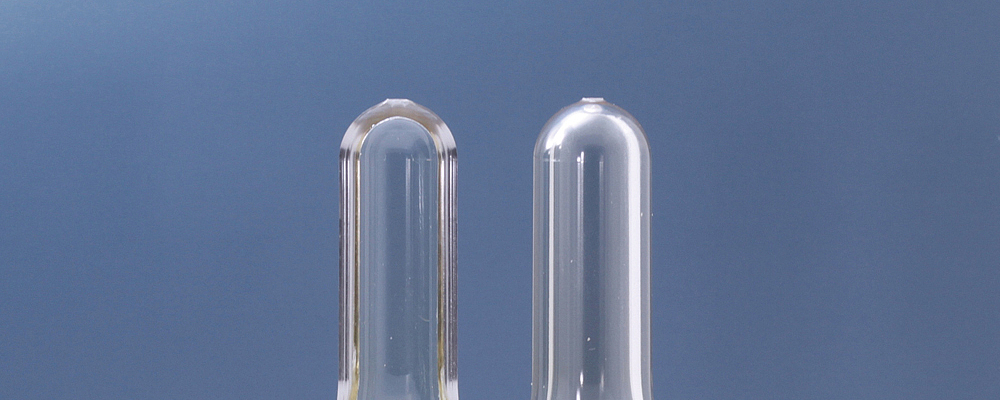
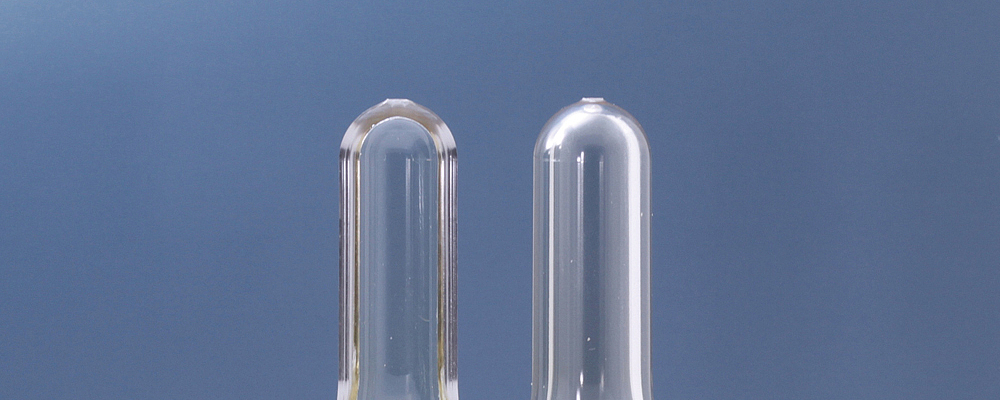
(Source: Avantium)
Material
Improving the sustainability and performance of multilayer barrier containers with PEF
Over the past few years, there has been a concerted move throughout the entire packaging value chain towards implementing a circular economy. Brand owners are committing to using more recycled materials and are advertising broader sustainability programs. Converters and material suppliers propose new technical solutions for the intelligent design and production of packaging. Recyclers also play a pivotal role in the newly vitalized market for post-consumer recycled materials, although at the same time face increased challenges when dealing with contamination issues arising from poorly recyclable items that enter their facilities.
The issue of contamination is also problematic for PET, despite it often being considered the champion amongst plastics when it comes to recyclability. Although PET is the material of choice for beverage packaging, it often needs help to overcome its limitations when it comes protecting products that are particularly sensitive or that require a longer shelf life, which cannot be achieved by monomaterial PET packaging alone.
This is where barrier technologies like those implemented in multilayer bottles play a role. Offering some of the functional advantages of a PET bottle, an interstitial layer within the bottle wall adds barrier protection that enables the necessary performance to satisfy the demands of the market. Current, commonly used barrier materials like polyamides, however, pose the problem of their poor recyclability when combined with PET, and their use is often conditionally limited to colored bottles. Even when such polyamide barrier layers are tolerated in the recycling stream, recyclers must attempt to completely remove this and heavily rely on the air elutriation step for this, with a delicate tradeoff between the resulting quantity and quality of their rPET product. It not uncommon that this results in this recycled PET which is only suitable for different, lower value outlets such as strapping, which is the opposite of the desired, high value bottle-to-bottle rPET stream.
Thus, in a circular economy model it is not only the material that comes back into the loop, but also the challenges too: producers that are introducing poorly recyclable packaging items will also face the problem of good quality rPET scarcity when, to comply with their sustainability promises and obligations, they will need to use PCR materials from the very same pool that they are contaminating.
Hence, rapid innovation in this area is key, and an opportunity for the entire packaging value chain is represented by polyethylene furandicarboxylate (PEF) with its excellent barrier performance and compatibility with PET.
