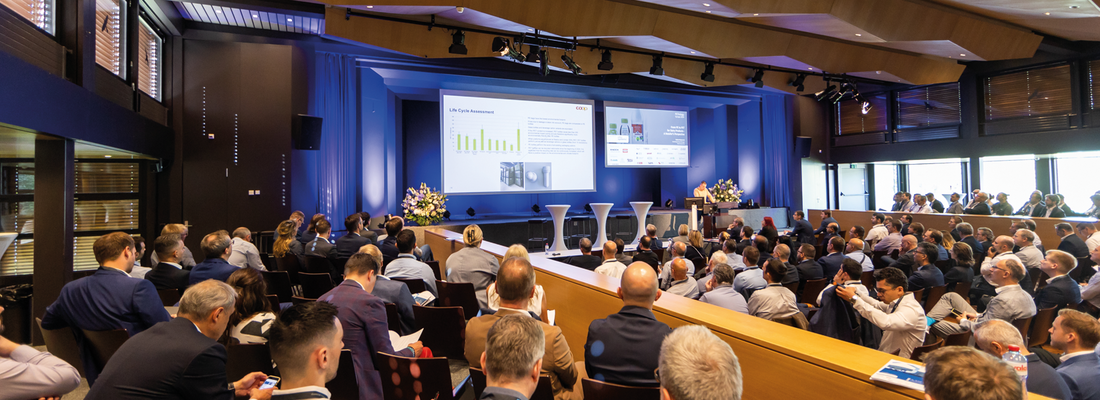
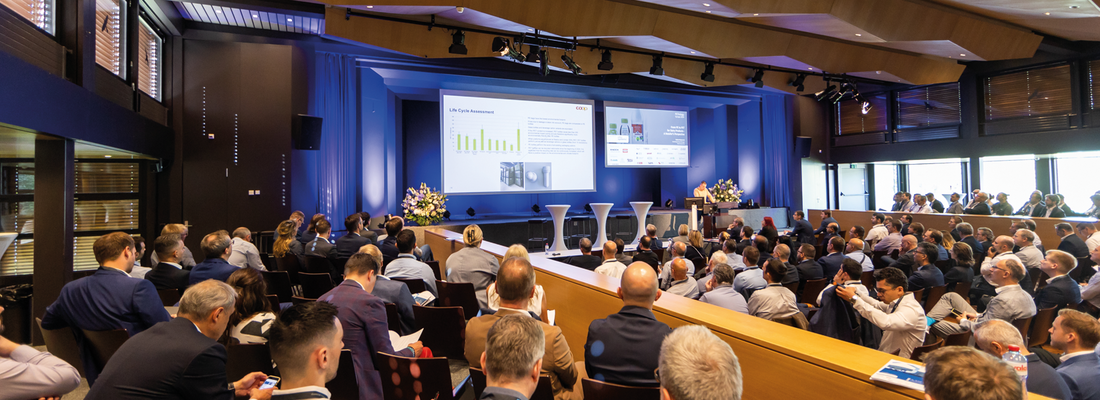
The PETnology conference helps the market discuss current and future issues, where the packaging market is heading and how the PET packaging industry can meet the challenges and opportunities ahead.
For many executives and experts, the focus on the challenges facing the market was at the heart of the PETnology Europe 2024 on Lake Zurich in Switzerland.
From PE to PET for dairy products
Darko Stojanovic reports on the project “From PE to PET for dairy products”, which was launched at the beginning of 2023 as part of a kick-off meeting between Coop and Emmi.
In order to test consumer acceptance of PET bottles for milk, a test with two Bio Regio milk products in transparent PET bottles (without advertising or communication support) was launched in Eastern Switzerland in June 2023.
Based on the test results and the results of the Life Cycle Assessment commissioned at the same time as Emmi, a decision was made as to which products should be converted to PET. Since January 2024, various milk and dairy products (own brands and branded products) have been converted to PET. The aim is to convert even more milk and dairy products currently packaged in PE to PET in the future.

Case study: Color Change on Preforms B(L)ACK TO WHITE
Colour change from black to white has always been considered one of the most difficult aspects of plastics processing. It is even worse when it comes to preforms and closures, where even the slightest imperfection can lead to the rejection of an entire batch.
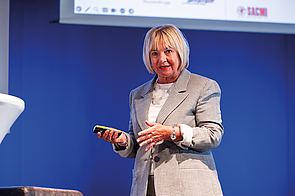
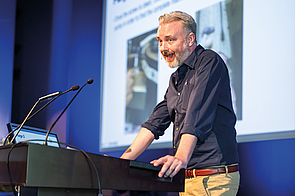
Fortunately, there is a solution by the use of a state-of the-art purging compound ULTRA PLAST with no need to change process parameters and for excample to change from B(L)ACK TO WHITE in less than an hour.
