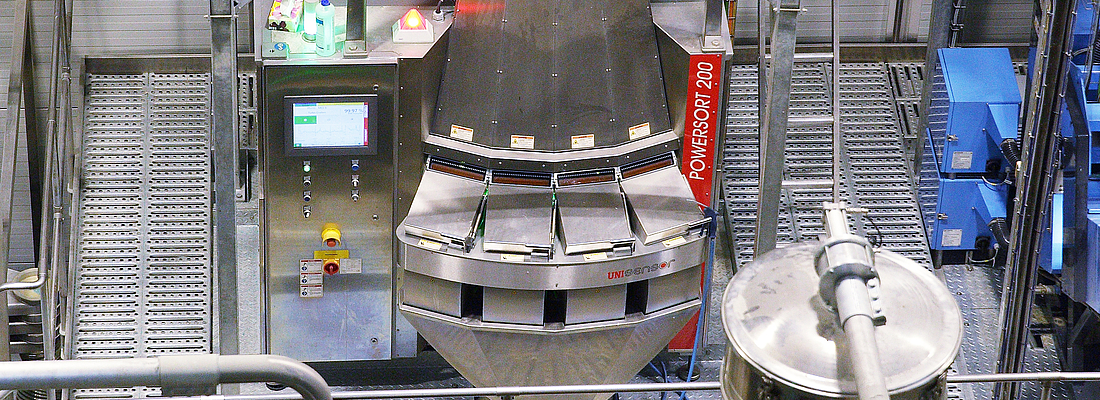
“The trend is clearly moving toward regranulate,” comments the Head of QM/QA at PET Recycling West GmbH in Übach-Palenberg. He is describing not just any regranulate, but a particular type of PET recyclable material sorted according to type and colour, which the waste processing company belonging to Mitteldeutsche Erfrischungsgetränke GmbH & Co. KG (MEG) manufactures using an elaborate process in preparation for the production of preforms. During our site visit, he and the Head of Engineering discussed the particular aspects that require monitoring and the reason for combining the “black zone” and the “white zone” at the same site.
There are many ways for a company to protect the environment. For PET bottles, reduced wall thickness has long been the recipe for resource conservation and thus environmental compatibility. While there are limits to the continuous reduction of wall thickness, it remains an important topic in the industry. Yet it is essential to find alternatives. An environmentally friendly solution that MEG developed for itself is mixing regranulate with virgin resin at a particular ratio. The company continues to use virgin resin to maintain the recyclability of its materials. This proprietary solution is sustainable and future-oriented, and very sophisticated. It comprises all steps from collection to delivery of filled bottles to the discounter. At five locations in Germany, MEG fills 0.5 litre and 1.5 litre bottles with mineral water and other soft drinks for various branded companies, and is recognized as one of the largest beverage producers in Europe. In light of this reputation, the bottling company attaches a great deal of importance to its on-site recycling. MEG was already operating a PET recycling site in Saxony when they decided to build a second facility in Übach-Palenberg. Construction of PET Recycling West GmbH began in 2015, and just one year later, the facility was up and running. For MEG, the new production site meant logistical advantages, an increase in production capacity for regranulate, and the ability not only to maintain the proportion of recyclable materials during bottle production, but to increase it, along with the guarantee of a higher quality product. This was a key piece in the puzzle of demand for quality and recycling.
The high quality materials produced at the bottle-to-bottle recycling facility in Übach-Palenberg are mainly due to the systems technology used. The recycler optedforawashingstationfromKrones AG, integrated at their request with Powersort, the high-capacity sorting facility from Unisensor Sensorsysteme GmbH in Karlsruhe. “We chose the system from Unisensor very deliberately because we were already familiar with it. In our eyes it is the best system in the market for re-sorting foreign plastic materials,” says theHead of Engineering. PET bottles are the feedstock material for the recycling process.
