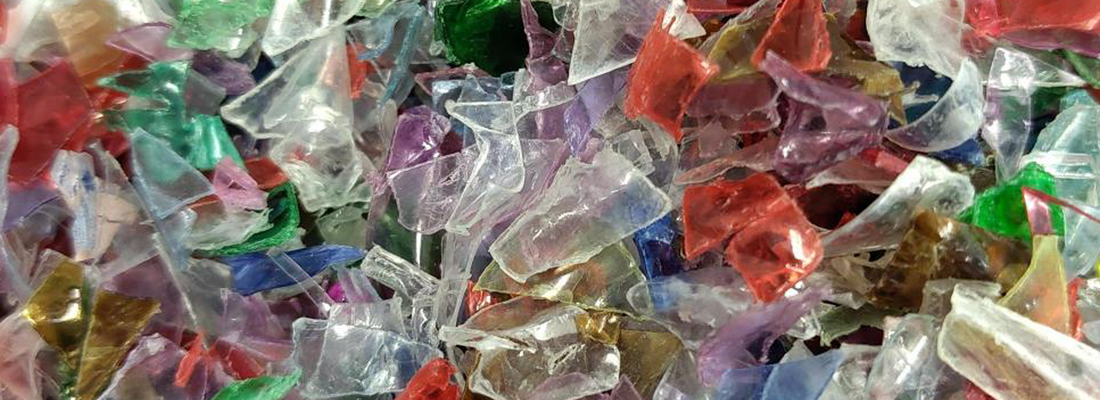
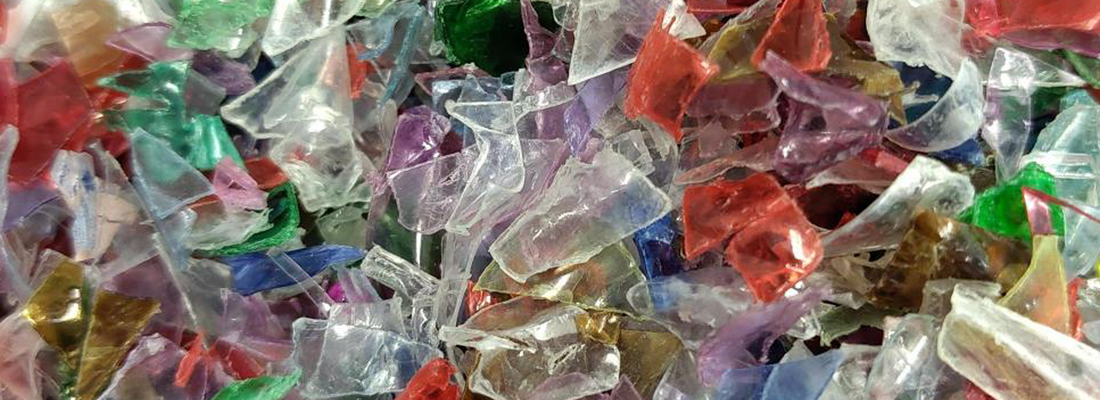
(Source: Ioniqa Technologies)
The importance of recycling
Ioniqa Technologies: Denua(TM) technology - PET recycling without compromise
General public awareness of environmental issues is presently rather high and has been on the agenda of governments around the world for the past several decades. One of the major environmental challenges identified within this agenda and with a strong visibility to the public concerns plastic pollution. Nevertheless, despite this awareness on the part of the public and actions taken by governments, the annual global plastic consumption has continued to increase for decades, from 40 to 300 million tonnes since the 1990s and until the present day /1/.
The main cause of plastic consumption is plastic packaging, which has grown from 2 million tons in 1950 to over 390 million tons in 2021 /2/. Plastic packaging has clear advantages over alternatives, such as its high performance, reduced production cost and low weight. It has also intrinsic environmental benefits such as low fuel consumption during transportation, reduced food waste due to prolonged shelf lives of fresh produce /1/.
This has meant that there is a need to lower the environmental impact of the vast amount of plastics eventually finding their way to landfills, which is where recycling has been gaining increased relevance. Overall global plastic recycling rates are however still below 10% at present. This low recycling rate, in combination with the slow degradation rate of plastics, means that the majority of all plastics ever produced are still somewhere in the environment.
