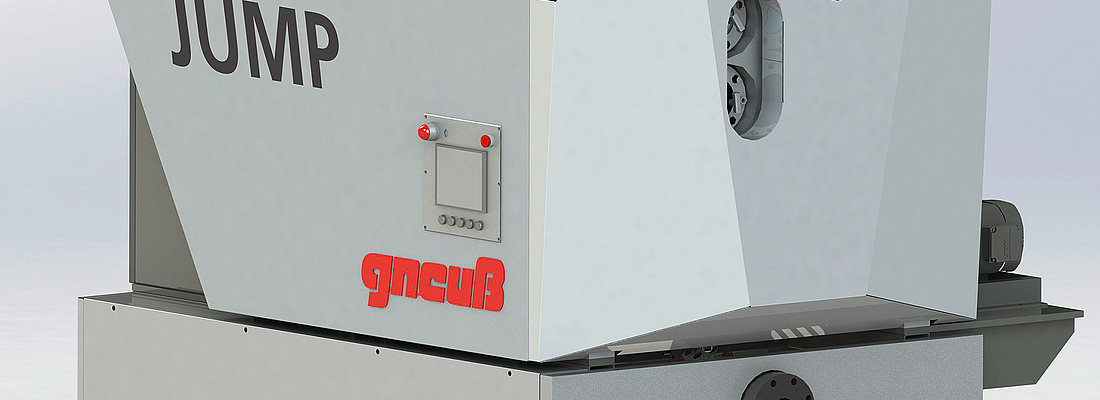
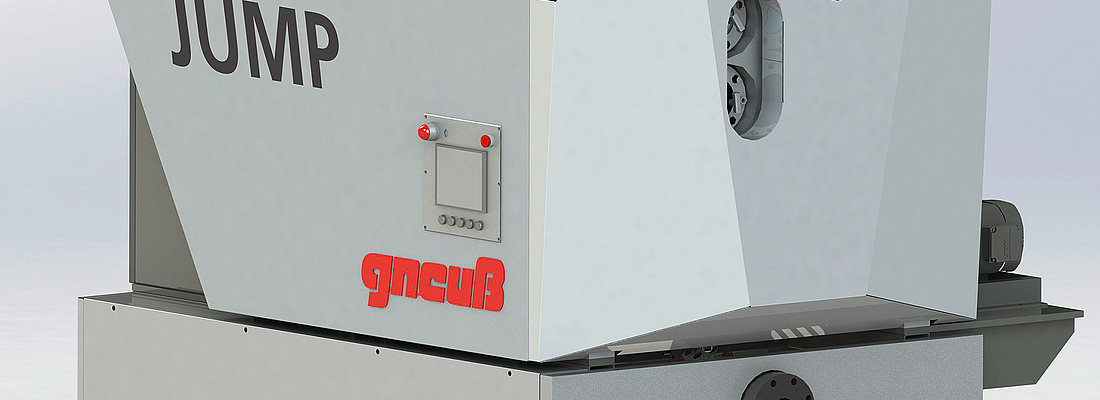
At the K trade fair in Düsseldorf, three companies presented an alternative to SSP: a continuously operating reactor for the post-treatment of PET recyclable materials. The plant engineering company Aquafil Engineering GmbH from Berlin, Germany has named their reactor EverPET IV Lift, Gneuss Kunststofftechnik GmbH, Bad Oeynhausen, Germany now features JUMP in its product portfolio, and Next Generation Recyclingmaschinen GmbH based in Feldkirchen an der Donau, Austria calls their system P:REACT. Whereas the reactor designs, examined in greater detail below, vary slightly, they all fulfil the same purpose. In order be able to use recycled materials in more high-value applications, the IV value of PET waste materials from fibre, film or bottle production, as well as from post-consumer material must be increased in a targeted manner.
Despite of the fact that PET virgin resin is not much more expensive than recyclable materials at the moment due to excess capacity installed around the globe, the demand for regranulates remains high. This is down to our ecological conscience, the corresponding legislation, and also positive connotations in marketing arguments. This has led us to the point where a good 50% of all bottles, or 1.8 million metric tons, are collected and processed across Europe today. (Source: Petcore). At around 98%, the recycling quota of PET bottles in Germany is extremely high, particularly as a result of the single-use bottle deposit system. More than a third of bottles collected are reused in bottle manufacturing (Source: Forum PET). But in addition to post-consumer bottles, industrial waste from fibre, film and bottle manufacturing is also suitable for the production of high-grade regranulate – and is used for this purpose. The global PET consumption for products from the packaging industry, such as bottles and trays, amounts to a total of over 20 million metric tons, and this figure is approximately twice as high in the fibre industry. Consequently, large amounts of material are available for sensible recycling processes.
