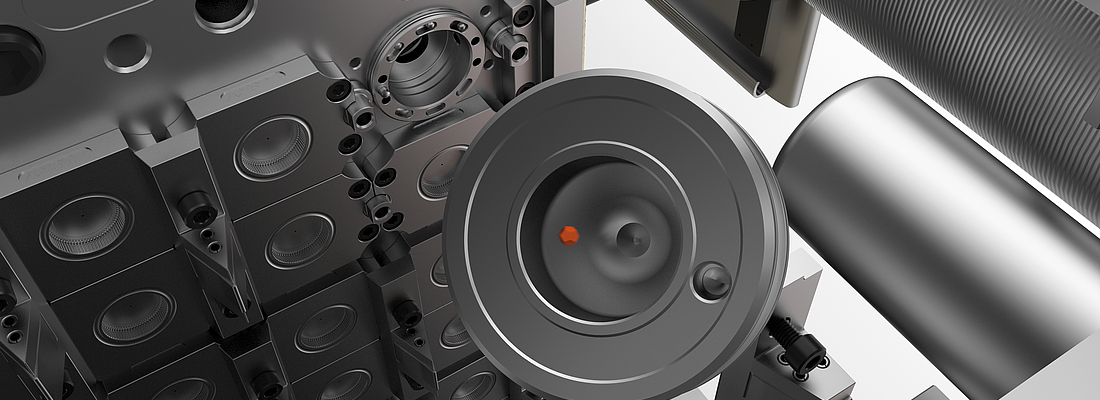
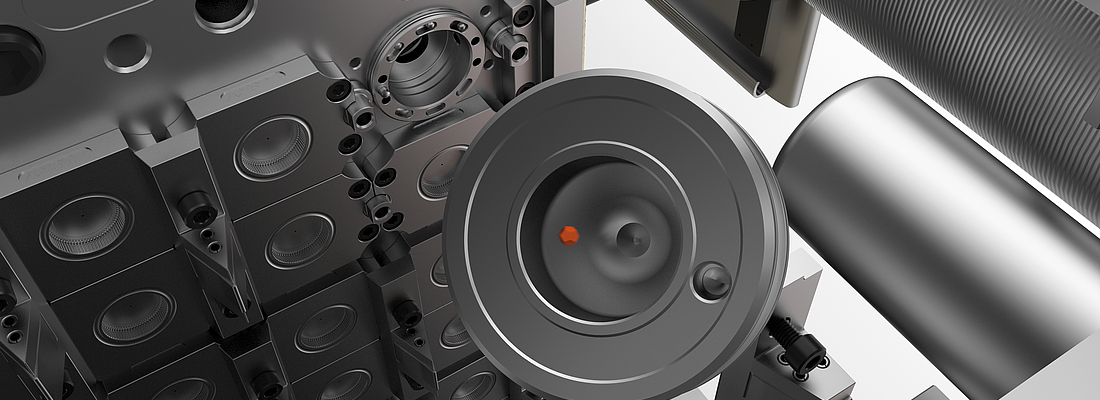
Reducing the maintance requirements for injection molding tools
Innovative tooling technologies decrease maintenance time while improving uptime
Blocked cavities result in significant downtime and lost productivity
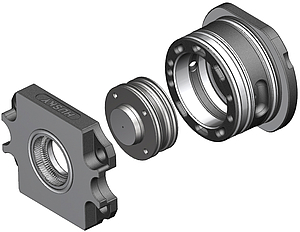
Injection molders often suffer from the after effects of raw material that is contaminated with substances of a higher melting temperature than the plastic being molded. Such particles are the most common cause for clogged cavities in molds with thermal gates. Debris that blocks the gate holes is typically small bits of packaging or wrapping used for resin transportation and storage (e.g. wood, paper or cardboard). Equipment to convey the resin between a warehouse and the molding machine exposes the resin to various sources of metal, stones and cross-contamination with dissimilar resins. Even uncooked rice can be found with plastic resin in some regions of the world. Most of the small, un-meltable fragments pass through the machine extruder and the hot runner towards the mold.
The gate hole is the narrowest point in the flow path of the melt towards the molding cavity. Consequently, most particles collect between the nozzle tip and gate, which is commonly referred to as the gate bubble. The cleaning procedure can be a laborious task, especially on a high-cavitation production system, because of the number of interfaces that need to be disconnected until the gate bubble can be reached. The affected positions usually require a cleaning of the gate holes from the direction of the melt flow. Traditionally, the hot runner must be significantly cooled down before any disassembly can begin. Cool down of the hot runner is necessary in order to prevent scoring of the delicate sealing surface between the hot runner nozzles and the cavities. Once the hot runner has been cooled, the cavity plate is removed from the hot runner to gain access to the gate and remove the particles clogging the gate. All mounting bolts that secure the cavity plate to the hot runner need to be unfastened and all hot runner nozzles need to cool down to the ambient temperature in order to prevent damage to the individual sealing surfaces.
