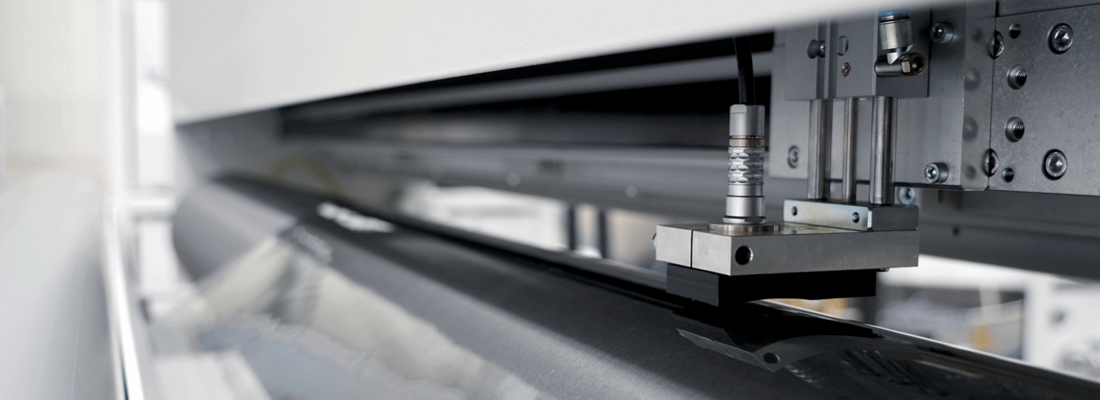
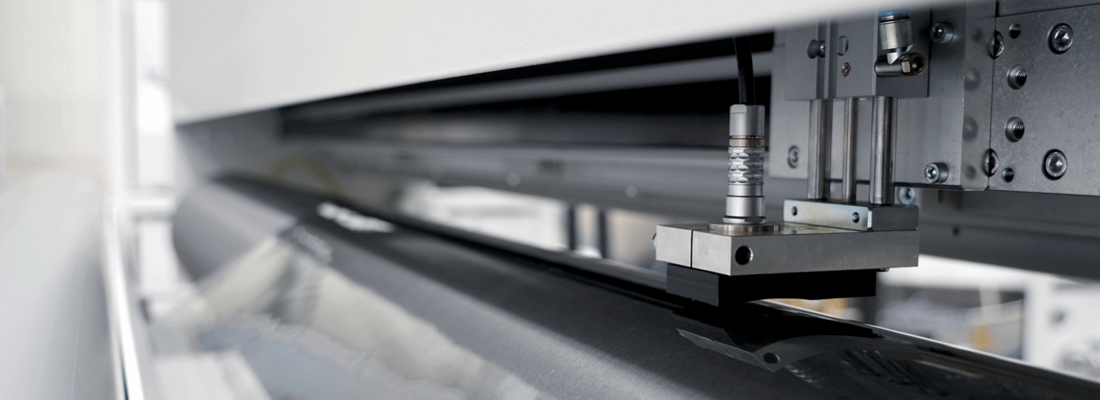
(Photo credit: PETnology)
Recycling
High-Tech with the letter R: Recycling Learning by doing. Showing that it works.
Meeting with Paul Niedl Starlinger recycling technology Markus Fellinger Starlinger viscotec.
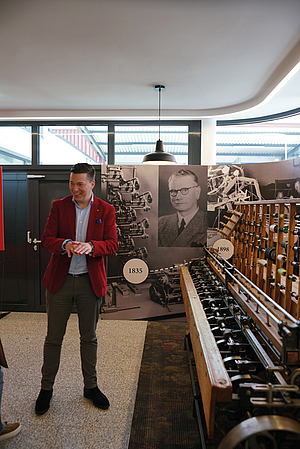
The PET industry associates the name STARLINGER with recycling. Systems for bottle-to-bottle recycling, reactors, plants for sheets made of PET and rPET – this is what Starlinger is known for.
In fact, the Starlinger name stands for more than plastic recycling technology. Starlinger & Co Gesellschaft m.b.H. is a family-run business based in Vienna/Austria. In 2035 the company will celebrate its 200th anniversary. Mechanical engineering was the focus right from the start. Today Starlinger consists of three divisions and we met representatives of the two that focus on recycling for an interview.
Starlinger textile packaging is the most original division. With the production of equipment and the associated process technology for woven plastic sacks, it is continuing the technologies that go back to the beginnings: Here, everything revolves around weaving. At the heart of Starlinger’s site in Weissenbach an der Triesting, near Vienna, there is a representative technical center where you can experience these machines in operation. They produce polypropylene tape, which is further processed into sacks. These serve as packaging for bulk goods such as cement, chemicals, seeds, grain - and also for PET flakes and granules.
