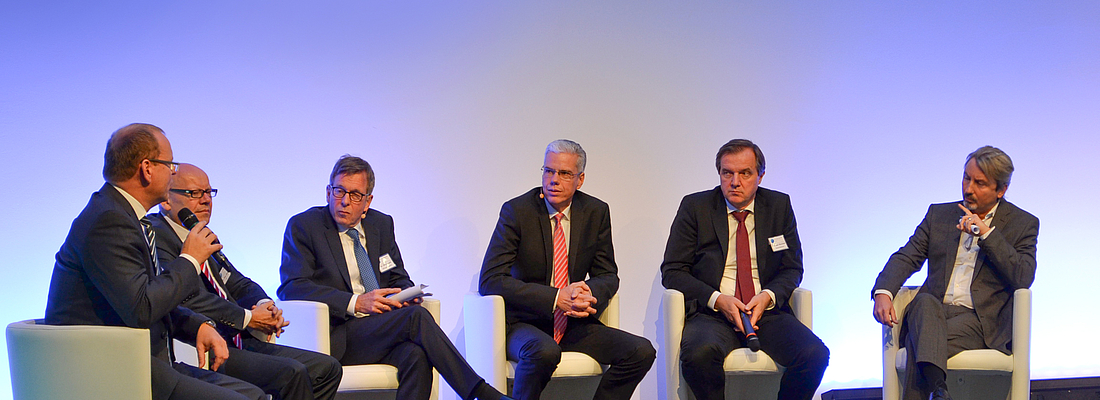
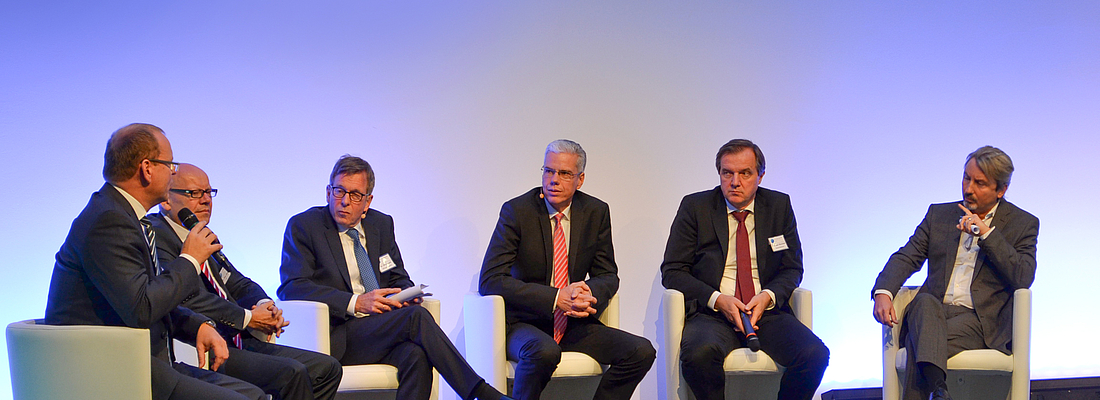
Increasing digitisation is offering companies in the PET industry a wealth of opportunities, yet developments are still in an early stage
“When we reach the limits of our understanding – that’s the point when it will get really exciting”
The fourth industrial revolution, Industry 4.0, digitisation or the Industrial Internet of Things (IIOT) – regardless which name you want to use, they all refer to the same concept – the increasing digitisation of previously analogue technologies and the integration of cyber-physical systems.
Digitisation is a hot topic and subsequently, what everyone is talking about. For this reason, we busied ourselves with the topic in our magazines, during the PETnology Conference 2015 and we even made digitisation the subject of the panel discussion on the first day of the PETnology europe conference 20016 in Nürnberg.