Innovations in Cost Effective PET Manufacturing
While Polyester manufacturing technology dates back to 1950’s, over the past 70 years, the polyester capacity growth has continued at a steady pace of about + 4- 5%. As this market continues to grow, the capital and operating efficiencies have become far more important and the development of end uses / specialty PRODUCT APPLICATIONS are about to reach an end point.
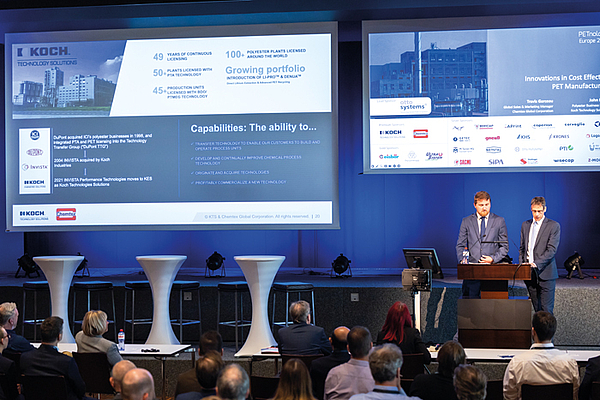
Koch Technology Solutions, in collaboration with Chemtex, presented their innovative solutions for highly cost effective large scale plant solutions that meet the needs of different end uses with highly cost effective capital efficiency. They explained their aim to create value for customers for the long term sustainability of their production facilities from both an economic and environmental sustainability perspective.
Challenges facing PET preform manufacturers today
The economics of PET preform production are at the heart of the challenges facing manufacturers today. But how can this be achieved in the face of volatile raw material prices and record energy costs? What is the impact of the increasing importance of product sustainability and EU requirements for recycled content? How are manufacturers meeting their customers’ demands for flexibility, delivery times and availability? What new requirements will manufacturers face as their customers ask them to report on their carbon footprint and ESG performance? How will skills shortages affect the production and operation of high performance systems?
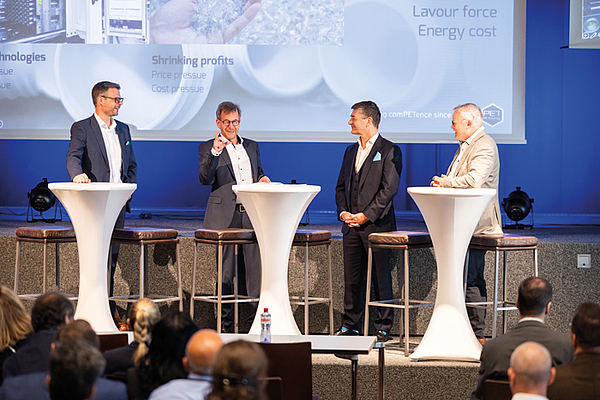
Otto Appel discussed these and other questions with: Otto Hofstetter of Otto Hofstetter AG, Reto Bamert of Otto Systems and Wolfgang Bonerath of Rawoplast GmbH.
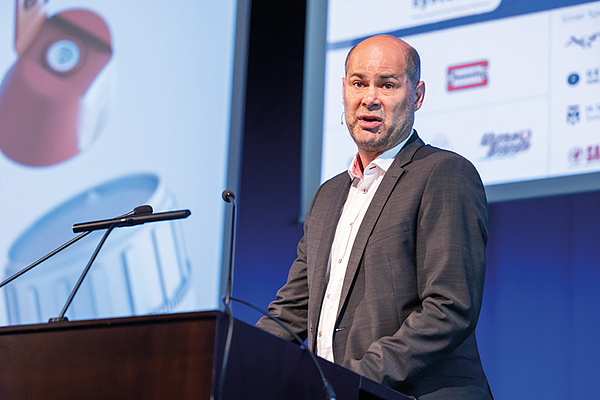
Latest Developments in Closures – meeting consumer and market trends
Thomas Schmidt’s speech described how BERICAP closure solutions contribute to the packaging of today and tomorrow. Consumer convenience and safety, product integrity and operational excellence, e.g. reliable filling lines, define the key performance of closures. He explains how sustainability is addressed through continuous lightweighting of BERICAP closures and new developments in neck finishes and application technology. Mono-material designs and the use of PCR - where appropriate - support the circularity of their products and the whole pack.
