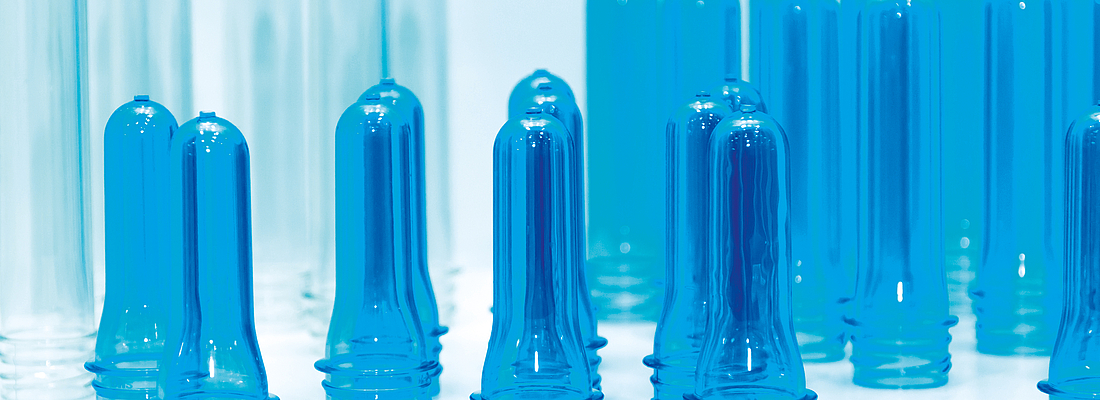
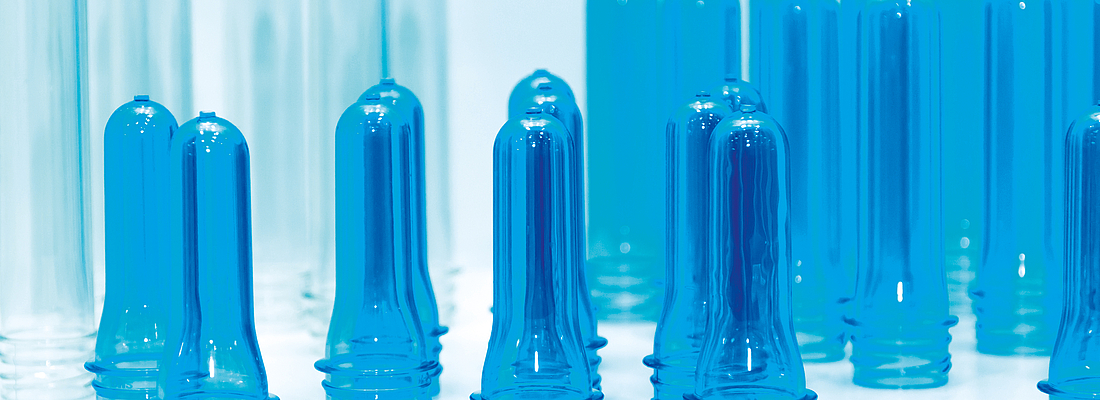
The PET bottle, one of the most important mass products in the beverage industry, is made from a preform, which is produced in-house by converters or by fi llers when there is a very high demand. Injection moulding machines are used to produce such preforms - or more precisely injection moulding systems that consist of several components and therefore require special know-how. Even if the PET market is growing inexorably, the margins are not enormous; they are only achieved through large quantities or with niche products for special requirements. There is not much room for manoeuvre when it comes to purchasing PET raw materials. In the case of converters, this is compounded by the fact that their preforms are often sold as bulk material by weight, which means that the price structure does not allow much scope for pricing with known raw material prices. It is therefore not advantageous for the converter to achieve material savings by keeping the preform weight of the individual preforms as close as possible to the lowest tolerance limit - or by keeping the weight dispersion as close as possible to the tolerance limit. It looks more favourable for the direct end customer: every weight percent saved on the preform immediately brings a cost advantage.
Within the beverage industry, the preform industry, as already mentioned, generates its margins more from the mass, so that the PET raw material throughputs at a production site of approx. 100 to 400 tons per day are the usual order of magnitude. But where are profi t optimizations possible under these conditions?
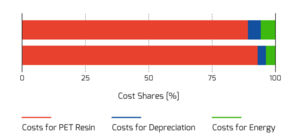
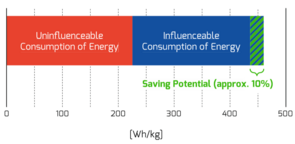
IN PREFORM PRODUCTION, THERE IS ALMOST ALWAYS SIGNIFICANT POTENTIAL FOR COST OPTIMIZATION, WHICH CAN HAVE A DIRECT IMPACT ON MARGINS.
First there are the fi xed costs, in which cost-intensive capital goods, typical of the preform industry, play a significant role in addition to salaries.
