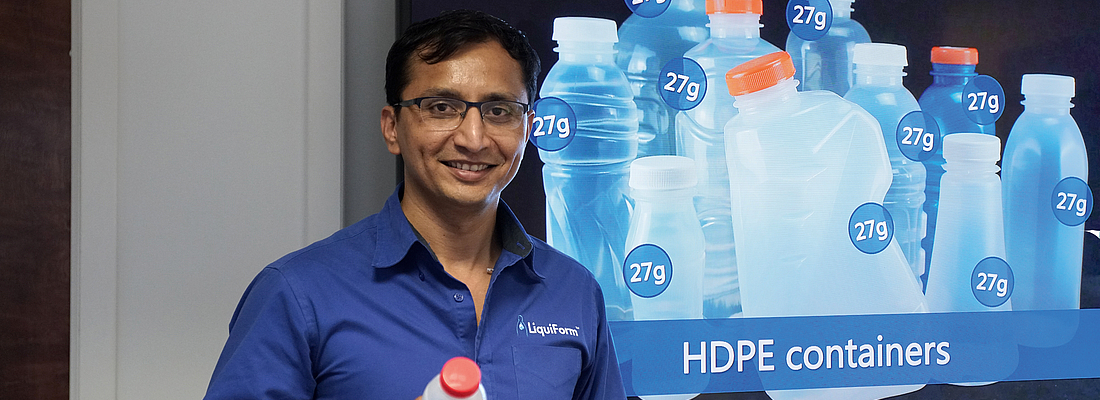
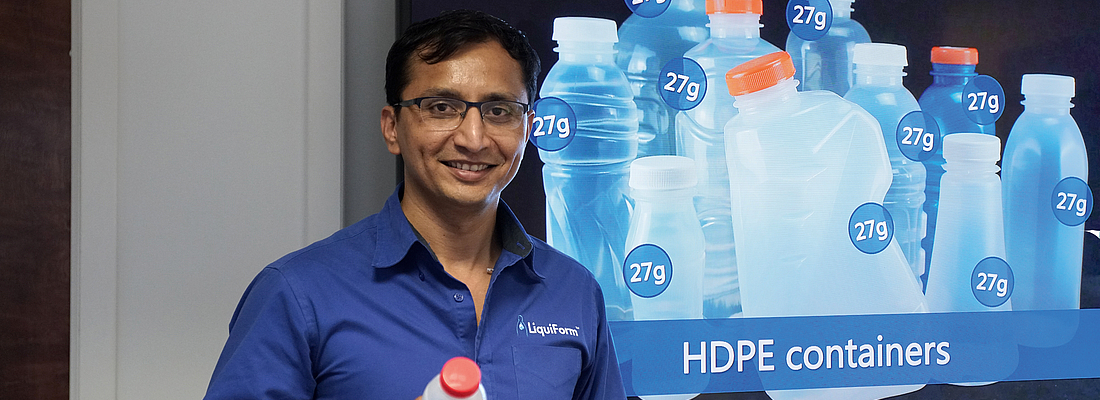
The LiquiForm project was first presented at the PETnology Conferences in Nuremberg, Germany, in 2014 and 2015. Since then, the LiquiForm team has carried out numerous tests and trials to demonstrate the capabilities of this innovative process. Now in 2017, we can confirm that this development project has been successful.
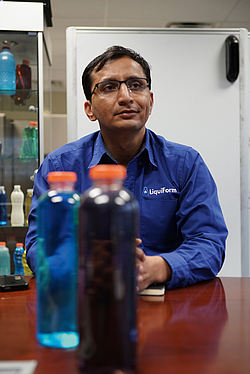
During our meeting with Ashish Saxena, VP and GM of the LiquiForm Group, we discussed the status, improvements, surprises and challenges of this innovative technology. While the proof of concept was carried out on a rotary platform machine, LiquiForm has conducted their R&D work on single-station lab machines. Saxena emphasised that this work has not yet been implemented on an industrial scale.
At LiquiForm in Saline, MI, USA we met an enthusiastic and dedicated team who think outside the box and are deeply involved in the development work. We greatly appreciated the update Ashish Saxena gave us on the fascinating LiquiForm project.
