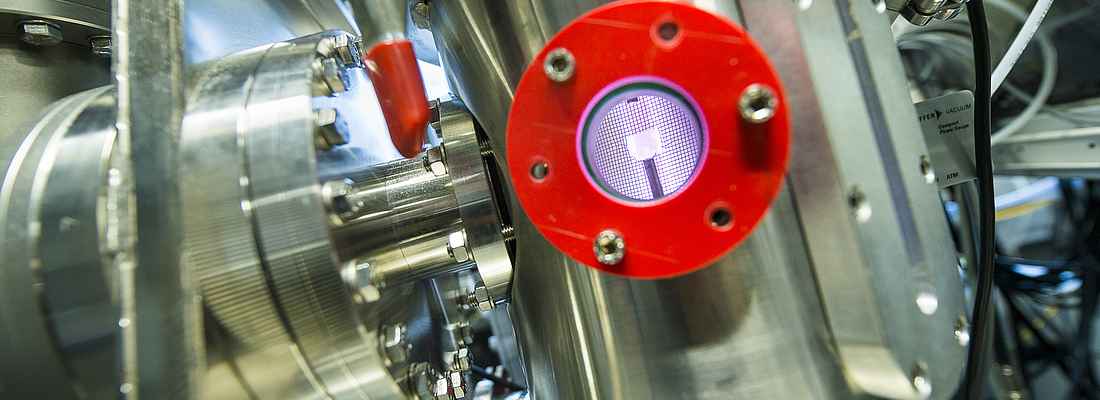
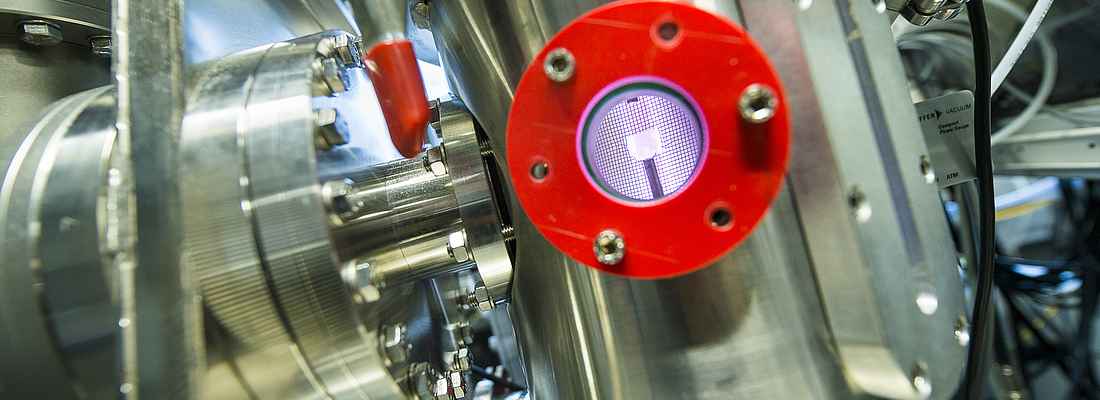
Organic light-emitting diodes, artificial kidneys and PET bottles have one thing in common: they are all made of synthetic materials. Unfortunately, these materials are permeable to various gases. In order to make plastic more impervious, RUB engineers use plasmas to apply wafer-thin layers on surfaces.
PET bottles have replaced glass bottles in many instances, cooling shelves are full of plastic packaging, a current debate revolves around supplying baby food in plastic containers rather than jars, seeing as they are lighter and less likely to break. However, too many people are yet concerned that harmful substances contained in the packaging may seep into the food. Novel plasma-based coating processes may provide a remedy, and they may also extend the food products’ shelf life. At the Institute for Electrical Engineering and Plasma Technology, Prof Dr Peter Awakowicz and his team develop processes for coating surfaces with protective layers that render the synthetic material less permeable.