For variable costs, production-related energy consumption and raw material (PET-material and additives) are by far the largest items in the cost structure. However, it has already been mentioned that converters often sell preforms by weight, so that the cost of the resource raw material seems less attractive at first. However, this assessment will be examined in more detail later. Energy consumption in preform production, on the other hand, always carries a worthwhile potential for cost savings, which is often underestimated and to which more attention should be paid.
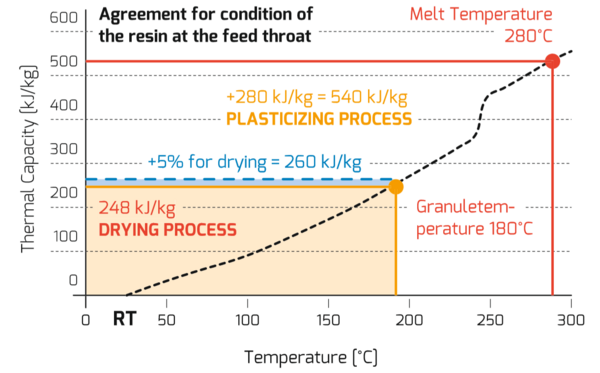
EXAMPLE
An average preform system which, for example, uses 900kg/h of PET material has an approximate annual energy requirement of 3,200 MWh. If the price for industrial electricity is around 10 cents per kWh as in Germany, energy costs of around € 320,000 per system must be calculated. The processes of energy absorption of the PET material and the subsequent cooling of the finished preforms are subject to physical laws: On average, an energy consumption of between 420 and 500Wh/kg (average 460Wh/kg) is calculated specifically for 1 kg PET during production with a modern injection molding system. Depending on external influences, between 210 and 240Wh/kg (average 225Wh/kg) of this energy is physically bound by the PET and cannot therefore be influenced. However, the remaining energy quantity of 235Wh/kg - a good half of it - can be influenced, of which experience shows that an average potential saving of approx. 10% is possible.
For this example, that would be €16,000 per year, which could flow directly into the margins, not taking into account any tax benefits. In order to realize this potential, in many cases hardly any investment is required - and if it is, it will be amortized within a reasonable period of time.
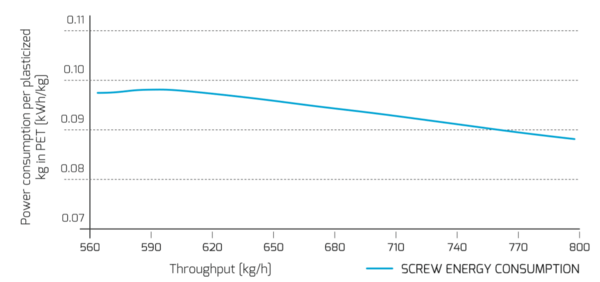
WHERE DOES THE ENERGETIC COST OPTIMIZATION START AT THE PREFORM SYSTEM?
Decisions about the equipment of the components and also their positioning within the system are already decisive for energy consumption when purchasing cost-intensive production systems. Good negotiation skills and independent purchasing of individual components can apparently save a lot of money quickly: Injection molding machine manufacturers convince their customers with fast cycle times, efficient injection molds and low maintenance costs with low energy consumption. Dryer manufacturers praise efficient drying with likewise low energy consumption, and manufacturers of injection molds and cooling equipment argue similarly. But how do these components work in the finished system?
Of course, a functioning production system can be put together from the offers of individual components, the preforms can lie within their specifications - but when it comes to checking the energy efficiency of the individual components for their specifications, it becomes more difficult than assumed. A rough overview of the overall power consumption is usually easy to obtain, but individual components of a PET system often cannot be evaluated because of a lack of relevant information.
The energy consumption of individual components of a PET system depends not only on external influences, but also on their interaction during the production process. This has a considerable influence on energy consumption. As already mentioned, a savings potential of approximately 10% on variable energy consumption is possible. But if the individual components cannot be assessed, how can the overall process be optimized?
A training course on energy management in preform production helps to realize significant savings. Comment of Western Container Corp. (WCC) Sugarland TX, USA, Roger Kerr, Paul Lovell: “It was eye-opening to see how much opportunity there is with injection presses!”
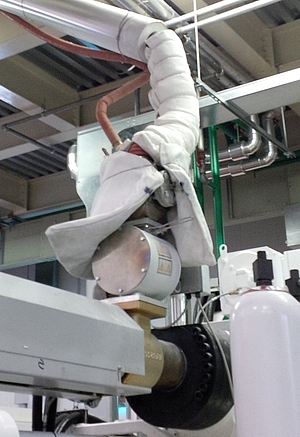
AN IMPORTANT AND OFTEN UNDERESTIMATED COMPONENT - THE DRYER UNIT
At the beginning of the production process there is the dryer, whose task is not only the drying of the PET raw material - the second and equally important challenge is to supply the material with sufficient energy for the plasticizing process. The dryer’s ability to absorb large quantities of material gives it suffi cient time to condition the material economically. Whether the plasticizing process. This requires a clear agreement on the condition of the PET material if it is to be transferred from the drying process to the injection molding process:
- Regardless of the incoming PET material condition (temperature and humidity within the dryer specifi cation), the material must be delivered to the injection molding machine in a constant condition.
