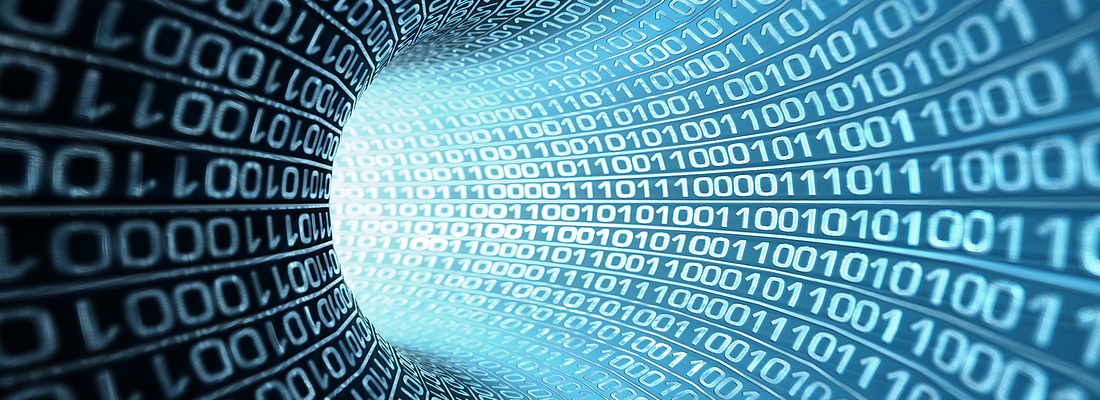
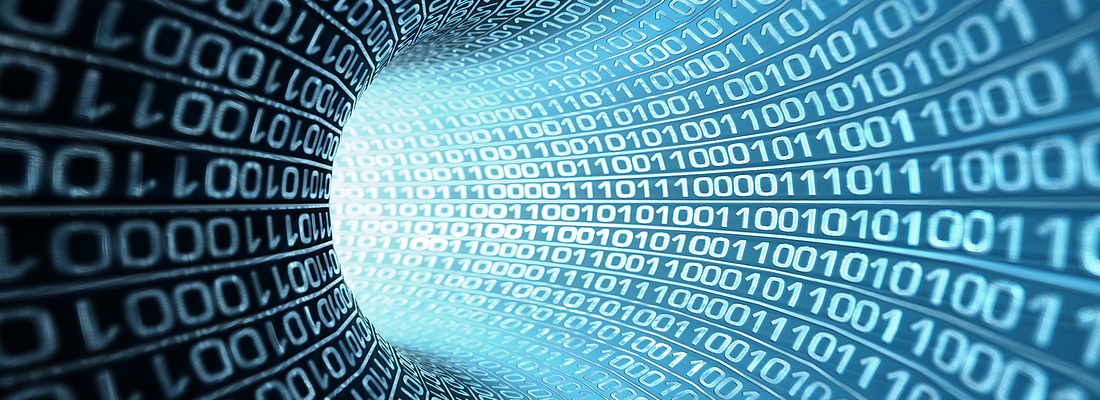
Smartphones, tablets, smartwatches, the internet and – of course – social media: constant availability, monitoring and networking have become almost indispensible parts of our daily lives. Why would it be any different in business and industry?
The magic word is Industry 4.0. It has been looming over the whole industry including the drinks industry since the Hanover Messe trade fair in 2011. But what exactly does the fourth industrial revolution mean? And to what extent has it already found its way into everyday technical life? At the 19th PETnology Conference, PETnology posed these questions to some conference participants. They found that whilst some aspects are already a matter of course, the industry still has a long way to go until widespread implementation.
Industry 4.0 works towards the concept of the Smart Factory, which is characterised by adaptability, resource efficiency, ergonomic design, the integration of customers and partners into business operations and the value added process. Cyber-physical systems and the “Internet of Things” (IoT) form its technical foundations. But the discussions showed that even though the concept has been defined, each company has different priorities for the implementation of Industry 4.0.
If you think about fuzzy-logic systems or remote-control units, it is clear that Industry 4.0 has already entered almost every business on a small scale. Piet Vlaminck, General Manager North, Central & Eastern Europe at Husky Injection Molding Systems Ltd., Luxembourg, has gone a step further and says: We have already made an important step in the direction of Industry 4.0. Our customers have been working with a central network, connecting all the units of a plant, for several years. The units are monitored, all production data is collected and customers can make long-term observations of quality which has a direct link to resource efficiency and which is the first step toward adaptability of production.”
Stefan Bock, Manager of Application Technology PET Systems by the Netstal-Maschinen AG from Naefels in Switzerland has to report: “Since 2014, we are implementing processes for networking and monitoring all plant components and peripheral equipment. This helps us to maintain a maximum level of security, where the processor can identify potential defects quickly, or ascertain whether measures such as maintenance or component replacement are necessary.”
Unlike the two representatives from injection moulding machine manufacturers, many conference participants reported that whilst the industry is well on its way towards Industry 4.0, many steps are still necessary to actually implement true connectivity, flawless monitoring and performance management. Whilst the necessity does not always seem obvious to small and medium-sized processing companies, large businesses require continuous and structured implementation. Integrating old plants into new systems can be bound up with difficulties, though. “It is not always possible to exploit existing potential,” reports Markus Juppe, Director of Sales at Intravis GmbH in Aachen. His company manufactures optical monitoring systems for preforms, bottles and caps, and would be able to increase production if such structures were in place.