_______________
''Today we have more than 45,000 looms installed in the market and over 900 customers around the world working with our technology.'' - Paul Niedl
_______________
Paul Niedl, Commercial Head of the division Starlinger recycling technology, gives us an insight into this exciting part of the Starlinger portfolio: “The success story began in the 1960s with the development of the circular loom. Today we have more than 45,000 looms installed in the market and over 900 customers around the world working with our technology.” Tape extrusion lines and winders were subsequently added, and the machine range completed with coating and printing machines. Highly efficient and user-friendly converting lines round off the machine portfolio for producing woven polypropylene sacks. In recent years, the technology for the production of PET (and rPET) tape fabric has also reached market maturity - the result of the symbiosis of decades of accumulated know-how in the fields of tape extrusion and plastics recycling.
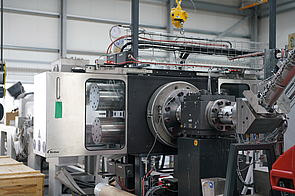
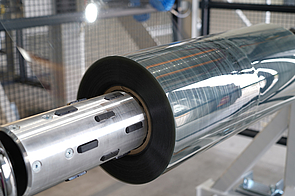
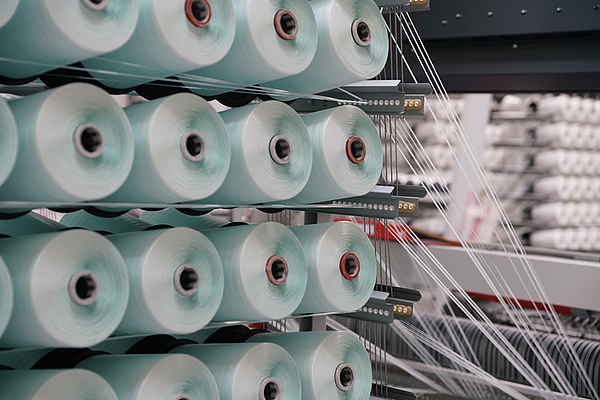
From the “boss’s hobby” to a successful supplier of plastic recycling systems
“In the beginning, recycling technology was regarded as “the hobby” of our late boss,” reports Paul Niedl of the rather critical voices in the company at the beginning. “In fact, he showed outstanding foresight back then and was already convinced of recycling in the 1980s.”
Today, recycling systems are developed in a specific division: Starlinger recycling technology has made a name for itself worldwide, especially in PET bottle-to-bottle recycling. According to Niedl, the installed capacity of bottle-to-bottle recycling systems is 2 million tons per year.
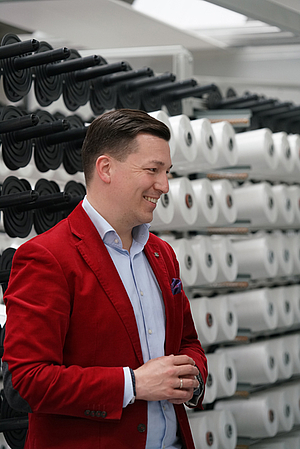
Starlinger recycling technology is headquartered in Weissenbach, but has also been producing in Schwerin, Germany, for several years. The expansion was due to the ever-larger machines and plants: Schwerin is where the large and medium-sized recycling plants are built, as the site has large halls. The smaller plants continue to be produced in Weissenbach. “We have great manufacturing depth and the latest tooling and processing machines in many areas,” says Niedl.
The latest model in the portfolio of PET bottleto-bottle recycling lines is the recoSTAR PET art, presented at the K trade show 2022 in Düsseldorf, a new system that is characterized by particularly low energy consumption. There is always room for improvement, so for the new machine concept, Niedl’s team examined the PET recycling process and its technical solutions from front to back. His team has also succeeded in shortening and simplifying various process steps - including material preparation and extrusion - as well as machine maintenance. “We were even able to increase the production output - while ensuring recyclate at top-quality, for which we are known. With the combined know-how, we have created a “piece of art”, so to say - and hence the name: recoSTAR PET art.” The first machines were already sold at the K trade fair, and Niedl is very satisfied with the positive feedback from the market.