Saxena noted that it takes a certain amount of time at the beginning of a new idea or innovation to mull it over and define the value proposition. This is necessary even when the benefits seem obvious, such as was the case with LiquiForm, even at a very early stage. Nowadays, LiquiForm has a much clearer vision than back in 2014. “We have really done our homework,” Saxena added, quantifying the technical benefits.
The capabilities demonstrated by LiquiForm today reflect the variety and potential of this technology. Over the past couple of years, Saxena and his team have formed over 100 different packages with varying shapes, sizes, weights, designs, and materials. These include swirls, ovals, and off-centre necks using PET, 100% PCR PET, HDPE and PP in a variety of weights ranging from 8.5 to 92 g and volumes from 200 to 2,000 ml. LiquiForm has successfully formed containers for products under cold, ambient, and hot fill fluid temperatures, and ranging from 1-10,000cP, including water, iced tea, soap, shampoo, motor oil, surface cleaner and laundry detergents.
From Blowing to Forming
The LiquiForm filling process utilises fluid (instead of air) to expand the preform to the shape of the container mould. The entire process occurs in a fraction of a second. It’s really that simple. For our readers who are not familiar with the process, it is described in fig. 1:
WHAT ARE THE BENEFITS OF LIQUIFORM?
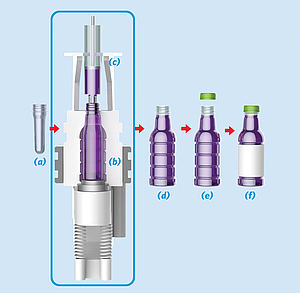
While some of the benefits are obvious, Saxena summarizes the key advantages of LiquiForm thus:
- Uniform material distribution
- Increased resin flexibility on the same platform
- Better container definition, i.e. improved ability to feature text, symbols, and texture
- Reduced energy consumption
- Reduced carbon footprint
- Improved logistics - supply chain reconfiguration possibilities
Removing high-pressure compressed air from the process is a big step and saves on equipment, maintenance and service for blow moulding equipment. It also removes the need for large compressors. This brings about significant savings in space and reduces energy consumption. Other opportunities stem from the option to eliminate multiple platforms and the resulting opportunities to reconfigure supply chains, to mention but a few of the many cost and sustainability benefits.
Wall Thickness distribution
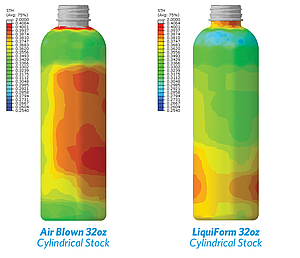
According to Saxena’s description, wall thickness distribution is improved and more consistent compared to the conventional air blow process. How? The interaction of the fluid with the preform prepares the preform in such a way that it expands in a more precise and uniform manner. Demonstrated over a variety of shapes, sizes, and materials, the preform expansion behaviour has been found to be similar. LiquiForm uses principles of fluid dynamics in the fill head technology to precisely control the fluid delivery, making it repeatable over multiple cycles and ensuring container consistency over time (fig. 2).
“Being able to control the wall thickness distribution is a major advantage point,” emphasises Saxena. “We have concrete experience in comparing containers produced using the conventional air-blow technology to those produced via LiquiForm.”
In addition to improved wall thickness distribution Saxena sees another unintended advantage: LiquiForm also increases the top-load. Why? The bottle shrinks slightly after it is capped, thereby increasing the internal pressure, resulting in an improved top-load. This certainly opens up some commercial opportunities.
Material and Shape Flexibilty
Saxena explained that one of the best examples of the flexibility and accuracy of the process, and the capabilities of this technology, is a two-stage bottle which is easily made from a HDPE preform. The challenge with HDPE has always been that the glass transition is very close to the melt temperature, leaving only a very narrow process window. This is not a problem with LiquiForm: the container is already formed before the material freezes. Another potential advantage which also shows the flexibility of the process is found with oval containers. Due to proprietary reasons, LiquiForm has only been able to form certain complex shapes on a case-by-case basis without the use of preferential heating techniques.
