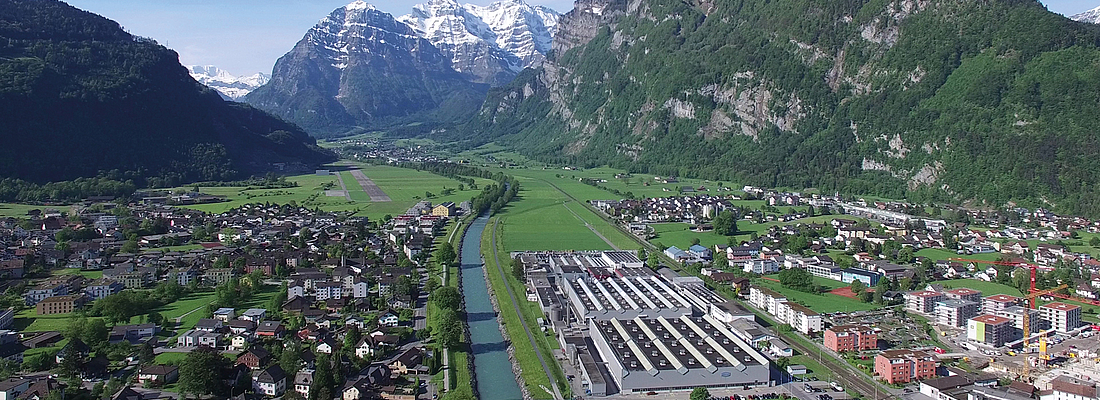
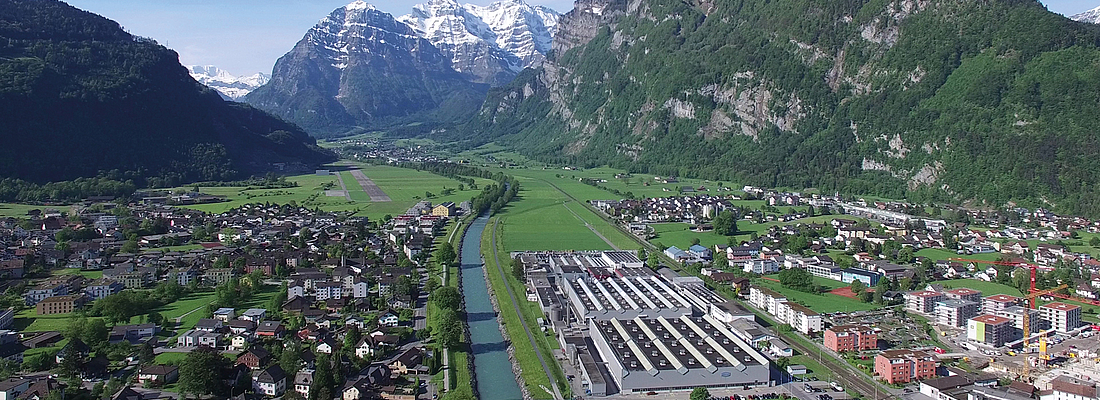
There are sometimes special moments in the PET packaging world. Moments in which developments are presented. When I received the invitation for the introduction of the new NETSTAL PET-LINE, I sensed that this was one of those moments, that a new era could begin.
I felt it right away, on the way from the reception on the Näfels factory premises to the production hall: pride. And the joy that was written on the face of the Netstal team, as radiant as the blue sky behind the incredible alpine backdrop. The team wanted to share both pride and joy with us on that day.
Chapter 1: An observer‘s perspective
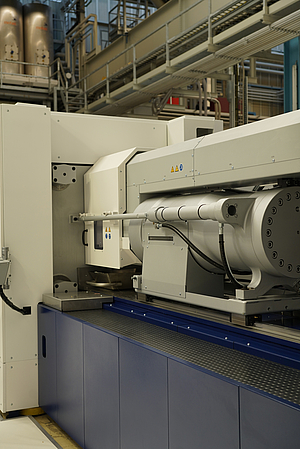
Fit to battle
The joy of one’s ability, of measuring oneself with pride and conviction and yet being in harmony with the team, create innovations. Perhaps one or the other reader knows this excellent saxophone piece “Fit to Battle”, which Kirk Whalum plays with his father and son*. Three saxophonists, enthusiastic about what they do, who set their accents in the solos and inspire in their interplay.
Somehow, I can see parallels to the “music” that plays in the PET packaging world: Enthusiasm leads to top performance; only the top-level lives up to the expectations. The requirements are the same for all players: playing a piece together in terms of sustainability of PET packaging, but also shining as individual players and setting accents. A competition with the same instruments, on a common stage. Side entry. Fit to battle.
