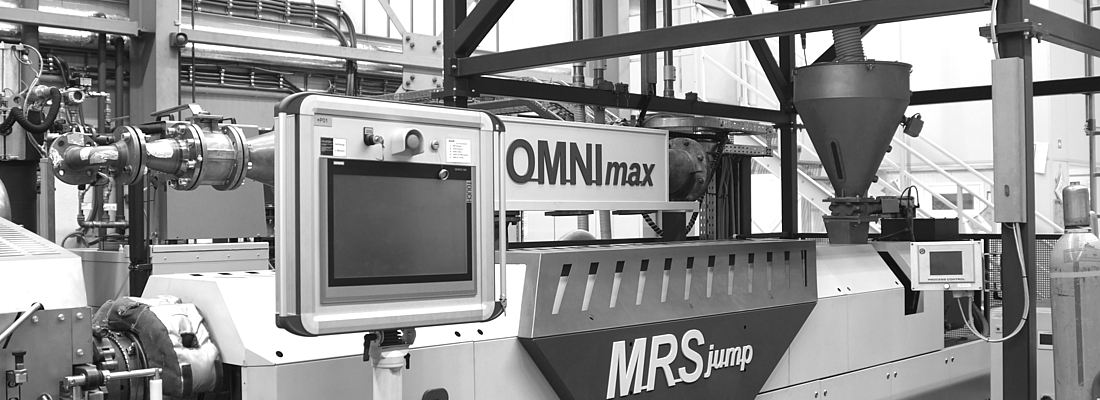
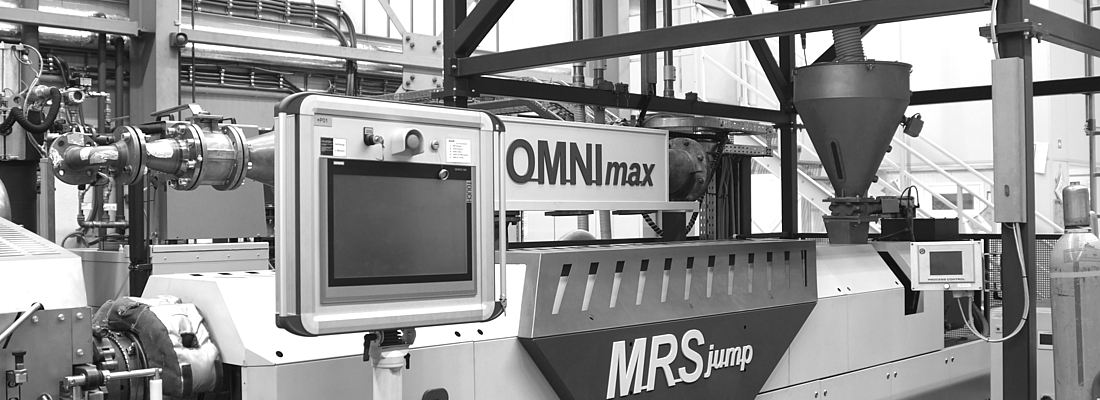
PLASTIC RECYCLING
Gneuss - Plastic Recycling - We could do more and faster - Meeting with Gneuss Kunststofftechnik on innovations and investments in a challenging time and environment
When it was founded in 1983, the family-run German company Gneuss Kunststofftechnik focused on the development of innovative extrusion lines and systems. Today, Gneuss has more than 100 patents, a subsidiary in the USA, branches in Brazil and China, a cooperation partner in Japan and worldwide representatives. Gneuss Kunststofftechnik describes itself as a technology leader in the extrusion of plastics and plastic waste of all kinds. With its business units POLYMER TECHNOLOGY, TURNKEY SOLUTIONS and MEASUREMENT TECHNOLOGY, Gneuss offers turnkey solutions for the production of films, fibres and pellets.
The focus of our meeting with Dr Stephan Gneuss (Managing Director), Dr Axel Hannemann (Head of Business Unit Fiber and Pellet) and Andreas Hunold (Sales Manager) is the new OMNIboost recycling system for processing PET and other plastics from industrial and post-consumer waste. But our conversation is not only about engineering and technology - as so often in recent times, since crisis management does not just mean troubleshooting. And Stephan Gneuss puts it in a nutshell: “The clear motto for business meetings used to be: no religion, no politics; today you can’t avoid taking a position.”