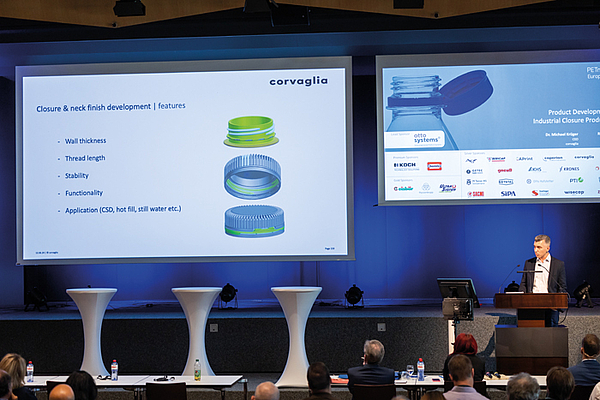
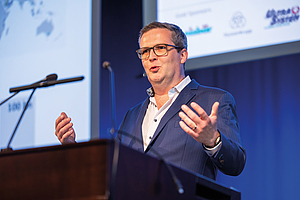
Product Development X Industrial Closure Production
The presentation introduced the Corvaglia Group, its role in closure development and recent advances in neck finishes and closure designs. The importance of neck finish standardisation and the benefits of Corvaglia’s mould technology were discussed. Dr Michael Krueger and Rufat Dauti highlighted the importance of quality in closure production and how it is influenced by product development. Finally, the differences between slit and injected bridges were discussed.
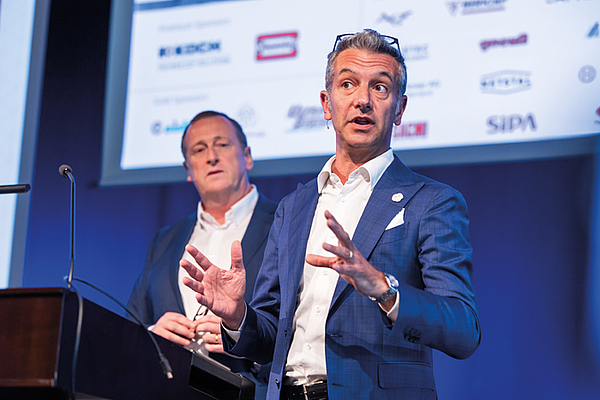
The Tethered Challenge – From EU Directive to Deliverable Product
The two speakers described a long journey from the publication of EU Directive 2019/904 to today. There are only a few days left until the principles of the directive officially become part of our daily lives as consumers of beverage products.
The industry as a whole has faced many challenges and has shown a unique ability to challenge all recent achievements and results. Wisecap® and SACMI have taken the audience through the various stages of this shared journey, focussing on the advances in products and technologies.
A kind of journey from day to day, where it became clear that nothing comes for free and that the impact on the supply chain was always at the centre, trying to minimise it as much as possible. Other events are somehow linked to or fuelled by this revolution.
Education is revolution: only the right education of the end consumer will support this revolution in the packaging market and make it even more effective! New neck finishes are entering the market at an unprecedented pace and activities such as DRS and bottle-to-bottle will be further strengthened. Wisecap® and SACMI sought to answer questions such as: Will more and more countries adopt tethered caps? Will consumers help drive the tethered cap concept forward?
How to Address Raising Demands on Ecological and Economic Factors in Closure Production
In a case study on the production of flat water closures, z-moulds demonstrated how the demanding requirements of closure production can be met today.
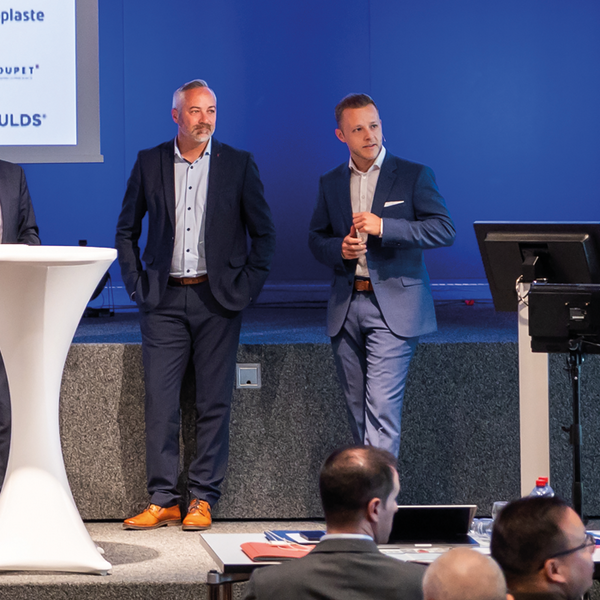
In a very price-sensitive market, the weight of the closure and operational performance are the main challenges. With the latest development from z-moulds it has been possible to reduce the weight of the closure by around 25% while increasing output by more than 50%.