European PET waste is estimated to be about 5.5 million tons in 2022, of which only 54% ever gets collected for recycling. Of the total waste volume, an estimated 38% is recycled only once. To be suitable for mechanical recycling, plastics must be made from a single polymer component (mono-material), preferably sorted by colour. However, a large fraction of valuable material is ‘lost’ due to processing (process loss) and exports. And once mechanically recycled PET quality will be negatively impacted, also know as downgrading. Of PET waste collected for recycling, 34% goes to PET bottles. The rest goes to other application such as textiles, construction and similar, which can be considered as down cycling as recycling of these applications is currently not possible. Partly due to this downcycling effect, only 8% of the PET gets recycled twice (Figure 1) /3/.

Chemical recycling, on the other hand, offers the possibility to recycle streams that are considered difficult to recycle mechanically, for example socalled ‘sorter rejects’, and mixed colours . In fact, the ‘sorter rejects’ are considered process losses for the waste sorters. As such, chemical recycling approaches do not have to compete for feedstocks with mechanical recycling processes, but can be complementary to these /4/.
To provide some perspective, 17.8 million tonnes of post-consumer plastic packaging were collected in Europe in 2018, with 17% of total plastic packaging being constructed from multi-layer material. Only 42% of the collected plastic packaging was recycled, while 39.5% was incinerated and 18.5% landfilled. This situation is still far from the objective to recycle 55% of the plastic by 2030 /5/. Mono-material plastic such as bottles can be recycled mechanically, but the multilayer materials and other less pure streams are currently not recycled at all. To meet the Single Use Plastics Directive (SUPD) which mandates the European bottle industry to include an average of 25% recycled content in PET bottles placed on the market by 2025 and 30% by 2030, the volume of the available feedstock for recycling must significantly increase /3/. This volume will come partially from the increase in collected beverage bottles. As the same the directive mandates 77% collection rate in EU on beverage bottles and 90% by 2029 via separate system. The rest of the needed feedstock must come from the currently difficult to recycle streams.
DenuaTM technology
Denua™️ technology was developed by Ioniqa Technologies in partnership with Koch Technology Solutions to enable recycling of most post-consumer PET waste, especially the feedstock that mechanical recycling processes cannot treat such as sorter rejects, fines, and mixed coloured flakes.
The heart of the technology is a glycolysis process, in which PET is depolymerised to bis(2-hydroxyethyl) terephthalate (BHET) with the help of a magnetic catalyst, which is, due to its properties, easily recoverable after the reaction. After the glycolysis reaction has been completed, BHET is further purified to remove other reaction byproducts as well as contaminants which might be present in the waste plastic feedstock. BHET is a monomer known in the PET industry, as it is an intermediate in today’s PET polymerisation processes. Denua™️ technology can be therefore easily integrated into an existing PET facility to take advantage of the infrastructure including utilities, logistics, and fundamental maintenance and operations capabilities.
rPET created from BHET produced by Denua™️ retains virgin-like performance, versatility, and clarity, no matter how many times it is recycled. The purity of the BHET allows for the production of rPET that is suitable for high-quality food-grade and all other polyester applications. In addition, this technology also gives PET plant operations the ability to optimize the feedstock between virgin hydrocarbons and recycled plastics to produce high quality rPET with up to 100% recycled content.
Glycolysis chemistry /6/
In the PET glycolysis process, the ester bonds in PET are cleaved by MEG to form BHET (Figure 2). This process is typically performed at temperatures around the boiling point of MEG and in the presence of a catalyst. Whether partial or full depolymerisation is achieved depends on reaction conditions, such as PET/MEG ratio and reaction time.

The glycolysis process also leads to the formation of various side products, which needs to be controlled during the glycolysis process to obtain a stable and consistent process. The major byproducts (Figure 3) present in a typical glycolysis process are mono-2-hydroxy-ethyl-terephthalate (MHET), BHET dimer, [2-(2-hydroxy-ethoxy)-ethyl]- 2-hydroxy-ethyl-terephthalate (HEEHET) and bis2-hydroxy-ethyl-iso-phthalate (BHEI). These are also known as “BHET-likes”.
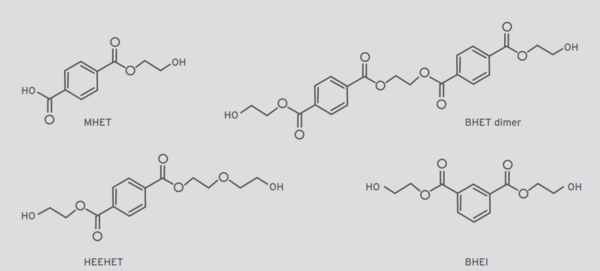
The amount of dimer present in the reaction mixture is mainly dependent on process parameters, such as reaction time and the used PET/MEG ratio. The higher this ratio, the more dimer (and sometimes longer oligomers) will remain. The presence of these short oligomers can never be completely prevented, due to the presence of a dynamic equilibrium with BHET and MEG (Figure 4). Since oligomers will repolymerize into PET, they have no effect on final PET quality and may therefore not be considered as an impurity. However, their presence may have an effect on the downstream processing and it is therefore important to be able to control their concentrations.