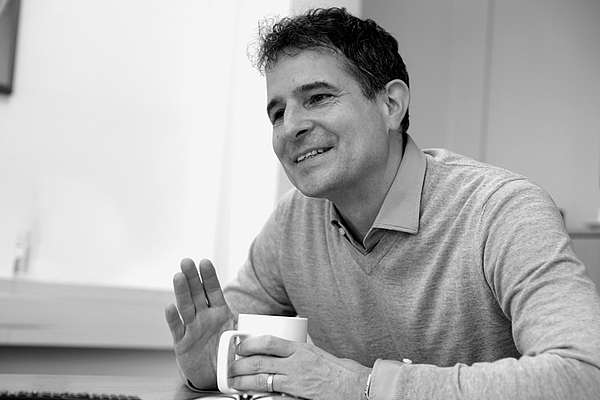
Space is getting tight at the headquarters in Bad Oeynhausen: in addition to the administration building, the production centre, the development department (engineering design and technical development) and one of the two technical centres for customer trials are located here. A second technical centre with a focus on PET processing was installed a few kilometres away. A new assembly and production hall is under construction at the headquarters.
So it’s going well at Gneuss – isn’t it?
Gneuss: Yes, you could put it that way... As you can see, we are expanding. However, there are many uncertainties at the moment. It starts with the world crises, their impact on supply chains, material availability and staff shortages, and extends to the political embedding in Germany and the EU. From a technical point of view, we are very busy with approval procedures, especially in the recycling of food contact materials and food packaging. We feel thwarted in Europe and are certainly not the only ones in the industry. But we are continuously developing our technologies; the demand is immense and will continue to increase.
_______________
''We are very busy with approval procedures, especially in the recycling of food contact materials and food packaging.'' - Dr. Stephan Gneuss
_______________
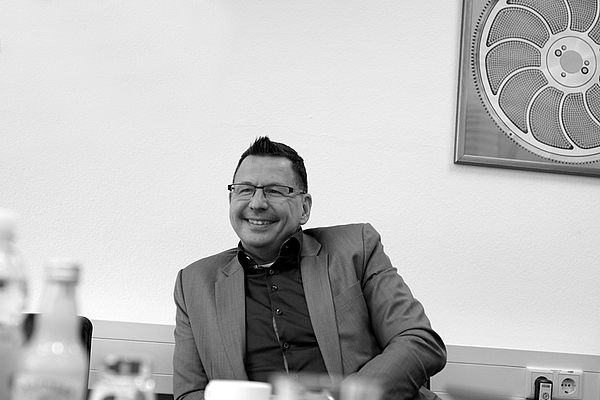
Recycling is currently the top topic in the plastic packaging industry and is nothing less than the essential step towards the circular economy and sustainability. In this environment, a technology specialist like you feels thwarted by approval procedures!? Can it really be that approval procedures for recycling processes and technologies take too long?
Gneuss: Let me explain this using the example of polystyrene recycling for food contact. Already ten years ago, we sold a plant for the recycling of polystyrene for food packaging to a customer in Japan: Challenge tests had shown that our plants are suitable for processing postconsumer polystyrene into recycled material for food contact. The American FDA issued us with a corresponding LNO. In South America, our equipment is also used to produce food packaging from recycled polystyrene. At the European EFSA, the evaluation process has still not been completed.
Hannemann: We again carried out challenge tests for polystyrene recycling - with excellent results from our point of view - and applied for approval from the EFSA. We expected it to go quickly, and the process apparently got off to a good start, because EFSA immediately asked questions, which we were able to answer quickly. But now EFSA is letting us down and unfortunately, the arguments are far from clear. All in all, this means a long wait for polystyrene recycling in the food sector in Europe. And there is concern that developments will also not be pushed forward if there are no positive signals regarding approval. It seems that anything that is not PET has little chance. EFSA distinguishes between “existing” and “new” recycling processes. “Existing processes” are those that existed in the field of mechanical PET recycling before the EFSA Regulation on recycled plastic materials came into force. All others are considered “new technologies”. And the criteria for evaluating them probably need to be precisely defined first.
You don’t have to reinvent the wheel, but it’s still not easy?
