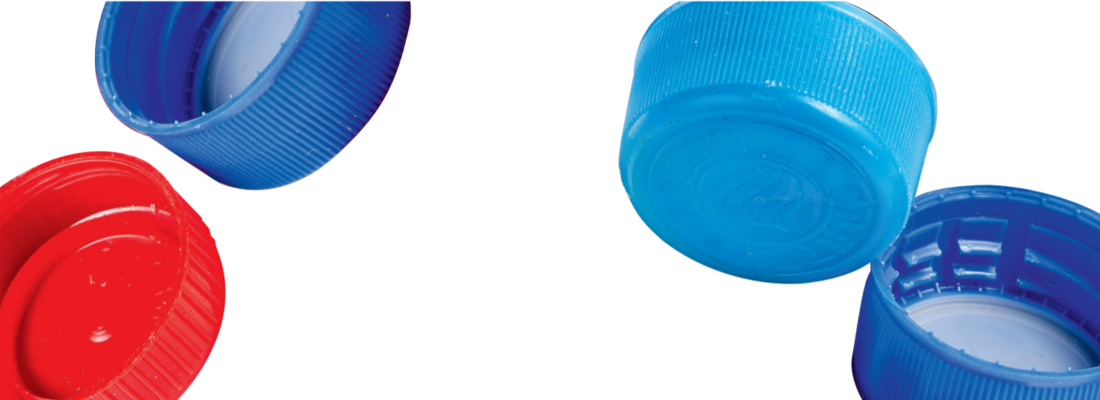
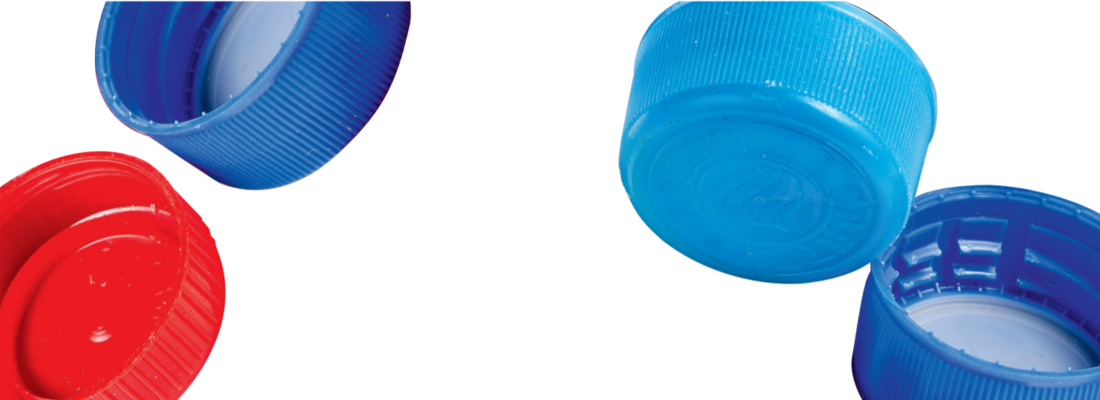
When discussing the development of a beverage closure with someone outside the industry, we often hear the saying: “Come on, it’s just a plastic closure! Developing such a simple piece of plastic cannot be that hard!”. Well, it is.
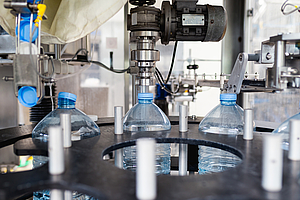
What might look simple from the outside reveals tremendous work of development if you look at it more closely. But before going into details of the closure product requirements we shall take a look at three major steps in the life of a closure and what makes developing them so difficult in each section. Firstly, we talk about manufacturing of closures, secondly, we talk about the application of closures and thirdly, we talk about the usage by consumers.
ROBUST ENOUGH TO TOLERATE VARIABILITY
Obviously, a beverage closure is a mass product. Hundreds of billions of beverage closures only for PET containers are being used per year. This scale – together with standardization of neck finishes – gives our industry the chance to reach very high efficiency levels. The result is high cavity molds with short cycle times. The challenge is not to manufacture one hundred closures every two seconds on one line but to manufacture one hundred ‘good’ closures every two seconds. Requirements for a ‘good’ closure design start with robustness. If we only take a look at material diversity as an example: we have sampled more than a hundred different organoleptic HDPE resin grades with our closure designs over the last couple of years. And a multiple of this number for color masterbatches. A ‘good’ closure design should manage to result in ‘good’ closures with the vast majority of these resin and masterbatch grades. A ‘good’ closure design also needs to be robust enough to balance variations of manufacturing equipment like different injection or compression molding machines and the various types of up- and downstream equipment.
PRECISE ENOUGH TO GUARANTEE HIGH SPEEDS
If we follow the value stream of beverage closures, the next set of requirements stems from application of the closure on the bottling lines. Bottling lines handling more than 2’000 bottles per hour per capping head have become frequent sights rather than lighthouse examples. High speeds usually mean tolerances for processed parts become tighter. Especially as allowable reject rates – naturally – have not been increased along with the challenges. So even though everything around the closure design can change, closures need to be reproducible in vast quantities. In other words, the first cap must look and perform exactly like the last.
PERFORMANCE AT THE LIMIT
So far we have only talked about requirements stemming from manufacturing and application of the closure. Most closure functions aim at fulfilling requirements of the final product – the filled bottle. These requirements can be categorized as follows: safety requirements (e.g. secure venting, tamper evidence), tightness requirements (e.g. sealing against inside and outside), ergonomic requirements (e.g. easy opening and reclosing), environmental requirements (e.g. withstanding temperature, mechanical impacts) and design requirements (e.g. give brand owners a chance for differentiation). corvaglia performs forty different laboratory tests to validate a closure or closure design against requirements of the final product. Passing forty different tests while being identical in vast numbers and robust enough to tolerate that everything around it can change. Not bad for a simple piece of plastic, is it?
