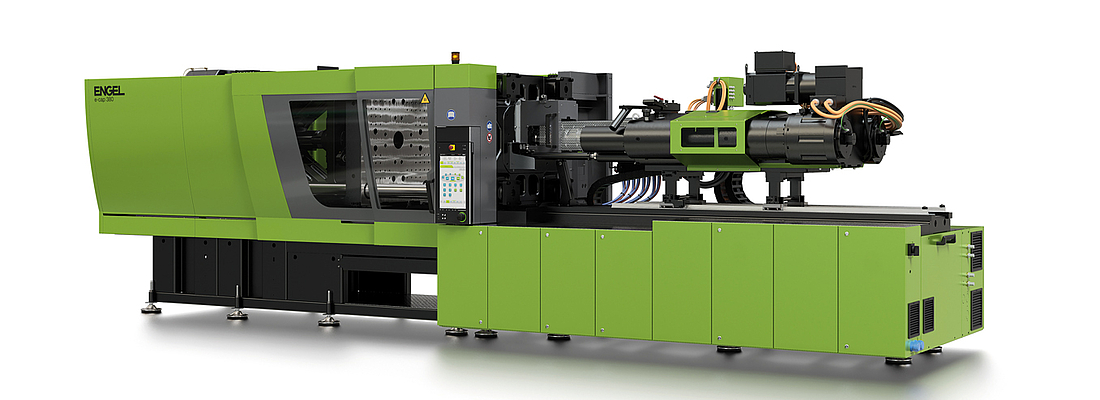
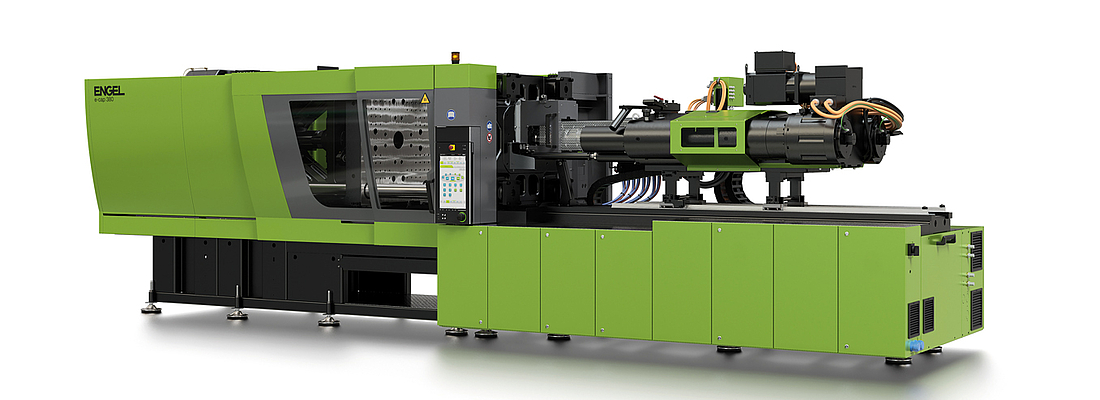
Photo credit: ENGEL AUSTRIA GmbH
The production of 29/25 lightweight caps on a new e-cap 380 machine
Highest stability and precision with the shortest cycle time
Multi-use PET bottles come out significantly better in life cycle assessments than single-use PET bottles ENGEL set new standards with the presentation of the first all-electric e-cap injection mould-ing machine at K 2010. Until then, hydraulic machines using accumulators for the injection movement were the standard for the production of caps. The all-electric drive technology in this field of application was a revolution at the time. To date, the e-cap is the most energy-efficient cap machine on the market and at the same time the only high-performance machine tailored to the requirements of the caps and closures industry providing allelectric operation even with a clamping force range as high as 4,200 kN. With an average ROI of less than two years, the e-cap has quickly established itself worldwide since its market launch.
Highest dynamic performance with frequent load changes
Since 2010, the requirements for beverage caps have changed substantially. This is why the continuous further development of e-cap now is being integrated into a next generation machine. Continuous part weight reductions play a central role. For still water, caps with a weight of significantly less than one gram are produced today. As a result, the cooling and cycle times have continued to drop. Where the cycle times ten years ago were still 2.5 seconds, today’s cap machines need to be able to produce at 2-second intervals and faster. When developing the new generation of machines, the main fo-cus was therefore both on performance and on stability. The new e-cap achieves even faster mould movements and is designed with an even more stable machine bed for more frequent load cycles.
Ejector drives amplified with booster
An e-cap 2440/380 is demonstrating the series’ new performance achievements by
force producing 29/25 caps in a 96-cavity mould by Plastisud. The shot weight is 1.3 grams per cavity with a cycle time of less than 2 seconds. An HDPE from Borealis/Borouge is processed. The sys-tem is equipped with camera-supported 100 percent quality inspection by IMDvista and a dry air system by Eisbär. Further system partners are Piovan, PackSys Global and PSG.