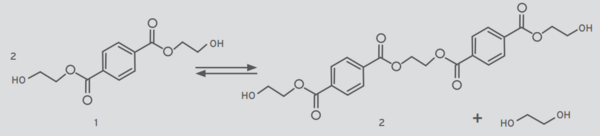
The DenuaTM process
DenuaTM technology breaks down PET into BHET monomer, which makes it much easier to remove further impurities compared to depolymerisation reactions that produce oligomers. The four main steps that can be distinguished in the process are: reaction; inert and catalyst separation; purification, including the colour removal; and product isolation (Figure 5). The MEG, water and catalyst used in the process are recycled as much as possible.
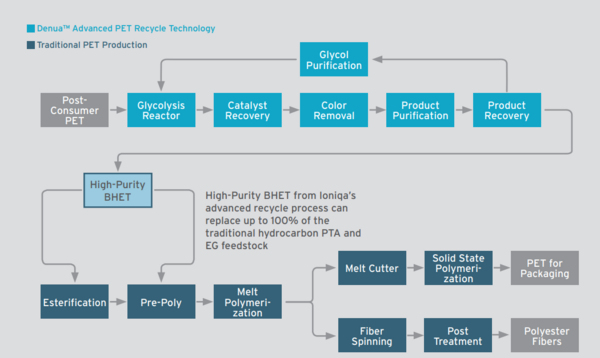
The process starts with feeding the reactor with low-grade, mixed-colour PET flakes that will react in a transesterification reaction with MEG. The glycolysis reaction is catalysed by a heterogeneous, functionalized, magnetic nanoparticles. The relatively mild process conditions in combination with fast depolymerization kinetics when using the catalyst result in high selectivity and minimal side product formation. By recovering and recycling the oligomers, high overall yields (>95 mol%) of BHET on PET can be obtained. Due to its high activity, relatively low catalyst-to-PET ratios can be used /7,8/. Figure 6 shows the yield of BHET from the depolymerization with different catalysts, as well as the yield of a main byproduct. As it can be seen, the DenuaTM catalyst offers not only the increase in the kinetics of the reaction but also helps suppressing the byproducts. This further simplifies the downstream purification process.
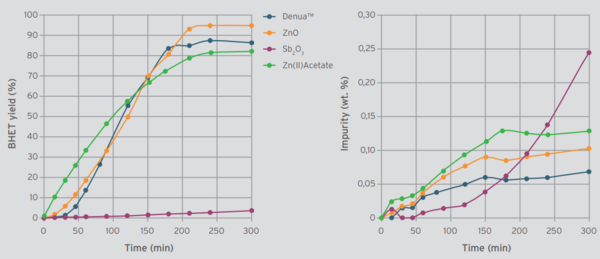
In addition, the surface of these magnetic particles is functionalized with a stabilizing component that makes them behave as a colloidal suspension of nanoscale superparamagnetic particles. This catalyst complex possesses the functionality to be recovered from the reaction mixture and be recycled back into the process.
Figure 7 shows the performance of the catalyst over several cycles. It can be seen that the catalyst’s favourable activity is kept over time.
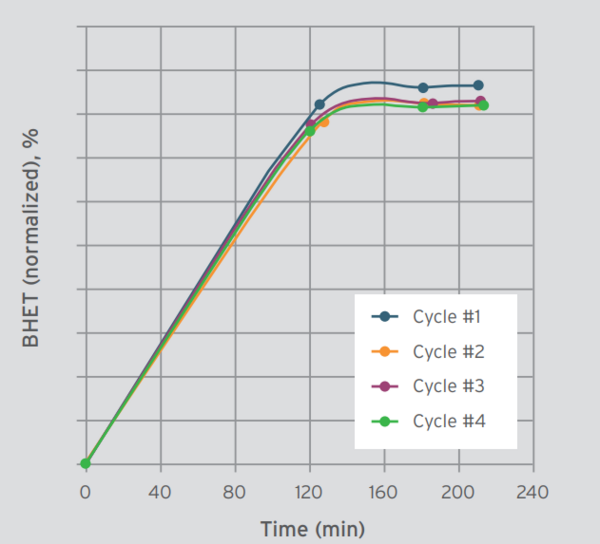
After the glycolysis reaction, the reaction mixture also contains, next to the desired BHET monomer, a variety of non-PET components that should be removed to obtain the final polymer-grade BHET product. In the first separation step, the nonPET remnants, mostly undissolved solid particles such as other polymers, metals, sand and paper, are removed using their difference in physical and chemical properties under the given process conditions. Hereafter the catalyst is separated from the reaction mixture. Non-PET remnants that dissolve and become sticky residues belong to the most challenging group of remnants. Depending on their concentration in the feedstock used for the process, the process design may include the removal step prior to the reaction.
