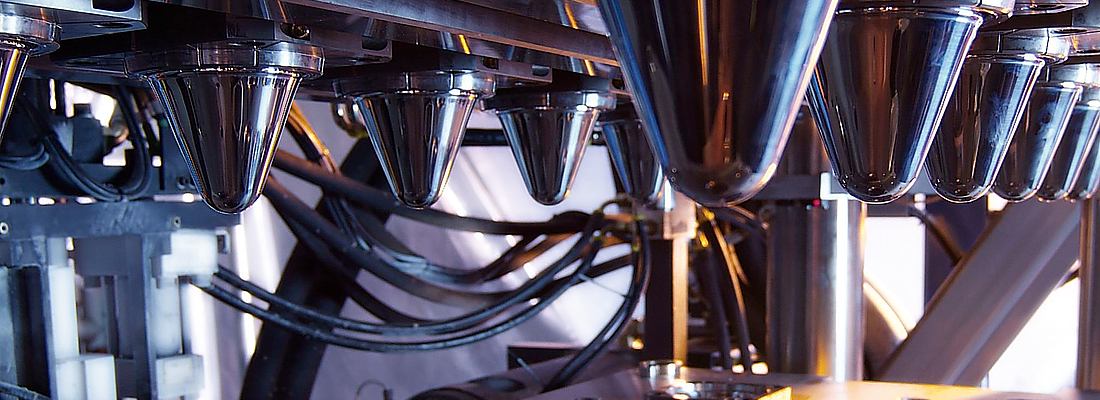
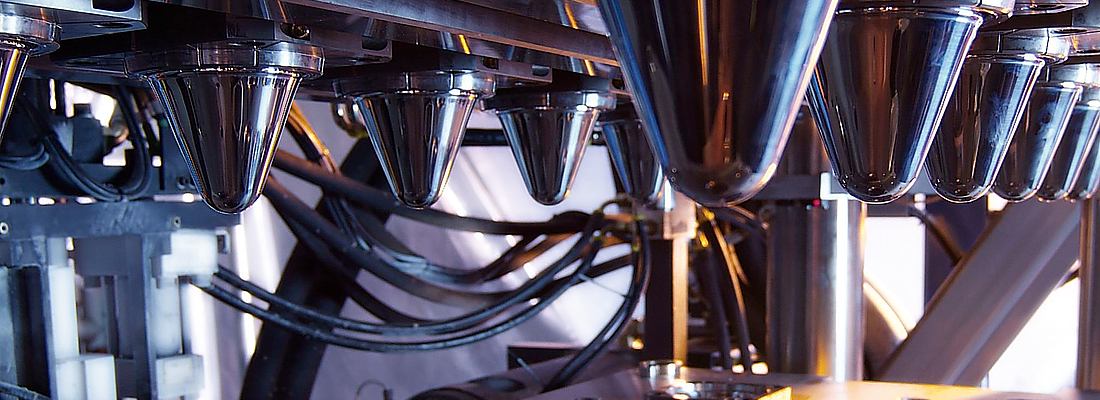
SIPA’s expertise in injection-stretch-blow molding systems is probably unrivalled, stretching as it does both in time – more than 30 years – and in type. The company now makes ISBM units capable of making anything from miniatures for spirits that are particularly popular among airline companies keen to reduce weight on their planes, through to large containers holding as much as twelve liters. Customers like them because the costs associated with several elements of two-step processes (preform handling, preform storage, preform cooling & reheating) disappear and they are not limited to the preforms present on the market.
ECS STANDS FOR VERSATILITY
SIPA has been designing and manufacturing “ECS” integrated ISBM systems since 1986. They are extremely versatile, being capable of producing a wide range of standard and customized containers: lightweight bottles for standard or hot fill use, ultra- clean or aseptic bottles, pasteurizable containers, warm filled bottles, wide mouth jars, round or square shaped bottles, oval, asymmetric or tailor-made containers. Production of containers at output anywhere from 2,000 to 30,000 b/h is possible. SIPA delivered almost 700 systems along his history, in the early days in Europe and then in very large numbers in Asia and North America.
The ECS platform was extended in late 2014 when SIPA acquired the ISBM equipment production activities of Automa S.p.A. The acquisition made considerable sense strategically for SIPA, since Automa’s line, in smaller systems, complemented SIPA’s existing ECS line of larger machines very well, and strengthened its position in specialty containers for pharmaceuticals, cosmetics, liquors, food, automotive and personal care products.
