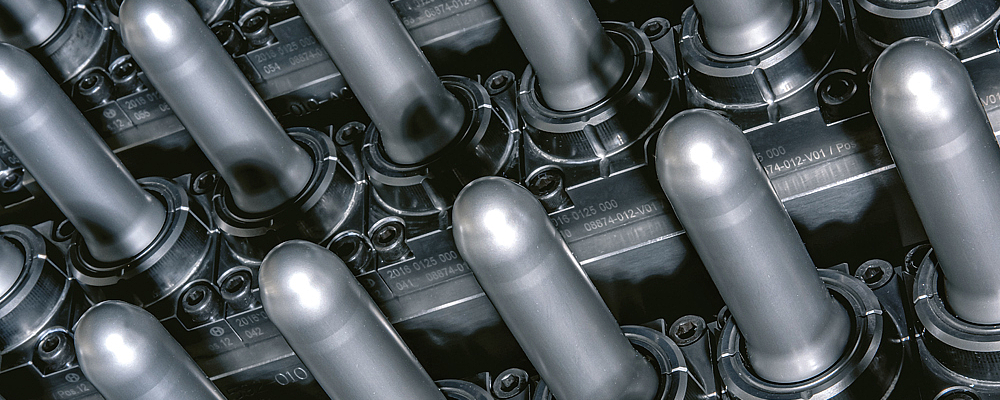
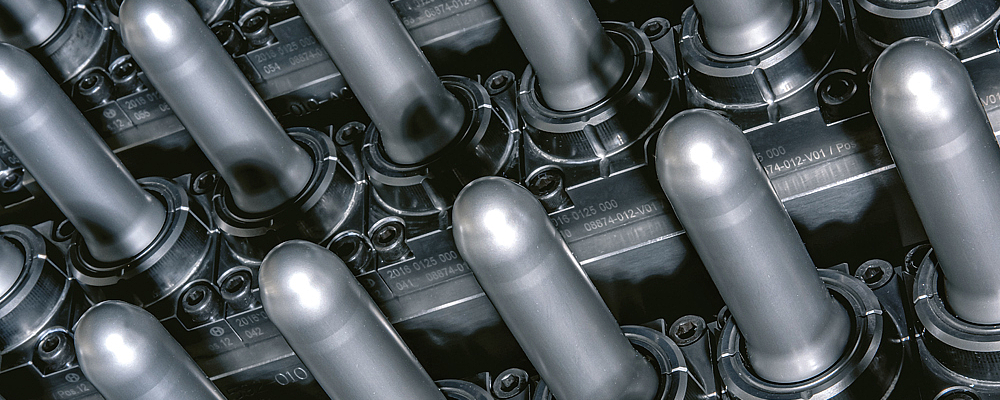
Fig 1: 80% reduction of number of cleaning stops with OH Xblow (Source: Otto Hofstetter AG)
Preform Moulding
Increased production thanks to continuous cleaning with OH Xblow
Shortly after market rollout of OH Xport, Otto Hofstetter AG from Switzerland releases its next productivity boosting product called OH Xblow. OH Xblow keeps neck splits clean, particularly when operating with dust-prone rPET material. This reduces the number of manual cleaning cycles at great extent, adding up to 200 production hours to the year.
Preform manufacturers are well aware of the issues caused by sublimates. Sublimates tend to agglomerate in and around the venting channels of the neck splits. Such unwanted deposits decrease the venting capabilities of the preform injection mould. Unless cleaned, flow lines or round edges may appear on preforms.
rPET increases the need for cleaning
Sustainability initiatives by the brand owners push the use of post-consumer resins in manufacturing of preforms. Producers which have already done the first step in using of rPET often find themselves dealing with an increased load of dust and deposits. This happens because rPET typically contains certain additives an impurities from the previous bottles lives.
In addition to dust, oily excretions of color residues in the rPET also promote further deposits. Obviously, the extent of accumulated production grime determines the need for maintenance stops. With the growing use of recyclates, the need for cleaning increases for conventional moulds.

The approach of OH Xblow
The working principle of OH Xport is to prevent the dust from sitting down on the neck splits. The goal therefore was to find a way which prevents dust from docking on the critical surfaces. The R&D specialists from Otto Hofstetter AG developed a methode to keep sublimates in motion and guide them out of the neck zone with help of compressed air pulses. The now commercialized product continuously cleans at every production cycle.