To summarize: companies cannot afford to, nor want to close themselves off from new technology, but what exactly this means, looks different for each company at this point in time. Every company is at a different stage of implementation and there is variation in breadth and depth of implementation. We spoke to some of the experts in the PET industry about Industry 4.0 and will highlight some of the various aspects discussed below.
The Fourth Industrial Revolution
First of all, a few general words on the terms used: Just as the first, second and third industrial revolutions were sparked by technical innovation – the industrialisation around 1800 resulting from the development of the steam engine, the conveyor belt and piece work; the beginnings of automation due to the introduction of electricity towards the end of the 19th century, and the introduction of computers which lead to the electronic revolution in the 1970s – the fourth industrial revolution, which we are talking about today, will be sparked by the internet. “The physical world which surrounds us is becoming ever more closely connected to the virtual world. The ‘Internet of Things’ allows us to have one foot in the real world and one foot in the virtual world at the same time. Products, environments and events will be experienced as well as influenced both virtually and physically simultaneously, in different ways”, saysProf. August-Wilhelm Scheer in the foreword to his e-book “Industry 4.0 – What will production processes look like in 2020?”. It is important to note that Industry 4.0 is not an established standard which has been set in stone, but is more of a project for the future. The German Federal Ministry of Education and Research (BMBF) set Industry 4.0 in motion and comments: “Industry 4.0 aims to put German industry in a position where it is well-equipped for the future of production. It is distinguished by a strong individualisation of products in the midst of the conditions set out for highly flexible (large-scale) production. Customers and business partners are directly involved in business and value creation processes. Production is being coupled with high-quality services. And the use of intelligent monitoring and decision-making processes will enable companies and entire value added networks to be controlled and optimised in near real-time. German industry now has the opportunity to actively participate in shaping the fourth industrial revolution. This opens up unprecedented business models and vast potential for optimisation in production and logistics.”
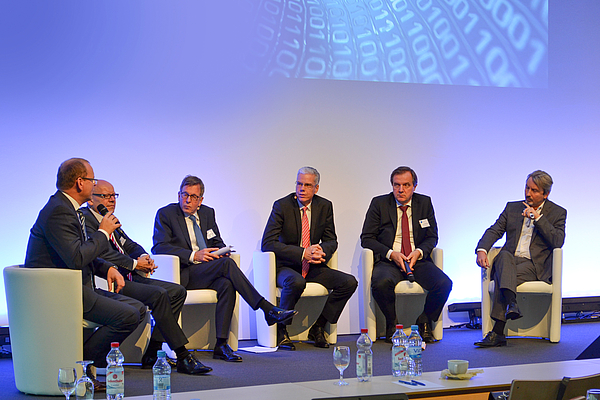
New business models and individualisation
This opening up of “unprecedented business models and vast potential for optimisation in production and logistics” is one aspect of the increasing digitisation which has provoked great interest from all the companies in the value-added chain of the PET industry. Christoph Klenk, CEO of Krones AG, Neutraubling, Germany is convinced that “Business models will undergo considerable change in the coming years” and presents an example of how consumer behaviour is changing: “In the USA, customers already do their shopping over the internet and then go to the supermarket just to collect the goods.” At the same time, customer requirements are becoming increasingly individual, and lot size 1 is an issue which is constantly growing in importance. Digital printing has been around for a good two years now. At the touch of a button, motifs viewed on or created on computers are printed on bottles – and if you want, only on a single bottle. “We can print onto 36,000 bottles per hour, and in extreme cases, each bottle can be printed individually as all the printing stations are equipped with their own minicomputer”, explains the Chairman of the Executive Management Board of KHS GmbH, Dortmund, Prof. Matthias Niemeyer, during a press conference at the BrauBeviale. An example of a “strong individualisation of products in the midst of the conditions set out for highly flexible (large-scale) production“, says Karsten Vollmer, Head of Innovation Management at the filling line manufacturer KHS: “Nowadays, individuality is very important for our customers. Oettinger has 28 different types of beer on the market, for example. The company therefore needs a solution which enables it to fill, label and pack the required type of beer in the desired quantity – which is no problem if you have a suitable programme.”