Before recovering the BHET monomers, the residual colour components and additives from the PET feedstock are removed from the reaction mixture. It is important to note that the range of colour components and other impurities as well as their concentration can vary significantly in the feedstock. Every plastic flake may be contaminated with different impurities and has been subjected to various degradation processes. Feedstock variations from different geographical regions is yet another added complexity. Different types of plastic additives are used in different parts of the globe. Even within the same region, even at the same sorter, the same product code offers large variations in feed composition. To illustrate this, Figures 8 and 9 show the variation of the composition of three commonly used dyes in PET bottles for selected feedstocks. It can be seen that the concentration of dyes in different feedstocks, and even within the same feedstock over time, varies significantly. The sizing of the colour removal unit accounts for these variations. Furthermore, the design must be based on the data measured with real reactor effluents, as the presence of various impurities influences the efficiency of the separation step. As an example, Figure 10 shows the adsorption isotherms of a dye on an adsorbent both in model and real plant solutions. Design must be based on the ‘red isotherm’, as using ‘blue and grey isotherms’ will result in severely underdesigned adsorption column.
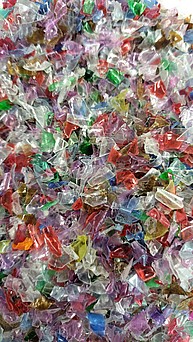
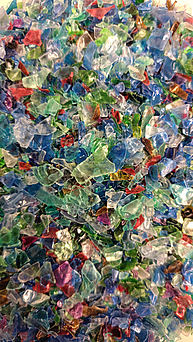
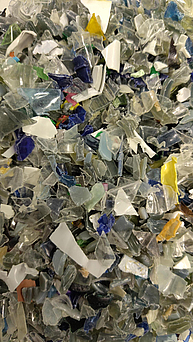
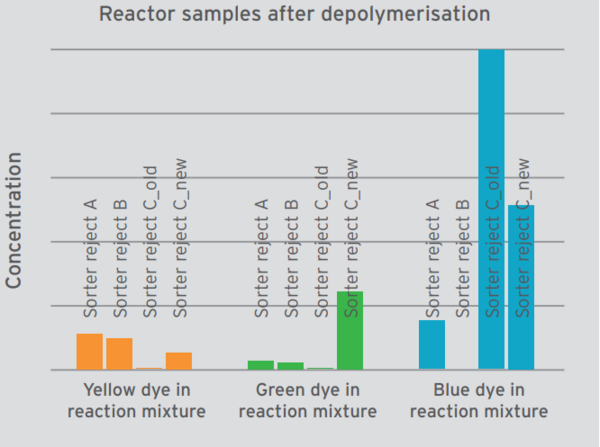
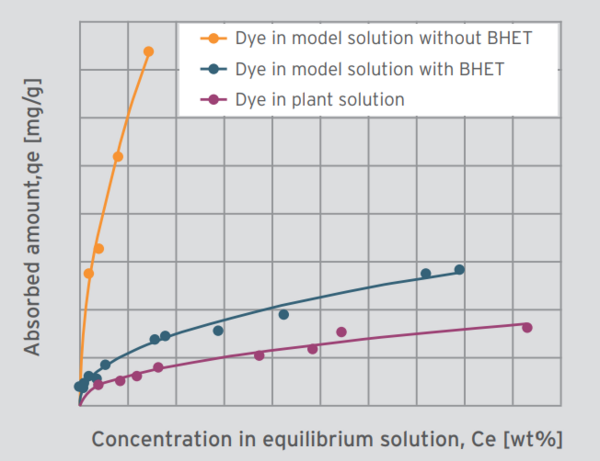
The purified stream is cooled to crystallize the BHET product. As some reaction byproducts, namely the BHET-likes, can co-crystallize with BHET, it is important to keep their concentration in the product stream low. This technology achieves this already at the reactor as the catalyst supresses the byproduct formation sufficiently to keep their concentration downstream of the reactor low enough to enable a relatively straightforward crystallization. This results in a high purity monomer. Overall, the process achieves the high yield of the monomer per PET.