Removing gate blockages is a laborious process. Many operators shut down the blocked cavity/cavities by turning off the individual nozzle heat zone(s) and continue production with fewer cavities active. This procedure is repeated until the productivity of the molding system is reduced to an unacceptable level. A perceptible impact of shutting down a number of positions on a high-cavitation mold is lost productivity. However, the quality for the remaining cavities is also affected due to unequal melt balancing, cold resin in the melt channels, and the required adjustments of the processing parameters such as shot size, injection and hold pressure.
Paradigm shift
A comprehensive Voice of Customer analysis indicated that unplanned downtime due to blocked cavities was a widespread pain point. Blocked cavities seemed to afflict molders globally regardless of molding skill level and existing resin handling practices. Listening to the expressed needs of the operators at the plant floor level, Husky developed and designed our unique Front Mounted Cavities™ (FMC) for closure molds. This patent-pending design allows for individual mold cavities and gate inserts to be mounted to the front of the cavity plate. This design change introduces a significant paradigm shift in how operators approach the issue of blocked cavities during daily production. Now, all critical areas of a single nozzle location are accessible with a few small-scale screw turns. There is no longer any need to uninstall or latch-over the complete cavity plate, and disengage all nozzles to clean a single position. No more accumulated shut down of cavities because of blocked gates and permanent process adjustments to the remaining positions; no extensive cool down and heat up period for all nozzles, which carries the risk of damaging the nozzle-seal interface. With Front Mounted Cavities, the operator only needs to act where the issue occurs and can return the system back to production faster than ever before.
With this re-design of the cavity plate, Husky has introduced an all-new concept for closure molds. The approach of individually replaceable cavities is well-known in the industry from nearly two decades of PET molds from Husky. The design allows for conformal flow of cooling water in close proximity to the molding surface; right where it’s needed, with the exact amount required. All nozzle seals remain engaged during service, eliminating the risk of seal damage and presenting a significant decrease in nozzle cool down times. Additionally, the hot runner can remain in stand-by mode, thereby minimizing the amount of time required to get back to operating temperature.
The time savings that FMC offers over the conventional tooling design is significant. The actual time savings realized depends upon a variety of factors, including but not limited to: tooling cavitation, the number of blocked gates, the number of blocked cavities allowed prior to shutting down to remove the blockage, and the proficiency of the operator(s) performing the work. Taking the above factors into consideration, the FMC design offers cavity unblocking time savings between 70-80% versus a conventional mold design.
Available as part of our recently-introduced HyCAP™4 beverage closure manufacturing system, the Front Mounted Cavities solution is designed for injection molding customers who experience blocked gates due to contamination in the resin and who are looking for the ability to clean the affected position, quickly and easily. Producers who process recycled material, factory re-grind or cross-contaminated virgin resin, or those who don’t want a pricey ultra-fine-grid filter unit on every molding machine should consider the new Husky Front Mounted Cavities design. Operators who have to turn around a logo change without a crane or heavy tools will appreciate the ability to simply swap the inserts from the front of the mold.
All advanced features of the Front Mounted Cavities are incorporated into a single cavity plate that is compatible with all existing Husky 3.0 Closure Molds and Hot Runners.
Key Features:
Productivity:
- Industry-leading cycle times with conformal cavity cooling
- No shut down of individual blocked cavities
Ease of Maintenance:
- Individually removable cavities without the need to un-install the entire cavity plate
- Faster turnover of maintenance tasks with all nozzle seals permanently engaged
Closure Logo Change:
- Gate insert removal and installation while the cavity plate is engaged to the hot runner
Compatibility:
- Full compatibility with all Husky HyCAP 3.0 Molds
The comPETence center provides your organisation with a dynamic, cost effective way to promote your products and services.
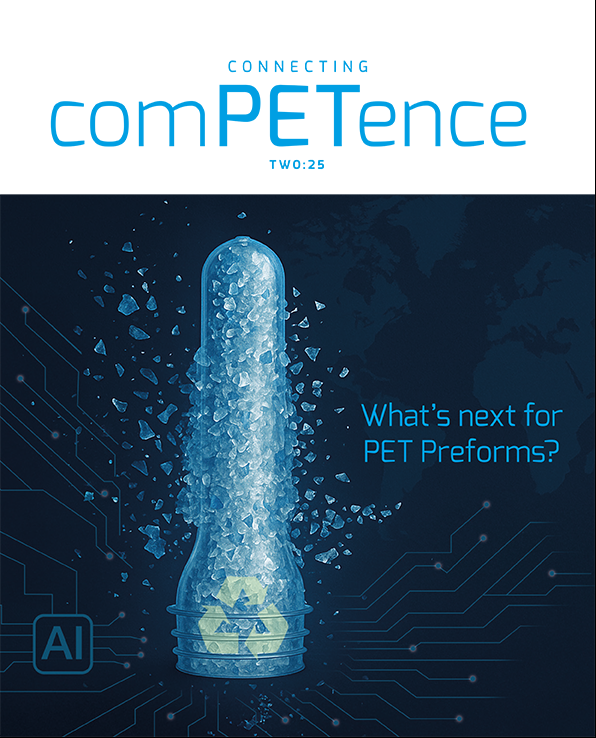
magazine
Find our premium articles, interviews, reports and more
in 3 issues in 2025.