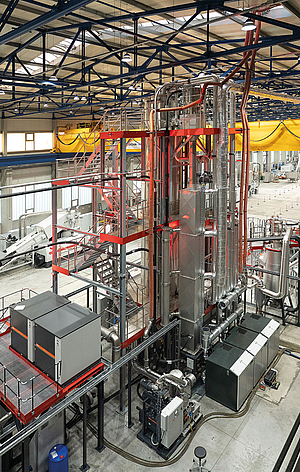
Solid State Polycondensation for Bottle-to-Bottle Recycling
Markus Fellinger, Managing Director of the division Starlinger viscotec, joined Starlinger in 2001, bringing with him not only experience in the plastics recycling industry but also his vision of PET recycling for food contact. “We built the first prototype for bottle-to-bottle recycling in Weissenbach in the early 2000s. It already had everything that is still the core of the system today: pre-drying, extrusion, filtration, granulation,” says Fellinger. At that time, also solid-state polycondensation (SSP) was developed, and food contact approvals were obtained from regulatory authorities in North America.
In 2006, Starlinger installed the first bottle-tobottle recycling plant at one of their customers in Austria, now belonging to one of the world’s largest packaging specialists. The rPET pellets from this plant went to a major brand owner. Fellinger: “That was an important door opener because the requirements of brand owners for the purity of the material are known to be even stricter than those of the European Food Safety Authority.”
The order volume grew and food contact approvals by national and international European authorities and other brand owners followed. The Starlinger management then tasked Fellinger to develop larger SSP reactors and founded a new division in Upper Austria, Starlinger viscotec.
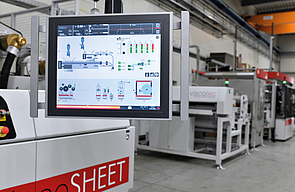
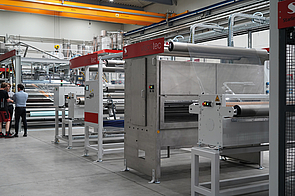
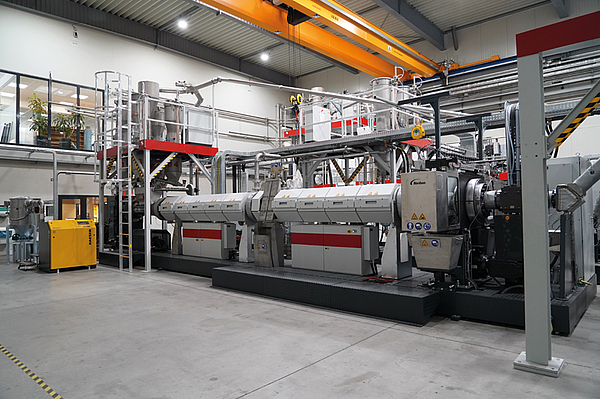
Sheet extrusion lines for recycled PET
With the establishment of the new site, viscotec also focused more on decontaminating recycled PET material upstream of the sheet extrusion line. But OEMs from the packaging industry and sheet production showed little interest and did not see the need for supercleaning for sheets for thermoformed packaging. That was when Starlinger reinvented itself: If decontamination technology is hard to sell separately, then let’s produce our own sheet extrusion lines - with supercleaning right in front of the line. “That wasn’t easy at first, I admit, but now we’re very successful with sheet lines that process PET and recycled PET,” says Fellinger, “partly because we offer everything in a perfect package.”
The art of simple handling
„Perfect package“ that means: The systems were not only built right from the start with the highest possible in-house production, but they are also operated from just one terminal, including the gravimetric dosing unit, the extruder, the roll stack and the automatic winder. “Operating a roll stack like this was not easy with the equipment available at the time,” Fellinger smiles, “so our focus was on automating our line from the very beginning.” Thus, automated sheet production was already possible with the first system in 2012 and has been continuously developed since then. “That was the breakthrough for us,” says Fellinger. “I don’t think there is currently a larger plant manufacturer for sheets made of PET and rPET on the market.” Fellinger attributes the success of the sheet extrusion lines to another point: foodgrade without compromise - supercleaning in front of the sheet system, exactly his argument, which just a short time before had not been taken seriously.
_______________
''In order to use trays on a larger scale in the PET recycling loop, some things have to change in the packaging itself.'' - Markus Fellinger
_______________
Trays for the loop
Since the prices for PET bottle flakes have risen sharply in recent years, alternative material sources such as trays have also come into focus. viscotec has been working on tray-to-tray recycling technology for several years. Fellinger: “In order to use trays on a larger scale in the PET recycling loop, some things have to change in the packaging itself.” His view of tray packaging is clear: the classic PET/PE multilayer composites have long had their day and must be replaced by PET mono-material. Fellinger cites impressive figures: One million tons of thermoformed packaging are on the European market, of which about 500,000 tons are multilayer. “We could use this quantity additionally for closed-loop recycling. That’s a lot of potential for the loop in Europe alone.”