PEF, an innovation that fits the drive towards circularity
PEF is a performance polyester that is made from 100% renewable resources. Thanks to its outstanding gas barrier, coupled with balanced thermomechanical and processability properties, it has an excellent fit in packaging applications. Additionally, PEF is compatible with PET mechanical recycling assets, and when it is processed as part of the PET recycling stream it has been proven that PEF has lower impact than other barrier materials on haze and other properties of the resulting rPET products. /1/, /2/
Avantium Renewable Polymers, a 100% subsidiary of Avantium, plans to build the first commercial-scale plant for the production of FDCA (furandicarboxylic acid), a monomer for PEF and other high performance polyesters. This firstof-a-kind plant, which Avantium aims to have on-stream during 2023, will be built in Delfzijl, the Netherlands and will produce 5 metric kilotons of FDCA and PEF per year. Avantium has already proven its technology to produce these novel materials at smaller scale from its pilot plant in Geleen, the Netherlands, and is using the FDCA and PEF produced here to develop and accelerate the market introduction of various highvalue applications. Key amongst these pioneering uses of the novel polymer is its application as a barrier material in multilayer PET bottles, where PEF represents a valid alternative to the current barrier materials used today /2/ , combining enhanced shelf life performance with vastly improved sustainability.
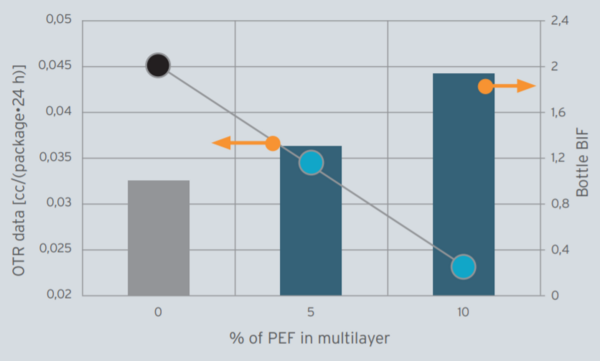
All-polyester multilayer bottles with the right barrier performance
In a previous article published in ComPETence Two:20 /2/, multilayer PET bottles utilizing PEF as a barrier layer were shown for the first time. These bottles were produced using standard PET bottle processes and geometries, and resulted in similar material distribution and mechanical performance as a monolayer PET reference, with no appreciable color or haze differences when compared to monolayer PET.
When it comes to the barrier performance of the multilayer bottle, OTR data were presented which showed that the shelf life of a product can be extended by 80% when a 10 wt% PEF layer is used compared with a monolayer PET bottle of the same weight and design.
In this further communication, the CO2 retention of the PET/PEF multilayer bottles will be detailed, including a comparison with incumbent solutions from the market where Polyamide is used as a barrier layer. Figure 2 shows the loss of carbonation from these bottles with time - as expected, after an initial drop in carbonation during the first two weeks, the trend stabilizes. The CO2 transmission rate depends on the permeability of the bottle walls to CO2 and the carbonation level in the bottles at every given moment, however in the interval of time studied the loss of CO2 can be considered to be approximately linear with time. Therefore it is possible to calculate the CO2 loss rate in units of g/(L24 h), which allows for a relative comparison between the different variants. From Figure 3, it is evident that the use of PEF as a barrier layer in multilayer PET bottles can also be an effective measure to extend the shelf life of carbonated drinks as well as oxygensensitive beverages.
Furthermore, when compared to the monolayer PET bottle of the same mass and design, a multilayer bottle with 10 % PEF achieved a barrier improvement factor above 2. This translates to a doubling of the shelf life, which is in line with or even outperforms market incumbent multilayer bottles containing up to 7% polyamide.
Sustainability value of multilayer PET-PEF bottles
During recycling, the decontamination via air elutriation of flakes from PET multilayer bottles containing polyamide is absolutely necessary to remove as much of the incompatible barrier material. A well-produced polyamide based multilayer barrier bottle is therefore optimized for delamination to occur during flaking and washing. Recycling of such multilayer bottles relies heavily on the capability of bottle preform and bottle production as well as on the efficiency of the elutriation step to avoid the devaluation of the quality of the PET recyclate. The separated polyamide flakes cannot be further recycled independently, and are commonly incinerated which leads to the release of N2O into the atmosphere. N2O is a greenhouse gas which has an effect 298 times more severe than CO2 . Therefore, even if multilayer bottles containing polyamide can be considered as being recyclable, this unavoidable release of powerful greenhouse gases will significantly worsen the carbon footprint of such a bottle. PEF’s chemical composition contains no nitrogen, and it is far more compatible with PET so therefore does not necessarily need to undergo such extensive removal during recycling. An increased yield as well as reduced carbon footprint can therefore likely be achieved in industrial recycling of PEF based multilayer PET bottles. Avantium is currently performing an extensive LCA study of PEF in multilayer bottle applications which will be published in the course of 2021.
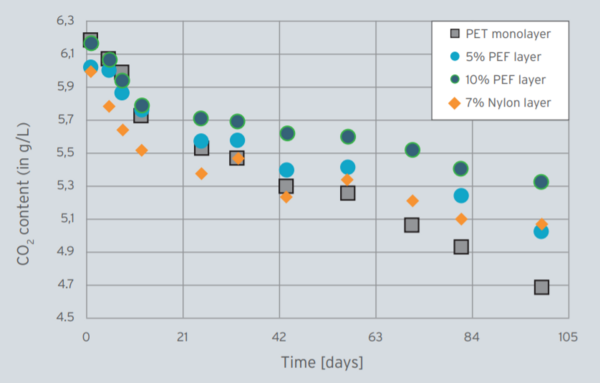
Conclusions – and a call to action!
