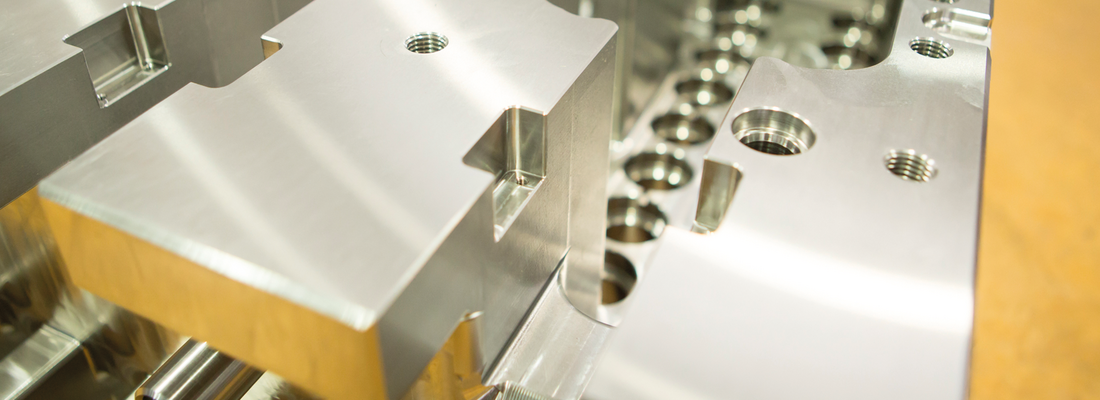
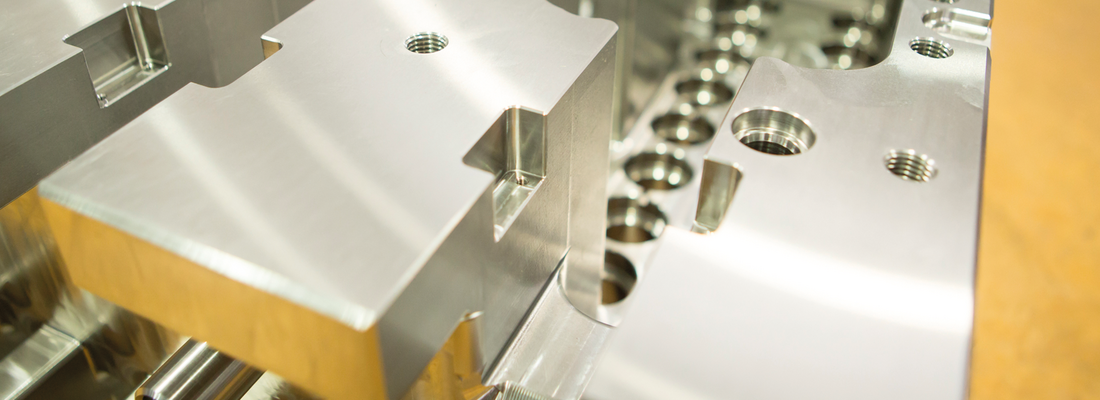
(Source: thyssenkrupp Materials Schweiz AG)
PLASTIC MOULD STEEL
Innovative surface technologies - The all-stainless concept for maximum performance in tool and mould manufacturing
The requirements for high-performance tool when processing plastics are constantly increasing. An effective material concept that combines steels with outstanding corrosion resistance, durability, hardness, and machining properties can significantly improve the efficiency of the entire plastics production process. The all-stainless concept provides a solution to these increasing challenges.
Improved plastic mould steels
Modern plastic mould steels, such as THYROPLAST 1.2294 and THYROHARDXtra, are specifically designed for longterm use. They offer an exceptional combination of properties that are perfectly tailored to the challenging requirements of plastic injection moulding:
- Corrosion resistance: protection against the effects of moisture and chemicals
- Hardness: High levels of hardness up to 60 HRC, ensure longer mould life
- High durability: High durability even when exposed to extreme operating conditions
- Hardness: High hardness of up to 60 HRC, ensuring extended mould life
- Machining: Good machining properties, even with a high level of hardness
Performance and availability
Mould manufacturers frequently guarantee injection numbers of 7-10 million and operating times of 2-3 years. From a practical point of view, this means that the moulds must provide extremely high reliability. This is particularly important in the fields of medical technology and food packaging, where the highest standards of hygiene and material resistance are required, the steels of the all-stainless concept have a significant impact.
