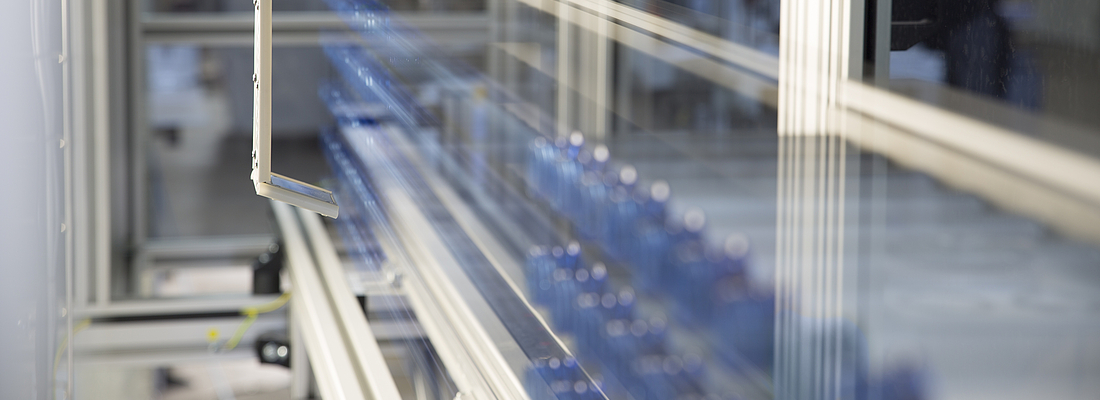
In the last issue of comPETence an overview was given on the development of Vision Inspection Systems in the plastic packaging industry. Vision inspection systems already came a long way: They evolved from systems which removed faulty products from the output of blow molding or injection molding machines. And then they became reliable early indicators of systematic machine errors. However, operators are still needed to translate even the most narrative error statistics into measures that improve the production efficiency.
So it seems a natural idea to couple the vision inspection system with the production machine and let them talk with each other. This is the principle idea of Industry 4.0.
Closed loop control
Humans are highly precise machines in spite of the fact that the movements of their actuators, their hands, arms and legs are pretty unprecise. The trick is the closed loop control: When a human reaches for a cup of coffee in front of him, all his senses, especially his eyes and his sense of touch are constantly giving him feedback about the position of his fingers in relation to the object and about the grip with which the fingers are finally holding the cup. How much the feedback loop improves the ability for the proper handling of the cup, everybody can easily try out by closing the eyes and wearing thick gloves, when trying to take a sip from the morning coffee cup.
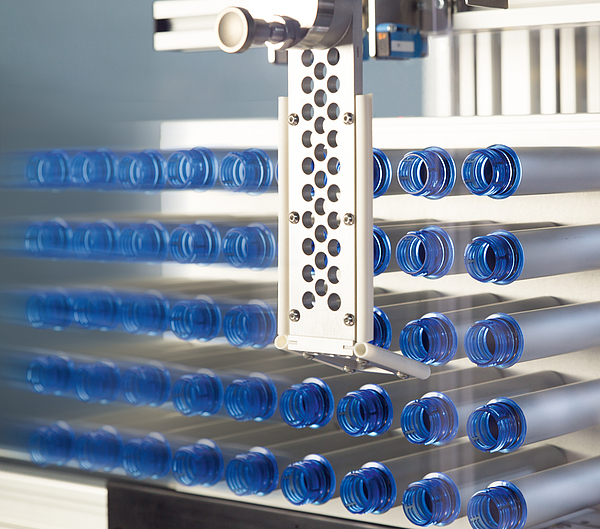
FIG 1: The ColorWatcher Integrated by Intravis is implemented directly into the production machine,
inspecting preforms right after they are produced.
control feedback engineering
As easy as the procedure of taking a cup from the table in front of you looks – it took you years to train your feedback system before you were able to drink without spilling.
And here we already see one reason why it isn’t so easy to couple technical sensors and actuators to take advantage of the feedback loop: Because the control element - “the brain” - needs to know what the adequate reaction to the actuators is, when a certain sensor signal is given as input. This is exactly what control feedback engineering is about. Control engineers strive to find the algorithm which let the actuators act in the right way. For that reason they model the system in the control element and try to find the system answer. This can be a very difficult task, because little is known about the mathematics behind the system’s behavior in case of such complex systems like an injection molding machine.
In cases where it is difficult to model the system and to figure out the system answer, controls based on Artificial Intelligence (AI) might help. Neuronal Networks and evolutional optimization strategies were used to implement some impressive examples where the injection molding process was stabilized in the optimal working point.