This is about emotions, isn‘t it?
As a technician, you try to look at things soberly. From my point of view at NETSTAL, it was relatively calm until our meeting today. I’ve noticed it that way since I met Renzo Davatz in the summer of 2017 on the occasion of our interview (see comPETence, THREE:17). I know the circumstances, at least in part, and can imagine that it was not an easy time. Decisions were pending; the name NETSTAL was on the brink. What does it mean for a company, for every single employee, when you have lived NETSTAL - for many years - and suddenly the NETSTAL company sign on the hall is dismantled? That causes uncertainty, disappointment, challenges and hopes. Employees leave; you have to strive to find new ones. Add to that the tension in the market.
_________________________________________________
''There is no getting around Netstal.'' - Renzo Davatz
___________________________________________________
With all of this, there was also this big project, a topic - supposed to turn the NETSTAL world upside down: a new PETLINE, a PET-LINE with side entry. Against this background, I think there must have been a lot of emotions and discussions, even today. I am looking forward to today.
Renzo Davatz confirms my assessment. Yes, it was demanding; it also hurt. He doesn’t want to gloss over anything. He speaks of a “guiding star” that you needed to help you find your way in a storm. That helped to recognize that the Näfels location is justified for PET. According to Davatz, the new PET-LINE became this guiding star. Davatz and his team have worked - in concerted action and with full motivation - to ensure that this motto will also apply in the future: “There is no getting around Netstal”.
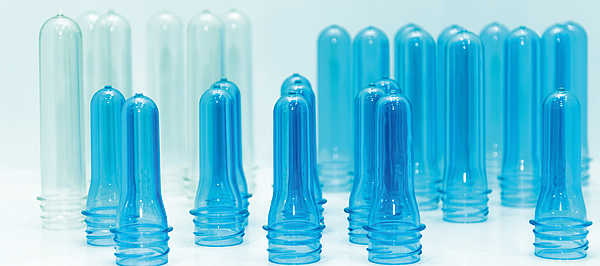
The internal presentation of the machine took place a few days before our visit. A highlight, so to speak, for the entire staff: “side entry” was a “no go” in the NETSTAL world in the past. Now everyone was talking about “side entry” - no longer just the narrow core team that was involved in the strategy, development, construction and production of the new PET-LINE. To see a new PET machine - that even breaks with the old philosophy - to see an all-new PET-LINE, to hear it and to be able to touch it when it is in production for the first time, that is a significant moment for both doubters and pushers. Good signs for a good start.
Chapter 2: Milestones in the company‘s history
Know-how in PET injection moulding
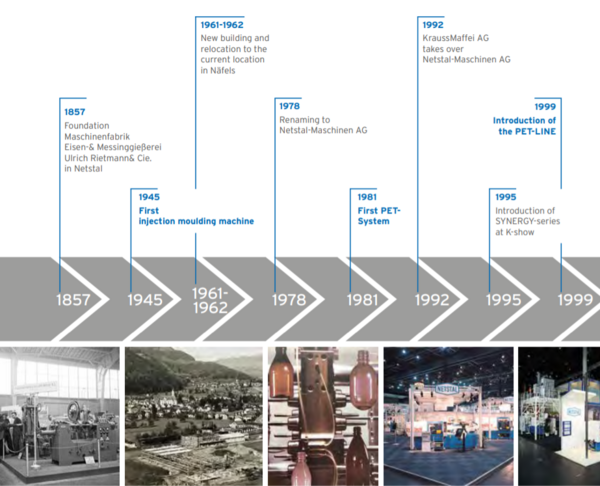
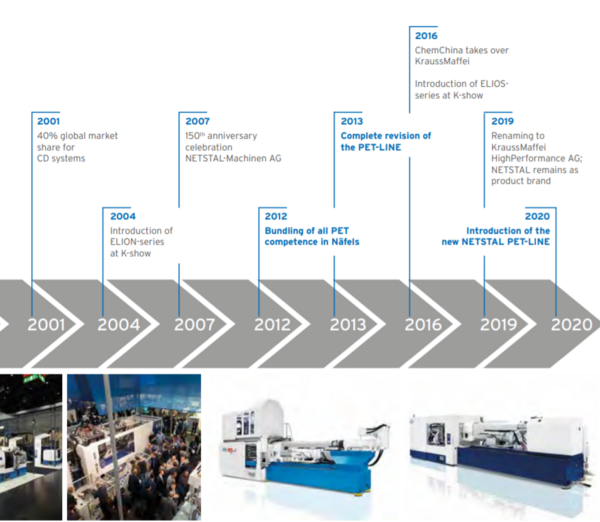
Chapter 3: The PET injection moulding market calls for a strategic decision
Change of direction
In the core segment of PET application, the global CSD and water market, side entry to pick up the preforms from the mould has become established in the high-performance area of PET preform production. This concept accounts for around 80% worldwide and amounts to 500 to 600 PET systems with mould sizes from 48 to 144 times for the beverage market. The NETSTAL PETLINE has not been part of this area until now. (see fig. 1)

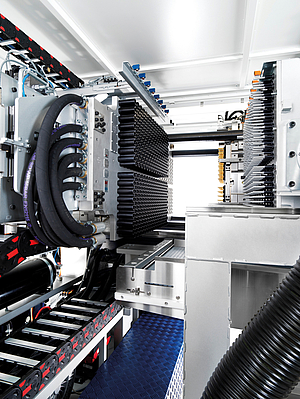
The main difference in the mechanical engineering concept of the established machine suppliers lies in the pick up and tack out system of the preforms. KraussMaffei removes from the rear with the PETForm and from above with the classic PET-LINE, with the advantages of a small footprint. The new PET-LINE now follows the side entry concept to take out the prefroms, as do all systems of the other competitors.