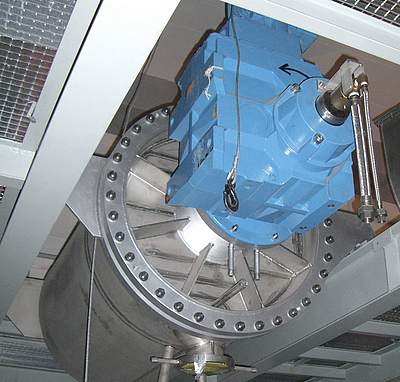
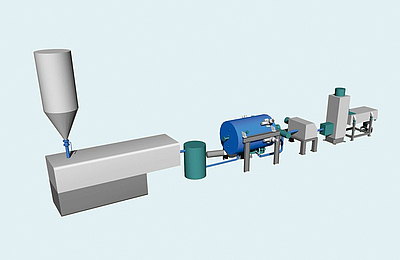
1.EverPET Aquafil Engineering
Polycondensation polymer polyethylene terephthalate reacts to heat, mechanical stress and moisture by breaking down the polymer chain length and thus decreasing the viscosity. Systems which counteract this process are therefore essential for the production of regranulate. Twin-screw or other multi-shaft extruders, which ensure gentle processing, are commonly used for processing PET residual materials. They are also equipped with degassing devices for removing moisture and volatile constituents. After being processed in the extruder, the manufactured regranulate then often undergoes post-condensation in a solid-state polycondensation (SSP) reactor, so that high IV values can be attained.
At the plastics trade fair, the companies presented their continuously operating reactors as an alternative to familiar methods.
The JUMP solution offered by Gneuss enables viscosity to be increased by between 0.2 and 0.3 dl/g when used in combination with the specially developed Multi Rotation System (MRS) extruder. The machinery manufacturer highlights the compact design of the JUMP as a particular advantage, as it only requires a small floorprint and stands at just 2.5 metres tall. The inner workings of the reactor are constructed such that they are easily accessible and therefore easy to clean. The process takes places as follows: The PET melt, removed of most of the volatile constituents by a simple 25 mbar vacuum in the MRS, reaches the JUMP and passes through several slowly rotating, mixing elements, forming a polymer film whose surface is constantly being renewed. The reactor is under a vacuum which ensures that glycol and other volatile constituents are safely removed. Surface exchange and also dwell times can be varied widely, so that dwell times of between 5 and 100 minutes can be achieved. According to Gneuss, one of the advantages of the end product is that the lack of oxygen intake during processing prevents to the greatest possible extent the yellowing of the materials.
The so-called liquid-state polymerisation (LSP) process from NGR utilizes a pre-treated PET melt, which in this case comes from a shredder-feeder-extruder combination. As an example, the company explains the processing phase in the P:REACT reactor for residual materials from the fibre industry, which have an initial IV value of 0.56 dl/g and, in addition to a moisture content of 3,600 ppm, may also contain up to 15% spin oils: After the first processing stage in the shredder-feeder combination, which already includes one degassing process, the IV value increases to 0.66 dl/g ± 0.015 dl/g and the spin oils have been safely removed. Then, the temperature in the reactor is maintained at a consistent level and a second degassing process takes place. The IV value, which is measured online, can be adjusted during the dwell time. The end product after granulation is an rPET granulate with an IV value of 0.7 g/dl. The builder of recycling systems views the low energy consumption of 0.12 kwh/kg including granulation and the simplicity of the process to be particular advantages of the system. Furthermore, the IV value fluctuations, which are well-known in discontinuous processes, are significantly smaller. Thanks to FDA approval, rPET granules manufactured in this way could even be reused in contact with food products.
Better known from plant engineering for their specially developed large polyester polycondensation systems, Aquafil Engineering now offers EverPET, a complete system for processing recyclable materials. This system also consists, for example, of a cutter compactor, an extruder, the EverPET IV Lift continuous reactor and an optional granulation unit. As, according to Aquafil Engineering, it does not always make sense to granulate the processed melt, the melt could also be put directly back into the production process, for example, for fibre manufacturing. Among the advantages of their complete system with reactor, Aquafil Engineering lists operating principles which which are gentler on materials than conventional extrusion systems, along with reduced yellowing and gelling.