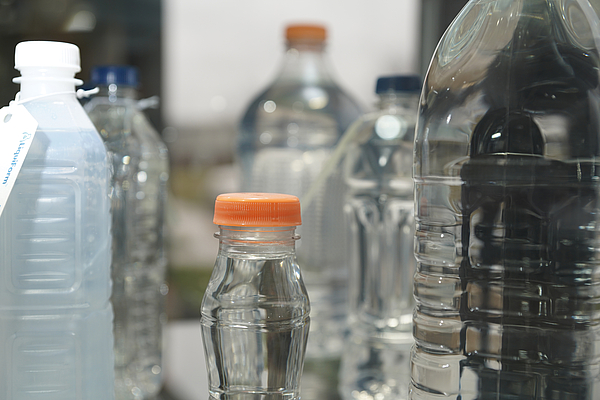
Process control & process-package interaction
A great deal of expertise has been built up over the last two years at LiquiForm. As noted above, once an optimal machine process has been identified, the repeatability is very high. Liquid filling temperatures range from10°C to 87°C. The warmer the liquid, the easier the filling and forming process, which depends on time and temperature. The cooler the liquid temperature, the more difficult it is to perform the filling and forming process. But all advantages would be irrelevant if the liquids filling the containers were harmed or altered during the LiquiForm process. A wide range of materials have already been tested after undergoing LiquiForm processing. Extensive testing for polymer breakdown, polymer migration, stability, and breakdown of the chemistry of the products by two certified, independent labs as well as some major CPG end users, has shown no evidence of degradation or contamination of the fluids compared to air blow.
What about producing a consistent headspace in the bottle? Saxena: “We have developed process capabilities to control the filling level and as a result, we have been able to ensure consistent head space that meets specifications.”
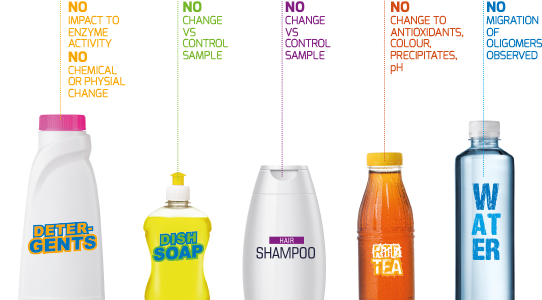
Liquiform prepared to go from lab condiitions to use in industry
According to Saxena, the benefits are manifold: The lines are getting simpler, the quality of the packages is improving and the energy consumption is reduced significantly. Speed is another substantial advantage. Lab scale outputs demonstrate a process time of 1.0s-1.3s which would translate to an output rate of about 2,500 - 3,500 bottles/h per cavity. Saxena: “We foresee challenges once we exceed 3,000 – that really is very high speed.” He continues: “Handling a filled, heavyweight bottle is a completely different story to handling an empty lightweight PET bottle. This is a key topic for commercialisation and a challenge facing our licensees. But machinery is their day-to-day business.” The LiquiForm licensees are Amcor, KHS-Corpoplast, Krones, Sidel, and Yoshino, and these top players all have their own individual plans for LiquiForm. Saxena: “We expect the first commercial application to be on the market within the next 6-12 months, then to go on to expand other applications in the following 24 months.”
What are the commercial advantages?
Lower cost, smaller, simpler and more flexible packaging lines with superior container quality and sustainability impact – says Saxena in summary, before adding concrete figures:
- energy reduction: about 50-70%
- space saving > 50%
- carbon footprint reduction: 5-10%.
“The flexibility and simplicity of Liquiform,” Saxena says, “can be used to reconfigure supply chains and move packaging closer to demand. This brings about tremendous savings in logistics costs and a considerably reduced carbon footprint.”
What are the challenges today?