There is no compatibility among the different take out mechanisms: A top removal mould cannot - as of today - be used on a machine that works with side removal. There are various reasons for this: the differently structured moulds, the specific post-cooling stations, robot systems as well as the different tie-bar spacings and ejector positions on the machines.
Netstal consequently has a significant problem with substitution in the new machine business and only a basis for the follow-up business in traditional areas. On this basis, Netstal cannot generate sustainable growth in the PET area with top entry systems alone - and thus, a growth problem.
For Netstal, the market has set the tone to move into side entry technology and leave the path that has shaped the brand.
Chapter 4: A “No-go” comes down
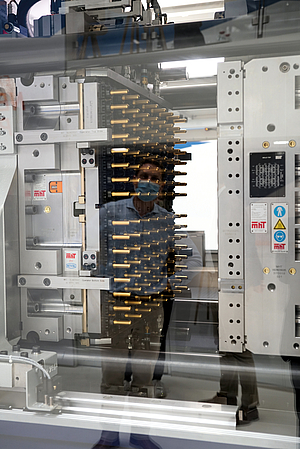
Decision
Preform manufacturing is a mature technology. Quantum leaps through new technologies or concepts are not on the horizon, and NETSTAL does not have a disruptive preform concept in mind, which in the short term - in whatever way - achieves 50% higher emissions with even lower energy consumption.
So a “no-go”, set for a long time for the further development of the PET-LINE, has been dropped at Netstal: Side entry instead of top entry. With this decision, creative space is free for ideas towards NETSTAL’s new path.
After the market analysis, the competitive situation came into focus; the team dealt critically with its strengths and weaknesses, exchanged ideas with customers, partners and suppliers; all of this driven by translating the knowledge gained into technically innovative and, above all, customer-oriented solutions.
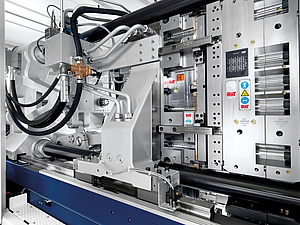
So far this is nothing new and and goes without saying with new developments - but if you make a fundamental change of direction, like NETSTAL, and leave your own, established path, it has an extraordinary significance. Davatz clarifies: “You have to join the side entry market uncompromisingly and without taboos. And: You have to create added value for the customer and not a competitive copy.”
For Eric Overbeek, Vice President Global Sales, this is also important: “With all changes, we have to keep an eye on the “100% Netstal” brand image. For many customers, the NETSTAL logo is essential on the machine, because like nothing else, it conveys the NETSTAL performance promise: speed, precision and reliability.”
____________________________________________
FACTS & FIGURES
MACHINE PROGRAMME
PET-LINE 5000 - max. 144 cavities - coming soon
PET-LINE 4000 - max. 128 cavities - clear width: 928 x 928 - lock-to-lock-time: 1.9 s
PET-LINE 3000- max. 96 cavities - coming soon
PET-LINE 2250 - max. 72 cavities - coming soon
_______________________________________________
A system approach and partnerships in the supplier environment play a crucial role in PET injection moulding systems, unlike other plastic systems. Quality and performance are not only due to the interaction between machine and tool, but everything depends on each other: machine, mould, robot, cooling system, material pretreatment, dosage, dehumidifier, etc. must be perfectly coordinated to develop an optimal PET preform production cell. In some cases, competitors have more peripheral devices in their portfolio, such as tools, hot runners, etc. In-house equipment may allow stronger networking with the machine.