- The PET material temperature stands for an energy content that must be defined.
- The residual moisture must also be determined
While the dryers for residual moisture measurement can usually be very well equipped, monitoring the energy input is rather rare, only a few dryers have enough equipment to control this properly, as this can also be costintensive.This starts with the fact that very few dryers are able to measure the temperature of the incoming PET material in the hopper. Normally assumptions are made and then a necessary amount of dry process air is determined that approximately fits.
With low PET material consumption and higher feed temperatures, this is hardly noticeable: excess energy is fed to the cooling unit via a heat exchanger. This means that this air has been heated unnecessarily and then cooled down again: The excess energy is therefore paid twice over.
If, on the other hand, the throughputs are high and the material is not heated sufficiently, this is to the expense of the plasticizing unit. It is important to know that an injection molding machine reacts very sensitively to fluctuations in the energetic state of the material. This is reflected in the high shear of the material, which then leads to high temperatures in the metering zone that can no longer be controlled. In combination with additives such as colors or AA-blockers, the conveying of the material also breaks down. This damages the material (degradation), which leads to acetaldehyde (AA) and can therefore exceed the limit values of the individual specifications. This phenomenon is usually compensated by an increase in the cost-intensive AA blocker dosage. The appropriate training impressively conveys the cooperation between dryer and Extruder. After a workshop the finding of Coca-Cola European Partners Deutschland (CCEP DE), Halle, Germany Ingo Schröter:
“The training has demonstrated us the possibilities of energy saving in relation to our material drying. Measures were initiated to optimally align our dryer plant technology with our current production processes.”
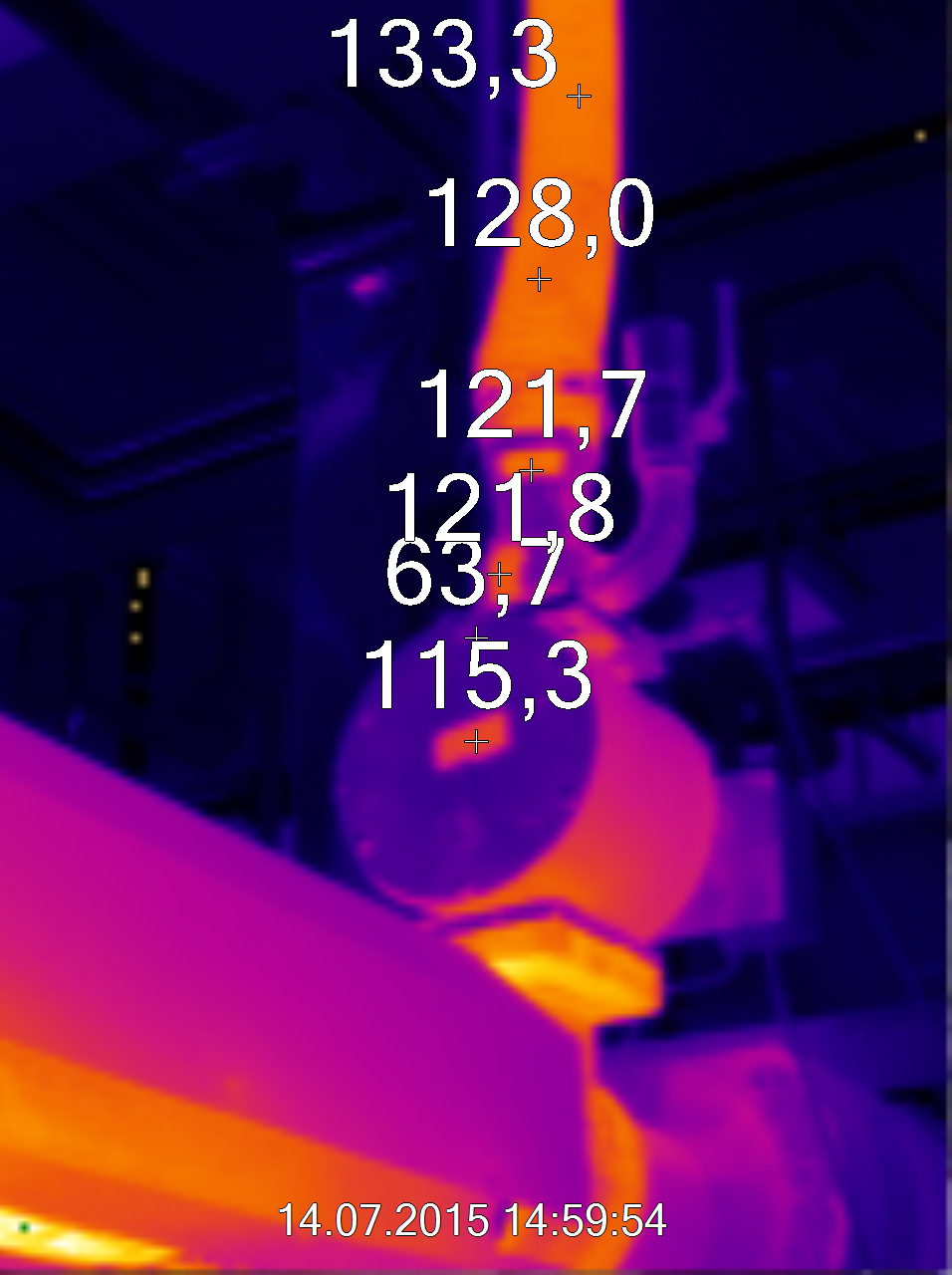
It is also often overlooked that the real capacity utilization of the plasticizer has a large influence on the energy consumption compared to the nominal value of the throughput. It is not uncommon to observe that when the demand for preforms is lower, the systems tend to run at a reduced cadence, as this is expected to lead to more stable production. This effect is often unknowingly bought with a significantly higher electricity bill.