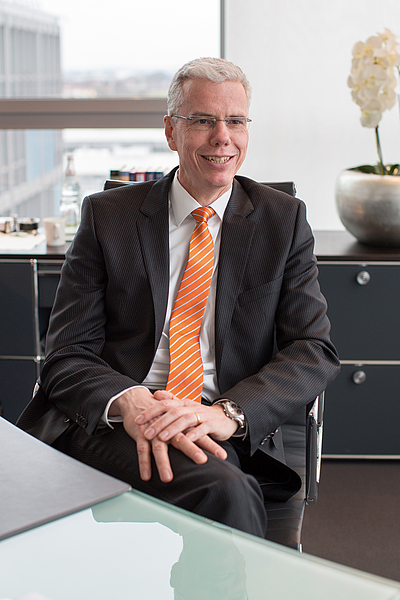
Christoph Klenk
Potential for optimisation in production could arise from the ability of individual systems to provide information which triggers an action: “Production is becoming coupled with high-quality services.” Dr Gerd Fuhrmann, the Managing Director of Intravis GmbH in Aachen illustrates this point with an example: “If the material stock in the silo of a plastic processor begins to run low, the logistics company is automatically informed, and a truck is then automatically sent – and all of this happens without the need for operator intervention.” Digitisation also offers potential for optimisation in the organisation of a company. “We have digitised our entire Human Resources department”, says German Reichert, the Chief Executive Officer of Hansa-Heemann AG in Rellingen. In his company, for example, job applications are received digitally and pass through a fully-automated process. “All monitoring tasks are automated so personnel capacity can be used to complete other tasks”, he says, pinpointing one clear advantage.
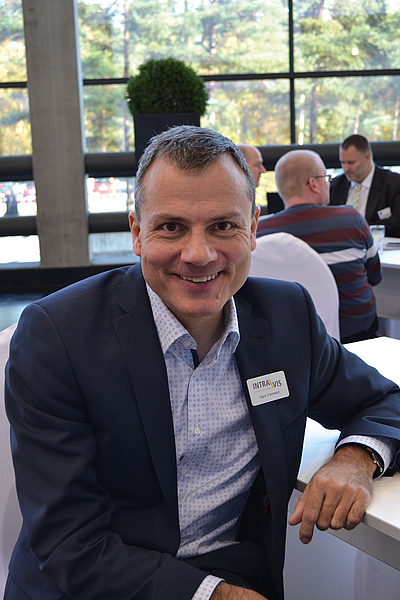
Dr Gerd Fuhrmann
For Hansa-Heemann, digitisation of processes on the whole is now a must, in order to guarantee faster and safer procedures. It is important not to leave your employees behind, but instead to integrate them and inform them, emphasises German Reichert, and admits: “The effort expended in digitalising a process is enormous. We have 17 core processes in-house, and need approximately a year to digitalise just one of them.” One core process can range from the admission of materials to customer deliveries. According to Reichert, the main task in automating a process is creating a process organisation, for which Hansa-Heemann employed an IT architect. Also in this area, every process in every company has to be individually tailored to its particular task.
