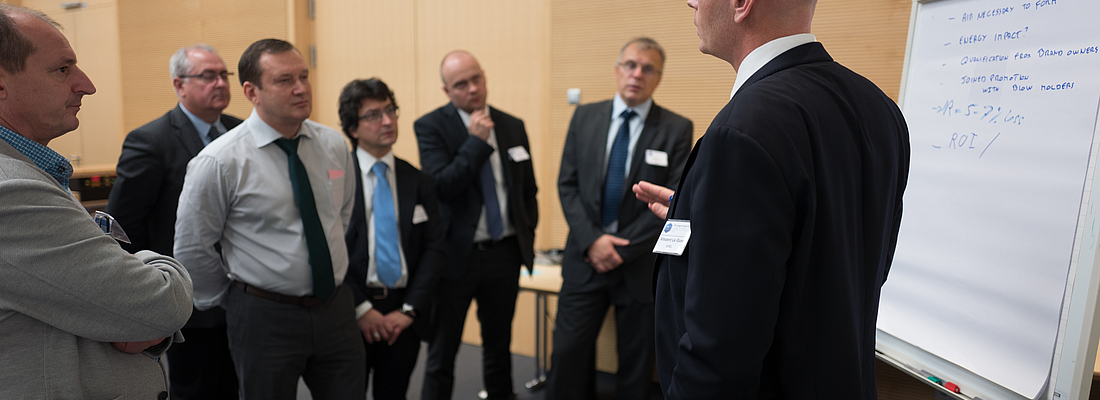
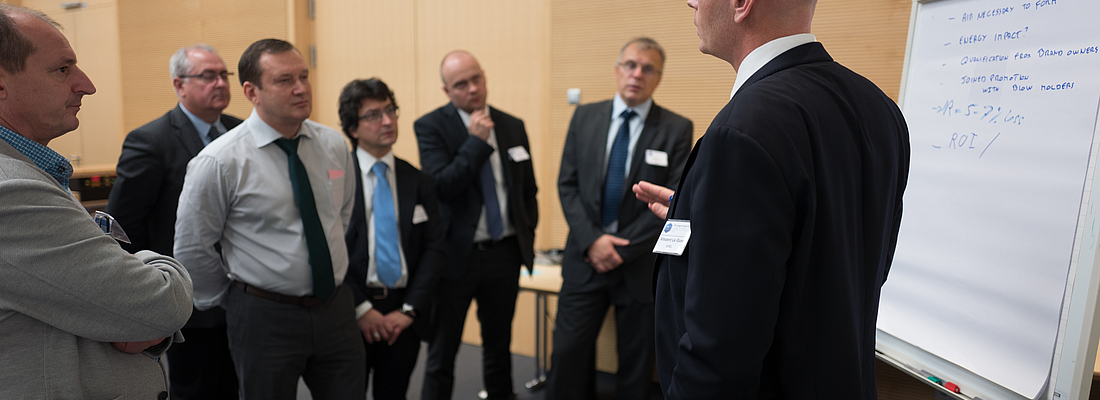
Thin-walled preform bases for a significant weight reduction in the bottle base - Interactive workshop at PETnology yields valuable results
The collaborative work between Creative Packaging Solutions, Krones, MHT, Netstal, Otto Hofstetter and Sidel on weight reduction has met with a lot of interest.
Lightweighting has been a perennial issue since the breakthrough of PET bottles in the drinks industry. The objectives are to save material and costs, as well as resource conservation and sustainability. However, the end of the road has been reached as far as further weight reduction of the bottle surface is concerned: Very thin bottles lack the required stability and are not accepted by consumers. Nonetheless, weight and consequent cost reduction remains an important and much talked-about topic across the industry. This became very clear during the interactive workshop on “thin-walled preform bases for a significant weight reduction in the bottle base” held during PETnology Conference 2015. With over 60 participants, the workshop was particularly well attended, with diverse and constructive contributions to the discussion. In this workshop we have learned what processing companies find important when introducing a new technology.