When connecting the material flow from the drier hopper to the plasticizer, conductive steel components are often used that are not actively heated and rarely insulated. This applies to the PET material feed line often in conjunction with magnetic grids and to feeds of additives such as paint dosers or material mixers. This means that even if the dryer has supplied sufficient energy to the PET material, it is still discharged uncontrolled and thus causes additional energy costs.
Experience has shown that the PET material loses about 10- 15°C in a colour mixer alone. This corresponds to a specific output of 4.5 -6.8Wh/kg. With a standard throughput of 900kg/h, the annual loss is approx. 50,000kWh, the additional output of the extruder, which has to be paid for, then reaches 65,000kWh/year, in Germany the equivalent of 6,500 €/year.
In today’s generations of plasticizing screws, a color mixer is unnecessary if the material reaches the screw feed sufficiently conditioned.
The company ReduPET is specialized in the energy evaluation of preform production systems in the production process in order to determine the savings potential and to propose measures to the operator. For this purpose, comprehensive training is offered in advance, in which the employees at the production site gain a practical understanding of the energetic interrelationships in preform production. This helps to optimally adjust the processes to the energy consumption. Since each too much energy used automatically damages the PET material, the preform quality (Black Specks AA values) also benefits from these measures - and just as important: the stability of the production process.
Well-known manufacturers of preforms on the market have already taken advantage of the ReduPET offer and were able to implement advantageous measures and further training. As a result, the investment paid for itself in a very short time in the form of an increase in margins and tax advantages. PDG Plastiques, Malesherbes, France:
“Thanks to the training, we were able to identify the potential for conserving resources. The proposed measures to exploit the savings potential are being implemented in our company to the greatest possible extent.”
The comPETence center provides your organisation with a dynamic, cost effective way to promote your products and services.
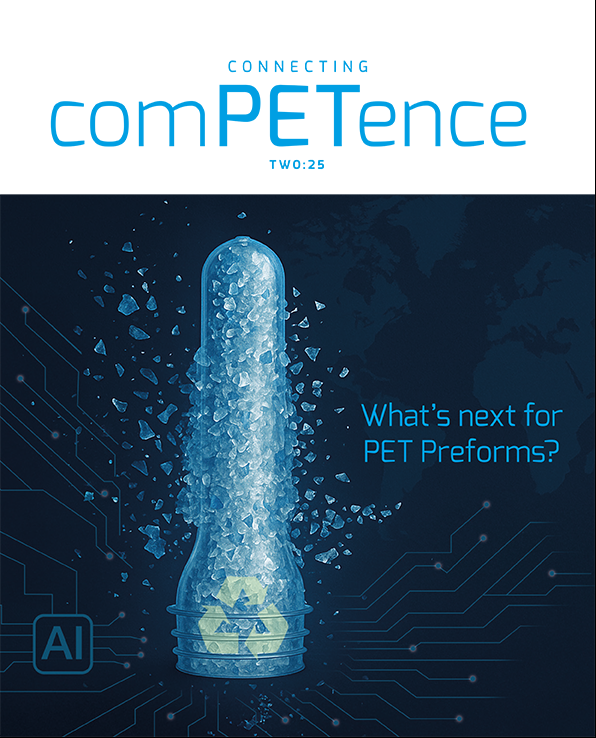
magazine
Find our premium articles, interviews, reports and more
in 3 issues in 2025.