These BHET crystals are separated from the mother liquor by filtration and washing, and are finally dried to the required specifications. Alternatively, instead of drying, a molten product can be obtained that is easily introduced to the PET polymerization process.
For a more favourable process economy as well as favourable environmental impact, the excess of MEG is recovered from the crystallization mother liquor and recycled to the reaction step.
Outlook/Conclusion
The continuing dependence of our society on the advantages and convenience of plastic packaging, coupled with public increased environmental awareness means that plastic recycling processes will continue seeing an increase in relevance. As plastic waste cannot be easily managed and due to the inexistence of a single “silver bullet” capable of addressing this challenge, multiple approaches and strategies must be considered. Chemical recycling shows great potential to be an effective tool in the plastic recycling arsenal, both due to its easy pluggability to and complementarity with other processes, and its potential to allow for continuous recycling of the target polymers and thus unlock further upcycling approaches.
Chemical recycling of PET assumes then great importance, not only due to the ubiquity of PET in plastic products, but also as it is frequently used together with other products in plastic packages and becomes thus difficult to recycle via other means. The DenuaTM process has the potential to greatly contribute to the overall plastic recycling strategies, as it not only is capable of chemically recycling waste PET from different feedstocks and sources, including sorter rejects, but also to provide a good quality product, BHET, which can be integrated seamlessly into the overall PET process chain.
_______________
/1/ D. Ellen McArthur, The New Plastics Economy: Rethinking the Future of Plastics & Catalyzing Action, Ellen McArthur Foundation, 2017
/2/ Plastics – the Facts 2022; Plastics Europe AISBL, EPRO; October 2022
/3/ PET market in Europe: State of Play (2024); Eunomia
/4/ Vasileios Rizos, Patricia Urban, Edoardo Righetti, Amin Kassab, Chemical Recycling of Plastics, CEPS In-depth Analysis, 2023
/5 /Website: https://merlinproject.eu/project, consulted 17 May 2024
/6/ M. Gravendeel, M. de Groot, L. Slenders, B. Stevens, M. Stolk, J. Wolters, A. Wolters, F. Wouters, (2023), Chapter 67: Depolymerisation of PET Polymers at Ioniqa Technologies (Case Study), Industrial Arene Chemistry: Markets, Technologies, Processes and Case Studies of Aromatic Commodities. Edited by J. Mortier. ISBN 9783527347841
/7/ A.M. Vilaplana, L. Mestrom, R. de Groot, V. Philippi, C. Guerreo Sanchez, T. Hooghoudt US Patent 10703703B2, 2020
/8/ S. I.-M. R. Castillo, V. G. A. Philippi, US Patent 10927231, 2021
_______________
The comPETence center provides your organisation with a dynamic, cost effective way to promote your products and services.
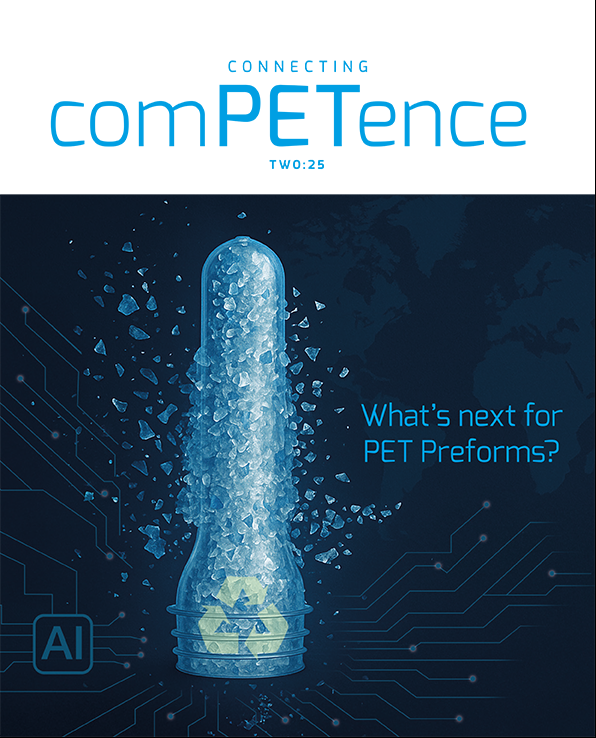
magazine
Find our premium articles, interviews, reports and more
in 3 issues in 2025.