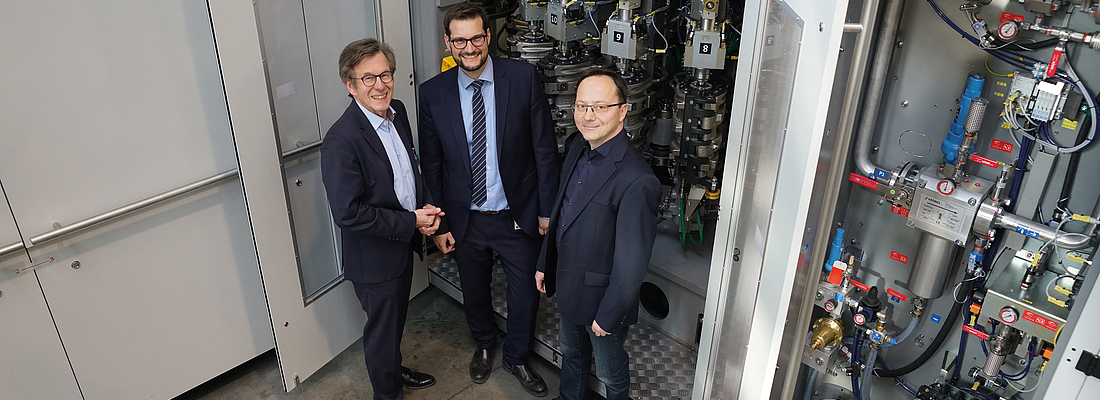
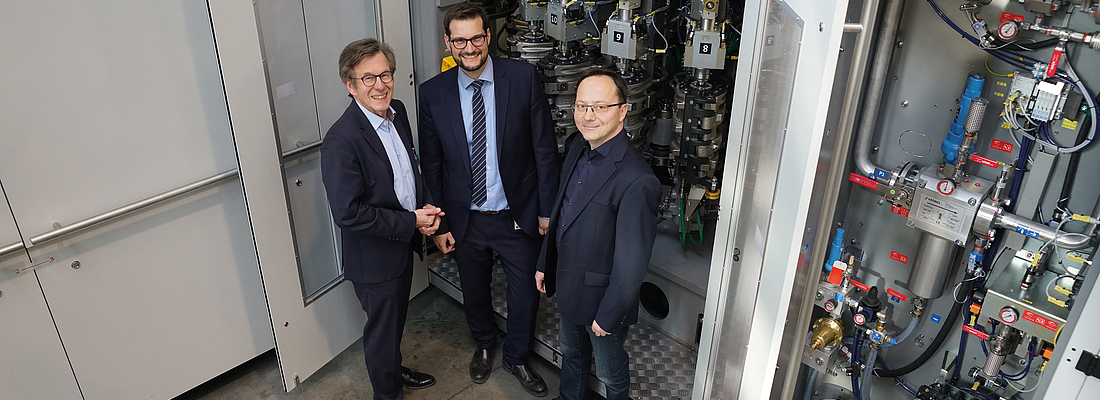
Developing individual machines while thinking in terms of systems. Dr. Otto Appel spoke with Jochen Hirdina, Head of Plastics Technology, and Robert Aust, Head of Product Management, Plastics Technology, Krones AG, Neutraubling, Germany.
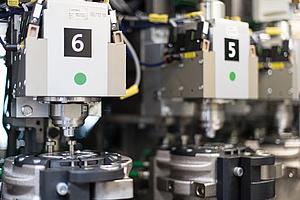
The path through the Krones premises leads me past new assembly halls that are close to completion, buzzing with the hubbub of construction. I meet with Jochen Hirdina and Robert Aust from the Plastics Technology product line, and we went our way through the assembly halls, past blow moulding machines and block systems. It’s clear that the blow moulding and filling machines at Krones AG are hard at work, despite the global debate about plastic waste from the packaging and beverage industries.
This precision engineering - the synergy between mechanical engineering, control technology, process engineering and methods engineering - never fails to amaze me. But, for some time now, I have been sensing a certain disillusionment. It’s not only that consumers are unable to see the highperformance potential of PET bottles. No, it’s more that people are growing increasingly suspicious of plastic packaging, and therefore also PET bottles, in terms of their environmental impact. But there is no plastic material that can be recycled better than PET when it is done right, and done globally.