The current barrier materials utilized in multilayer bottles, such as polyamide, offer sufficient performance at a reasonable cost, but pose significant doubts in terms of their fit with recycling infrastructures and the circular economy. The recyclability of PET multilayer bottles with polyamide is conditional, with such limitations as only being used in colored bottles and/ or at a maximum layer percentage at a limited market penetration. Furthermore, the recycling of multilayer polyamide bottles also heavily relies on the efficiency of the decontamination step, where the vast majority of the polyamide must be removed by the recycler to avoid severely affecting the quality of the recycled PET. Recyclers are therefore left with the problem of finding the delicate balance between quality (removing polyamide as much as possible) and quantity (not sacrificing the yield of rPET).
When it comes to performance PEF is a very valid alternative to polyamide barrier layers, matching shelf life extension at a similar or slightly higher dosing level. However, PEF comes with significant added value: it is made from renewable sources, and its compatibility with PET is a definite advantage during recycling. PEF truly represents an innovative solution to be added to the toolbox of designing for recycling and circular products. It is good news for recyclers and converters, but is especially valuable for those brand owners who are loudly and proudly announcing their commitment towards building a more sustainable world.
Nevertheless, in its path to commercialization PEF will face the same challenges typical of every innovative product - its acceptance will be constantly endangered by purely economic concerns, which ignore the significant sustainability benefits that PEF can bring to help brand owners achieve their promises on sustainability, and prove to both the industry and consumers that they are truly pioneers who walk-the-walk and will lead the transition to a circular economy from the front.
Avantium is committed to bringing PEF to the world and helping it to find its rightful place in the market. However, we cannot do this alone – we currently, and will continue to, partner with pioneering adopters along the value chain who live up to their promises and see their sustainability commitments as more than a marketing opportunity to a concrete reality. Will you come with us? Let’s Go!
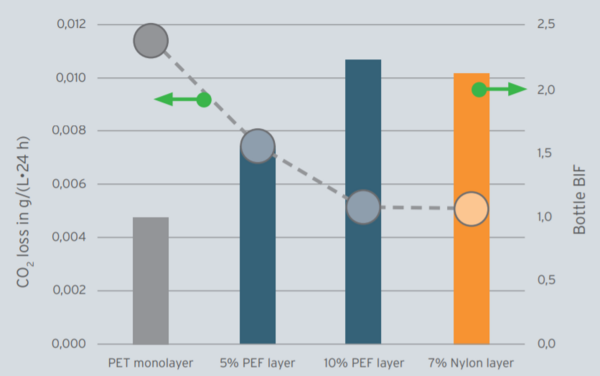
Acknowledgements
The support of Husky for the preform production and the know-how of coinjection is greatly appreciated. The bottle blowing and bottle testing was done in collaboration with Logoplaste Innovation Lab.
_______________
/1 / ComPETence Magazine, ONE:20, p 100-103, “PET and PEF. A combination fit for future sustainable barrier packaging solutions
/2 / ComPETence Magazine, TWO:20, p 56-61, “PEF as a multilayer barrier technology: a sustainable way to enable long shelf life in PET bottles”
The comPETence center provides your organisation with a dynamic, cost effective way to promote your products and services.
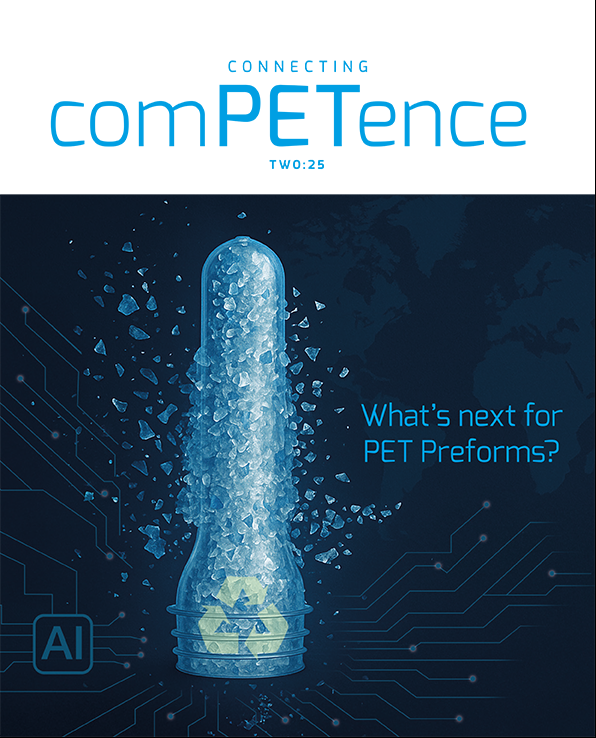
magazine
Find our premium articles, interviews, reports and more
in 3 issues in 2025.