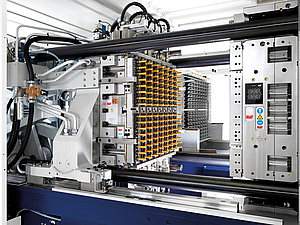
Stefan Kleinfeld, Product Manager for the new PET-LINE, emphasizes the importance of the partnerships for the efficiency of the system: “We have never just developed and built an injection moulding machine. No, from the beginning, we always involved our partners - such as MHT, Otto Hofstetter, Eisbär, Piovan and other peripheral manufacturers - to work out together the optimal preform production cell as a team. So, in our showroom, we display our new PET-LINE and show - together with MHT, Piovan and IMD Vista - what is possible in an innovative preform production cell.”
_________________________________________________________________
''We have to join the side entry market uncompromisingly and without taboos. And: We have to create added value for our customers and not a competitive copy.'' - Stefan Kleinfeld
__________________________________________________________________
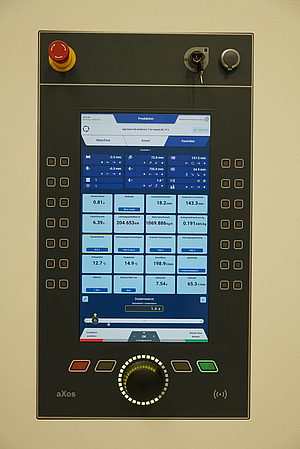
Today, preform producers on bottler or converter side run their systems with 97 - 98% efficiency. Even at this high level of technical performance of the preform systems, the challenges are the same as they have always been: How do we enable our customers to achieve even higher availability and also to produce more costeffectively? Refinements and innovative ideas continuously lead to an increase in machine availability and a reduction in energy consumption in production. Of course, the new PET-LINE also pursues these goals.
Overbeek: “We want to grow massively and double our PET market share in the coming years. And we don’t achieve that simply because we are now also relying on side entry. What we need are USPs, features that, given the current state of technology, no one else has on offer.”
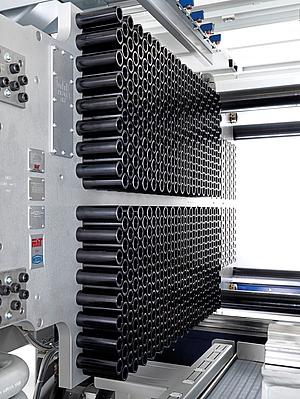
Real comparability
Highest availability, lowest preform costs - that’s what everyone says! I want to know exactly where are the differences. How big are they and who is the benchmark or best practice in the market?
The PET-LINE team does not evade. “We didn’t want to compare apples with pears,” says Davatz. “The comparison is successful when we work with the same preform and the same material. What we were able to do, with excellent comparability: PET-LINE new with sideentry versus the established PET-LINE with top-entry.”
____________________________________________________________
''We want to grow massively and double our PET market share in the coming years.'' - Eric Overbeek
____________________________________________________________
“In terms of energy, we know that the PET-LINE top entry was the best machine on the market,” adds Kleinfeld. “The new machine is even better in this area. We celebrate these measurement results, of course, as they set the standard for competitiveness. Now nothing prevents using tools from the side-entry world. Not with us and not with our customers either.”
The team continued the comparison between the new and the previous system, checking all topics and influencing variables point by point with regard to customer requirements. “You know where the machine stands compared to the competition” and, according to Davatz, you can anticipate reasonably how the new PET-LINE compares to the competition concerning the main customer requirements:
- Low mould wear
- Compatibility in the footprint
- Compatibility in the mould
- Compatibility in the post-mould cooling stations
- Short cycle times
- Low energy consumption
- High availability & easy handling
- Safety
Chapter 5: The new PET-LINE
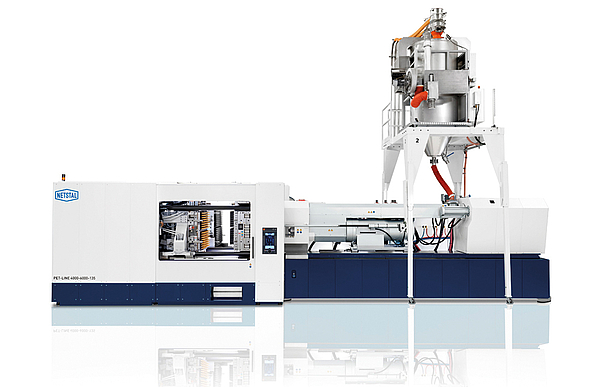
Details
Based on the challenges that have been worked out and described, the aim is to deliver turnkey systems under the NETSTAL brand - as in the past 20 years - by avoiding compatibility problems and with a significantly higher degree of networking and integration. The new PET-LINE has been in development for about three years, the microsite has been providing initial customer information since May, and the official promotion and release of the machine began on September 15, 2020. Two prototypes are already running in the customer test field.