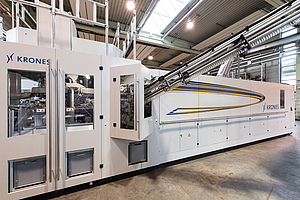
Today we are talking about the new Krones Contiform 3 Speed. We are also talking about whether the success story of the PET bottle - and, by extension, the success story of Krones AG’s stretch blow moulding technology - can continue unaffected by doubts and by all of the environmental debate.
CC: High-tech machines on the one hand, environmental concerns on the other. Is there an increasing need for machine and plant manufacturers to take a stance here?
Hirdina: This is something that affects us on more than just a professional level. On the personal side of things, none of us wants to leave an environmental wasteland to our children and grandchildren. As machine developers, we are keenly aware that we can and must help work on a wide range of solutions - and we are happy to do so. To answer your question: yes, these issues are being brought to our attention. We have been receiving client queries about them for around a year now. Big brands are proclaiming their environmental targets. The question of how to implement these falls to us. It’s about recycling, recycling concepts, materials streams, and the processing of recycling materials. But, as always, there is still a focus on increasing performance and reducing weight and energy consumption.
CC: What does the future hold?
H: That’s an important question. One thing we have in our sights is the “economy of scale”. In the world’s mega-plants, this remains the core focus. They would like to operate the lines with even higher system capacities - from 90,000 to over 100,000 fillings per hour. There’s no limit to what people can dream up here. This is the context that our new Contiform 3 Speed is situated in.
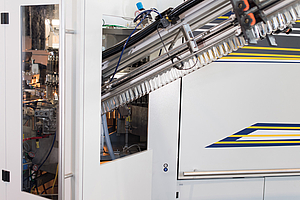
CC: That’s probably just one side of the coin.
H: Exactly. The circular economy approach is also something that drives us. We want to know whether a facility with several high-performance systems can also be “fed” with recycled material and the associated materials streams. Could smaller, local production sites even be - or become - more economical using this approach? The range of possible applications in the field of stretch blow moulding is broad, and it’s possible that the future will bring completely new distribution channels, such as bottleon-demand concepts delivered via a channel like Amazon. How would that change things? At the moment, it’s difficult to say.
CC: Engineers and technicians need measured variables. They need parameters that they can use to measure and compare solutions and make decisions. In terms of sustainability, the parameter that has been used thus far is the carbon footprint of a unit of packaging. Has this parameter disappeared as a comparative variable? Or has it lost its relevance?
Aust: The technical facts for the PET bottle are easy to list. Nothing about those facts has changed, and the same principles that have always applied still apply today: the less energy and compressed air used, and the more recycled material used, the lower the carbon footprint. But the facts have to compete with perceptions, which are shaped by media reporting and photos of mountains of waste. Our CEO Christoph Klenk likes to say that “perception is reality”. Perceptions move people emotionally and become fixed in their minds, even if facts, figures and data might tell a very different story. For our PET industry, this means - on the one hand - that PET packaging is the sustainable solution if we want to package and transport water, food, and non-food items safely and hygienically. On the other hand, it shouldn’t be ending up in our environment, in the oceans! We need to get a handle on this situation.
Development of the air- and energy-consumption of the Contiform (0,5l bottle, normalized)
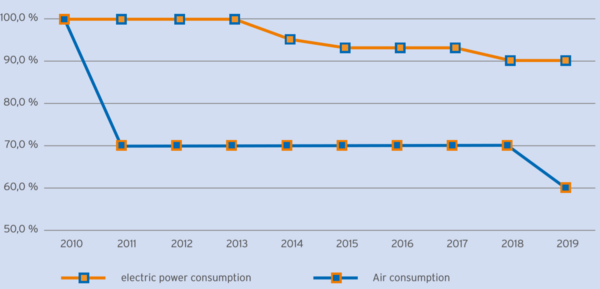
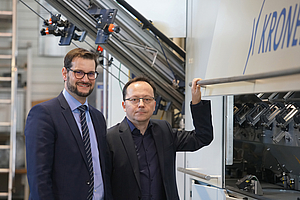
CC: Let’s talk about the key factors in sustainability for PET bottles: performance and energy consumption. Were they the impetus behind the new Contiform 3 Speed?