Poor Gas barrier
Plastics have a very poor gas barrier, i.e. they are permeable to air which can pass through the material in both directions. “This is why water stored in PET bottles loses carbon dioxide and why food goes bad, for example by changing its flavour,” says Peter Awakowicz (Figure 1). The coating his group is working on would make plastic packaging one hundred times more impervious than it is today. Consequently, the shelf life of food products would be prolonged, and they would be protected from substances that seep out from the synthetic material. “Sometimes you hear people say, ‘This tastes of plastic’, and they are right,” explains Awakowicz. “A synthetic material that does not leak ingredients of some sort does not exist. With our coating, the volume of those substances could be reduced to one per cent of the volume that usually seeps out.”
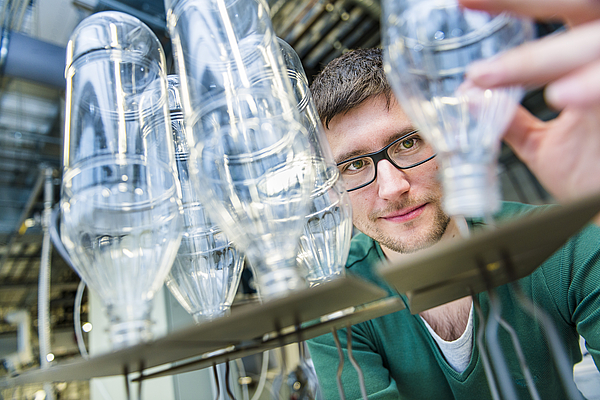
FIG 1: The RUB engineers developed plasma-aided coating processes for PET bottles.
A barrier layer inside the bottle makes the plastic less permeable © RUBIN, photo: Gorczany
RUB TEAM
The RUB team studies in what way an object with any chosen shape made from a specific synthetic material may be best coated using a plasma. For this purpose, the researchers utilise plasma enhanced chemical vapour deposition, i.e. PECVD. In the course of this process the substance hexamethyldisiloxane is vaporised, blended with oxygen and dispersed in plasma. Thus, silicon dioxide deposits on the synthetic material. The plasma provides the energy necessary for the process. The barrier layer which the RUB team thus applies to the synthetic material has a thickness of a mere 50 nanometres. Thicker layers would tear and they would, moreover, disrupt the recycling process, because the silicon dioxide layer is nothing but wafer-thin glass. Negligibly small, the quantities in the coating layers applied by the RUB researchers are not relevant for recycling. They are not applied to the synthetic material directly, however; the process begins with a protective layer. This is because tests have shown that the oxygenated plasma process for depositing silicon dioxide affects the synthetic surface. The result is a so-called weak boundary layer
(Figure 2). “No matter how great a barrier layer you apply to this damaged layer, it will never hold,” says Peter Awakowicz.
Water vapor (ingress/loss)
In order to render this problem measurable, the RUB team, together with their colleagues from Paderborn, came up with a trick. Rather than applying the barrier layer to a standard synthetic surface, they used a self-assembled monolayer, or SAM, for their experiment. “These are molecules that assemble on an activated surface like tin soldiers,” explains Awakowicz. Thus, an extremely regular layer is created (Figure 2).. Compared to it, standard synthetic surfaces are nowhere near as tidy; consequently, it is impossible to quantify how much additional destruction the PECVD process causes in them. In the SAM layer, conversely, even the slightest disorder is immediately apparent (Figure 2). The greater the mess caused by PECVD, the more strongly the surface is affected by the process. Thus, the team from Bochum and Paderborn have demonstrated that the coating process destroys the topmost atom layers by oxidising surfaces.

FIG 2: The oxygenic plasma process for depositing the silicon dioxide barrier layer (green) damages the synthetic surface. The RUB team demonstrated this using a self-assembled monolayer (SAM) which becomes disordered due to the deposit. © RUBIN, photo: Gorczany
In order to prevent this, the RUB engineers initially apply an oxygen-free protective layer to the synthetic material (Figure 3). The oxygenic barrier layer is deposited on top of the protective layer. “We used to think that, by applying the protective layer, we are covering the synthetic material with glue, with a bonding agent. The whole world used to think that,” explains Peter Awakowicz. “But that’s simply not true!” Experiments have shown that the underlying protective layer is transformed by the growing barrier layer. Through oxidation, it gains similar properties to those of the barrier layer, thus making the synthetic material more impervious.