Eisbär‘s Sustainability: Remarkable Technical Advances in PET Processing and Exciting New Solutions
Since its foundation 30 years ago, says Elfie Breuss, Eisbär has been a leader in providing drying solutions for recycled materials.
With a focus on rapid recipe changes and the flexibility to process small batches efficiently, Eisbär’s product range ensures high availability for both short runs and continuous operation.
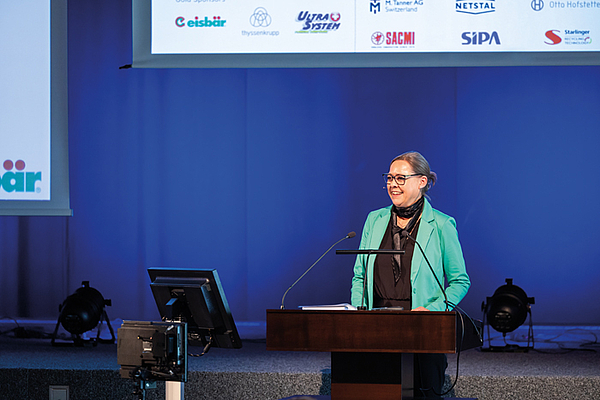
In particular, Eisbär is adapting to the evolving landscape with new features such as redundant heat exchanger systems, improved selfregulation and fast product changeovers, emphasising adaptability even with highly contaminated materials.
At the heart of all Eisbär products is the desiccant wheel, which efficiently retains moist air while dehumidifying and continuously regenerating the processed air at low temperatures.
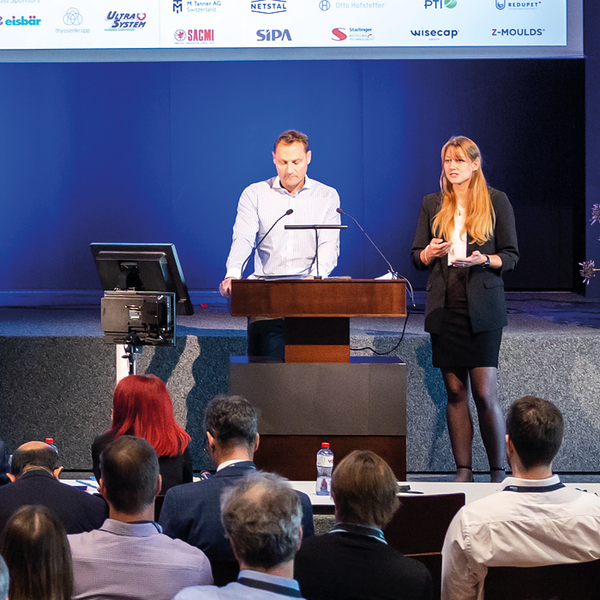
PET Preform Production - Achieving More with Less
Preforms for PET beverage bottles can present a number of challenges to production operations: the increase in recycled content and reduced wall thicknesses, coupled with the need for higher output rates, are significantly increasing the demands on production equipment. Today’s solutions are different from those of a few years ago.
The presentation by Alexandra Stuber and Stefan Kleinfeld focused on how availability can be further increased, energy efficiency reduced and preform quality continuously monitored.
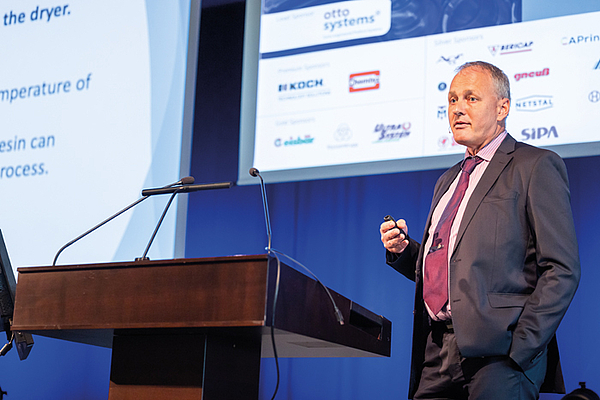
WAVE: New Rules how to drive a PET Drying-System
In a preform system, the PET dryer and the injection moulding machine are equally important. While the injection moulding machine is optimised down to the last detail by the operator, the dryer, which is often installed on a mezzanine floor, is hardly known in detail. This is best left to the dryer manufacturer’s control system, says Stefan Bock. From an energy and process point of view, this is often a disadvantage for the preform manufacturer.