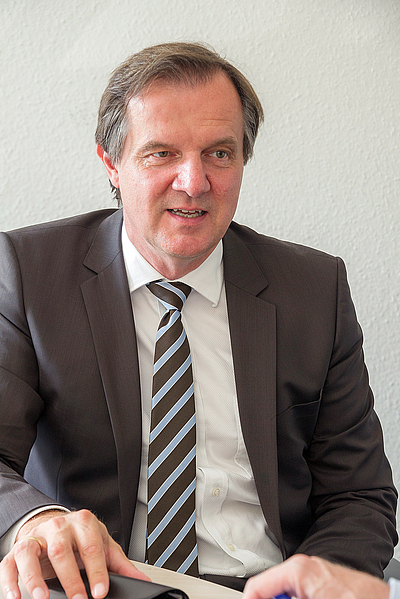
German Reichert
New insights through a VR headset
Virtual reality (VR) is an important area with close links to the topic of digitisation/Industry 4.0. VR is defined as the representation and perception of reality and its physical characteristics in an interactive, virtual environment generated by a computer in real-time. The VR applications most widely-known in everyday life are flight and racing car simulators. In addition to finding application in medicine, architecture and chemistry, VR is increasingly being used in mechanical engineering and production processes. Many mechanical engineers have already brought VR systems into play for their plastics processing and filling lines. With this sort of simulators, it is not only possible to hold employee training programmes, but also to visualise the services offered to customers – the customer can really “walk” through the plant and take a good look at all the individual components. “Simulation with virtual machines allow us to perform trials and test optimisations without damaging or stopping a real machine and thus avoiding any associated any costs. As a result, new machine designs can be introduced into the market more quickly”, says Michael Thomas, Head of Production Machines at Siemens AG, Erlangen, who firmly believes it will also be possible to test real production processes digitally in the future.
The umbrella term augmented reality, AR, is another aid already being put to use in a number of different ways. AR refers to a computerised-supplemented perception of reality. For example, using a tablet, a machine operator can record a video with audio of a failure in the production plant. The data is then sent over the internet to the service technician, who can then input the necessary action to be taken directly into the document. Repair measures can be carried out quickly and easily. An AR headset carried by the machine operator allows service technicians to have a direct view into the plant, even from a remote location, which enables them to offer the machine operator live support.
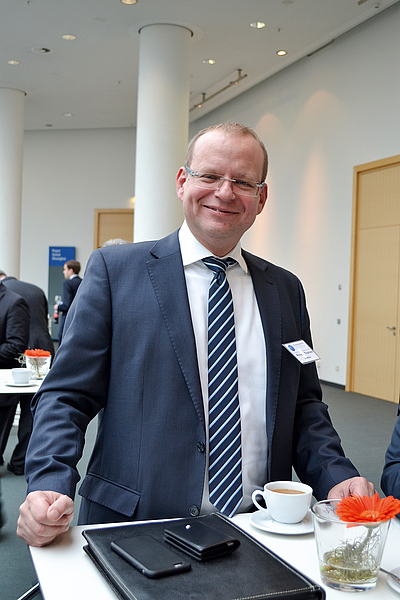
Michael Thomas
Big data must be processed
The implications of digitisation and Industry 4.0 extend far beyond automating production processes, connecting production and logistics, or programming VR systems – huge amounts of data are also generated which need to be skilfully used and connected. Dr Stefan Seiss, Supply Chain Director for Coca-Cola European Partners Deutschland GmbH sees it this way: “We are already generating huge quantities of data. But we will only succeed in making the crucial leap if we can also analyse the data accordingly and above all, intelligently connect the different data sources and information available to us. Only then when we have made this step will the foundations for new findings, as well as for faster and, most notably, better decision-making have been laid.” And it is precisely this which presents the future task for our entire industry: how to meaningfully process and connect huge amounts of data, the so-called big data. There are a number of different approaches and ideas for this. Data acquisition laid the original groundwork, but has also made significant progress in recent years. Nowadays, not only temperatures, pressures or rotational speeds are measured, but also entire data packets are generated. Average values, limiting value violations and product parameters, such as gloss or transparency, to name just a few, are recorded online by intelligent sensors. But there are not only more possibilities for collecting huge amounts of data – there are also more possibilities for processing this data. Nowadays, computers with enormous processing power are available for processing big data. In contrast to traditional control engineering, which uses a matrix where input and output, or the data collected and the action derived from it, are closely connected; new approaches are being applied now. “Firstly, there is an empirical approach”, explains Dr Fuhrmann from Intravis. Information is collected and meaningful courses of action are deduced from it on the computer.