H: To give you a clear answer: we recognised the quality and performance of the Contiform 3 Pro, and we wanted to develop that further. Because “if you always do what you’ve always done, you’ll always get what you’ve always got.”
CC: A quote by Henry Ford. He was constantly re-thinking the old to make something new. This changed the face of industry. Is the same true of Krones?
H: Re-thinking the old to make something new. That is always our goal. That’s why we always strive to be one step ahead in terms of development and innovation.
A: Our approach to the Contiform 3 Speed is no different. Naturally, we wanted to develop a stretch-blow moulding machine that had the potential for higher performance. And with a station output of 2,750 b/h for the Contiform 3 Speed, we achieved just that. But to get back to your original question, performance and energy consumption are particularly closely linked to process technology. So we asked ourselves: how can we make things even better?
CC: What sort of things did you look at improving for the Contiform?
A: The first question that came up was actually whether the pressure compensation pad on the mould carrier would still be needed. It quickly became clear to us how much installation space we could save and what the benefit of that saving would be: a compact blowing station with an optimised mould carrier, more stations on the pitch circle, or a smaller blowing wheel diameter, making for more compact machines. In fact, we were able to eliminate the pressure compensation pad and could therefore use our most common mould concept on the market, with an external diameter of 125 mm. This means we are able to blow any bottle size up to a volume of 2,000 mL. It’s a good opportunity for us to optimally serve the market, since 98% of the bottles on the global market are within the volume range of 2,000 mL or less.
CC: Good idea. The pressure compensation pad has long been a necessary evil. Was this a particular challenge for the engineers?
H: Yes, that’s right. Initially, it was the designers who were asked to come up with a solution to eliminate the pressure compensation pad. After that, it was the turn of our production engineers. Implementing the idea was a real challenge in terms of production technology. One thing that really helped was that we were able to build the mould carrier completely in-house, allowing us to optimise the production technologies in our own lines and make significant adaptations to them.
A: With pressure compensation pads, the mould carrier has a movable side and a rigid side. This asymmetrical structure results in slightly different heat flows between the left and right sides of the mould carrier. By dispensing with the pressure compensation pad and modifying the machine accordingly, we get rid of these thermal irregularities, meaning that there is no risk of exerting a negative influence on the neck by shifting the moving half of the mould. And, of course, forgoing the pressure compensation pad also reduces compressed air consumption. For the Contiform 3 Speed, this results in an impressive reduction of up to 15%. H: No longer having to control the pressure compensation pad means gains in process angles. As a consequence, we can run the machine faster. This requires an optimised valve block with fast responding valves. For the mould carrier, it was a matter of eliminating the play and bringing about a kind of ‘self-healing’ in order to get to zero.
CC: Of course, these changes also led to some weight reductions, which reduce the load at high rotational speeds.
H: Yes, but the weight of the bottom mould carrier was a further challenge for our development engineers. One disadvantage at high speeds was the stroke length of 40–50 mm, for instance. What we needed here was weight optimisation. We managed to achieve this extremely well.
CC: What do the process engineers think about the new possibilities that have opened up for you?
H: In terms of process technology, our engineers definitely see even more room for improvement. In terms of blow moulding, we have no problem achieving high performance. We are still working with the same stretch speeds and our well-known electromagnetic stretching system. We have a bigger process angle, and we are translating that into improved performance. That’s what it’s all about.
CC: With all these new mechanical developments, have you changed your entire range of stretch-blow moulding machines?