They are delivered as bale and then stored in a hall. The Head of Engineering emphasises the company’s commitment to the environment: “It is very important to us that the storage location for our input material is covered, so that no scraps from the paper labels escape into the surrounding environment.”From the very start of processing the bale goods, the colour purity is monitored; clear and coloured bales are therefore processed separately. First of all, PET regrind is produced via metal separation, wet-shredding and swim-sink separation. And not only does the entire washing station operate efficiently, it is also environmentally friendly. A microfiltration system repeatedly processes the caustic solution in the first washing stage and ensures a closed circulation sytem. PET Recycling West requires fresh water only for post- washing. A single treatment plant for the accumulated wastewater operates roughly 3 km away, connected to the production site by a vacuum sewer line.
Following mechanical dehumidification, the regrind is either bagged up and delivered to the affiliate, or reprocessed in-house. The two greens tones “Grafton green” and “border green” are reprocessed on-site; blue tones are processed at the sister site. The coloured regrind passes through two sorting stages: Sorting by colour takes place on Bühler equipment, which works by detecting near-infrared waves; the Powersort equipment from Unisensor separates foreign and contaminant materials. “Our sorting unit works with laser spectroscopy,” explains Jan Meyer, Sales Manager for Powersort at Unisensor, specifying the functional principle: “Every material has a specific molecular fingerprint. Very high intensity laser beams excite the material to fluorescence, which is recorded and analysed.” This occurs in a very short time – up to 1 million spectra are recorded and analysed each second. The material falls through a funnel into the sorting unit and is distributed from here via several chutes. The particle matter falls through the laser scanner level onto the chutes and is either passed through as good material, or blown away with the help of compressed air jets. “With this, our customers receive PET flakes of up to 99.99% purity,” stresses Jan Meyer. Foreign plastic particles such as PC, PVC and silicon waste are culled out.
After the separation stage, the flakes leave the production operation’s “black” zone and proceed into the regranulation line in the “white” zone. The entire plant is comprised of a pre- flushing unit, an extruder with melt filter and an underwater pelletizer as well as a secondary reactor. Solid- state polycondensation (SSP) takes place in order to increase the IV value of the input material. The regranulate is temporarily stored and combined with virgin resin before it is processed into preforms by the in-house injection moulding department in preparation for bottle production. “It is really amazing that we have combined the black and white production areas here on site,” explains the director of Engineering, “it provides us several advantages.” One advantage is definitely logisticalas the supplied residual materials are not only processed, but also reprocessed on site. The preforms can be delivered directly to the nearby bottling facilities. And with this, PET Recycling West pursues its goals of resource conservation and environmental protection. “The key advantage is, however, that we control the entire production process, which allows us to ensure that our regrind, regranulate and preforms are of high quality,” summarises the Head of QM/ QA.
The comPETence center provides your organisation with a dynamic, cost effective way to promote your products and services.
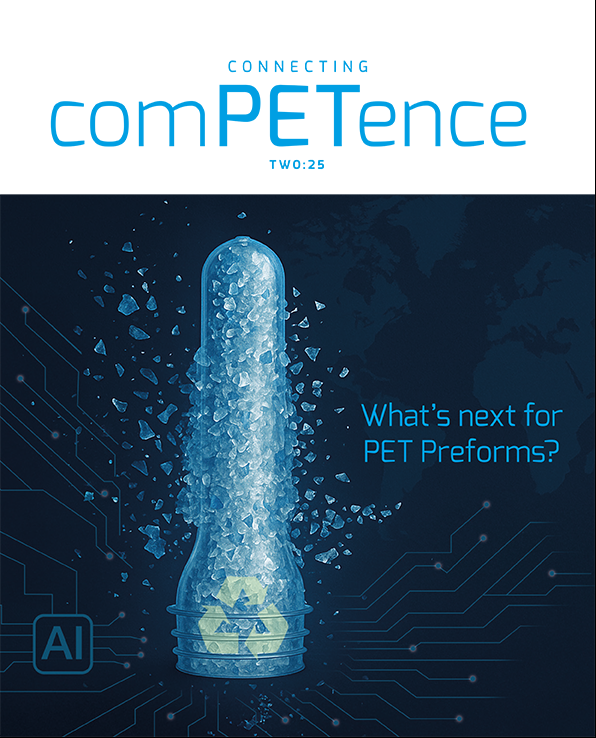
magazine
Find our premium articles, interviews, reports and more
in 3 issues in 2025.