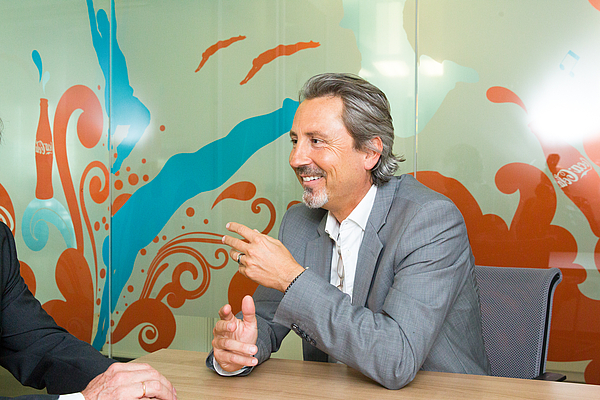
Dr Stefan Seiss
Another possibility would be an evolutionary approach, he says. For example, following the biological principle of the survival of the fittest, the machine settings which have proven to be most meaningful in most cases could be selected and used. It could even be possible eventually to work with self-learning neural networks. “We are still at the very beginning, I expect it will take at least eight years until the new digitisation methods are implemented”, says Dr Fuhrmann, articulating both advantages and disadvantages of the new methods. He expects advantages to include greater stability in processes and a reduced call for labour, which would then free up employees to work in other areas. The current lack of transparency is among the disadvantages, he continues, expressing the difficulty in knowing exactly what is happening with the data and whether machine operators can really rely on it. “But when we reach the limits of our understanding – that’s the point when it will get really exciting”, is his take on the matter. For this reason, he is looking forward to future developments and is set to play an active role in them with his company.
The cloud requires security and trust
One option for storing huge amounts of data from different plants, from different companies, or even from competitors is by using the cloud. “Everyone is required to decide what level of detail to store data in”, says Thomas Haessler, Plant Digitalisation at Syskron GmbH, Regensburg, who is well aware of the concerns around the security of the cloud. “Bringing together information in a cloud and processing it in its context offers enormous opportunities for everyone involved.” He cites Google as an example of a company which has long used anonymised data from users around the world to identify trends and tendencies which can be used for the good of society as a whole. For this reason, he thinks that: “Storing data in the cloud means investing something and receiving valuable information in return.” The following example gives a more concrete example of what he means: If more blow moulding companies were prepared to feed the data and information collected in their processing machines into their machinery manufacturer’s cloud, comparisons could be made which would result in the optimisation of machine parameters – which would benefit everyone.
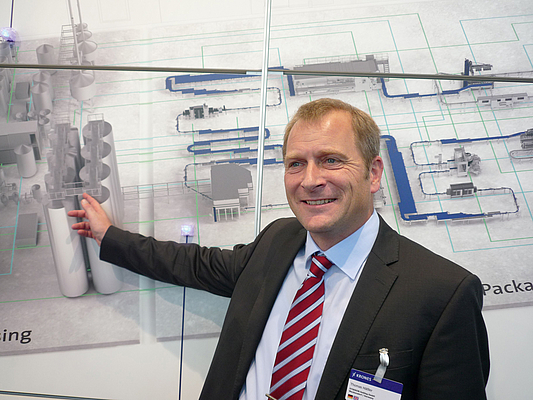
Thomas Haessler
A cloud solution can also directly bring company-specific advantages. Digital printing developed by KHS and marketed by NMP Systems GmbH is using a cloud solution for the bottle decoration. “Nature Multi Pack (NMP) is a new business model offering customers a flexible, and more importantly, a sustainable packaging solution for their PET drink bottles. The cloud solution is speeding up the time to market and is supporting the trend towards individualization”, says Dr Peter Stelter, Head of Strategy and Technology Management at KHS.