Before Stefan Kleinfeld, professional for the technical features, goes into the details, Davatz proudly announces: “We can state that here: The new PET-LINE will be the machine for standard PET preform injection moulding. The competitors will orientate themselves on this machine It will take some time before they achieve this new performance.”
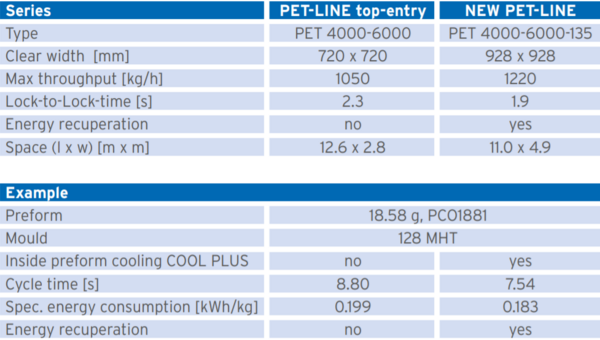
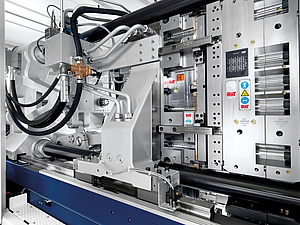
Clamping unit and take out
The distance between the tie bars and the plates have become a little larger in the new PET-LINE because top entry moulds are smaller and therefore also the clamping unit. According to Kleinfeld, it was nevertheless possible to be a lot more effective by optimizing the electrical drive technology, converters, etc.: “We got everything out of it.”
The five-point double toggle lever is driven completely electrically (PET-LINE top-entry: hydraulic drive), as has been implemented in other NETSTAL machine programms for years. The double toggle lever for the PET-LINE has been optimized by adapting the force transmission and reducing the weight of the panels, as the large-area PET moulds require less thick panels, taking into account the panel deflection.
Short cycle times mean frequent and quick opening and closing. That, in turn, means frequent acceleration and deceleration. This results in high demands on the accuracy of the dynamic behaviour; at the same time, a long life expectancy with minimal wear is expected. However, there is an advantage that can be used energetically:
Recuperation
The main reason for the electrical clamping unit was the opportunity to recuperate braking energy. The recovered energy is fed into an intermediate circuit in which the converters are connected to one another. Each electrical axis was analyzed against this background. “The customer does not notice this, he saves energy unnoticed, so to speak - and the components used, together with the linear guides, lead to a clamping unit that is optimized to minimize wear.”
___________________________________________________________________
''The new PET-LINE will be the machine for standard PET preform injection moulding. It will take some time before the competitors achieve this new performance.'' - Renzo Davatz
____________________________________________________________________
Mould movement
The high customer requirements for wear and tear and life cycle concerning the availability of the machine and tool have led to the use of racks that are more expensive than spindle drives but are more effective in terms of accuracy, dynamic behaviour, life cycle and energy efficiency.
Output
The mould, cooling system and machine work together to achieve the shortest cycle times. On the machine side, the lock-to-lock time was reduced from the magical 2s to 1.9s. The fastest cycle times are standard; there are no extra fee-based packages to reach the highend area. The same goes for the mould chip that shall be used in the sense of customer needs: The new PET-LINE will not run any slower when equipped with competitor moulds.
Mould
Initially, the PET-LINE team considered designing the new machine so that it could worked with top entry tools. For the new 3-platen machine, this would have meant a larger distance between the tie bars, and the plates would also have had to be larger, thicker-walled and therefore heavier. The higher costs, but above all the energetic disadvantages, could not compensate for the advantage of flexibility. The new PET-LINE is backwards compatible for standard side entry tools until at least 2004.
Alignment under clamping force
The mould closes with a fraction of the clamping force so that the tool can be held between the plates for alignment before the full clamping force is applied. Under this controlled condition, the operator can open the door to attach the tool correctly.
Inside preform cooling
Depending on the preform, the inside cooling has a greater or lesser impact on the cycle time. With thick-walled, heavier preforms, the inside cooling has a more pronounced effect than with thin-walled, lighter preforms. In one case, for example, the cycle time could be reduced from 12.4s to 10.8s.