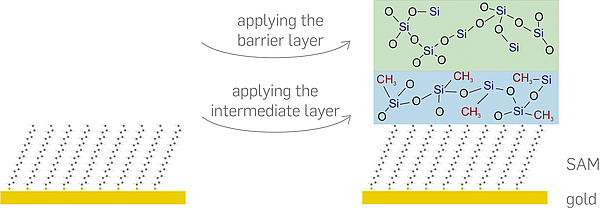
FIG 3: If the RUB team applies an intermediate layer (blue) prior to applying the barrier layer (green) to the synthetic surface, the surface remains intact. In the experiment, the group substituted a self-assembled monolayer (SAM) for the synthetic surface. © RUBIN, photo: Gorczany
Despite these findings, different items cannot be simply plasma coated in the same manner. The results depend on a number of parameters, e.g. plasma density, oxygen content, and the intensity of ion bombardment. The plasma parameters ultimately determine how impervious, hard and elastic the barrier layer becomes. Different synthetic materials, such as PET, polypropylenes or polycarbonate, require different plasma properties. The item’s shape is likewise significant. The RUB team begins their search for the correct settings for a new object with values that have worked for other items. Subsequently, they analyse the thus resulting layer.
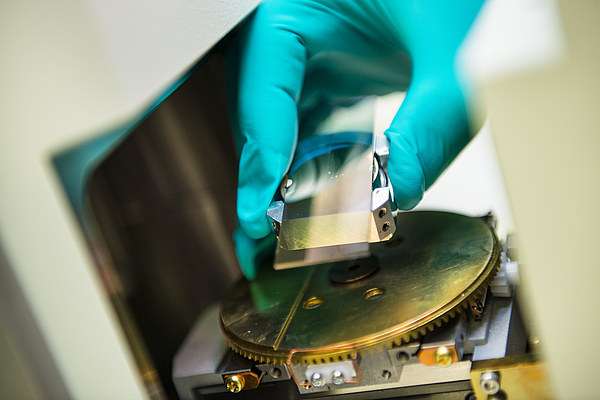
FIG 4: A team member places a sample into the scanning electron microscope for analysis.
© RUBIN, photo: Gorczany
Holes with diameters in the nanometre and micrometre range, which render the barrier permeable, will always occur. Their numbers and sizes are indicative of the quality of the process. The Institute for Electrical Engineering and Plasma Technology has developed an automatic process for detecting, counting and measuring holes. The problem is: even with electron microscopy it is impossible to detect the defects in the barrier layer. It takes a specific treatment to render them visible. For this purpose, the researchers utilise the holey barrier layer as a mask. They etch the underlying layer with oxygen radicals through the holes. In it, much larger, sharp-edged holes are thus created (Figure 5), which can be seen under the electron microscope due to their shape and size. A computer programme written by the researchers detects the defects through pattern recognition and assesses them.