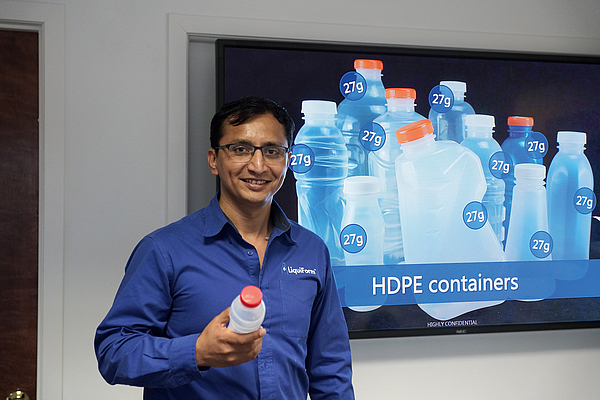
LiquiForm combines filling technology with blow-moulding technology and must therefore evolve to the realities of both. This includes handling filled containers at high speeds, cleaning considerations (CIP/COP), and the evolution of the supply chain to adapt to new manufacturing methods.
Saxena: “Fortunately, each of these challenges also presents our licensees with a wealth of opportunities, and also creates new logistical models that have the potential to yield major transportation savings. On-going work by our licensees and internal team is showing promise and new intellectual property is currently being developed. We are confident this will lead to the above challenges being addressed in the near future.”
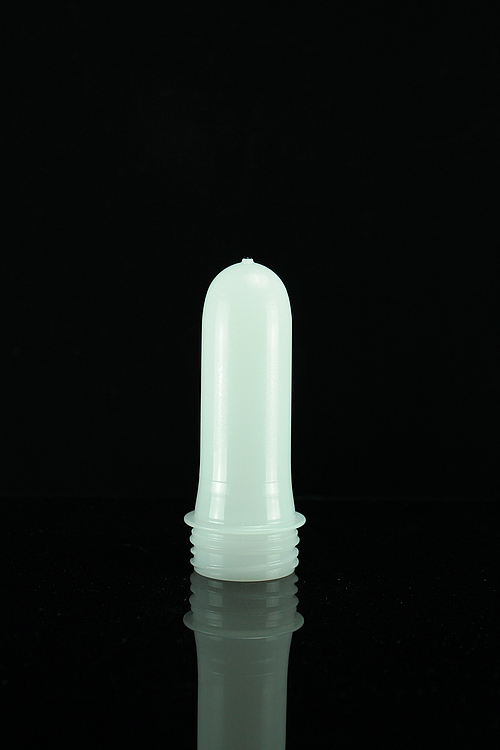
Fig. 4: HDPE preform 27g
From our point of view, the LiquiForm process is a real innovation in filling and shaping packaging containers. During our meeting, we were blown away by the impressive results of the team’s development work, and we are looking forward to hearing more about it at the upcoming PETnology Conference held in Munich in conjunction with Drinktec on 11-12 September 2017.
The comPETence center provides your organisation with a dynamic, cost effective way to promote your products and services.
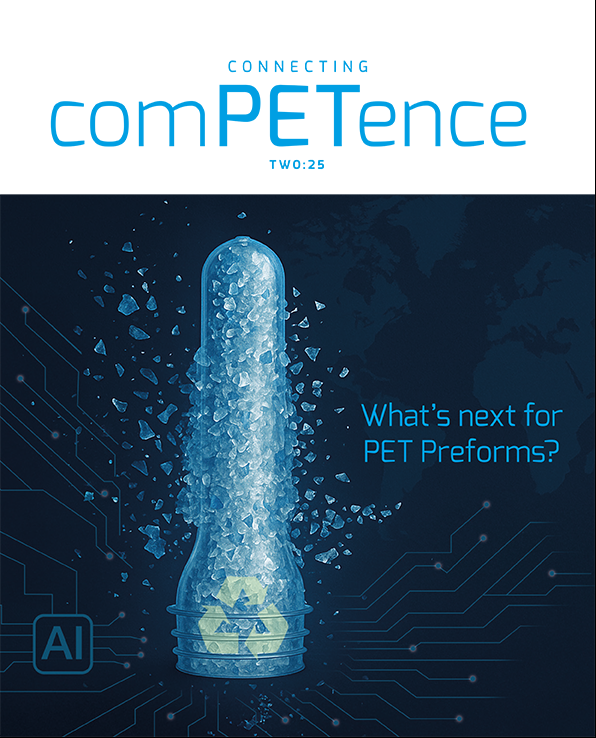
magazine
Find our premium articles, interviews, reports and more
in 3 issues in 2025.