H: No, we are taking a two-pronged approach. There is something that I really want to emphasise here. While the Contiform 3 Speed is optimised for highperformance applications up to 2,000 mL, the Contiform 3 Pro can actually do everything — including heat setting and large-volume bottles, up to a gallon. However, the output of the blowing station is limited to a maximum of 2,500 b/h in this case. The Contiform 3 Speed only works with the optimised mould concept with a diameter of 125 mm. Anything that fits into that can be blown and produced for standard applications. It cannot be used for special applications, such as bottles with handles or heat-set bottles. You could look at the Contiform 3 Speed as our “worker bee” for high performance, whereas the Contiform 3 Pro provides maximum flexibility. It has more installation space and can also be used with blow moulds with external diameters of 125, 150, 160, and even 200 mm. The Contiform 3 Pro can therefore accept all of the usual blow mould formats on the market. Here the pressure compensation pad continues to play an important role, including for dealing with any differences in play. In principle, the platforms are identical. What is different is the mould carrier, and therefore the blowing station, allowing multiple blowing stations to be accommodated on the pitch circle.
A: I’d like to add that in 2018, we delivered multiple aseptic blow moulding machines that also had no pressure compensation pads. This brings with it significant advantages for aseptic applications. As you saw on the way here, a new assembly hall is being built for these aseptic blow moulding machines and blocks. The number of machines, the required hall size, and the required load capacity for the crane are what made this necessary.
ErgoBloc – at a glance:
• Blow moulding, labelling, filling and capping
• Output: up to 81,000 containers per hour
• Processing range: - Carbonated and non-carbonated beverages - Cylindrical and square PET containers - Standard and lightweight containers - Volume of 0.25 to 3.0 litres - Self-adhesive and reel-fed plastic labels - Flat caps and sports caps
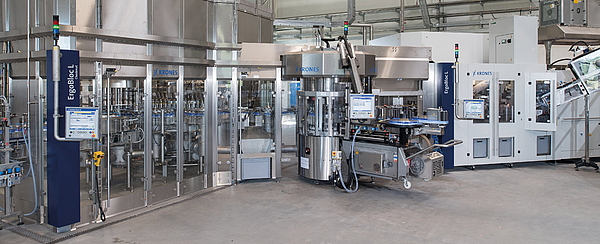
CC: What has changed with regard to the heating module?
H: The heating module is identical in both machine designs, Speed and Pro. When we were creating the new version, the focus was on minimising the radiation space, depending on the length of the preform. This was achieved using base reflectors that can be adjusted in height, thus allowing them to be optimally adapted to the preform length in question. The radiation space has been minimised, which reduces the radiation lost. Actually, we had discussed using mirrored reflectors—after all, such concepts do exist. However, we made a conscious decision not to take this route because we feel it is less suitable for everyday use, and more problematic in terms of cleaning. We have had great success with ceramics, which are extremely advantageous even in the long term as they lose a maximum of 2% of their reflectance over their life cycle.
CC: So the microwave heater that was unveiled at the last K trade fair is not yet ready for use?
A: We currently have machines with this technology on the market. As it is stateof-the-art, it will not be included in our plants for the time being. Microwave heating works well, but, compared to IR, it is still too expensive for the moment. But I am very optimistic that we will be able to unveil a solution that is ready for serial production in a few years.
CC: Could you give us an insight into how the Contiform 3 Speed was developed?
H: Development began about two years ago with the blowing module, the heart of the system. Actually, the blowing station is something of a perennial issue for us in our development work - it keeps us busy all the time. In order to verify the new development, we carried out the initial field tests on customers’ premises relatively quickly. The systems have been in operation for one and a half years now. The actual machine development was done in 2018. Today the machine is already on the market. At the same time, we are checking all quotations to see whether the Contiform 3 Speed can be used. If it fits into the concept, there are benefits for the customer, such as achieving comparable output rates with fewer moulds. The first serial production machines will be delivered in April. We expect the Contiform 3 Speed to be a top seller.
CC: Does the Contiform 3 Speed fit into the modern block concept?
A: The Contiform 3 Speed has been designed very much as part of the block concept. This means it is perfectly adapted to the current trend. The degree of blocking at Krones is about 80%, so there are few individual machines. With the Contiform 3 Speed, we will be continuing the success story that began with the ErgoBloc L. This concept - the 250 ErgoBloc L - (is being installed at Niagara Bottling in Mexico) is what brought about the major technological boost. ErgoBloc L provides stretch blow moulding, labelling, filling and capping in a single block.