Gneuss: My impression is that plastic simply has no lobby in the current political processes, so that it is disadvantaged in the regulations compared to other materials. If it can take up to seven years for EFSA to complete its safety assessment for a recycled food contact plastic product and for the European Commission to approve the process, then of course that is an investment blocker. It is hard to imagine that recyclers invest in new plants without knowing whether they will be allowed to operate them permanently to produce the intended packaging. And that coupled with very high quotas for the use of recyclate in new plastic packaging! It doesn’t make any sense. It doesn’t look like it at first glance, but: On the one hand, the producers are forced to use a significant proportion of recyclates in their packaging; on the other hand, it is not ensured that the material is available in sufficient quantities. In addition, no secure legal basis is established that allows the use of such recyclates. Another problem is: There is no other type of packaging than PET bottles with such a high volume of homogeneous polymers. It is to be feared that, as a consequence, plastic packaging will be displaced by other packaging materials, even if these are ecologically and economically disadvantageous.
Is polystyrene more critical or less critical than PET in terms of purification and degradation mechanism?
Hannemann: Chemically, polystyrene is much easier to process. At some point, every polymer degrades if you thermally treat it too often. But there is no hydrolytic degradation reaction with PS as with PET. It’s all relatively simple, which is good for the recycling process itself. Nevertheless, monomers - styrenes - can arise and evaporate during the processing, but we have them under control with our degassing technology. Of course, the styrenes must not get into the food.
Where do you currently see plastics recycling?
Gneuss: From a technical point of view, it’s clear: plastic recycling for packaging has enormous potential. The industry already offers the solutions – as described for polystyrene, also for polypropylene and HDPE. And for PET anyway. I assume that common sense will prevail, not least because Europe is not an island. We are in competition with other continents, there are imports from other countries. There is a risk that the regulations will be watered down, which would be a shame - because we recycling specialists know what we are capable of.
_______________
''From a technical point of view, it’s clear: plastic recycling for packaging has enormous potential.'' - Dr. Stephan Gneuss
_______________
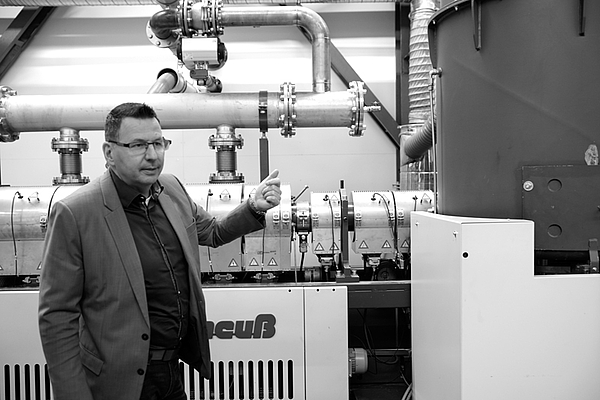
You talked about political hurdles. Where would you like to see more support from politics and politicians?
Gneuss: Of course we have our challenges, and support would do us good. We family entrepreneurs are suffering from the enormous energy prices. At Gneuss, this applies in particular to the steels; they are all hardened and nitrided. We need gas for that. If we run out of gas - and the risk was looming just before winter, when Germany was discussing the filling levels of the gas storage facilities - we will no longer be able to produce. This is not a global problem; it is a European problem - due to dependency structures that we have created. Now to your question: A politician from our region recently put it in a nutshell: As long as tax revenues are high, the threatening situation will not be noticed. But the situation is threatening for many companies, and I sense that once the momentum picks up speed in the wrong direction, it is difficult to stop. We talk about it in entrepreneurial circles and associations, too: so many are toying with the idea of job relocation. The topic has never been on the agenda so often. Further burdens for the domestic industry: high production costs, lack of employees, high level of regulation. Other regions lure with attractive tax options. My concern: once these jobs are gone, they won’t come back.
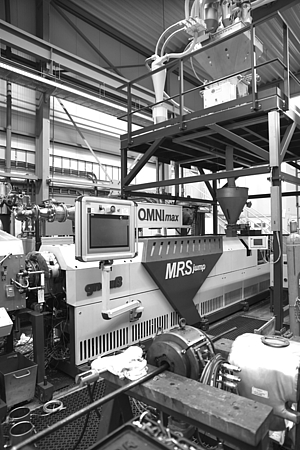
All of theses issues involve major challenges and keep you extremely busy as an entrepreneur. On this basis, you still need to focus on engineering and technology.