The reinforced frame and the reinforced mould mounting platens on the new e-cap ensure excellent stability of the machine movements even with extremely short cycles and very small shot volumes. The result is outstanding reproduction of surface detail and a maximum number of good parts.
The fast dry cycle times of 1.3 seconds with the e-cap 380, for example, and the parallel movements included in the standard right from the outset make an important contribution to achieving cycle times of less than 2 seconds. Ejection occurs parallel to the mould opening. What is new is that the direct-drive servoelectric ejectors can be amplified by a switchable hydraulic booster on demand. With the two different drive types, ENGEL ensures that the ma-chine operates with the best possible efficiency both during running production and during start-up after a production interruption. While the caps are not yet completely cooled and very easy to demould during ejection in ongoing production, the ejectors have to apply more force in stop situations to remove caps that have already cooled down in the mould. Since produc-tion interruptions are rare, it is more efficient to use servo-hydraulic drive amplification than to generally equip the machine with more powerful ejector drives. High forces only when they are actually needed – that is ENGEL’s motto.
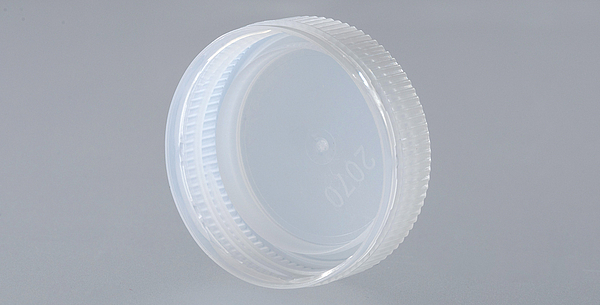
More powerful plasticising unit for poor-flowing HDPE
The plasticising unit was completely redesigned in the course of the e-cap’s further develop-ment, as the properties of the materials to be processed have also changed. The raw material manufacturers have adapted the materials to the lower cap weights. For CSD (carbonated soft drink) caps, the melt flow index (MFI) of today’s HDPE grades is between 0.8 and 1.4 g/10 min. With very short cycle times, these values require particularly high plasticising rates.
ENGEL has increased the torque of the plasticising drive accordingly and developed both a new plasticising screw and a new highly wear-resistant sliding ring non-return valve specifically for cap manufacture. Both products are part of the standard scope of supply of the new e-cap machines. With its new design, the barrier screw processes high viscosity HDPE in a particularly gentle way, even given high throughput levels, while ensuring a very good melting rate and homogeneity of the melt. This further contributes to the high process stability and repeatability of e-cap machines.
Optimising energy consumption across the entire system
Cleanliness and energy efficiency have been essential characteristics of the series right from the outset. With an encapsulated toggle lever and a very clean linear guide of the moving plat-en, the e-cap machines reliably meet the requirements of strictly regulated production in the food industry. The machines’ all-electric drive technology makes a major contribution to their outstanding energy efficiency. In addition, braking energy is recuperated, reliably preventing the need for expensive peak power. Thanks to the very high efficiency of the drives used, the e-cap ma-chines also only require a minimum of coolant. The e-cap 380, for example, operates at high speed with an energy consumption of 0,37 kWh per kilogram of pellets.
As a system supplier, ENGEL precisely coordinates all the components of the production cell right from the start of the project. This allows ENGEL to fully leverage the efficiency potential throughout the entire production cell.
The new e-cap is available in the sizes 220, 280, 380 and 420 with clamping forces from 2,200 to 4,200 kN.
The comPETence center provides your organisation with a dynamic, cost effective way to promote your products and services.
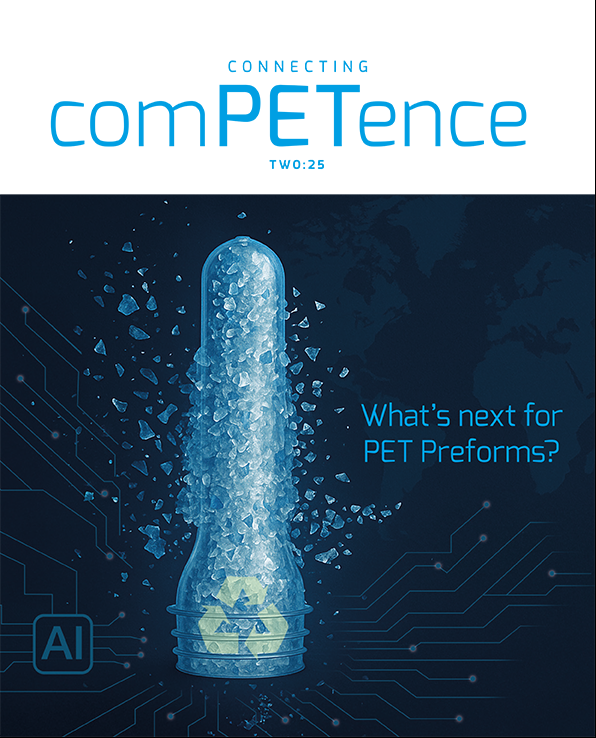
magazine
Find our premium articles, interviews, reports and more
in 3 issues in 2025.