Corrosion resistance is the solution
In view of the high performance parameters, an “all-stainless” concept always pays off throughout the mould and eliminates unexpected failures due to corrosion. At the same time, it is important that the entire mould is designed for corrosion resistance, otherwise individual components will develop rust particles during production and contaminate the entire mould.
Corrosion is the reaction of a metallic material with its environment, resulting in permanent damage and degradation of the material’s function.
Corrosion phenomena can be seen as cracks, holes, pits or flat wall thickness reductions on the material and it is still one of the biggest challenges to mould life and productivity.
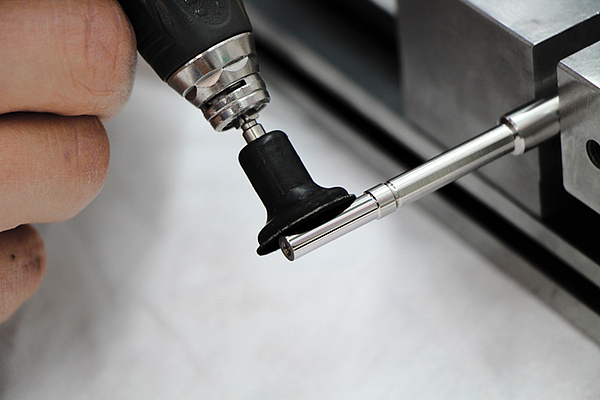
Production volume and cycle times
The cost-effectiveness of a mould is significantly impacted by the production output and cycle times. High-quality plastic mould steels permit shorter cycle times and therefore an increase in the production rate. The increase in efficiency resulting from the use of highperformance materials considerably reduces costs in terms of parts.
Innovative surface technologies
High-gloss polished surfaces are a must for transparent plastics. The nitrogenalloyed steel THYROHARD-Xtra is ideal for polishing and laser texturing work thanks to its homogeneous and fine carbide microstructure. This homogenous and fine carbide structure ensures a high-quality surface, which is required for applications with demanding visual requirements.
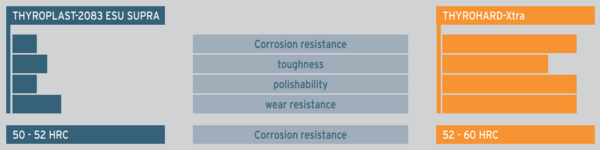
Polishing trial and laser machining
As a comprehensive service provider for tool and mould manufacturing, Reichle Technologiezentrum GmbH is always looking out for new materials that are efficient in machining and can achieve excellent results. The opportunity to process the new THYROHARD-Xtra mould insert steel in a joint project with thyssenkrupp Materials Schweiz AG was therefore a great opportunity for Reichle to not only conduct large-scale polishing tests but also to evaluate its latest Femto- laser technology.
High-gloss surfaces require extremely fine preprocessing, which can involve a great deal of polishing depending on the hardness of the material. The nitrogen-alloyed, corrosion-resistant, and martensitic steel THYROHARD-Xtra is ideal for polishing and laser texturing work thanks to its homogeneous and very fine carbide microstructure. Reichle was able to evaluate the steel’s polishing properties on a total of three parts - two valve gates and a round disc with a hardness of 60 HRC.
Polishing trials on two valve gates and one round disc manufactured using THYROHARD-Xtra
On the valve gates, the round ground surface was pre-polished with Ra 0.13 µm crosswise to the grinding direction and alternately crosswise with oilstones and paper up to 1200 grit and finally highly polished with diamond pastes and polishing fleece up to N1 - Ra 0.015 µm in the demoulding direction.
The round sample was mechanically flat-lapped and delivered to Reichle by thyssenkrupp Materials Switzerland. The surface was refined by means of further lapping with oil stones and polishing lapping with hardwood and finally highly polished to N1 with a very fine fleece. The 60 HRC and the fine structure of the THYROHARD-Xtra were crucial for a perfect result. The sample could be processed without any problems within an hour. Despite its toughness and high hardness, THYROHARD-Xtra was very easy to polish in all three cases thanks to its extremely fine carbide matrix. The efficient processing resulted in an extremely homogeneous high-gloss polish with outstanding brilliance.