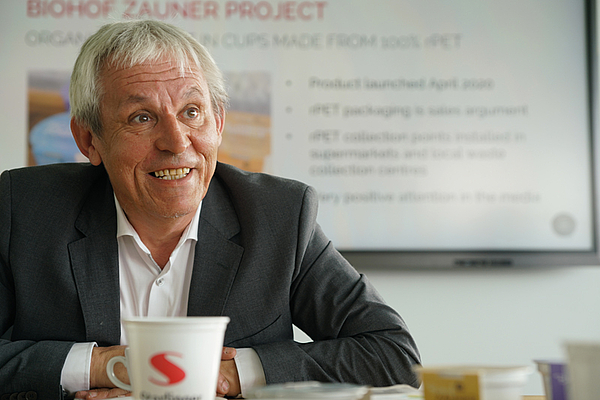
Safe food contact
Starlinger is also at the forefront of HDPE recycling. The HDPE pellets produced with Starlinger’s recycling process can be used in food contact packaging at a rate of up to 100%, as also confirmed by two Letters of Non-Objection from the US Food and Drug Administration (FDA). “These two LNOs were another important success in the area of food safety for Starlinger,” says Paul Niedl. “Just as with PET, 100% recycled HDPE resin can now be used in direct food contact applications.
The latest viscotec development to achieve food grade quality for plastics like HDPE, PP or PS is the melt phase decontamination reactor called viscoZERO that was presented at K 2022. Closures of beverage bottles are an obvious application example for food contact products made from recycled food contact material. Fellinger calculates the potential quantities: “Between 2 and 2.5 g per closure, makes 500,000 tons of pure closure material per year - and that in an existing collection stream.”
_______________
''It’s good that the image of PET recycling and recycling per se has changed.'' - Paul Niedl
_______________
FDA approvals have already been obtained, yet it is more difficult with the EFSA approvals. As in many other discussions, dissatisfaction with the procedures of the EU authorities is also evident here. “The approval process takes a very long time, there are many questions, the staff changes… But the principle is clear, and the arguments are so obvious – we have to seize this opportunity,” says Fellinger, convinced of the new technology. Other applications include production waste from fiber and textile production, punching grid waste or strapping bands, which can be recycled thanks to the high cleaning efficiency of the new technology.
“It’s good that the image of PET recycling and recycling per se has changed,” comments Paul Niedl from Starlinger recycling technology at the end of our visit. He still remembers customers who didn’t want it to be known that they were working with recycled material. “It was frowned upon, was considered a cheap alternative.” Fortunately, that has long since changed. His closing remark: “Recycling is sexy.” He is right!
The comPETence center provides your organisation with a dynamic, cost effective way to promote your products and services.
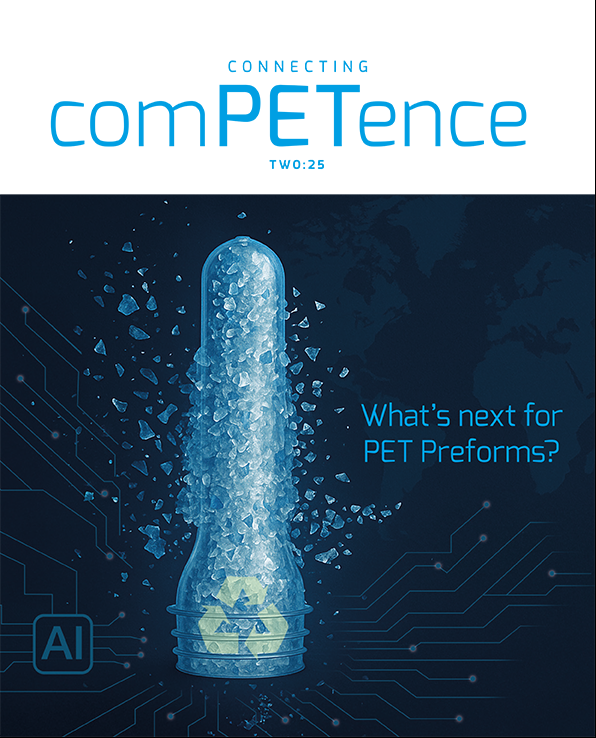
magazine
Find our premium articles, interviews, reports and more
in 3 issues in 2025.