Take out
The take out system has double belts with two drives as standard and is integrated in the machine. Compatibility and the shortest lock-to-lock time were also the requirements here. The take out is set up for all common pitch distances with four after-cooling stations. The solution requires an offset of the cooling sleeves at certain pitch distances. The cooling sleeves are not only arranged in a row, but also staggered, which only requires a small stroke - once up and once down - for picking up the preforms.
Cooling water
Standard on the market is a large water supply and return with a water temperature of 8 ° - 10 ° C for the tool and the cooling sleeves. The new PET-LINE has a separate temperature control circuit for the in the post-mould cooling (PMC) stations. This has the advantage that cooling sleeves can be run a little warmer, which results in more uniform cooling over the circumference of the preform.
Amount of oil
Although the new PET-LiNE has an electrical clamping unit, it was decided to install a larger oil tank. Advantage:
The oil remains in the tank for longer, so that suspended particles or dirt particles can slowly settle. As a result, the oil has a better quality under production conditions in the hydraulic circuit - besides, the life cycle of the oil increases. An HLP 46 is used, which can be operated with an oil temperature of 40 degrees. This is 10 degrees lower than with the previous solution, which shortens the heating-up time and less heat goes into the production hall through thermal radiation. In addition, the maintenance intervals are extended and the availability of the system increases.
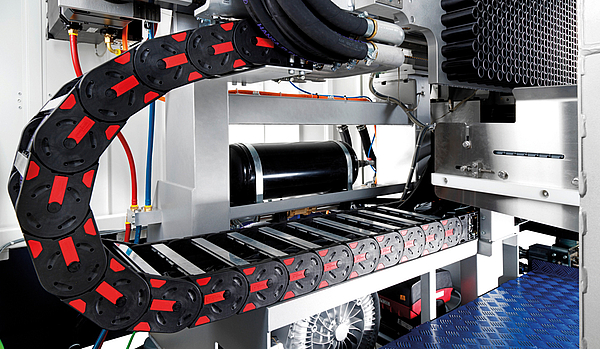
Plastication
Following the general standard, the new PET-LINE has a two-stage plastifying system: plasticizing above, shooting pot below - separated from each other. In this way the higher material throughput is achieved with the same screw size and better homogeneity of the melt and melt distribution. The hydraulic system has also been adapted by reducing the system pressures for reloading the melt into the shooting pot compared to the top entry, which enables further energy savings.
Intrusion / Automatic dosing
During the intrusion, the screw continues to rotate even if the material is pushed into the shooting pot. This enables higher throughputs and better mixing if, for example, AA blockers or other additives are used. The automatic dosing system analyzes the dosing time and the dosing time reserve (break time) for each cycle. The automatic adjusts the dosage to the conditions of the plastication. The resulting, gentle conveyance of the melt achieves lower AA values than on comparable machines, as well as a lower IV drop of the melt.
__________________________________________________________________
''The new PET-LINE has a separate temperature control circuit for the cooling sleeves.'' - Stefan Kleinfeld
___________________________________________________________________
Screw
The objective when developing the PETX screw was to absorb quality margins in rPET materials. The process window now offers more flexibility, and the screw has a more powerful drive with higher torque.
Machine control
With the new control, the sampling rate has also been doubled. The higher this is, the more precisely each process or process step can be controlled. A higher sampling rate also makes it possible to adhere to tighter tolerances and to utilize the range of specifications better. The experience from the medical application world helped develop a patented control for the machine operator. He operates the machine with four buttons, while the application engineer has the full range of adjusting screws for the process at his disposal. With the tool “Smart Operation” of the new aXos control DSP/9, a lot of process know-how could be stored in the machine control.
____________________________________________________________________
''With the tool “Smart Operation” of the new aXos control DSP/9, a lot of process know-how could be stored in the machine control.'' - Stefan Kleinfeld
____________________________________________________________________
Data transport
Experience gained with the controls of the ELION standard machines flowed into the development of the aXos control DSP/9. So the new control offers the advantage that all devices, from the dryer to quality control, can be operated through the central PET-LINE control element. This is achieved by standardized interfaces such as Euromap 77 and 82 or OPCUA. The central evaluation enables central countermeasures if necessary. In the next development stage, the machine itself will offer knowledgebased proposals to correct errors.