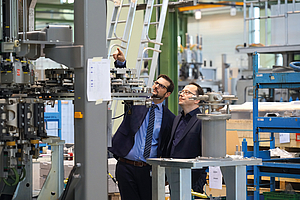
CC: The block concept surely requires some organisational adjustments as well.
H: Indeed it does. The high proportion of block machines made it necessary to introduce a separate organisational unit - Block Technology. It ensures that all the machines in the network run optimally. We foresee a lot of potential in the blocking of functions and tasks. The reorganisation has resulted in concepts and systems such as LineXpress, a comprehensive concept for format switching, in which the systems are also intermeshed in terms of software - in order to optimise consumables, for instance. Here, communication takes place along the line: Industry 4.0. CC: Does this mean the “digital breakthrough” for filling lines has already taken place? H: In the beverage filling industry, it is already possible to find many small examples that could be categorised under the heading of “digitalisation”. There is no doubt that digital concepts for the entire line are still in their infancy. So while we are seeing more and more potential, we are not expecting the digital revolution to come tomorrow. At any rate, the potential is there in the form of trends that could give rise to an integrated digital concept. The advantage we have is that, thanks to our subsidiary Syskron, we can take these opportunities into account at an early stage. Digitalisation is no stranger to us, and one way we have demonstrated this is with Share2Act from Syskron, the digital platform for the networking of employees, machines, and IT systems.
A: Naturally, the Contiform 3 Speed also has a digital aspect. We call it SmartKit. This encompasses functions that can be visualised in an app, for example, thus providing our customers with intelligent diagnostic functions. Software and machinery are the cornerstones of the beverage industry, and we bring them together under one roof. The aim is to use the systems to achieve an even better OEE (Overall Equipment Effectiveness), for instance through very early detection of imminent faults and the ability to react to those faults faster than is conceivable today. The skill of the operators will become less important, while the systems will become more complex. It’s clear that in the future - whenever that may be - there will be autonomous filling lines. The industry is moving further and further away from individual functioning. The focus is on networking, and this is what has to be optimised.
CC: How have the demands coming from the market changed?
A: Ten years ago, the ability to change out moulds quickly was the main requirement from customers. Today, they demand automatic changing - and it has to be smooth and error-free. The MouldXpress Robot, a part of the LineXpress, is the building block that allows the use of robot technology for fully automatic blow mould changing. H: What has also changed is the focus. Before, it was on the main machine. Today, it is on the system as a whole. This means that the sub-systems such as the preforms infeed are just as much in focus, because they contribute to the OEE of the overall system.
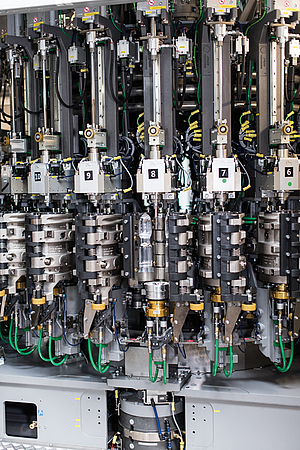
CC: So we can say that, in terms of performance, the Contiform sets the pace for the other machines in the line.
A: Yes, absolutely. This highlights why we are engaged in a discussion about our portfolio as a whole. We need to think in terms of networks. Optimising the mould changing for a single machine is useless if the rest of the system can’t be switched over more quickly.
CC: Do these approaches only apply to large systems? This would mean that the larger bottlers would be able to enjoy all of the advantages, whereas the smaller ones would have more and more difficulty exploiting the technological and therefore economic benefits.
H: With the Contiform 3 Speed, the focus is firmly on the high output range. We have the lower output range covered with our Kosme systems. And let’s not forget other technologies such as aseptic blow moulding machines. We have now extended this portfolio to the low output range with the 6-, 8- and 10-cavity blow moulding machines. So we have outstanding solutions here, too. A: The robot concept MouldXpress Robot was developed for the Contiform 3 Pro. Back then, we had ruled out the use of this concept for format changes in smaller machines. However, we realised that the break-even for using robot technology, or for our LineXpress, had to be considered on a case-by-case basis. In smaller systems that are operated with frequent format changes, it absolutely makes sense in individual cases. We installed a LineXpress application for one customer, a filling company in Austria, more than two years ago.