Gneuss: That is indeed the case. One example is our new assembly hall that I mentioned earlier, which is intended not least to make our development processes even faster and more efficient. All in all, the conditions for investors in Europe are not good at good. But in my perception, capacity expansions in the packaging sector are rather rare in Europe at the moment. I don’t know the current turnover situation of the manufacturers of film lines in detail - they are coming from quite a good level - but I do notice that something is threatening to be lost in Europe. And we can only hope that the markets in America and Asia will become accessible again.
What are your strongest markets?
Gneuss: It used to be roughly one-third each for Asia, Europe and South America. Due to the pandemic, Asia has become extremely difficult. In America, both in North and South America, we are very well positioned - which actually few companies in our industry can say. In South America, in particular, many are struggling. Thanks to our highly committed staff, we have built an excellent office there. The business there is different from ours: many small plants, almost all family businesses and only a few large companies. North America, one would think, is developing well under President Biden in the recycling sector. So far, however, this has not been the case as hoped, and the pandemic did the rest. The subsidy package the US government presented last summer, the Inflation Reduction Act, aims, among other things, at climate protection and recycling. This should have a positive effect in the coming years. It has yet to be passed in Congress, but if it is implemented this way, I think we also have great opportunities in North America.
How do you see the development in Europe?
Gneuss: For Europe, I am - frankly speaking - skeptical. I don’t think much will happen in the short term. The euro could lose further stability; energy costs and the inflation rate seem to remain high because we can’t take countermeasures. Politicians are well aware that raising interest rates to 5% or more would threaten many EU countries with high levels of public debt. And since we are desperately trying to keep the EU together... I fear that this could be a long-drawn-out affair.
And China?
Gneuss: The Chinese market is now developing again. I wouldn’t have thought this possible a few weeks ago, but it seems to me that some kind of energyzer is waking up the market. If only it weren’t for the Taiwan conflict. It has to be said: it would be a bitter setback not only for the German economy if China closed down because of the Taiwan conflict. If the USA sides with Taiwan, Germany will not be able to do business as usual with China. We are currently receiving many enquiries from China and Taiwan again, and my first business trip to Shanghai for new cooperations is already planned. Let’s see. All in all, there are big global challenges at the moment. Let’s work on - and hope for - a positive future.
How is Gneuss positioning itself strategically?
Gneuss: From our origins we are machine manufacturers, but today we see ourselves mainly as system suppliers. This offers enormous potential for our technologies. I see EREMA as an example, and I greatly respect them for their economic development. I don’t mind saying that because I think they have done a lot for recycling in general and have also developed very well as a machine and system supplier. But I have to add that, from a technical point of view, I see things in a more differentiated way and from a different perspective. Technically, we at Gneuss, have achieved an outstanding position in many areas over the last few years, and we can be very proud of this. What does that mean for us? We will continue to grow in the filter sector. But: We could significantly increase our turnover in the next five years if we continue on our path in the field of system solutions. Our technical treasures have many advantages to offer.
_______________
''From our origins we are machine manufacturers, but today we see ourselves mainly as system suppliers. This offers enormous potential for our technologies.'' - Dr. Stephan Gneuss
_______________
Do you still see potential for the polyester market?
Gneuss: In classic bottle-to-bottle recycling, the market is certainly already well developed, even if it has recently been a growth market again. There are few new entries and many established processes.
Compared to PET bottles, the recycling of other products such as trays or textiles is still in the starting blocks. Is this a potential market and a strategic focus for Gneuss?
Gneuss: Yes, I see a lot of potential in thermoformed products, films, and fibre recycling. Shockingly little is being done to recycle these products. Fibre production plants have 1 to 3 % waste due to start-up processes and scrap production but only a few producers currently recycle their post-industrial waste themselves. From our point of view, this makes total sense, and that is why we have developed technical solutions specifically for these cases. The clothing industry needs to think more in terms of “design for recycling”, because mixed fabrics, such as polyester and cotton, cannot be recycled. It is only a matter of time before public pressure hits the textile industry. Plastic consumption is similar to that in the packaging industry. If you look at the lifespan of textiles: fashion changes super fast. You could say garments are like one-way packaging, exaggerated.