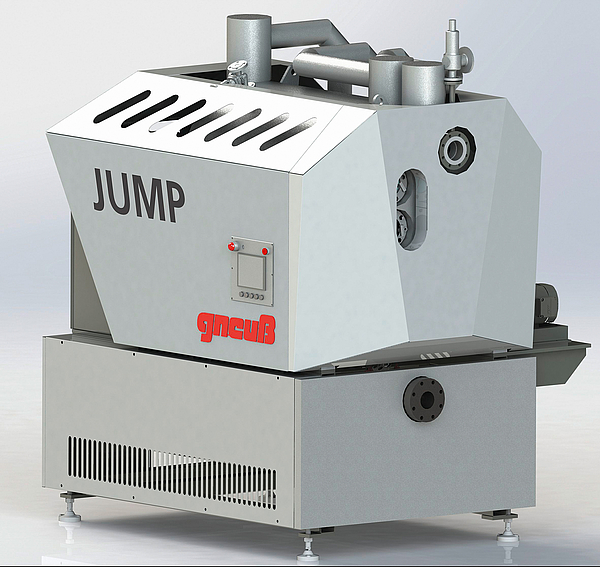
2.JUMP
Gneuss Kunststofftechnik
Aquafil Engineering offers recycling systems for flow rates of 200 to 2,000 kg/h, in which the IV value can be precisely adjusted and increased up to 0.4 dl/g. The plant engineering company even reported that it was able to produce an end product with an IV value of 1.0 dl/g in one IV Lift reactor which had been put into operation. Alongside the main function – IV value adjustment – the reactor also takes care of homogenisation and further degassing of the material, which has a beneficial effect on quality.
The three variations on the process therefore serve to increase and adjust the IV value using using fast and energy efficient methods which are also gentle on materials. Thus reactors represent an attractive alternative to the discontinuous processes used up till now, and offer waste processers an ideal opportunity to attain a higher added-value with regranulates. Which design is the most suitable for each individual set of circumstances, can only be determined on a case-by-case basis through individual discussions.
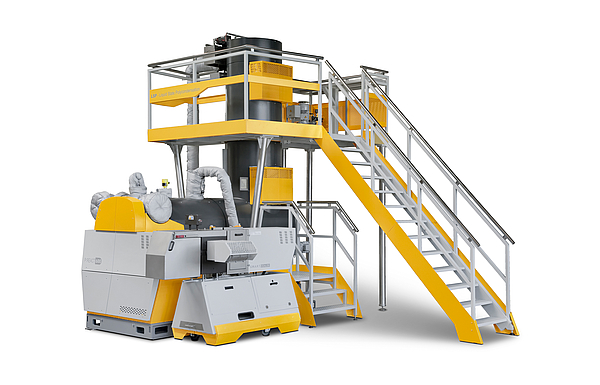
3.P:REACT
Next Generation Recyclingmaschinen
The comPETence center provides your organisation with a dynamic, cost effective way to promote your products and services.
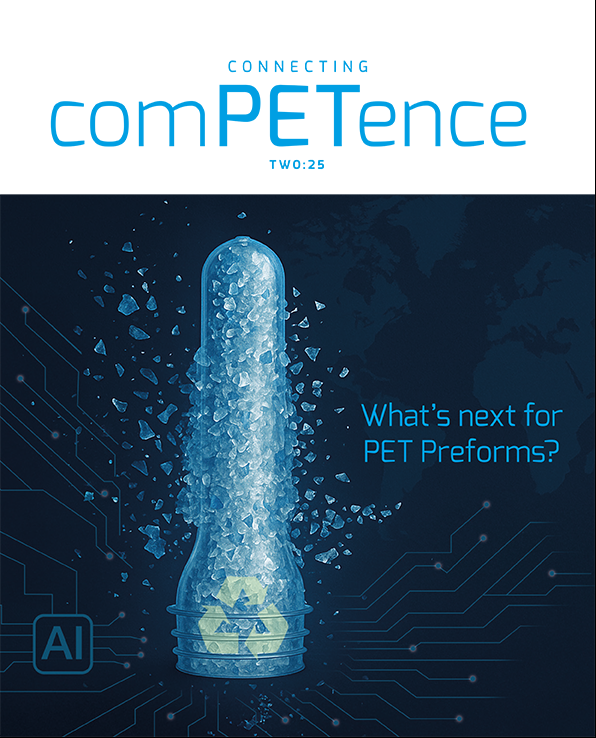
magazine
Find our premium articles, interviews, reports and more
in 3 issues in 2025.