Now with proposed EU directive procedure 2018/0172/COD the industry might even face a source of requirements that had not been very important in the past: legislative requirements that might limit or stipulate certain design features.
Most of the requirements and challenges discussed are valid for the complete beverage package (i.e. bottle + closure) but it is important to state and understand that most of the functions of the package are defined by the closure and not the bottle.
The part of the bottle that interacts with the closure (the neck finish) is more or less standardized in certain categories. The closure needs to take care that all the functions at the interface between bottles and closures are guaranteed.
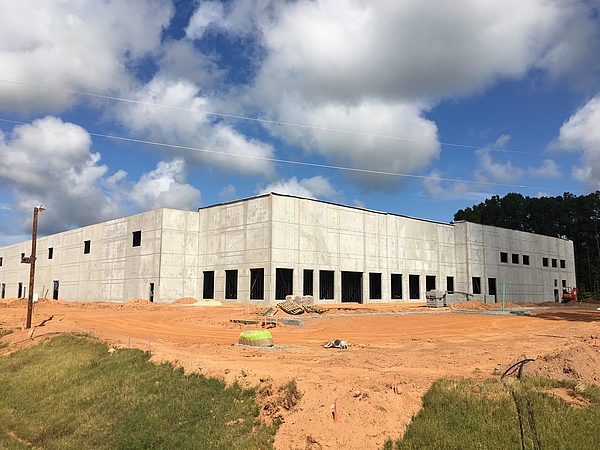
FACING THE REQUIREMENTS
We have discussed a lot of different requirements. It is not exactly rocket science but in order to be successful you need expertise along the complete value creation chain and intelligent closure designers. You cannot empirically try out all combinations. You can also not run a computer simulation with those combinations to optimize the problem, because there is so many different laws and interactions that govern the problem. You need a team with experience, know-how and a good gut feeling to limit the number of simulations you run and the number of empirical trials you do.
We mentioned that the vast volume of beverage closures gives our industry the chance to be effi cient. Every tiny material saving realized will have a gigantic effect on material and energy consumption along the value chain – and ultimately cost. Unfortunately most of the requirements we have discussed are harder to realize with less material in the closure. So lightweighting is the ultimate challenge that makes closure development so tedious.
It has become popular in our industry to call for ‘rightweighting’ instead of ‘lightweighting’. For us, this is not a question of ‘either/or’. For us, the right weight is the lightest weight that does the job. And the closure’s ‘job’ is to fulfi ll all of the above mentioned requirements. People that predict that lightweighting will soon come to an end remind me of renowned physicists at the end of the 19th century like Phillipp von Jolly, Albert Michelson or Lord Kelvin who were of the opinion that there is not much more to discover in physics.
FROM GOOD CLOSURE DESIGN TO A GOOD CLOSURE
When balancing requirements is so delicate, it is crucial to understand requirements in detail. So being close to the stakeholders that set the requirements is obviously essential. What defi nitely helps to get the right inputs is to have closure manufacturing in house with our manufacturing sites in Switzerland, Mexico and until the end of the year also in the United States.
In-house manufacturing not only helps to contribute to a good closure design. An effi cient and high-quality manufacturing operation is necessary to generate good closures from a good closure design. We have proven quality and effi ciency in the two existing plants already. Now, the whole corvaglia team is enthusiastic to bring the results of the closure development process described earlier and experience in effi cient closure manufacturing to the United States by opening a site in Newnan, GA, close to Atlanta (Fig. 1).
All of the closure designs we will bring to the United States will be one-piece designs, in line with our philosophy. Ever since Romeo Corvaglia founded the company in 1991, we have always proven that one-piece closures not only will do the job but in most cases a lot better than two-piece designs. We expect that economic and ecologic pressure on the plastics industry will continue to drive the change from two-piece to one-piece also in North America.
The comPETence center provides your organisation with a dynamic, cost effective way to promote your products and services.
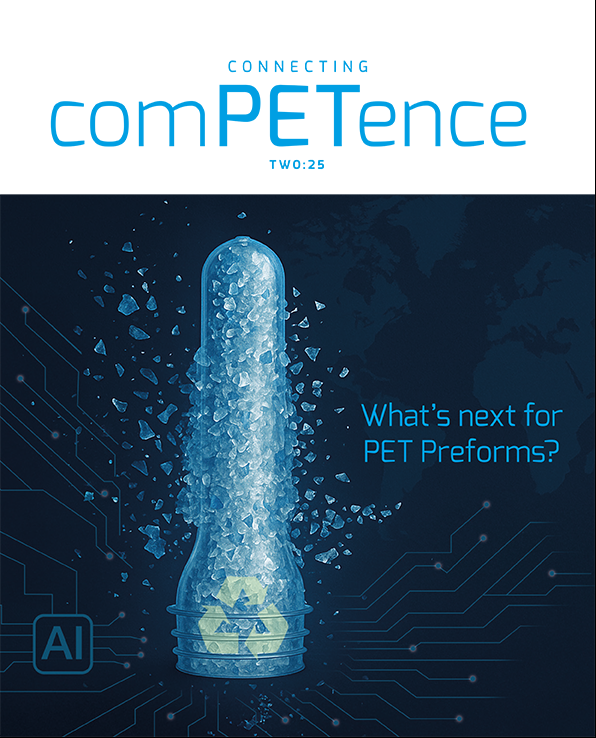
magazine
Find our premium articles, interviews, reports and more
in 3 issues in 2025.