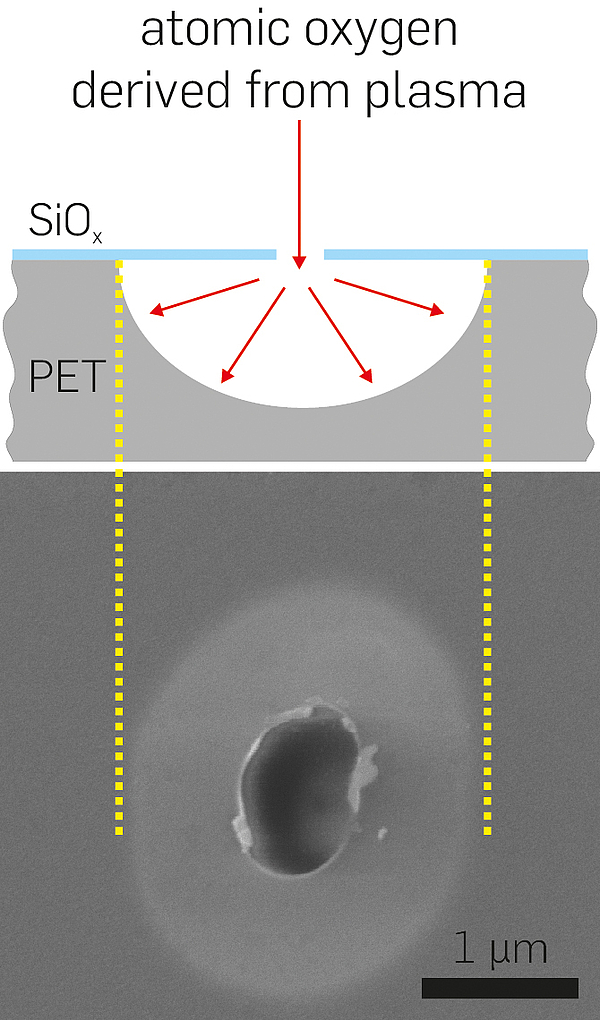
FIG 5: Each barrier layer (blue) contains small defects which, however, are invisible – a problem for quality analysis. The researchers’ trick: they use the barrier layer as mask and etch the underlying synthetic layer (PET) through the defects. Thus, larger holes are created that can be detected under the electron microscope © RUBIN, photo: Gorczany
This is only one station within the entire test parkour undergone by the coated samples in the Bochum lab. Elasticity and barrier function for various gases are likewise tested. The aim is to gain a better understanding of the extent to which the plasma properties determine the result of the coating process. In future, this is supposed to speed up the search for the optimal parameters for an object that requires coating. Depending on the item, the search can currently take anything between two days and one year. “There is an infinite number of combinations for plasma parameters. But the more experience we gain, the quicker the process,” says Peter Awakowicz.
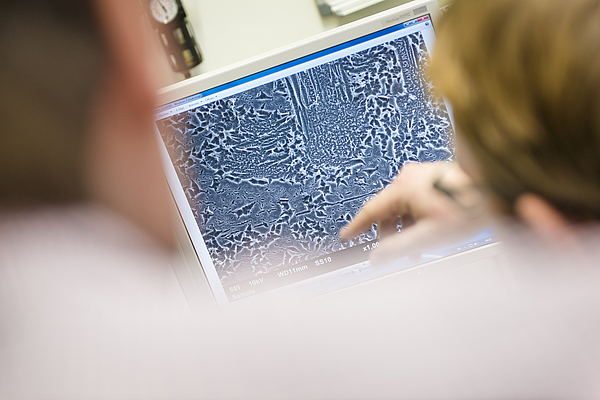
FIG 6: The RUB engineers analyse defects in the applied layers using scanning electron microscope images. © RUBIN, photo: Gorczany
In collaboration with partners from the industry, his team has optimised the process to a considerable extent for PET bottles, in the course of a project funded by the Federal Ministry for Economic Affairs and Energy. The research consortium owns a coating plant, too. To date, only one commercial manufacturer of such equipment has existed worldwide; the technology has not as yet established itself in the market. Products in coated packaging are few and far between; PET bottles are still being made without a barrier layer. This may change in one or two years, as Peter Awakowicz estimates, namely once the process developed in his institute is ready for industrial applications.
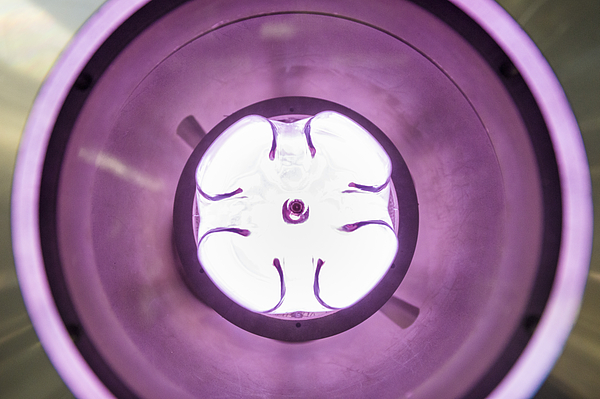
FIG 7: An argon plasma in a PET bottle - just the bottle bottom visible here.