PROGRESS THROUGH SYNERGY
SIPA has been exploiting synergies between the two operations, in packaging development, in process and container R&D, and in technical support. These synergies have led to some important upgrades to the smaller “ECS SP” systems in recent months (more later). The platform for larger ECS systems has also been upgraded to include new innovations.
CLOSED LOOP CONTROL
The “traditional” ECS platform start with PET granules and end the with finished container, with total automated control of all phases of production. The closed loop control system, active in each individual phase of the machines’ cycle, creates a closed, self-diagnostic system in which the parameters and changes in production can be controlled rapidly and efficiently with immediate effect.
PET granules are plasticized in a continuously-running extruder using a screw turning at around 50 rpm, specifically designed by SIPA to generate low shear stress and so minimize AA levels and any reduction in IV. Melt is conveyed to a shooting pot and injected into the mold. Injection profiles on the injection unit are tailored to the shape and weight of the preforms, which in turn depend on the container to be produced.
This configuration differs from other ISBM processes, where the extruder doubles as an injection unit. The screw can be sized exactly according to plasticizing needs, and injection is more accurate.
Preforms are taken directly to the conditioning areas that create the ideal thermal profile for the stretch-blowing phase. Depending on the application, the conditioning system may incorporate high power heaters, a patented air-knife system, and infrared lamps.
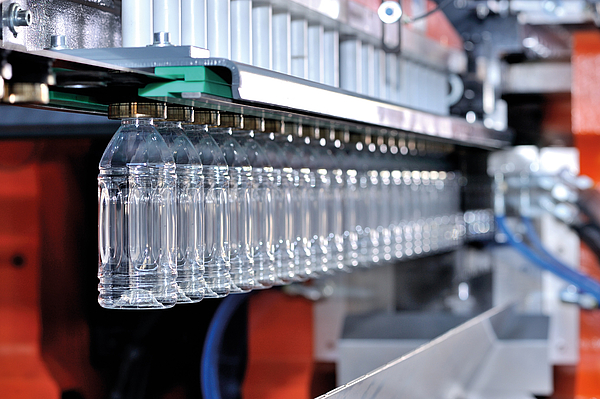
MULTIPLE HEATING OPTIONS
High power heaters are made of a ceramic cup in which band heaters are inserted/embedded. This allows very high temperatures to be reached (over 600°C) over the complete preform body profile, very quickly and effectively. SIPA’s patented air-knife system uses jets of very hot air (up to 800°C) to reheat only the preform transition zone; virtually no amorphous material is trapped in the shoulder of the container. Infrared lamps can create thermal pro les suitable for containers with high ovality ratios or with off-center necks, and which has uneven radial stretch ratios.
ELECTRIC STRETCH
In the stretch-blow molding section, stretching rod movements and blowing time parameters are electronically controlled. Containers are blown in two phases, first with low air pressure (approx. 10 bar) and then with high air pressure (25 to 40 bar). The blow mold can be heated if the container requires it.
The ECS FX-HS range includes models with between 20 and 80 injection cavities, and between 10 and 40 blowing cavities, providing for outputs between 6,000 and 36,000 bottles/hour.
FEEDS TWO FILLING LINES AT THE SAME TIME
The ECS FX has a single extruder feeding four preform injection units, which in turn feed two bottle production lines (two preform injection units per bottle blowing line). It can simultaneously produce containers with different sizes and shapes (for example, wide-mouth jars on one side and oval containers on the other).
COST SAVINGS
The integrated ISBM process guarantees low production costs thanks to numerous features. Preforms are blown immediately after molding, extra weight can be shaved off them; handling and logistic costs are minimized; there are no energy costs associated with preform cooling and subsequent reheating.
SIPA’s innovative ARS and ARS Plus air recovery systems allow the recovery of high pressure air to be used for other process phases and for others equipment. They cut air consumption by up to 40%, depending on bottle type. They also provide better control of the pressure inside the blowing cavity.
BOTTLE QUALITY
A further advantage of ISBM is that humidity levels from the granules to the preform to the stretch-blowing phase are controlled more effectively. The low level of humidity obtained results in a higher level of crystallinity in the container, resulting in higher mechanical properties and heat resistance.
Elimination of preform storage and handling ensures excellent aesthetic appearance of the container produced with no scratches or blemishes.
ISBM also provides the possibility of immediately adjusting process parameters in both in the injection and blowing phases to correct any defect found in the container, eliminating the risk of building large preform storage and discover later that the quality is low.