Chapter 6: Brand feeling comes from within - Interview with Renzo Davatz
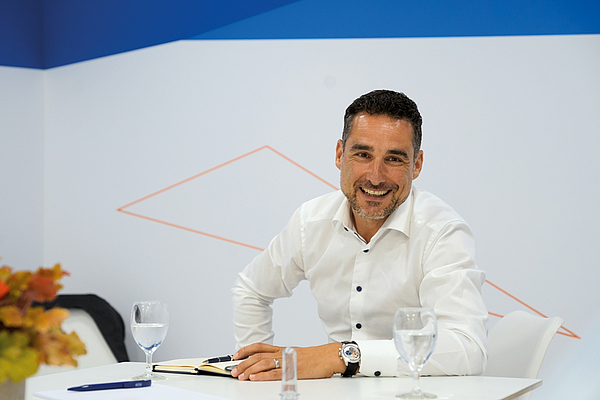
Has it been as quiet inside NETSTAL in the last few years as it appeared from the outside?
Davatz: There were certainly two perceptions. The external one, I agree with you: It was quite quiet. And the internal. A lot has changed, a lot has moved us. On the one hand there were management decisions at group level, NETSTALMaschinen AG disappeared as a company name. We first had to reorganize ourselves under the new name KraussMaffei High Performance. That challenged us all. At the same time, we delved into the development and reconsidered our top entry system.
Does a new development of this dimension have a special meaning in such a situation?
Davatz: For the internal direction, for our orientation - and by that, I mean both the management and the entire workforce - it quickly became clear to us that a kind of guiding star, a lighthouse, would help. The development work for the new PET-LINE and the perspective - that became exactly this guiding star. We want everyone to recognize that our plant here in Näfels has its right to exist here and that we are and will be successful as a team. We want to underline our claim “There is no getting around Netstal”. The new PET-LINE product range is one of the largest development projects in the company’s history. The new ELIOS series that we brought onto the market - incidentally unique in the thin-walled area - also helped us.
Has the market pushed you to move into side entry technology?
Davatz: Our customers have encouraged us to take the step. And you are right when you say that the market has pushed us to move into side-entry technology. Even a technically good unique selling point can be limiting for market access. It was a difficult decision to leave a development, a path that has shaped a brand. There are always people behind it who have driven these developments.
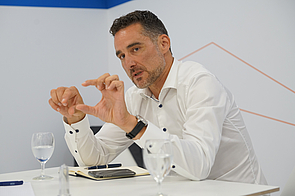
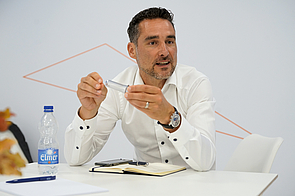
Has the thrill and enthusiasm spread to the workforce?
Davatz: Definitely, and we are particularly pleased about that. Because: Pride, in the context of such a development, is something that you need to feel from inside. Then it can also be carried outwards, to our customers. A brand feeling comes from within.
Would these developments have also been possible under the company name NETSTAL?
Davatz: From our point of view, the move from top entry to side entry has nothing to do with the company name. In retrospect, one could say that we should have had the courage to make this decision earlier. We may have tried too long - and also managed - to get better and better with top entry. And top entry undisputedly sets the market standard in these areas: Lowest footprint, lowest energy consumption.
Nevertheless, the side entry concept dominates the market.
Davatz: However, it is not always a question of the technical solution, but rather what will prevail best on the market in the long term. Our problem was that with top entry, we were caught in the compatibility issue and couldn’t expand our market share.
Has the pandemic hampered or mixed up your plans?
Davatz: Despite Corona, we stayed on schedule. The uncertain times have not led to any changes to the business plan. Our PET strategy is not wavering because of the pandemic. We will have access to a larger part of the market via side entry, and we will be able to increase our share. That is our deep conviction. And customers have confirmed that to us in many discussions. Besides: Due to the pandemic, there is a particular investment backlog in the industry. Sooner or later, it will come to an end. And we are ideally positioned for deliveries in the coming years.
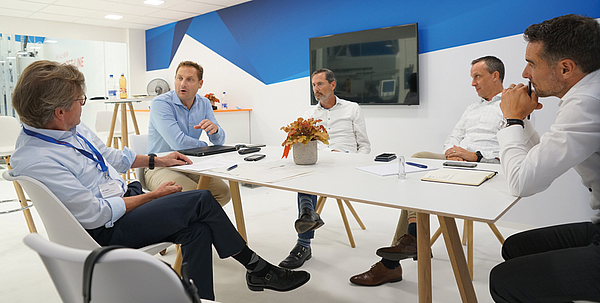
Chapter 7: Summary, reactions, opinions
Fit to battle
The race for ever-higher numbers of cavities has been put into perspective in recent years. A 500 t machine today typically runs a 144 cavity system, a 600 t machine a 192 cavity system. Bottlers mostly use 128-144 cavity systems, while converters are more in the range of 72-96 cavity moulds. This is the technical basis for today’s competition between machine and toolmakers.