WAVE (Waste Analysis Visualisation of Energy) now offers a completely new approach: three simple graphs on a screen immediately show the operator how economical the current drying process really is, so that he can intervene accordingly. WAVE is a patent-pending innovation from ReduPET GmbH.
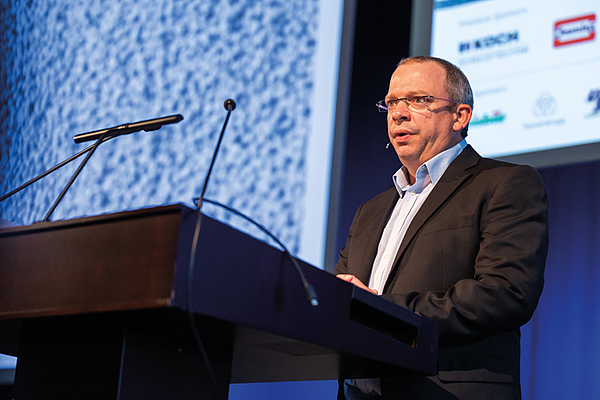
Creating a Snapshot of PCR Quality
With PCR, everything is a snapshot in time, and you need to collect data over a long period of time to get a baseline of the true quality of all providers, reports Dr Jérôme Larrieu, and that’s not as easy as you might think. Through rigorous testing systems, one can begin to understand the quality issues in all types of PCR collections, from street collection to deposit collection, and create a roadmap of expectations and opportunities to ensure the success of PCR in your packaging.
Dr Jérôme Larrieu calls for this study to be developed beyond the basics. We realised that we not only need to test the pellets, but also develop plaques and optimise the design of the preform and the bottle. We need to keep this discussion going with new data and insights!
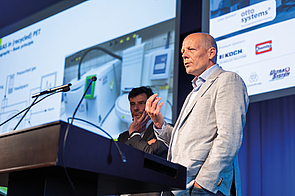
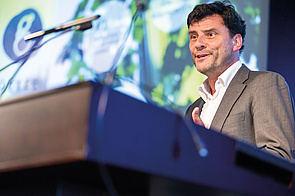
Monitoring non-intentional added substances (NIAS) in rPET matters!
The importance of safe packaging products is imminent. With rising rPET content obligations in PET packaging the monitoring of NIAS impurities in rPET becomes more important.
GETEC laboratory helps PET recyclers, packagers and Brand Owners detecting the rPET NIAS content. GETEC introduced a new analysis methodology to detect Bisphenol-A in rPET. Herewith, more insights in NIAS levels in rPET can be achieved.
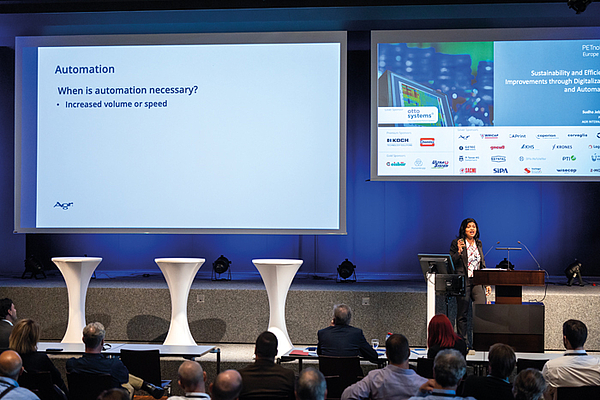
Sustainability and Efficiency Improvements through Digitalization and Automation
Agr’s products for plastic include in-the-blowmolder thickness control and process management systems for PET containers as well as high-throughput, vision-based on-line inspection systems for containers and preforms, automated measurement devices and a variety of manual gauges that can be used in the laboratory or on the production floor.
Agr International is strongly committed, Sudha Jebadurai mentioned, to be the industry leader in container quality management while offering products that can help bottle manufacturers improve efficiencies, reduce costs and contribute to responsible management of resources.
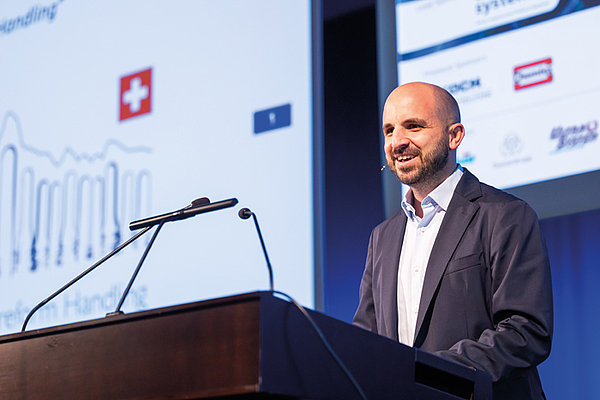
Shaping the Future of Preform Handling
Tanner has been developing and producing preform handling systems for our customers worldwide for over 40 years. Over 4,000 systems are currently in operation.