ULTRA-CLEAN AND ASEPTIC CONTAINERS
The integrated process offers the intrinsic advantage of producing clean containers. It is easier to keep preforms and bottles sterile during the production process, and the elimination of preform storage and handling means there is no chance for dust to settle on or inside the containers. A clean and virtually aseptic container permits a minimized chemical treatment during sterilization processes and lower filling temperatures for hot-fill. Furthermore, any barrier coatings adhere more readily to the surface of the clean container.
AMORPHOUS HOT-FILL NECKS
The platform can produce any type of heat-set container for sensitive products than need to be hot filled, with the lowest running cost achievable in the market. SIPA was the first systems provider to introduce the amorphous reinforced neck for such applications. Eliminating the need for a crystallized neck dramatically reduces container production costs.
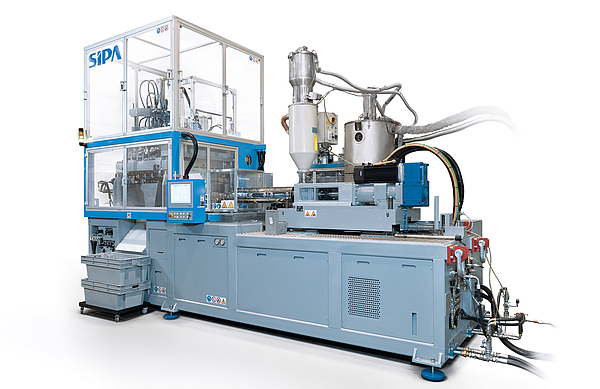
MADE TO MEASURE
SIPA aims to provide solutions that exactly fit customer requirements. For this reason, larger ECS ISBM systems are all built to order.
ECS SP80 AND SP50
The four-station ECS SP80 and its smaller sibling, the SP50 (the numbers refer to injection clamp force in tonnes), are ideal for production of containers as small as 10 ml. SIPA sees strong prospects for making inroads into the prestigious market for very high quality small bottles for cosmetics and beauty care products. It recently developed prototype cosmetic containers in a range of striking designs, in round, oval, and rectangular shapes. Large tie- bar spacing also enables production of containers up to 12.5 l in volume.
Both machines feature a compact layout, quick change-over between different mold configurations, and high energy efficiency. The ECS SP80 has a very fast dry cycle of 3.5s. An adaption kit makes it possible for the machine to run with molds from other OEMs.
Also ECS SP are totally built in Italy, with a care in details and a high overall quality noticeable as general strength, speed and precision and consistency of movements, thanks to a very accurate design, the use of top quality components and the extremely precise construction.
Blow air pressure of up to 40 bar can be used to produce very sophisticated and complex bottle shapes. The ECS SP80 can produce hot-fillable PET containers that withstand filling temperatures up to 85°C. Innovative features such as adjustable strokes for injection and stretch-blowing according to preform length and bottle diameter are useful for optimizing cycle time and energy consumption.
Latest versions of the ECS SP 50 and 80 units feature an upgraded user interface (HMI), as well as improvements to the injection system, preform conditioning, and bottle blowing. The machines now also accept a wider range of legacy molds.
IMPROVED INTERFACE
The HMI of the ECS SP has undergone a significant redesign. The company analyzed the various procedures that the operator needed to go through to set up the machine and created a set of shortcuts to simplify those procedures. The result is a much more intuitive interface that makes it much simpler for the operator to access, understand – and if necessary modify – the settings they are interested in.
BETTER INJECTION
SIPA has replaced the original thermal gating in the preform injection hot runner system with needle valve gates. Because the new gates can be purged much more quickly, the time taken to get the machine up and running is notably shorter. The number of tasks that the operator needs to carry out every time the machine stops and restarts has been reduced, and the simpler geometry of the gates enables a simpler solution for clearing the hot runner system.
REDESIGNED PREFORM CONDITIONING SYSTEM
SIPA design engineers have completely redesigned the preform conditioning system on the ECS SP. The process is now more energy efficient, and each individual cavity can be provided with its own conditioning parameters, determined according to the design of the preform.
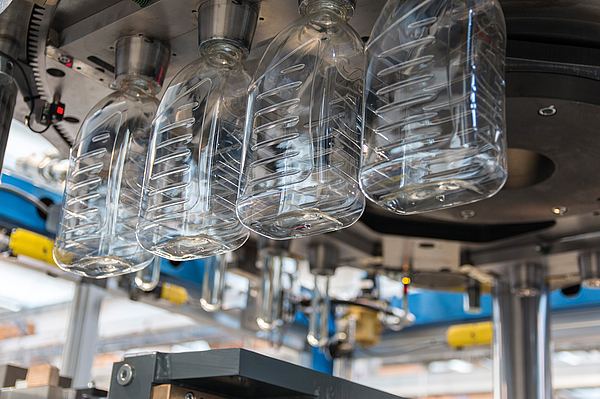
BLOWING INNOVATIONS
Numerous changes have been made to the bottle blowing section with the result that the process is now more stable and energy-efficient. It is possible to manage the blowing conditions in each cavity separately, so that every bottle is of the highest quality.