Against this background, the new PET-LINE is more than just a portfolio expansion for the NETSTAL brand. The question of product streamlining is, therefore, apparent because a complex product range requires ongoing product updates and produt support. So the question is justified how long the PET-LINE top-entry will be around. According to the current plan, Davatz says, injection moulding machines from the PET-LINE top-entry series will be available as long as there is a proportionate and economically feasible demand in the PET packaging market. “We will continue to serve our today’s top entry customers at top-level.”
NETSTAL is taking a big step towards a growth strategy. A push on the market that will certainly not go without reactions. NETSTAL embarks with the side entry system on the terrain of one hundred per cent comparability. As a consequence, more than before, comparability will move to the fore from the competitors’ perspective.
_______________________________________________________________
''The customer of the first machine - by the way, it doesn’t run with either an MHT or an Otto Hofstetter mould - took the machine into three-shift production after a few weeks of test operation.'' - Stefan Kleinfeld
________________________________________________________________
With its new side entry machine Netstal is part of the game and is now sitting at the table with new cards. In terms of image and brand, the cards are being reshuffled in the competitive environment. The PET market will welcome the game with the new cards; customers expect that this game will provide innovative high-tech solutions for their daily business, preform production. Let us hope that they do not just rely on a price war like the one that took place in the blow moulding machine business.
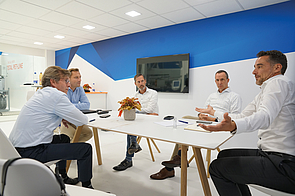
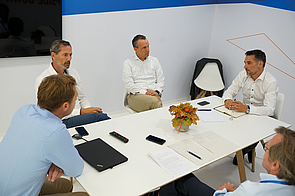
Last year, but especially in 2020, many customers put a brake on investments. I assume that there will be a lot going on in the PET market next year. It’s going to be exciting: HUSKY mould on NETSTAL machine, OTTO HOFSTETTER mould on Husky machine etc. The side entry PET market won’t be dull. Fit to battle.
We did not go into more detail about why the top entry system did not take the position in the market that side entry now has. The key questions today are: How do the big manufacturers differentiate themselves? What makes a significant difference in the customer’s eye? What matters when the machines are once technically almost identical?
______________________________________________________
''I think people will have respect for what we do. Just as we respect the performance of our competitors.'' - Renzo Davatz
______________________________________________________
What makes a successful company? In any case, more than “just” developing a right product, building it under high-cost pressure and being able to offer it at fair market prices. Successful companies are also particularly good at convincing customers of the added value of product and service. Fit to Battle.
Finally, I have two more questions: Firstly: How are the reactions from the customers who have the machines running in the field test? Kleinfeld: “Can there be better feedback than this: The customer of the first machine - by the way, it doesn’t run with either an MHT or an Otto Hofstetter mould - took the machine into three-shift production after a few weeks of test operation. That’s a strong message.
And secondly: Have you already received any reactions from the competition? Davatz: “We don’t hear a lot yet, but I think people will have respect for what we do. Just as we respect the performance of our competitors.”
The comPETence center provides your organisation with a dynamic, cost effective way to promote your products and services.
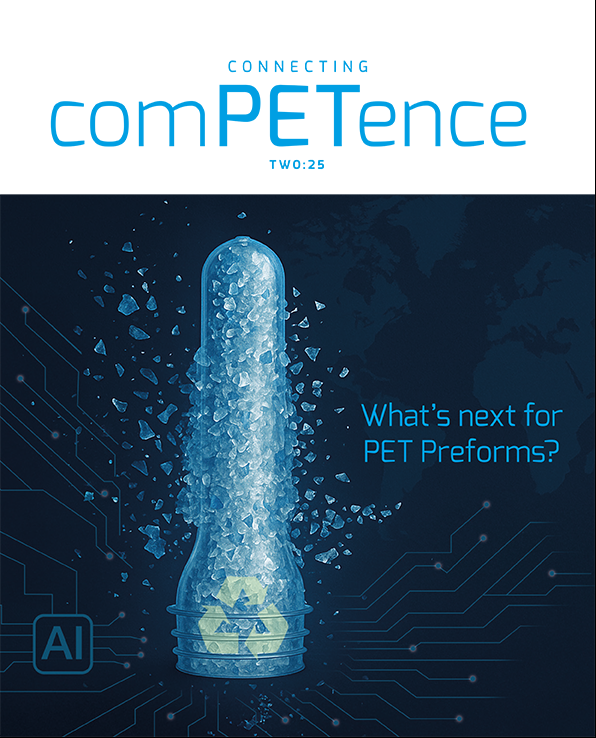
magazine
Find our premium articles, interviews, reports and more
in 3 issues in 2025.