Hunold: Our technical solution for fibre recycling, also for films and other post industrial and post consumer plastics, is our OMNIboost system. In our technical centre we are currently processing textile tufts.
Gneuss: Our newly developed cutting compactor offers new options here. We have also worked on the process and the entire control technology. The first part of the melting takes place in the cutter compactor and the second in the extruder. Degassing takes place partly in the extruder, and if there is a JUMP reactor in the system behind the extruder, the final degassing of the material occurs there, and the viscosity is significantly increased.
Hunold: Currently, our challenge is to match the processes for the specific application to achieve an ideal result. We have invested a lot in various systems for this purpose. Our development focus is to feed different materials and find the right level of already melted and starting to melt material. In all other areas, we are already very far in development and are now working on nuances. At the end of the year, we want to demonstrate our technologies for difficult materials live in an open house - ideally with FDA and EFSA approval.
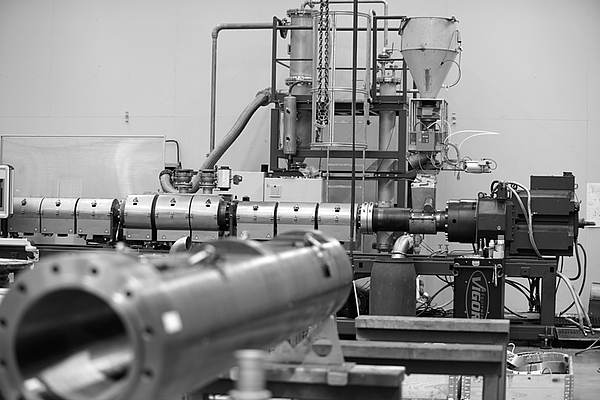
Where does Gneuss stand when you compare your technologies with the competition?
Gneuss: One of our main USPs is: Nobody has such a continuous and trouble-free wire-based filtration system as we do. This stands for high filtration performance. For everything below 100 µm, there is no more efficient and trouble-free filtration system in the world. Our sales figures are good, quite simply because our customers have no process disruptions despite the increasing proportion of recyclates. Our second USP: Nobody degasses as efficiently in the melt phase during the extrusion process as we do with our MRS system. The system was optimized precisely for this. We don’t shy away from comparison with anyone. Thanks to our patented technologies, we are a system supplier in the high-end sector, and it is therefore our task to transfer the customer’s product-related requirements into a technical process that achieves the required result. To come back to your initial question: Yes, Gneuss is doing well - and with our orientation as a system supplier and our technologies, we are on a good path.
We thank you very for this interview and the insights into Gneuss Kunststofftechnik.
The comPETence center provides your organisation with a dynamic, cost effective way to promote your products and services.
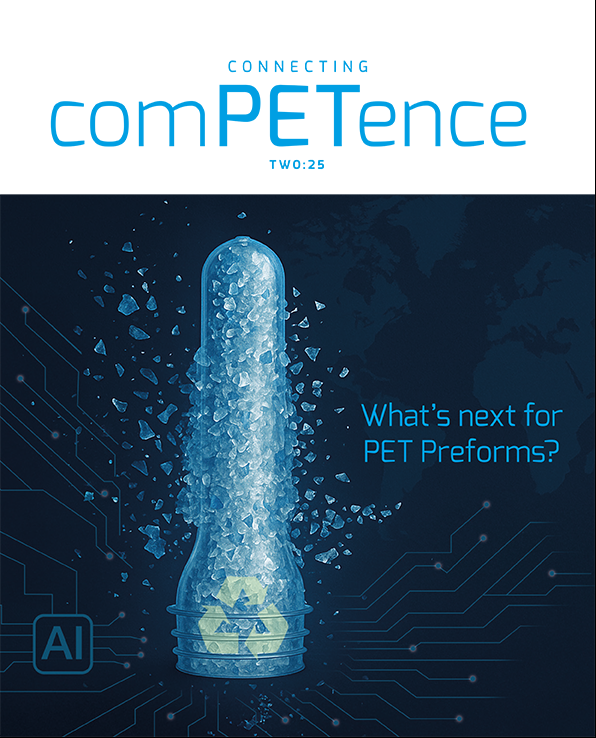
magazine
Find our premium articles, interviews, reports and more
in 3 issues in 2025.