What began with feeding preforms into the blow moulder has seen many products and functions added over the years. From preform loading in the first process step, to preform sorting and feeding, to complex quality optimisation, Tanner cover the entire preform handling process upstream of the blow moulder or inspection system. The next milestone „Future Preform Line“ was described in the presentation from Marco Tanner.
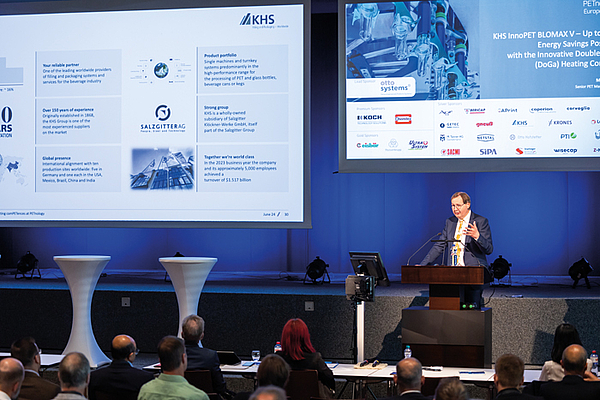
KHS InnoPET BLOMAX V – Up to 40% Energy Savings Possible with the Innovative Double Gate (DoGa) Heating Concept
Marc Eysel discribed the advantages of the innovative KHS heating concept in this presentation:
- Double lane with central NIR (near infrared) lamps
- Shorter heater length (double preform quantity in front of the heaters)
- Heater box ventilation control for maximum energy efficiency - Up to 30% energy saved* - Up to 40% reduction in the number of heater boxes / heater lamps**
* Compared to conventional IR heating systems. ** Compared to a single gate.
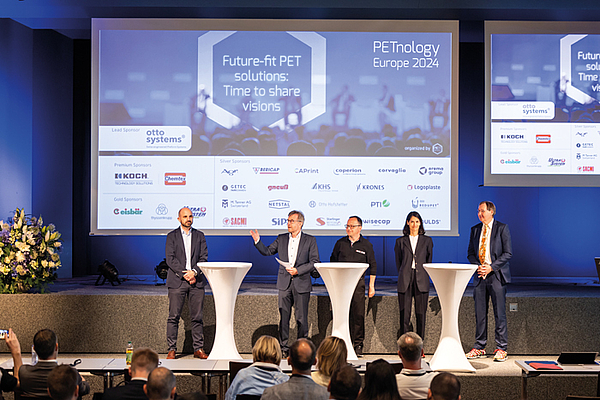
Challenging Container Production as an Example of SIPA‘s One-StopShop: Packaging design + Preform innovation + Advanced Container Production Technologies
For over 30 years, SIPA has been acknowledged as a comprehensive one-stop-shop, encompassing preform and container production technologies up to the turnkey lines supply. Thanks to this unique and complete offer, SIPA is able to provide the most demanding packaging solutions with flexibility, efficiency and a focus on the environment.
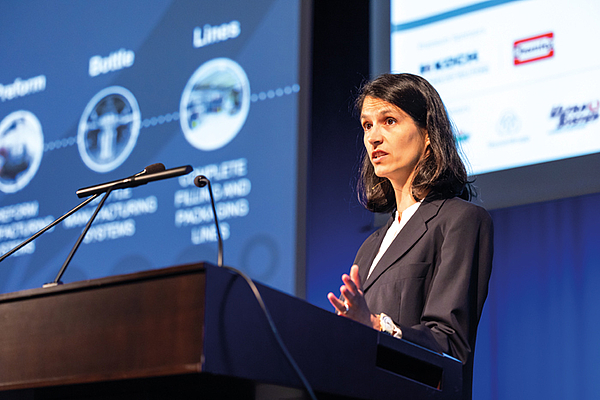
Sipa’s presentation featured a selection of innovative, sophisticated and sustainable container developments for various markets, from beverages to chemicals.
From material analysis, preform and container design to the final production steps, SIPA can flexibly select the right technology that not only optimises cost savings but also prioritises sustainability for the customer, says Anna Horecica-Csiki.