This article has explored just some of the many aspects of digitisation. All of the company representatives agreed that any company which wants to remain competitive cannot close its eyes to new technology. “Digitisation is the ideal instrument for improving processes, launching products more quickly in the market, and ultimately for increasing satisfaction for our customers and the consumers. And that is our main goal”, says Dr Stefan Seiss from Coca Cola, getting to the heart of the matter. Nonetheless – and this was also universally agreed upon – we still have a long way to go before the Smart Factory, where machine components communicate with each other and processes improve themselves independently, becomes a reality.
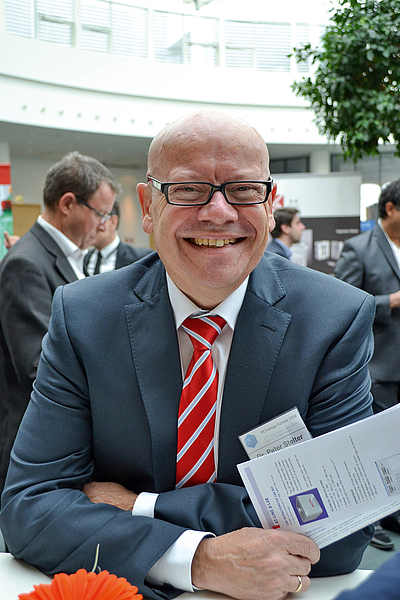
Dr Peter Stelter
A similar conclusion was drawn in the final report of the Science and Industry Research Union (Forschungsunion Wirtschaft – Wissenschaft) and acatech – the German National Academy of Science and Engineering: “The way to the vision of Industry 4.0 is an evolutionary process which is driven forward by companies and specialist industries at different paces. It is essential to swiftly develop demonstrators and to bring products onto the market.” The fact that follow-up projects had already been started by the end of the first project in 2012 is testament to the importance of Industry 4.0. Several projects run by the German Federal Ministry for Economic Affairs and Energy (BMWi) are combined under the title of “Smart Service World”, where important contributions are being made to ensure that “the economy perceives digitisation to be an opportunity and is approached creatively.” Digitisation is not an end in itself, but a prerequisite for many future developments. The PET industry will continue to pursue the topic of digitisation in the years to come – we will keep you up-to-date.
The comPETence center provides your organisation with a dynamic, cost effective way to promote your products and services.
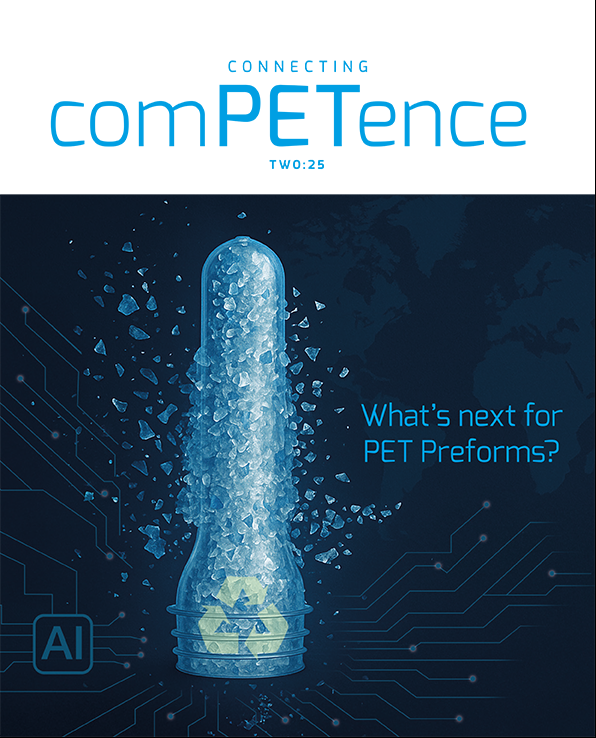
magazine
Find our premium articles, interviews, reports and more
in 3 issues in 2025.