GREATER MOLD COMPATIBILITY
A special “compatibility kit” is now available for the ECS SP that makes it ready to accept molds originally intended to run on ISBM machines from major competitors. It is now possible to quickly adjust the vertical position of extruder according to the mold.
SWIFTER AND SAFER MOLD CHANGES
In the last few weeks, SIPA has unveiled new quick mold change system for ECS SP 80 units that significantly cuts changeover times. New features also add extra safety and user-friendliness for operators, especially for some critical operations. The system involves a new automated procedure for loading and unloading the preform core plate; this incorporates additional sensors to ensure that the mold opening stroke adjusted correctly according to the preform length. Operations for assembling and disassembling the neck ring plate have also been modified. SIPA has developed a patent-pending system that now makes it possible for the procedure to be carried out by one person instead of two, in full safety.
Changing the blow mold is much easier, too. Intelligent modifications to the press and the introduction of roller bearings in critical positions, for example, now mean that once the forklift has positioned the mold next to the clamp unit, the mold can then be pushed into position by hand. Height adjustment of the mold, once it is in the clamp, is also easier.
Finally, modifications have been made to sealing plate and stretch rods, and standard screw fittings for the water cooling system have been replaced by quick- t push/pull fittings – all with the aim of making things simpler, faster and even safer for the operator.
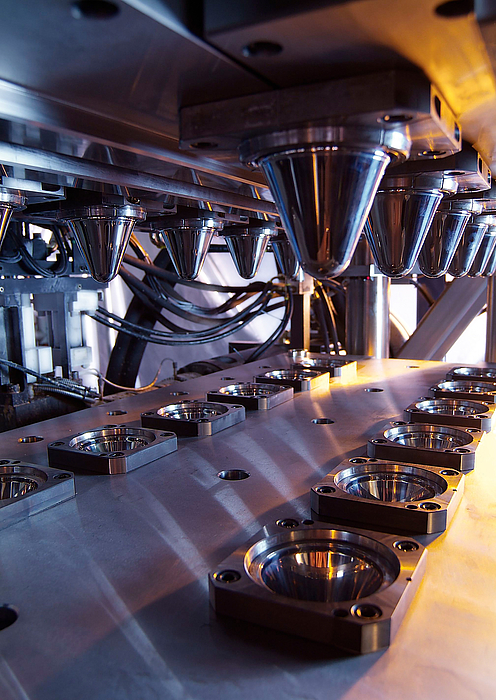
The comPETence center provides your organisation with a dynamic, cost effective way to promote your products and services.
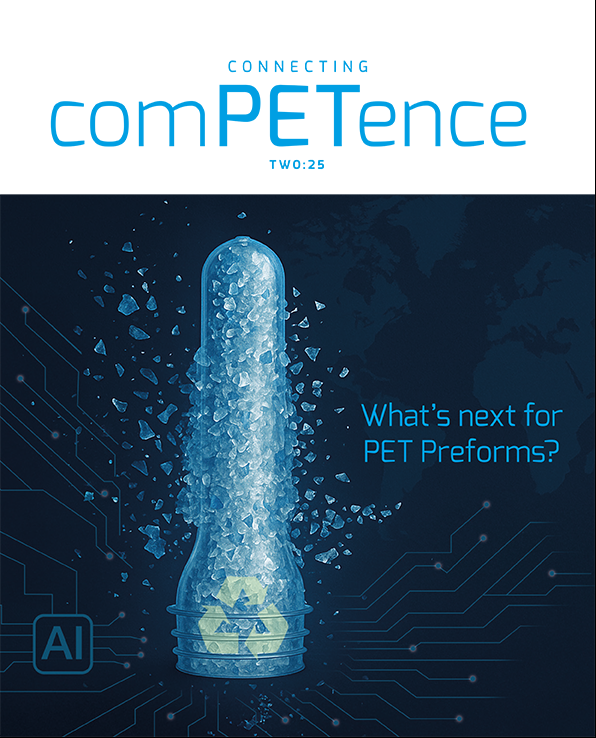
magazine
Find our premium articles, interviews, reports and more
in 3 issues in 2025.