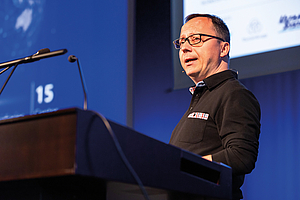
We close the loop
“The circular economy is a key approach to unlocking the sustainability potential of PET bottles. As the world‘s leading supplier of machines for filling and packaging PET bottles, we are committed to the sustainable establishment of this circular economy“, says Robert Aust.
To underscore this point, KRONES is now closing the last remaining gap in its portfolio and will in future be able to offer all the equipment required for setting up and operating this circular system from a single source - from preforms, through filling and packaging, right up to plastics recycling.
The presentation, discussed the associated opportunities for the circular economy and highlight the benefits for companies in the beverage bottling industry from the fact that KRONES can now supply all key components from a single source.
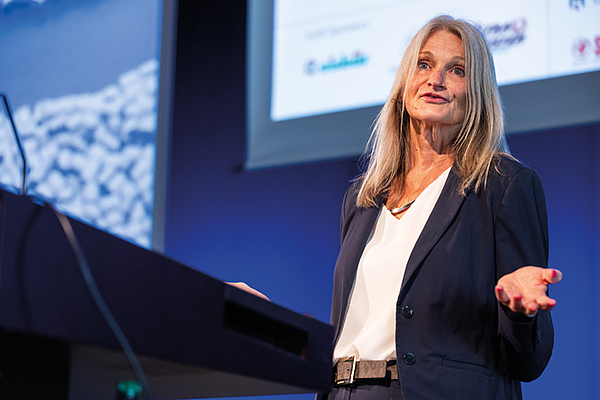
Recycling of PET on the co-rotating twin screw extruder
Coperion has been manufacturing twin screw extruders for the plastics and food industries for more than 60 years. The ZSK is the suitable twin screw for the processing and recycling of PET. Due to the high torque, the PET can be processed very gently at low screw speeds, and due to the large free volume, even high amounts of volatile components can be degassed safely
With the ZSK process, throughput is not limited by predrying capacity or screw size. For example, a ZSK with a screw diameter of D = 177 mm achieves a throughput of 8,000 kg/h. This throughput would require at least three 200 mm single-screw extruders.
rPET: 20 Years ago & now
Paul Niedl gave an insight into the rPET market 20 years ago and how it has changed to date.
He focused on current recycling targets, looked at PET recycling capacity and discussed extended producer responsibility.
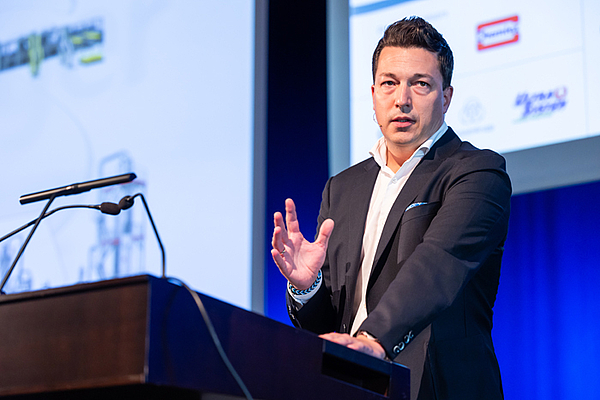
20 years ago, the economy was very price-driven - how has this changed over time? And last but not least, what has changed at Starlinger in the area of PET recycling?
Paul Niedl looks back at PET recycling solutions from 2004 and compares them with the latest innovative technology, the new recoSTAR PET art from Starlinger
EREMA Group’s Contribution to a Safe an “Easy to Digest” Circular Economy: CADEL’s Software Tool for Risk Assessment, Interpretation and Analysis
The use of recycled material in applications of added value, such as packaging designed for food contact, needs an exhaustive and routine quality control.
INTERPRETATION of data of the chemical composition of the material based upon rules such as FCM EU 10/2011, REACH, etc. is vital.
Cadel helps to carry out an effective risk assessment of your recycled plastic material to ensure their safety and to comply with the standards stablished by the relevant global organizations.
Cadel has developed a software tool that allows knowing if the material complies with the safety requirements for applications such as food contact, cosmetics or hygiene.