The workshop was remarkable on account of both the subject matter and the exceptionally collaborative approach. The companies MHT – Mold & Hotrunner Technology AG from Germany, Creative Packaging Solutions Ltd (Mint-Tec) from Turkey, Netstal and Otto Hofstetter AG from Switzerland presented their development work and results together. Netstal and Creative Packaging introduced their new processes, Preblow and Mint-Tec respectively, and MHT and Otto Hofstetter presented initial results attained with the new processes using selected practical examples. Following this, representatives from each company supervised small groups of around 15 people each and led them in discussion around four stations entitled:
1. “Advantages and disadvantages of thin-walled preform bases”
2. “How to improve my existing product with this new technology”
3. “Effects of savings as regards market, environment and promotion”
4. “Market barriers to new technologies”.
The results are displayed on the following pages. All of the discussions showed that while new technologies and their potential are important for processors, the ROI is an indispensable indicator.
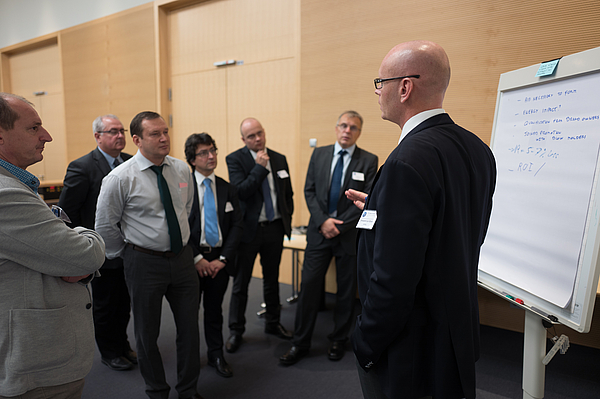
1) Advantages and disadvantages of thin-walled preform bases
Advantages:
-3-5% less bottle weight without losing principle properties
of the container
-or - Increasing quality properties
-Less energy consumption (IR-lamps) for the blow moulding system
-Less blowing pressure for blow moulding process
-Higher efficiency of the blow moulding system in terms of cycle time
-Higher stretch ratio in the base (stiffness)
-ROI is attractive within 6 month
-Less off-center with the pin of Mint-Tec
-Alignment injection moulding => blow moulding
-OEM(Original Equipment Manufacturer) for beverage and liquid container
Disadvantages:
-For CSD stress crack might be an issue, mainly with PreBlow
-=> unknown effect to the bottle specification
-Risk of “base roll out” in dependence of application
-Less flexibility in regards to CSD and still applications
-Investment Costs (ROI not clearly communicated)
-More stress in the base
-More complex preform production
-Effect for hotfill application (needs thickness at the base)
-The testing phase for new container might take longer
Weight reduction through preform base optimisation
While it is not currently possible to further reduce the thickness of bottle surfaces without sacrificing stability, there remains some potential for weight reduction. The focus is on two areas of the bottle: the neck and the base. The new PCO 1881 thread geometry in the bottle neck can save 2.4 g in comparison to its predecessors while a 1.4 g saving can be made with the new twist off cap 29/25. The workshop focussed on the bottle base, which offers clear potential for optimisation. Both of the processes presented aim to modify the base of the preform to achieve a much more uniform and hence thinner base, leading to a reduction in weight. This is achieved by optimizing the preform geometry. A larger surface (Figure 1) is easier to heat, leading more even moulding during the blowing process.