OH Xblow has proven to work in the field
With OH Xblow installed, up to four cleaning cycles can be skipped before the next manual cleaning stop. As a result of this, the production runs are now five times longer, compared to before installation of OH Xblow. The first customer - consequently - upgraded all his cold sides for long runner preforms with OH Xblow.
OH Xblow is now working in a number of commercial production lines. Peak product performance was reached in a production environment which works with 100% post-consumer resin and a blow at every cycle.
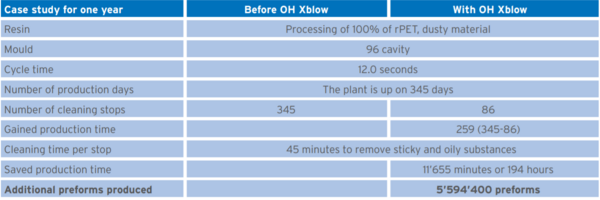
Unchanged working routines
OH Xblow’s on-the-fly cleaning does not disrupt production. The operators do not take notice of OH Xblow. They continue to produce highest quality preforms without extra training. OH Xblow works fully automatic and the cycle time remains unchanged. Automated cleaning with OH Xblow requires no interruption of production. No time is lost for automated cleaning and no material is wasted.
Unchanged maintenance routines
Because much less manual cleaning is required with OH Xblow, operation & maintenance staff can focus on issues other than cleaning. OH Xblow also does not require any maintenance. For this reason, also maintenance routines remain unchanged and no staff training for maintenance is required. Should the user however wish to play with the air pulse settings, then this can be easily done via touch screen of the controller.
Controlling the compressed air
OH Xblow requires compressed air to operate. Part of an upgrading package is the controller which is already known from OH Xport. The controller operates the compressed air valve. The compressed air pulses are triggered by the opening of the mould. The exact on/ off timing pattern of the air pulses are preset. The same settings work for a wide range of preforms.
Where to use OH Xblow
OH Xblow can be installed on all new preform moulds. Thanks to its reversecompatibility, it can also be retrofitted to most existing injection moulding tools from Otto Hofstetter AG. Upgrading of an existing mould can be performed at the plant. The modifications required come down to replacing the sliding bars and neck splits against new parts, premanufactured by Otto Hofstetter AG. No machining of reused parts is required. To add OH Xblow to an existing mould is a matter of few days, installation of the controller included.
OH Xblow’s rapid ROI
The math is simple: The less you need to clean, the faster OH Xblow pays for itself. Rapid return on investment is assured with Xblow. OH Xblow can add (or regain) well more than a week of production time in a year, for every single system in the production plant.
The specialists from Otto Hofstetter AG developed their new added value product in close collaboration with customers. The team succeeded with substantially reducing a major cause of shutdowns. OH Xblow is the smart way to lengthen the time between cleaning shutdowns. PET preform production lines are kept up and running up to five times longer.
The comPETence center provides your organisation with a dynamic, cost effective way to promote your products and services.
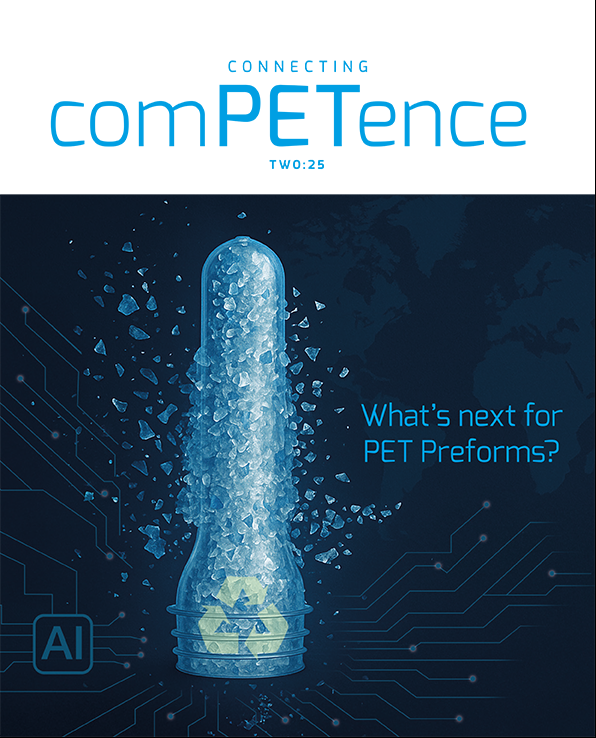
magazine
Find our premium articles, interviews, reports and more
in 3 issues in 2025.