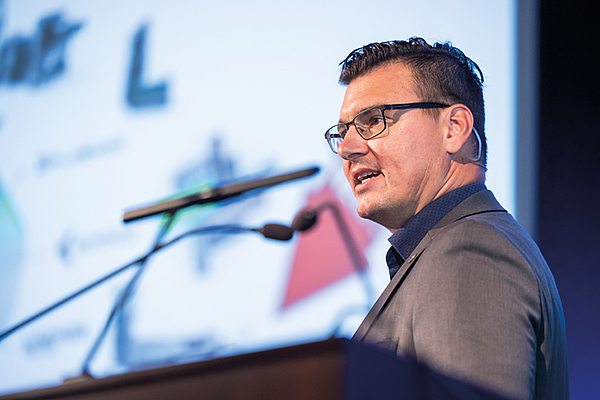
Cadel helps you to visualize the Marketplace positioning of your rPET material with regard to other competitors thanks to our database.
The software tool takes into consideration the safety standards that are currently scattered among different legislation and protocols.
And it promotes a quicker interpretation and economizes in data processing.
Cadel helps you to visualize the Marketplace positioning of your rPET material with regard to other competitors thanks to our database.
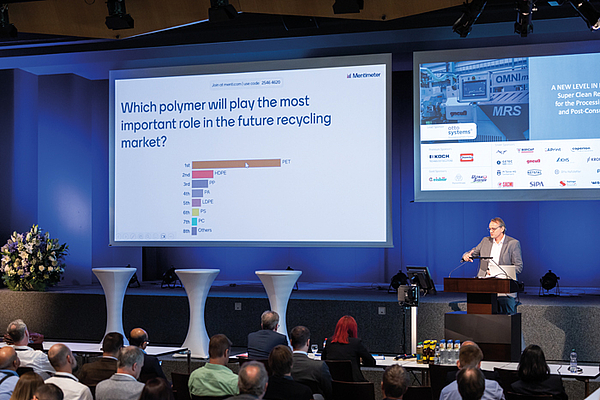
A NEW LEVEL IN PET RECYCLING – Super Clean Recycling Systems for the Processing of Industrial- and Post-Consumer PET waste
Plastics recyclers face a dilemma: on the one hand, the required recycling quotas mean that the quality requirements for the recyclate are constantly increasing. On the other hand, the properties of the available plastic waste are subject to strong fluctuations. The new OMNI recycling systems from Gneuss meet exactly these requirements. OMNI recycling systems are characterised by „super-clean“ recycling qualities in a single process step. This applies to all kind of PET waste.
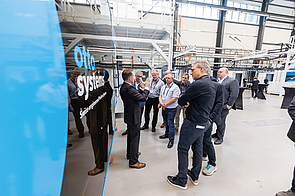
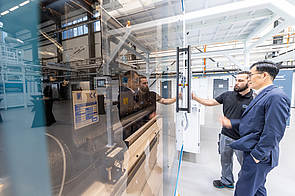
Exclusive insight into the new TechCenter
Otto Systems opens its new TechCenter, not far from the headquarters of Otto Hofstetter AG. Attendees of the PETnology Europe 2024 have been part of an exclusive tour of the new building and its infrastructure. In addition, a PET series and a HOD series system was presented in production and a brief insight into the Otto Hofstetter AG production facility was also part of this successfull open house.
The comPETence center provides your organisation with a dynamic, cost effective way to promote your products and services.
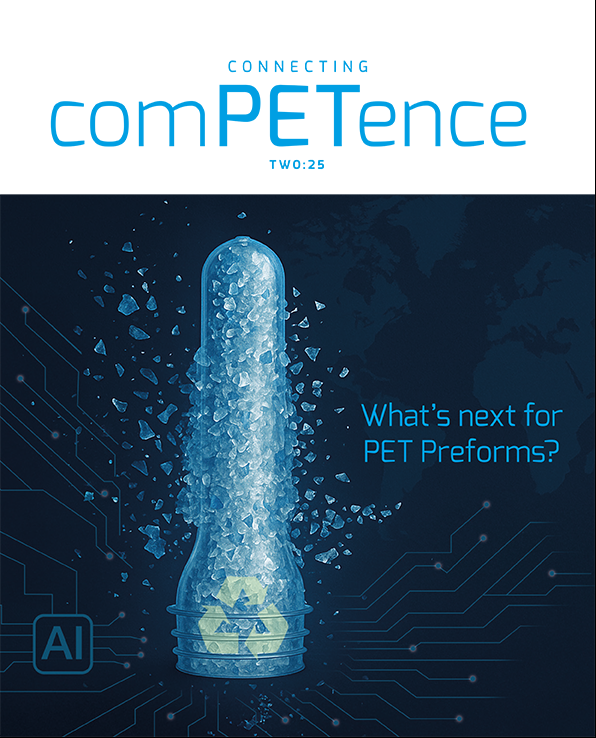
magazine
Find our premium articles, interviews, reports and more
in 3 issues in 2025.