The plasma “cleans” and activates the interior bottle surface. © RUBIN, photo: Gorczany
Plastic coatings are not the only matter that the engineers are interested in. Under the umbrella of the SFB/TR 87 project “Pulsed high power plasmas for the synthesis of nanostructural functional layers”, they are also developing methods for plasma-aided coating of metal surfaces. Ceramic layers can increase the resistance of metallic components such as drills, thus extending their service life. This approach is used for coating metal tools used for the production of synthetic components. It ensures, for example, that the liquid plastic does not adhere to the tool too much, nor too little. If the tool is optimally coated, the quality of the synthetic component thus created is ultimately improved.
CORE STATEMENTS
by Prof Dr-Ing. Peter Awakowicz
The oxygenic barrier layer is deposited on top of the protective layer. “We used to think that, by applying the protective layer, we are covering the synthetic material with glue, with a bonding agent. The whole world used to think that,” explains Peter Awakowicz. “But that’s simply not true!” Experiments have shown that the underlying protective layer is transformed by the growing barrier layer. Through oxidation, it gains similar properties to those of the barrier layer, thus making the synthetic material more impervious.
Different items cannot be simply plasma coated in the same manner. The results depend on a number of parameters, e.g. plasma density, oxygen content, and the intensity of ion bombardment. The plasma parameters ultimately determine how impervious, hard and elastic the barrier layer becomes.
Holes with diameters in the nanometre and micrometre range, which render the barrier permeable, will always occur. Their numbers and sizes are indicative of the quality of the process. The Institute for Electrical Engineering and Plasma Technology has developed an automatic process for detecting, counting and measuring holes.
The aim is to gain a better understanding of the extent to which the plasma properties determine the result of the coating process. In future, this is supposed to speed up the search for the optimal parameters for an object that requires coating. Depending on the item, the search can currently take anything between two days and one year. “There is an infinite number of combinations for plasma parameters. But the more experience we gain, the quicker the process,” says Peter Awakowicz.
The comPETence center provides your organisation with a dynamic, cost effective way to promote your products and services.
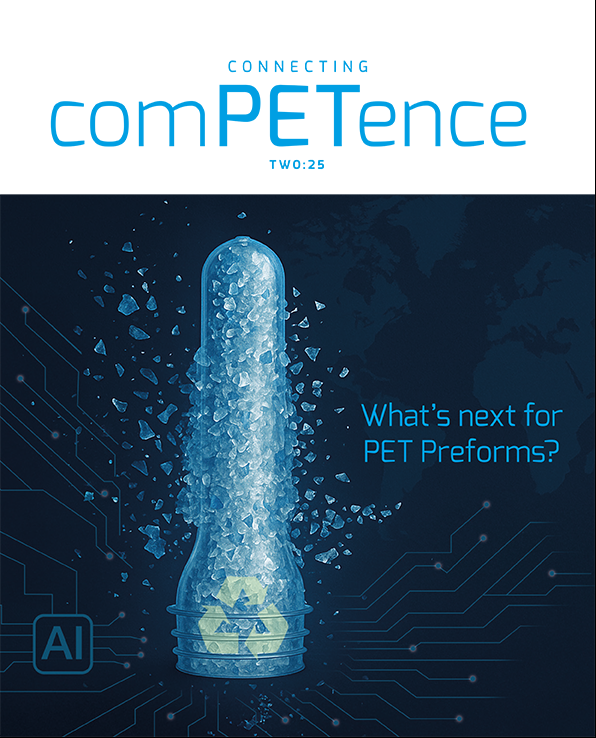
magazine
Find our premium articles, interviews, reports and more
in 3 issues in 2025.