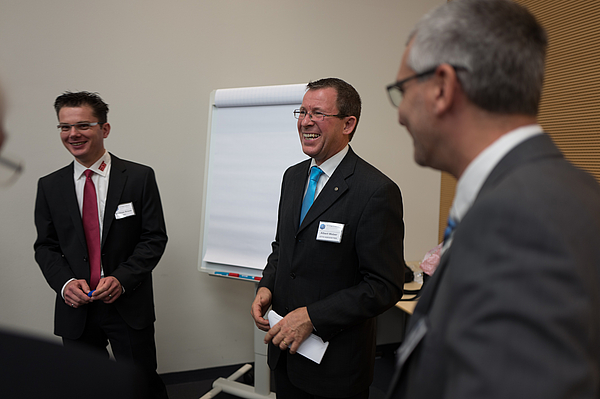
2) How to improve my existing product with this new technology
- Needs for an evaluation through a sampling process are:
Bottle samples, preform drawing
- Best approach with new mould equipment (highest ROI)
- Implementation in existing mould systems also possible
- Direct sampling for preforms with two mould maker MHT-AG
and OHAG
- Blowing tests to evaluate saving potential
- Adjustment of the base weight in regards to quality (modification of the core in the injection mould), supported by the involved companies
- Final sampling if requested
- Implementation of the production process in PET systems
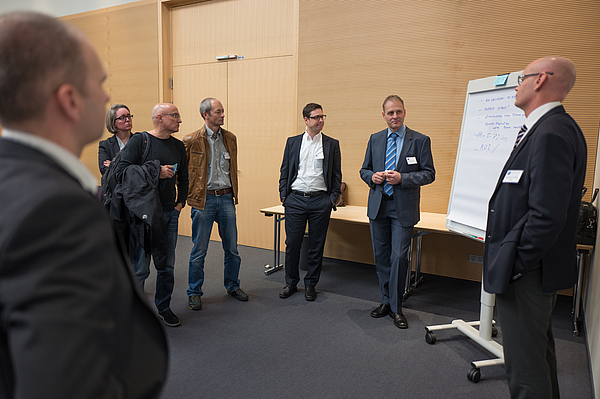
3) Effects of savings as regards market, environment and promotion
Effects of direct savings are:
-Energy for injection moulding (less raw material)
-Energy for blow moulding (IR-lamps, less pressure needed)
-Less resin in the bottle base needed
-Improved life cycle assessment (LCA)
Effects on the environment
-Less plastic needed for production of bottles
-Less energy needed to produce bottles
-Less time for bottles to degrade
-No wasted material in the bottle base
Effects for promotion
-Advertizing for reduction of raw materials on the bottle
-Raw material really placed where it is needed
-European technology
-Joined promotion with blow moulders
Qualification for brand owners
Improved plastic perception (appearance)
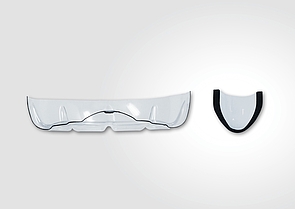
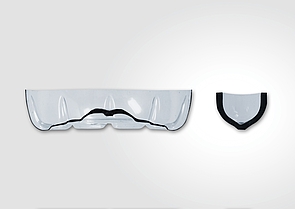
FIG 1: Preform and bottle base (Photo: Netstal
Both Netstal’s Preblow and the Mint-Tec process expand the surface; Netstal achieves this by moulding the base of the preforms with compressed air at 2 bar shortly before removal from the injection mould. In the Mint-Tec process, a plunger enters the preform after moulding – without touching the neck – and shapes the base as required.
Both processes were tested by the companies MHT and Otto Hofstetter and were shown to reduce weight considerably: Using the Preblow-process, MHT optimised the preform for the American brand Niagara’s still mineral water bottle – currently one of the lightest 0.5 l PET bottles. The bottle weight, which at 8.53 g already was very low, was reduced by 0.23 g to 8.3 g. Base optimisation could save 188 metric tons of PET and 207,000 euros per year in an annual production output of 817 million performs.
Using the Preblow process, Otto Hofstetter managed to optimise a 1 l detergent bottle weighing 23 g from the brand Dragao, reducing the weight by 1 g to 22 g. This could save 239 metric tons of feedstock material and 262,000 euros of costs in an annual production output of 239 million preforms.
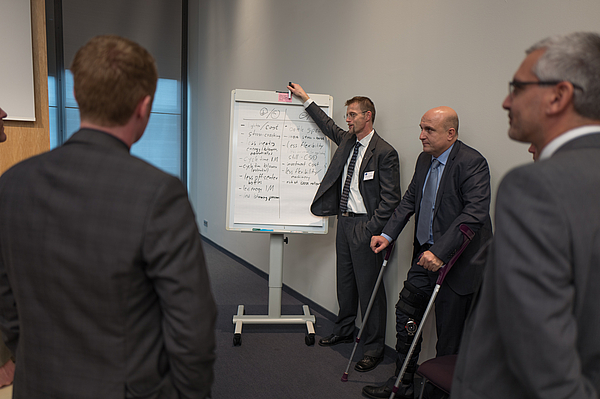
4.) Market barriers to new technologies
- How to enter the market - converter is not the right approach
- Better to go over beverage OEM
- Communication about return of invest (ROI) – actually not enough information available
- Communication in regards to the compatibility
- Communication about the testing phase of such bottles
- Communication about suitable applications
- Existing systems may have a higher barrier than new systems
due to ROI
Unlike in the Preblow process, which is currently only able to optimise preforms for still drinks and fluids, the Mint-Tec process has also been approved for carbonated drinks.