CC: We have talked extensively about the filling line as a system. Let’s go one step further. How does injection moulding fit into this concept? What’s behind the acquisition of MHT?
H: Now, along with our MetaPure PET recycling system, MHT is an important building block for us in terms of the circular economy - the preform is the link between the material and the bottle. We also asked ourselves: where are the synergies? How can we close the loop? The combination of preform and bottle seems particularly relevant in the context of RPET. We are now in a better position than ever to shape things in this area. This is important because we want to offer the best possible solutions. We are closing the technological loop, so to speak. For application technology in particular, it is of course useful to have this expertise within the group.
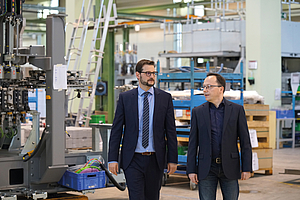
CC: Will this lead to in-house development of injection moulding machines?
A: No. Instead, we want to be able to offer our customers a comprehensive service for the project planning and development of new injection moulding systems. We already have a suitable partner for this in the form of IPS in Switzerland.
H: For us, an injection moulding machine based on standard technology is a nonstarter and not something we would be interested in getting into. If we were to do so, then there would have to be a paradigm shift with regard to the technology. But, as I said, that is not the reason MHT is on board with us.
CC: While we’re on the topic of injection moulding technology: is there anything new at Krones in terms of multilayer or barrier technologies?
H: We work with the entire system in mind, which means that we also take barrier technology into consideration. At the moment, and in particular in light of the demands of recycling and the circular economy, we think coating technology shows more promise than multilayer, so that’s what we’re working on.
CC: How do you see the future of PET packaging?
H: At Krones, working on solutions is what we do. High speed and environmental protection absolutely complement each other, as we have noted in our talk. We are responsible for what comes out of our machines. The products - i.e. the bottles - must be top-quality. For the filler, the consumer, and the environment. More needs to be done about the next stage, after our job as a machine and equipment supplier is complete: collecting, so that what has been used can be reused - over and over again. We have a lot of ideas and we hope that we will be able to unveil some of them at the K trade fair this year. There is still more room for improvement.
CC: That all sounds very exciting. Many thanks for talking to me.
The comPETence center provides your organisation with a dynamic, cost effective way to promote your products and services.
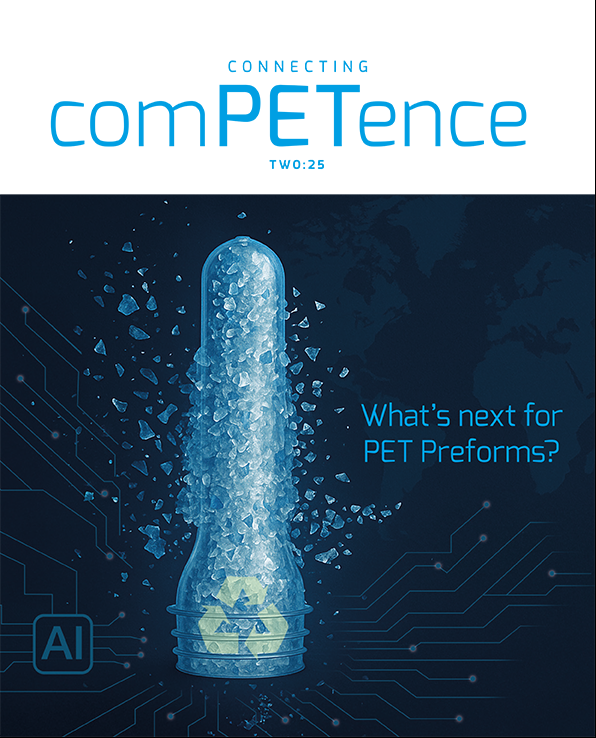
magazine
Find our premium articles, interviews, reports and more
in 3 issues in 2025.