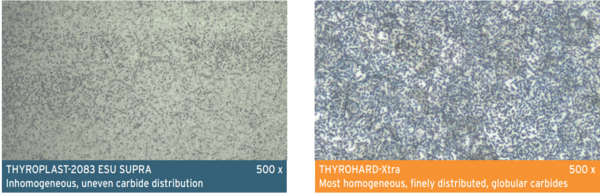
Femtolaser processing
With almost 20 high-precision 5-axis laser systems, the Reichle Technologiezentrum is not only a pioneer in polishing but also in laser texturing across Europe. As a result, the round sample of the THYROHARD-Xtra was additionally processed with the brand new femtolaser machine from the manufacturer GF Machining Solutions after high-gloss polishing. With this special femtolaser processing (ultra-short pulse), highly complex design and functional geometries can be achieved with the finest possible surface finish. This technology is particularly beneficial in the pharmaceutical and medical sectors, as special surfaces are anti-bacterial thanks to special structures. After processing the round sample, the geometry depth was about. 2 mm, the surface roughness was about Ra 0.1 and the edge and corner radii were reduced to a minimum of about 0.01 - 0.02 mm. Thanks to the ultra-short pulse, this special technology also produces no burrs. To create maximum contrasts between brilliant high-gloss and matt surfaces, femtolaser processing can produce ultra-matt surfaces with virtually no light reflection.

High-quality steel qualities are crucial for the processing of femtolasers, in particular a fine carbide structure such as THYROHARD-Xtra. This ensures that laser ablation can be highly detailed and precise.
After high-gloss polishing of the three parts and subsequent femtolaser processing of the round sample by Reichle Technologiezentrum GmbH, a detailed evaluation of the THYROHARD-Xtra can be made in terms of its polishability and suitability for laser texturing. The combination of such a robust and wear-resistant steel with the almost infinite design freedom of laser processing enables solutions for a wide range of special applications and therefore has extraordinary potential for many different branches, such as the medical industry, the plastic injection moulding industry, etc.
Conclusion
The all-stainless concept offers an innovative solution to the high demands of tool and mould making. The use of optimised plastic mould steels such as THYROPLAST 1.2294 and THYROHARD-Xtra can significantly increase the efficiency, durability and cost effectiveness of plastics processing. Excellent corrosion resistance and the ability to achieve precise surface finishes make these materials the perfect choice for high performance applications in medical, food packaging and other demanding industries. In all cases, this means less production downtime and lower maintenance costs for the entire mould.
The comPETence center provides your organisation with a dynamic, cost effective way to promote your products and services.
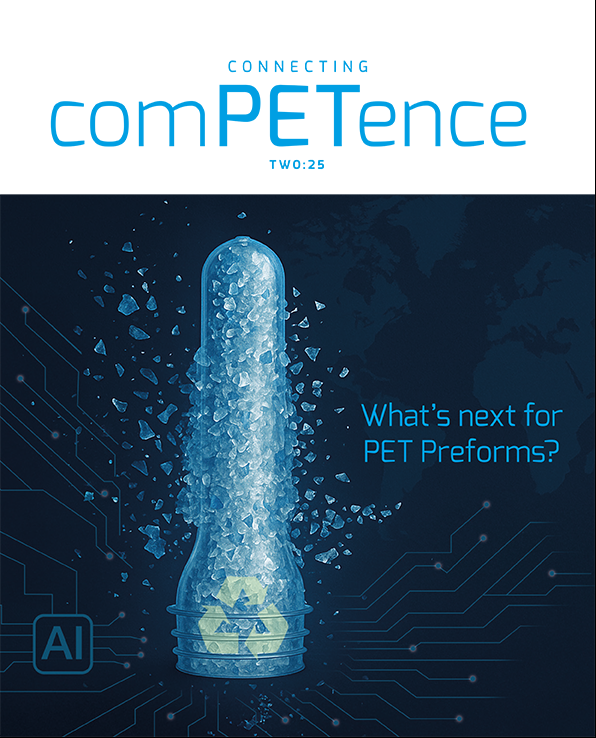
magazine
Find our premium articles, interviews, reports and more
in 3 issues in 2025.