Using the Mint-Tec process, MHT successfully optimised the preform for a 1.5 l bottle for carbonated water sold on the German market. Whilst the conventional preform weighed 27.1 g, the optimised form has a weight of just 26.5 g. This 0.6 g difference generates savings of 173 metric tons of materials and 190.900 euros in an annual production capacity of 289 million preforms.
The owner of Creative Packaging, Mahir Aktas, also reported that the French blow moulding machine manufacturer Sidel from Le Havre have tested the Mint-Tec process and obtained good results. “Due to the optimised base design, Sidel has successfully expanded the blowing process operating window and produced larger bottles at a higher output capacity.”
Since both Preblow and Mint-Tec are new processes, all partners involved were very interested in discussing them with customers, receiving questions and ideas, and carrying out further tests. The workshop was the first opportunity of this kind. Further questions and enquiries are welcome.
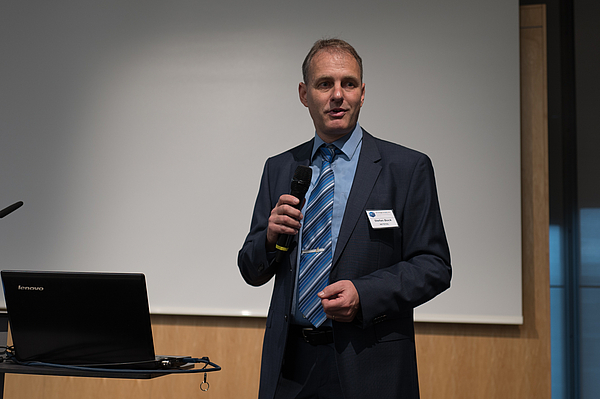
5) Conclusion
- Thin walled preforms with all their properties and saving potential may have a great future, if the technique is used in a suitable way.
- Thin walled preform bases should be used with precaution for special applications such as hot-fill
- It was highly recommended to show clear calculations for ROI on existing and new systems
- The approach through the sampling process should to be better communicated, the companies Netstal Maschinen AG, Creative Packaging Solutions (CPS), Otto Hofstetter AG and MHT AG are ready to support any project
- Beside savings, an easier and more effective blow moulding process might be expected with this new technology
- Promotional advantages for brand owners might are expected as well as a positive impact to the environment
The comPETence center provides your organisation with a dynamic, cost effective way to promote your products and services.
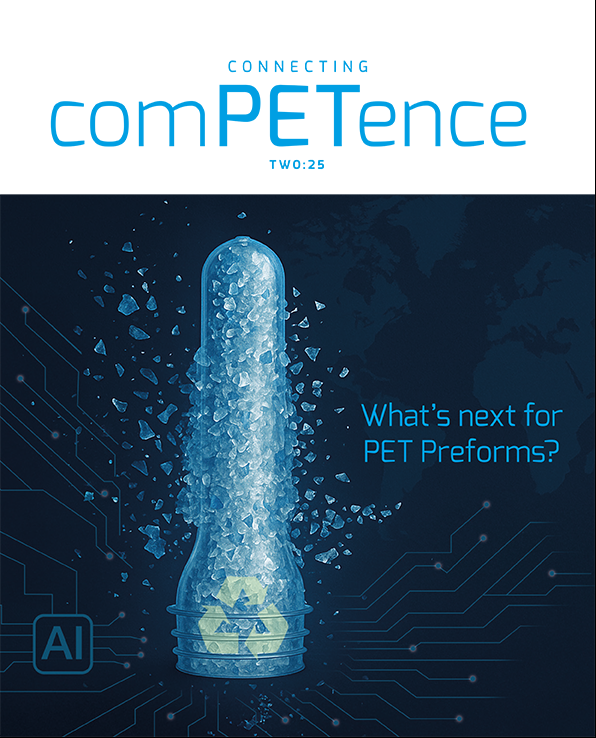
magazine
Find our premium articles, interviews, reports and more
in 3 issues in 2025.