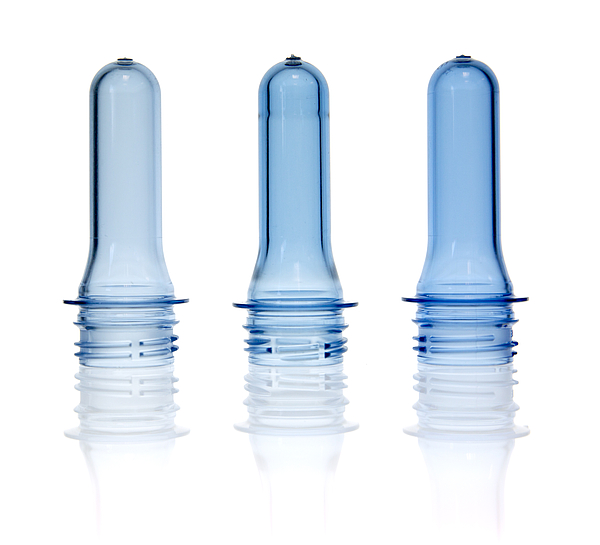
FIG 2: Color deviations belong to the most frequent defects in preform production.
Only the middle preform has the right color – the left one is too light, the right one too dark.
integrated quality inspection
Typically some time goes by before the product reaches the point at which its quality is inspected. As this delay time has an impact on the loop-back control, it is clear that only those disturbances can be successfully compensated which have a significantly longer time constant than the mentioned delay time.
This also is a reason for implementing modern quality inspection systems right after the production – in the best case they are integrated into the production machine. A good example is the ColorWatcher Integrated of Intravis which inspects the color of newly produced preforms already in the handling, right after they are coming out of the mold. At this position the preforms are exactly and repeatedly positioned, which is a prerequisite for an exact and repeatable measurement. The delay time is as small as possible. With this setup even the smallest color deviations of the preforms can be determined and the dosing process can be controlled to compensate for those deviations. In such a way problems can be avoided before they occur.
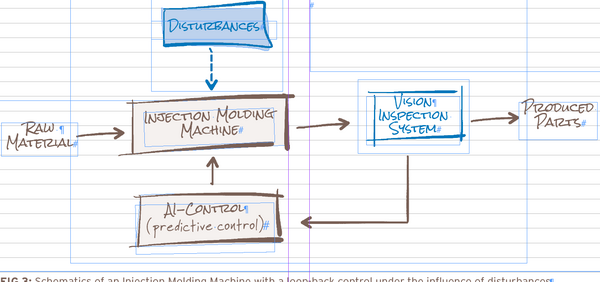
FIG 3: Schematics of an Injection Molding Machine
with a loop-back control under the influence of disturbances
The comPETence center provides your organisation with a dynamic, cost effective way to promote your products and services.
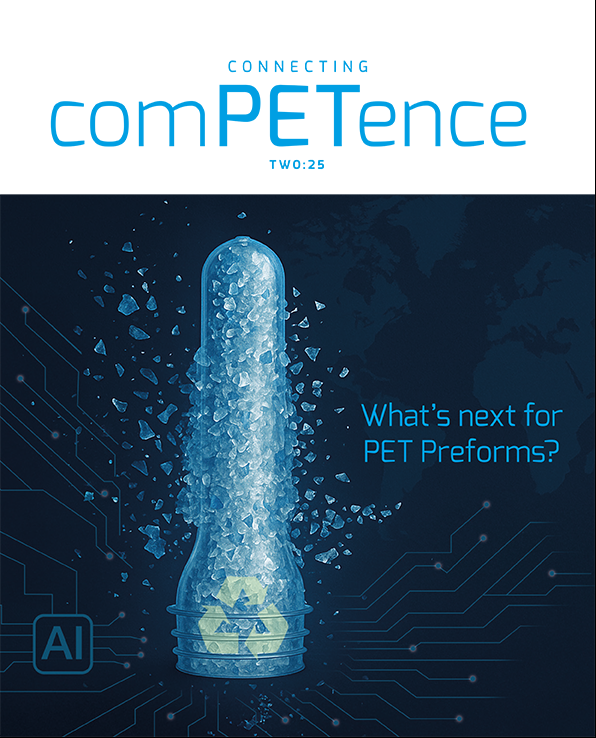
magazine
Find our premium articles, interviews, reports and more
in 3 issues in 2025.