In conversation with many visitors at the PETarena booth at the BrauBeviale 2015, it becomes clear that the technical potentiality for the implementation of Industry 4.0 or use of digitisation are already in place. It also becomes clear, that many companies have already moved into the digital era. Unlike the automobile industry which is already quite advanced in terms of vertical integration, the beverage industry seems to be more conservative and restrained.
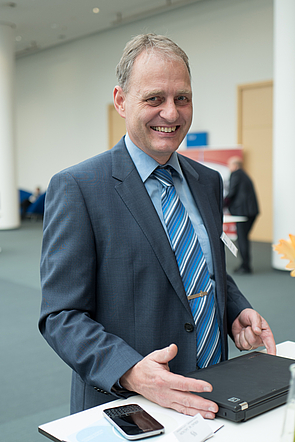
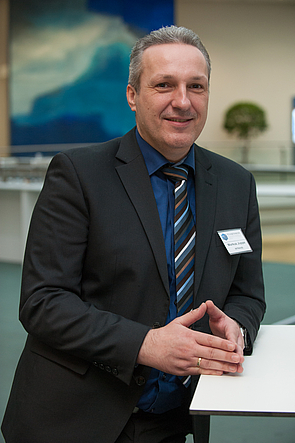
Stefan Bock, NETSTAL Markus Juppe, INTRAVIS
horizontal and vertical integration
Some divides digitisation into horizontal and vertical integration. Vertical integration refers to cyber-physical systems which connect the software components to the mechanical and electronic parts.
Horizontal integration describes the constant monitoring of a product from production through to after-sales service using appropriate software tools. This horizontal integration ensures a reduction in the engineering outlay and a shorter time-to-market.
Whilst horizontal integration has already been implemented in many companies, particularly in the beverage industry, vertical integration still has a long way to go.
safty
As soon as any company-specific data is stored on the internet or in the Cloud, questions about safety must be asked. For this reason, Arthur Kramer from Sumitomo (SHI) Demag Plastics Machinery GmbH in Schwaig points out that a company must ward off hackers, since it is theoretically possible to manipulate plants from the outside, and consequently for competitors to create advantages for themselves.
It is clear that Industry 4.0 is a hot topic in the industry and will surely remain so in years to come. However it is still unclear how it will be integrated into the day-to-day reality of production, and how far each company will go along the path of digitisation. Thorough preparation and careful consideration of the advantages and disadvantages should be made on a case-by-case basis.
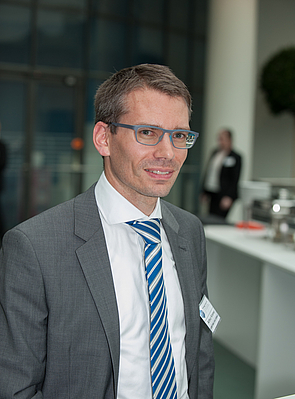
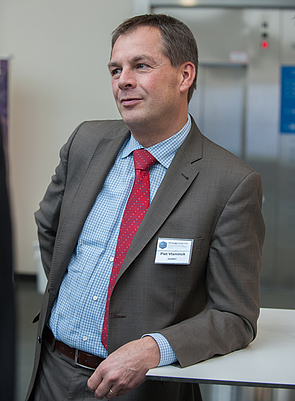
Athur Kramer, SUMITOMO DEMAG Piet Vlaminck, HUSKY
The comPETence center provides your organisation with a dynamic, cost effective way to promote your products and services.
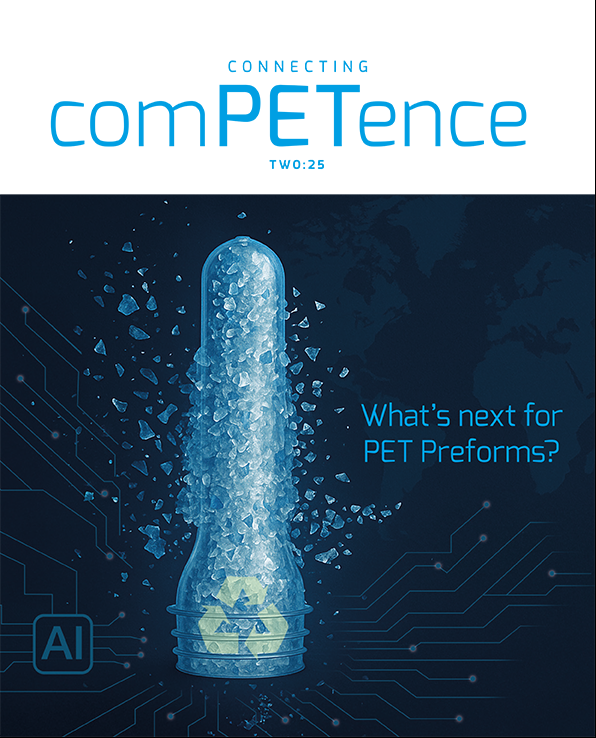
magazine
Find our premium articles, interviews, reports and more
in 3 issues in 2025.