Digitalisation - Industry 4.0
The increasing integration of the Internet for everything into the industrial value chain has built the foundation for the next industrial revolution.
As a result Eisbär is a part of a new plant for PET recycling and preform production in Germany. The focus is material pre-cleaning, material handling, conveying, distributing and drying (RFID distribution, MES connection, batch tracing, automated recipe adaption) (fig. 3).
For the brand new and maybe most modern plant Eisbär designed and supplied: Resublimate Flakes (Preliminary Purification), RFID Distribution, Mixing/Dosing and Material Drying and Mold Dehumidification
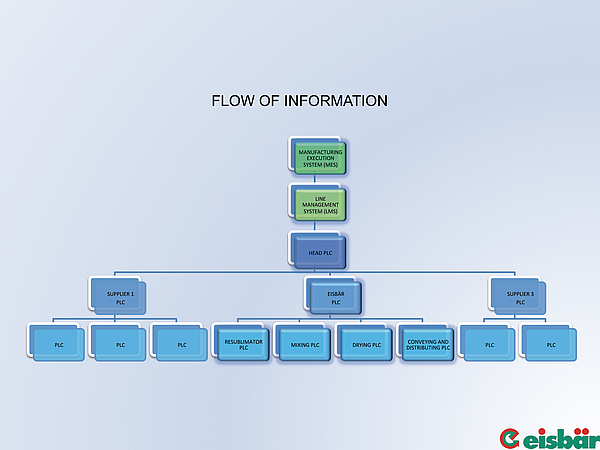
Fig. 3: Digitalisation – „Flow of information“
Conclusion
Our experience as an established manufacturer with extensive practical knowledge and main focus in understanding the customer requirements is our outstanding strength. The customer therefore has a flexible partner with Eisbär for new and competitive tailor-made system solutions. Another important Eisbär competence is digitalisation and clearly structured visualisation of all operational data for efficient control and maintenance.
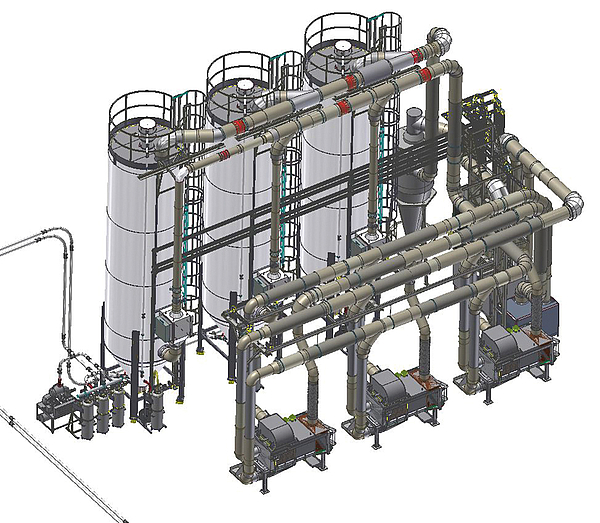
Fig 4: Resublimator
The comPETence center provides your organisation with a dynamic, cost effective way to promote your products and services.
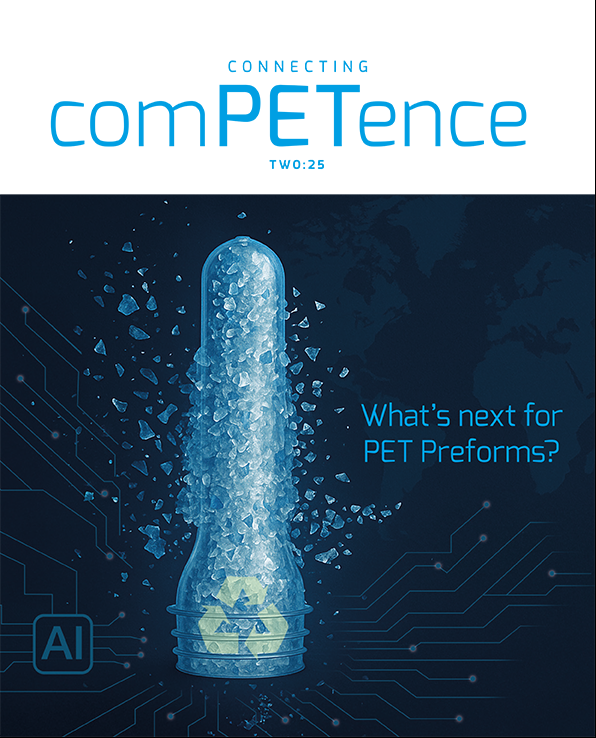
magazine
Find our premium articles, interviews, reports and more
in 3 issues in 2025.